- お役立ち記事
- For design leaders in the industrial burner ignition electrode manufacturing industry! Designed for both heat resistance and stability
For design leaders in the industrial burner ignition electrode manufacturing industry! Designed for both heat resistance and stability
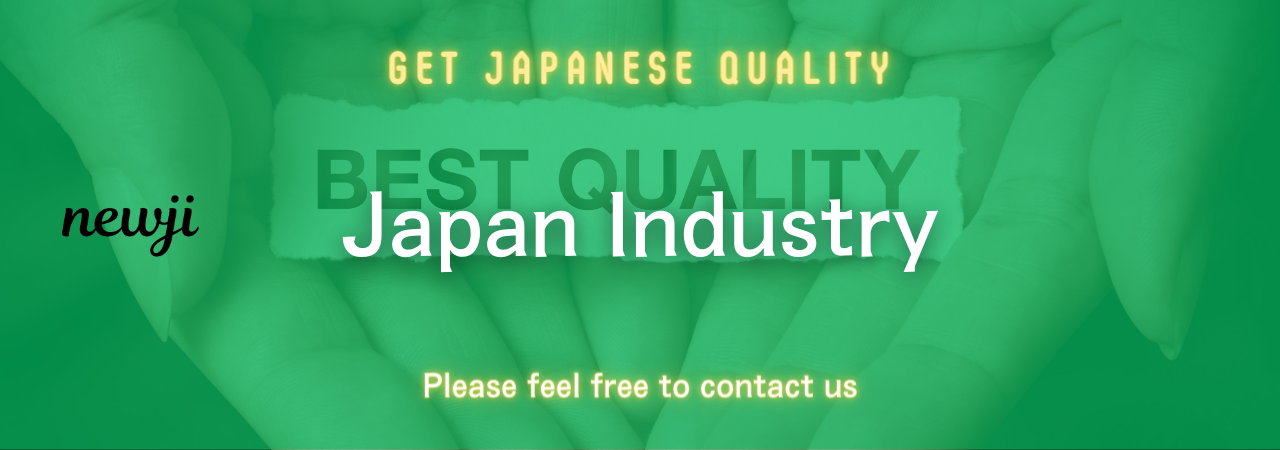
目次
The Importance of Industrial Burner Ignition Electrodes
In industrial applications, the need for efficient and reliable performance is paramount.
At the heart of many industrial heating systems lies the ignition electrode.
These components are crucial for initiating and sustaining combustion within industrial burners.
Manufacturers in the industrial burner ignition electrode sector continuously strive to enhance their designs.
The goal is to deliver components that can withstand extreme conditions while maintaining stability.
Understanding the Role of Ignition Electrodes
Ignition electrodes serve as the spark-generating elements that ignite fuel-air mixtures in burners.
Their primary function is to provide the necessary spark to initiate combustion, ensuring the burner operates efficiently.
Without a properly functioning ignition electrode, the burner might fail to start or could cause safety concerns due to improper ignition.
Furthermore, ignition electrodes must be designed to withstand high temperatures and harsh environments.
These conditions can wear out lesser materials, leading to premature failures and system downtimes.
Hence, the materials and design of these electrodes are critical for maintaining operational efficiency and safety.
Challenges Faced by Design Leaders
In the industrial burner ignition electrode manufacturing industry, design leaders face several challenges.
They must balance performance with durability and cost-effectiveness.
To meet these demands, design leaders require an in-depth understanding of both the physical stresses the electrodes will face and the specific requirements of different industrial applications.
One significant challenge is ensuring heat resistance.
Industrial burners often operate at very high temperatures, requiring electrodes that can endure without degrading or losing functionality.
This challenge necessitates specialized materials that can maintain integrity even under extreme heat.
Additionally, stability is another critical factor.
Stability ensures that the ignition process is not only reliable but also repeatable under varying conditions.
Materials and Engineering Solutions
To address these challenges, manufacturers innovatively use materials that enhance both heat resistance and stability.
Commonly used materials include nickel, tungsten, and certain ceramic compounds.
These materials are selected for their ability to withstand extreme temperatures while maintaining structural integrity.
Manufacturers may also incorporate innovative design features such as protective coatings.
These coatings can shield the electrode from oxidation and other chemical reactions that occur at high temperatures.
Such enhancements prolong the life of the electrode, reducing the frequency of replacements and maintenance.
By focusing on engineering solutions that cater to specific industrial requirements, design leaders can achieve a balance between performance and longevity.
Some designs also incorporate flexibility, allowing the electrode to function in different burner types and settings.
Sustaining Industrial Efficiency
In any industrial setting, efficiency matters.
A burner ignition system that works efficiently translates into reduced energy consumption and lower operational costs.
High-performance ignition electrodes are key to achieving such efficiency.
For operators and end-users, the assurance that a burner will ignite reliably on the first try is not only a matter of performance but also safety.
Any delay or failure in ignition could have significant repercussions, including equipment damage or safety hazards.
By prioritizing the design of ignition electrodes for both heat resistance and stability, manufacturers ensure that their products support consistent and efficient system operations.
This commitment evolves into a competitive advantage, offering end-users peace of mind and manufacturers a stronger position in the market.
Case Study: Successful Design Implementation
Consider a factory setting where high-temperature furnaces are used.
A leading manufacturer, recognizing the need for enhanced durability and stability, redesigned their ignition electrodes.
By using a proprietary ceramic composite, they extended the operational lifespan of these electrodes by 30%.
This change reduced maintenance intervals and improved system uptime significantly.
The design not only met the required performance specifications but also exceeded customer expectations.
Such success stories highlight the importance of innovative design approaches in overcoming industry challenges.
Future Trends in Ignition Electrode Design
As industries evolve, so too will the demands on ignition electrodes.
Future trends are likely to focus on additional enhancements in materials.
Improving resistance to both thermal and chemical degradation will remain a focus.
There may also be increased interest in smart technologies that allow for monitoring and predictive maintenance.
The use of data and analytics could revolutionize the way these components are maintained and replaced.
For example, electrodes could be equipped with sensors that provide real-time feedback on their condition and performance.
Such advancements would help in preemptively addressing potential failures and further optimizing burner operations.
Design leaders must stay abreast of these trends to remain competitive.
Investing in research and development will be crucial to developing the next generation of industrial burner ignition electrodes.
Conclusion
For those involved in the design and manufacture of ignition electrodes, the task is both complex and critical.
Ensuring heat resistance and stability is more than an engineering challenge; it is about delivering value to industrial users.
Through innovation and a commitment to quality and performance, design leaders can ensure the longevity and reliability of their products.
As the industry moves forward, those who prioritize these elements will likely lead the charge in driving efficiency and safety in industrial burners.
資料ダウンロード
QCD調達購買管理クラウド「newji」は、調達購買部門で必要なQCD管理全てを備えた、現場特化型兼クラウド型の今世紀最高の購買管理システムとなります。
ユーザー登録
調達購買業務の効率化だけでなく、システムを導入することで、コスト削減や製品・資材のステータス可視化のほか、属人化していた購買情報の共有化による内部不正防止や統制にも役立ちます。
NEWJI DX
製造業に特化したデジタルトランスフォーメーション(DX)の実現を目指す請負開発型のコンサルティングサービスです。AI、iPaaS、および先端の技術を駆使して、製造プロセスの効率化、業務効率化、チームワーク強化、コスト削減、品質向上を実現します。このサービスは、製造業の課題を深く理解し、それに対する最適なデジタルソリューションを提供することで、企業が持続的な成長とイノベーションを達成できるようサポートします。
オンライン講座
製造業、主に購買・調達部門にお勤めの方々に向けた情報を配信しております。
新任の方やベテランの方、管理職を対象とした幅広いコンテンツをご用意しております。
お問い合わせ
コストダウンが利益に直結する術だと理解していても、なかなか前に進めることができない状況。そんな時は、newjiのコストダウン自動化機能で大きく利益貢献しよう!
(Β版非公開)