- お役立ち記事
- Following the Lumber Manufacturing Process in Sawmills
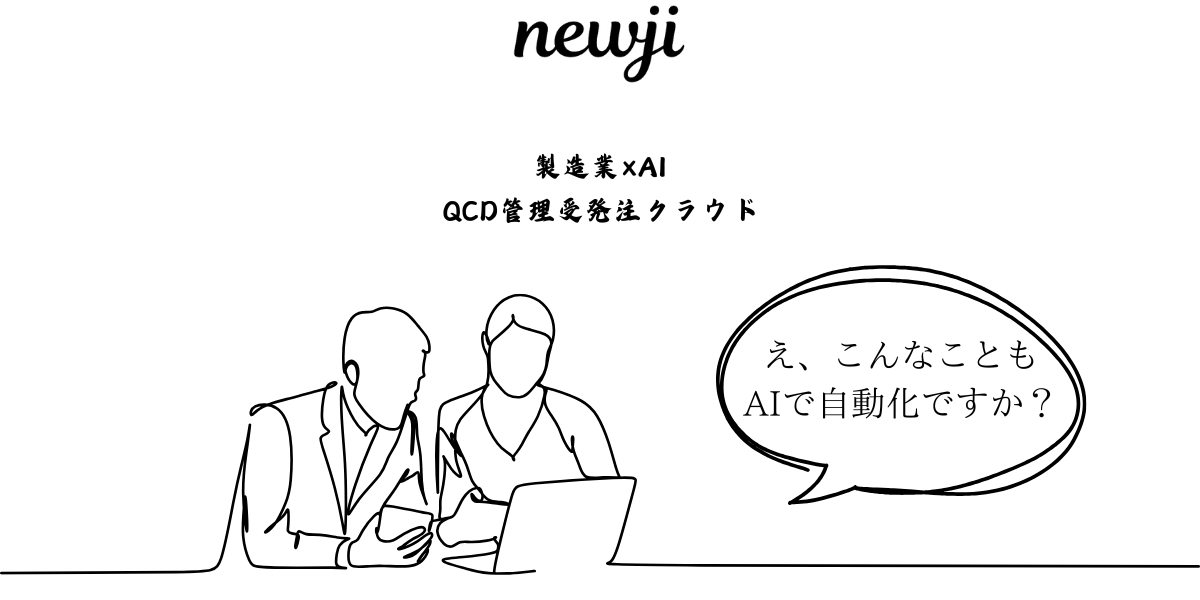
Following the Lumber Manufacturing Process in Sawmills
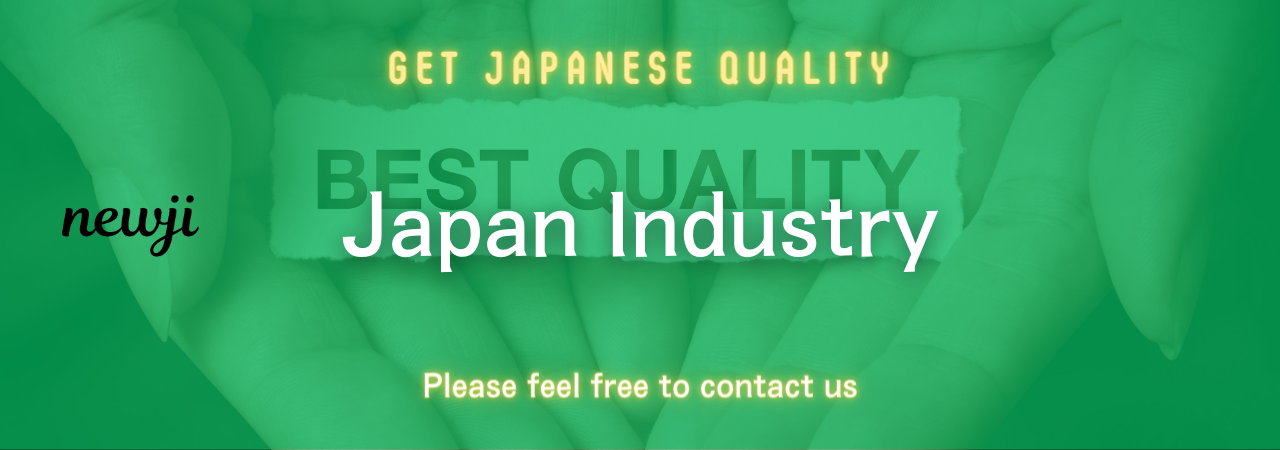
The journey from a tree in the forest to the lumber you see at a construction site is quite fascinating.
Sawmills play a crucial role in this transformation.
Understanding the lumber manufacturing process in sawmills can help you appreciate the meticulous effort that goes into producing the wooden boards and beams we often take for granted.
目次
Logging: The First Step
The lumber manufacturing process starts with logging.
Once a suitable tree is identified, loggers cut it down using chainsaws or other machinery.
The felled trees are then trimmed to remove the branches and leaves.
What remains are logs that are easier to transport to the sawmill.
Logging is often conducted during specific seasons to ensure the health of the forest.
Loggers pay close attention to sustainable practices, selecting only mature trees and leaving the young ones to grow.
Transportation to the Sawmill
Once the trees are cut and trimmed, the logs need to be transported to the sawmill.
This is usually done via trucks equipped to carry heavy logs.
In some cases, the logs are floated down rivers or transported by rail.
Choosing the right transportation method depends on the location and accessibility of the forest.
Transportation plays a crucial role in maintaining the quality of the logs.
Efforts are made to minimize damage during this stage, as flawed logs can affect the quality of the final product.
Initial Log Inspection
Upon arriving at the sawmill, the logs undergo an initial inspection.
Sawmill workers check for any defects such as rot, excessive knots, or cracks.
Logs that pass this inspection move on to the next stage, while defective logs are often repurposed or discarded.
This stage ensures that only quality logs progress through the lumber manufacturing process.
It also helps in categorizing logs based on their intended use – whether for construction, furniture, or other purposes.
Debarking and Scaling
The next step in the process involves removing the bark from the logs.
This is done using specialized machinery called debarkers.
Removing the bark makes it easier to cut the logs into lumber and helps in identifying any remaining defects.
After debarking, the logs are measured for length and diameter in a process known as scaling.
This measurement helps in determining the volume of lumber that can be produced from each log.
It also assists in planning how the logs will be cut to minimize waste.
Sawing the Logs
Once debarking and scaling are complete, the logs are ready for sawing.
Sawmills use large, high-powered saws to cut the logs into smaller, more manageable pieces known as cants.
These saws come in various types including band saws, circular saws, and head saws.
The cants are then further processed by smaller saws to create lumber of different sizes and shapes.
Each cut is carefully calculated to maximize yield and minimize waste.
Drying and Curing
Freshly cut lumber contains a lot of moisture.
To ensure the wood is suitable for use, it must be dried.
There are two primary methods for drying lumber: air drying and kiln drying.
Air drying involves stacking the lumber in a way that allows air to circulate freely around each piece.
This method is slower but uses less energy.
Kiln drying, on the other hand, involves placing the lumber in a specialized kiln where heat is used to remove moisture quickly.
This method is faster but requires more energy.
Both methods aim to achieve a specific moisture content that ensures the lumber is stable and durable.
Planing and Grading
After drying, the lumber is moved to the planing stage.
Planers are machines that smooth out the rough surfaces of the lumber, making it more uniform in thickness and width.
Post planing, the lumber undergoes grading.
Grading involves inspecting each piece of lumber for qualities such as grain pattern, knots, and other visible defects.
Lumber is categorized into different grades based on these characteristics, affecting its price and suitability for various applications.
Treating and Finishing
Depending on its intended use, lumber may undergo additional treatments and finishing.
For example, lumber that will be used outdoors often receives chemical treatments to protect it from insects, moisture, and decay.
Finishing may include sanding, staining, or painting to enhance the lumber’s appearance and durability.
These additional steps help in extending the life of the wood and improving its aesthetic qualities.
Packing and Shipping
Once the lumber has been cut, dried, graded, and treated, it is packed for shipping.
Lumber is often bundled and strapped together to make handling and transportation easier.
Proper labeling ensures that the origin, grade, and type of wood are clear.
Transportation to its final destination usually involves trucks, but trains and ships are also used, depending on the quantity and destination.
Efficient packing and shipping methods are essential to maintain the quality of the lumber.
Final Thoughts
The journey of transforming a tree into usable lumber is complex and involves multiple stages.
From logging and transportation to sawing, drying, and finishing, each step is crucial for producing high-quality lumber.
Understanding this process helps us appreciate the value of wood products beyond their appearance and utility.
Remember, responsible logging and efficient manufacturing are key to sustainable forest management and long-term availability of quality lumber.
資料ダウンロード
QCD調達購買管理クラウド「newji」は、調達購買部門で必要なQCD管理全てを備えた、現場特化型兼クラウド型の今世紀最高の購買管理システムとなります。
ユーザー登録
調達購買業務の効率化だけでなく、システムを導入することで、コスト削減や製品・資材のステータス可視化のほか、属人化していた購買情報の共有化による内部不正防止や統制にも役立ちます。
NEWJI DX
製造業に特化したデジタルトランスフォーメーション(DX)の実現を目指す請負開発型のコンサルティングサービスです。AI、iPaaS、および先端の技術を駆使して、製造プロセスの効率化、業務効率化、チームワーク強化、コスト削減、品質向上を実現します。このサービスは、製造業の課題を深く理解し、それに対する最適なデジタルソリューションを提供することで、企業が持続的な成長とイノベーションを達成できるようサポートします。
オンライン講座
製造業、主に購買・調達部門にお勤めの方々に向けた情報を配信しております。
新任の方やベテランの方、管理職を対象とした幅広いコンテンツをご用意しております。
お問い合わせ
コストダウンが利益に直結する術だと理解していても、なかなか前に進めることができない状況。そんな時は、newjiのコストダウン自動化機能で大きく利益貢献しよう!
(Β版非公開)