- お役立ち記事
- For leaders in equipment management departments! Basics and practical methods for effectively promoting TPM activities
月間76,176名の
製造業ご担当者様が閲覧しています*
*2025年3月31日現在のGoogle Analyticsのデータより
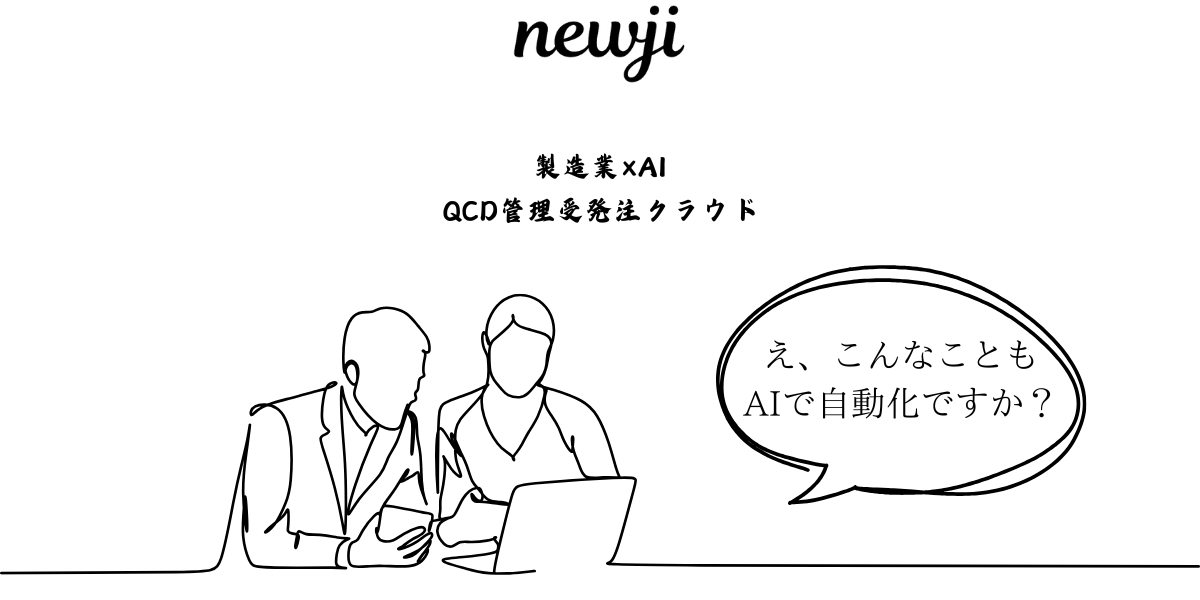
For leaders in equipment management departments! Basics and practical methods for effectively promoting TPM activities
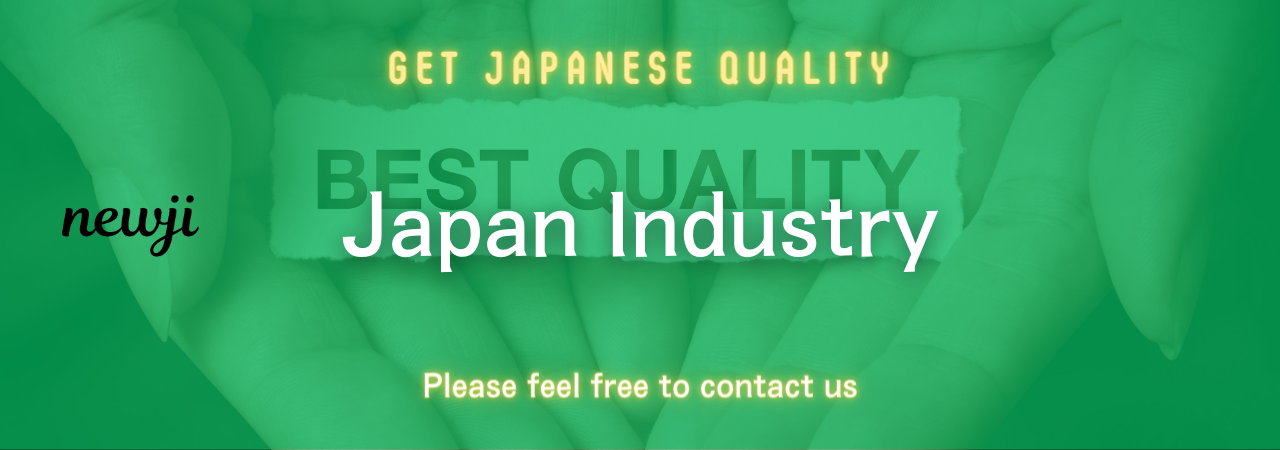
目次
Understanding TPM and Its Importance
Total Productive Maintenance (TPM) is a comprehensive approach to equipment maintenance that strives to achieve perfect production without breakdowns, defects, or accidents.
Originally developed in Japan, TPM is a vital component in enhancing the productivity and efficiency of manufacturing operations.
For leaders in equipment management departments, having a solid grasp of TPM basics and practical methods is crucial for effectively promoting these activities within their organizations.
The Pillars of TPM
TPM is built on eight foundational pillars, each designed to maximize the efficiency and reliability of equipment.
Understanding these pillars will provide leaders with a framework for implementing and sustaining TPM in their operations.
1. **Autonomous Maintenance**: Encourages operators to take responsibility for routine maintenance tasks such as cleaning, lubricating, and inspecting their equipment.
This involvement helps to build ownership and awareness of equipment conditions among operators.
2. **Planned Maintenance**: Focuses on scheduling maintenance activities to prevent unexpected breakdowns.
By analyzing equipment history and performance, maintenance can be planned effectively, reducing downtime and extending equipment lifespan.
3. **Quality Maintenance**: Aims to integrate quality assurance processes into equipment maintenance.
This involves enhancing equipment performance to prevent defects and reduce the production of faulty products.
4. **Focused Improvement**: Encourages cross-functional teams to identify and eliminate losses in equipment efficiency.
By empowering employees to work collaboratively on problem-solving, organizations can achieve significant gains in productivity.
5. **Early Equipment Management**: Incorporates maintenance perspectives into the design and installation of new equipment.
By considering maintenance needs early, organizations can ensure that new machines are easy to maintain and operate.
6. **Training and Education**: Provides operators and maintenance personnel with the skills and knowledge they need to manage equipment effectively.
A well-educated workforce is essential to sustain TPM activities and continuous improvement.
7. **Safety, Health, and Environment**: Emphasizes the importance of maintaining a safe and healthy working environment.
Incorporating safety practices into all maintenance activities helps to prevent accidents and promote a culture of safety.
8. **Office TPM**: Extends TPM practices to administrative functions.
This involves eliminating waste and improving efficiency in office processes to support overall productivity goals.
Practical Methods for Implementing TPM
Implementing TPM successfully requires a strategic approach and the commitment of everyone within the organization.
Below are practical methods to effectively promote and sustain TPM activities.
Gaining Management Support
For TPM to be successful, it requires strong support from top management.
Leaders must communicate the benefits of TPM clearly and align it with the organization’s strategic objectives.
Management should be actively involved in promoting TPM by providing the necessary resources and demonstrating a commitment to continuous improvement.
Conducting TPM Training
Training is a fundamental component of TPM implementation.
It’s important to organize comprehensive training programs that cover the TPM principles, objectives, and practical applications.
Training sessions should be tailored to different audiences, including operators, maintenance teams, and management personnel.
With proper training, employees will be empowered to contribute to TPM activities effectively.
Establishing TPM Teams
Creating cross-functional TPM teams is critical for success.
These teams should be responsible for driving TPM initiatives, identifying improvement opportunities, and facilitating communications among stakeholders.
By involving employees from different departments, organizations can leverage diverse perspectives and experiences to solve problems more efficiently.
Implementing a Pilot Project
Before rolling out TPM across the entire organization, it is advisable to start with a pilot project.
Select a specific area or piece of equipment as a test case for implementing TPM practices.
This allows the team to learn, refine, and demonstrate the effectiveness of TPM on a smaller scale before larger-scale implementation.
Tracking and Measuring Progress
It’s essential to establish metrics and KPIs to measure the success of TPM activities.
Key performance indicators may include equipment downtime, maintenance costs, and quality defect rates.
Regularly tracking and analyzing these metrics can help identify areas for improvement and ensure that TPM goals are being met.
Promoting a Culture of Continuous Improvement
TPM is not a one-time initiative but a continuous journey of improvement.
Fostering a culture that encourages continuous learning, open communication, and problem-solving is vital.
Regular meetings and feedback sessions can help sustain enthusiasm and ensure that everyone remains focused on achieving TPM goals.
Overcoming Challenges in TPM Implementation
While TPM offers numerous benefits, implementing it effectively can sometimes be challenging.
Facilitators must be prepared to tackle these obstacles head-on.
Some common challenges include resistance to change, lack of time, and insufficient resources.
Addressing resistance can be accomplished through effective communication that highlights the benefits of TPM.
Time constraints and resource limitations can be mitigated by developing a realistic implementation plan that gradually integrates TPM activities into daily operations.
The Role of Technology in TPM
Technological advancements play a crucial role in supporting TPM strategies.
For instance, predictive maintenance tools can help collect and analyze data to predict equipment failures before they occur.
Digital platforms can facilitate better communication, collaboration, and training, making TPM initiatives more efficient and widespread.
Conclusion
For leaders in equipment management departments, understanding and promoting TPM activities is essential for improving productivity, efficiency, and safety in manufacturing operations.
By applying practical methods and addressing implementation challenges, organizations can successfully harness the full potential of TPM.
Continued commitment to these practices will not only enhance equipment reliability but also contribute to a more engaged and proactive workforce.
資料ダウンロード
QCD管理受発注クラウド「newji」は、受発注部門で必要なQCD管理全てを備えた、現場特化型兼クラウド型の今世紀最高の受発注管理システムとなります。
ユーザー登録
受発注業務の効率化だけでなく、システムを導入することで、コスト削減や製品・資材のステータス可視化のほか、属人化していた受発注情報の共有化による内部不正防止や統制にも役立ちます。
NEWJI DX
製造業に特化したデジタルトランスフォーメーション(DX)の実現を目指す請負開発型のコンサルティングサービスです。AI、iPaaS、および先端の技術を駆使して、製造プロセスの効率化、業務効率化、チームワーク強化、コスト削減、品質向上を実現します。このサービスは、製造業の課題を深く理解し、それに対する最適なデジタルソリューションを提供することで、企業が持続的な成長とイノベーションを達成できるようサポートします。
製造業ニュース解説
製造業、主に購買・調達部門にお勤めの方々に向けた情報を配信しております。
新任の方やベテランの方、管理職を対象とした幅広いコンテンツをご用意しております。
お問い合わせ
コストダウンが利益に直結する術だと理解していても、なかなか前に進めることができない状況。そんな時は、newjiのコストダウン自動化機能で大きく利益貢献しよう!
(β版非公開)