- お役立ち記事
- For leaders in equipment management departments in the steel industry! A thorough method for detecting bearing abnormalities using vibration diagnosis
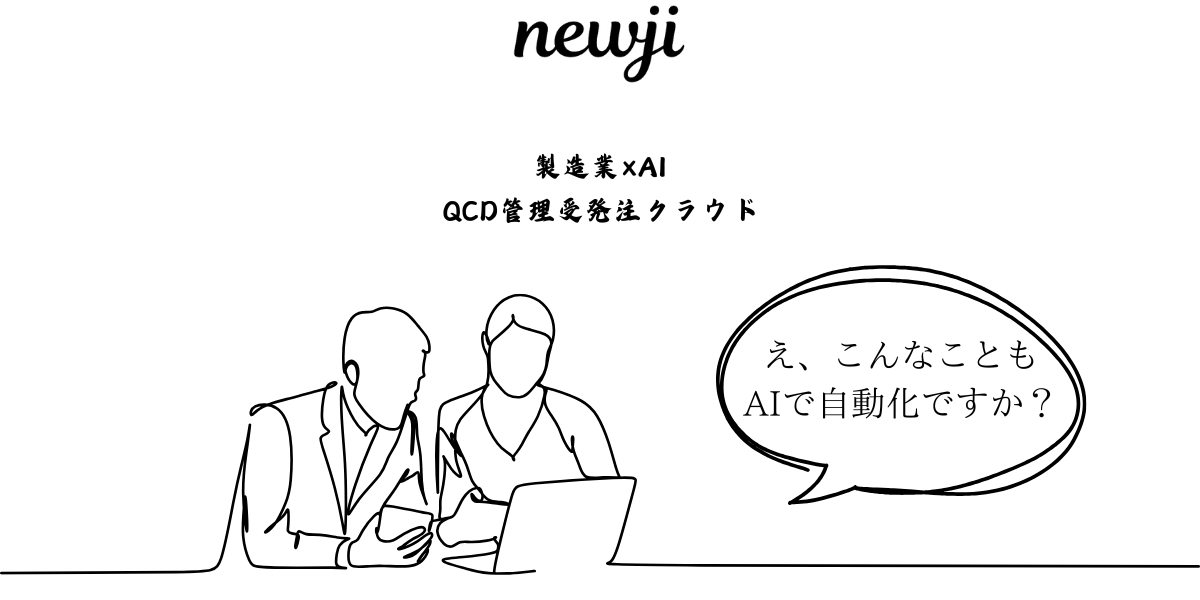
For leaders in equipment management departments in the steel industry! A thorough method for detecting bearing abnormalities using vibration diagnosis
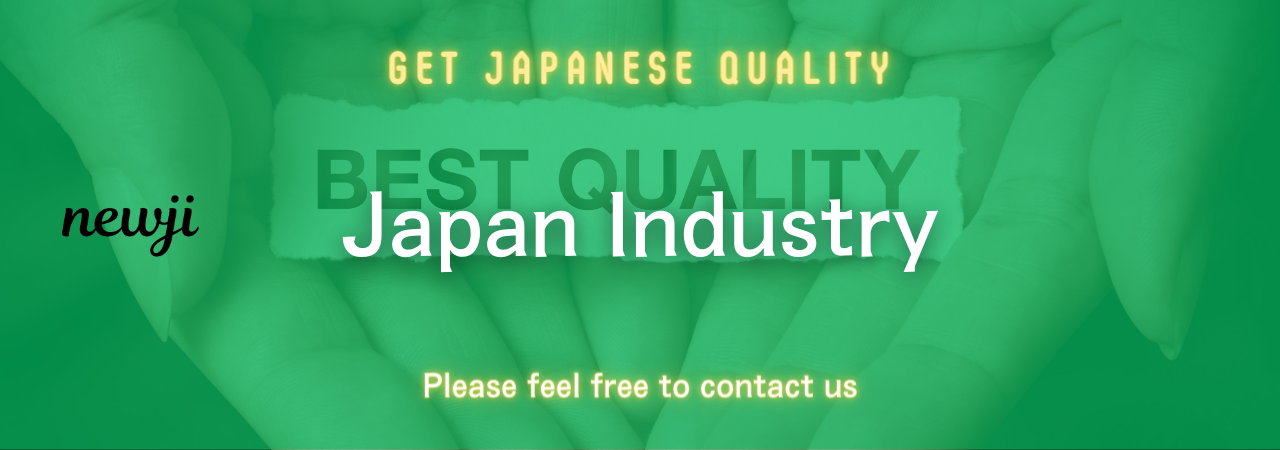
目次
Understanding Bearing Abnormalities in Equipment Management
In the steel industry, maintaining the efficiency and smooth operation of machinery is crucial.
One of the key components that can significantly impact the operational reliability of equipment is the bearing.
Bearings play a vital role in reducing friction and supporting various moving parts within machinery.
However, when they malfunction, it can lead to severe disruptions and costly downtimes.
For leaders in equipment management departments, detecting bearing abnormalities early is essential to prevent larger issues from arising.
One effective method of identifying disturbances in bearings is through vibration diagnosis.
This article will delve into the significance of bearing abnormalities, the principles of vibration diagnosis, and how this method can be implemented in your equipment management strategy.
The Importance of Bearings in the Steel Industry
Bearings are critical components that allow parts of machinery to move smoothly and efficiently.
In the steel industry, where equipment operates under high pressure and heavy loads, bearings are essential to maintaining the speed and load capabilities of devices.
If a bearing in a major piece of equipment fails, it can halt production and lead to significant financial losses.
Therefore, maintaining these components is a top priority for equipment management leaders.
Understanding their significance and potential impact when they fail helps in prioritizing maintenance activities and investing in diagnostic tools that can prolong their life.
Principles of Vibration Diagnosis
Vibration diagnosis is a valuable technique used to detect irregularities in machinery components, including bearings.
This method involves measuring the vibration signals emitted by machinery to assess its operational condition.
Each piece of equipment has a normal vibration signature, and deviations from this can indicate potential issues.
Key principles of vibration diagnosis include:
– **Signal Measurement**: Sensors are installed at strategic points on machinery to capture vibration signals.
These signals are then analyzed to identify any changes from the baseline.
– **Frequency Analysis**: By examining the frequency of the captured signals, technicians can detect abnormalities within the bearings.
Different types of faults, such as misalignment or wear, leave distinctive patterns in the frequency data.
– **Amplitude Analysis**: Changes in the amplitude of vibration can also indicate potential problems.
Higher amplitudes can signal excessive wear or developing faults in bearings.
Vibration diagnosis leverages these principles to provide early warnings about potential failures, enabling timely maintenance and repairs.
Benefits of Vibration Diagnosis in Detecting Bearings Issues
Implementing vibration diagnosis offers several advantages to the equipment management departments within the steel industry:
– **Early Detection**: Vibration diagnosis allows for the identification of issues before they evolve into major problems.
Detecting faults early means repairs can be planned with minimal disruption to operations.
– **Cost Savings**: Early detection and intervention can prevent unexpected failures that result in costly downtime and extensive repairs.
Regular monitoring can extend the lifespan of bearings, reducing the need for frequent replacements.
– **Improved Safety**: Faulty bearings can lead to catastrophic equipment failures, posing safety risks to personnel.
By using vibration diagnosis, potential failures can be mitigated, ensuring a safer work environment.
– **Enhanced Maintenance Strategies**: With detailed data on machinery conditions, maintenance can be more predictive rather than reactive.
This optimizes maintenance schedules and resource allocation, enhancing overall operational efficiency.
Implementing Vibration Diagnosis in Your Equipment Management Strategy
Introducing vibration diagnosis into your equipment management practices involves several steps.
These ensure that you capitalize on the benefits of this diagnostic tool:
– **Training and Skill Development**: Equip your team with the necessary skills to interpret vibration data.
Invest in training sessions and workshops to build a solid foundation in vibration analysis.
– **Invest in Quality Sensors**: Select high-quality vibration sensors appropriate for your specific machinery.
These instruments should be durable and provide accurate readings for reliable analysis.
– **Establish Baseline Measurements**: Conduct initial vibration measurements when the equipment is in optimal condition.
This data serves as a baseline for comparison during regular monitoring sessions.
– **Regular Monitoring**: Implement a routine vibration monitoring schedule to consistently evaluate equipment conditions.
Regular checks help in identifying trends and any gradual changes in vibration patterns.
– **Collaborate with Experts**: Work with vibration analysis specialists to ensure precise diagnosis and interpretation of data.
These experts can provide insights that enhance your maintenance decision-making processes.
Overcoming Challenges in Vibration Diagnosis
Despite its advantages, there are challenges in employing vibration diagnosis.
Understanding these can help in developing strategies to overcome them:
– **Interference from Environmental Noise**: External factors can affect vibration signals.
Ensure that sensors are correctly calibrated and environmental noise is minimized during diagnostics.
– **Data Overload**: Collecting vibration data generates significant amounts of information.
Focus on critical parameters and trends relevant to your bearings to avoid being overwhelmed by excessive data.
– **Initial Investment Costs**: While there’s an upfront cost for acquiring equipment and training, consider this as an investment towards long-term operational efficiency and cost savings.
In conclusion, vibration diagnosis is a crucial technique for detecting bearing abnormalities, offering numerous benefits to equipment management in the steel industry.
By embracing this method and overcoming its challenges, leaders can ensure efficient machinery operation, prolong bearing life, and minimize costly downtimes.
資料ダウンロード
QCD調達購買管理クラウド「newji」は、調達購買部門で必要なQCD管理全てを備えた、現場特化型兼クラウド型の今世紀最高の購買管理システムとなります。
ユーザー登録
調達購買業務の効率化だけでなく、システムを導入することで、コスト削減や製品・資材のステータス可視化のほか、属人化していた購買情報の共有化による内部不正防止や統制にも役立ちます。
NEWJI DX
製造業に特化したデジタルトランスフォーメーション(DX)の実現を目指す請負開発型のコンサルティングサービスです。AI、iPaaS、および先端の技術を駆使して、製造プロセスの効率化、業務効率化、チームワーク強化、コスト削減、品質向上を実現します。このサービスは、製造業の課題を深く理解し、それに対する最適なデジタルソリューションを提供することで、企業が持続的な成長とイノベーションを達成できるようサポートします。
オンライン講座
製造業、主に購買・調達部門にお勤めの方々に向けた情報を配信しております。
新任の方やベテランの方、管理職を対象とした幅広いコンテンツをご用意しております。
お問い合わせ
コストダウンが利益に直結する術だと理解していても、なかなか前に進めることができない状況。そんな時は、newjiのコストダウン自動化機能で大きく利益貢献しよう!
(Β版非公開)