- お役立ち記事
- For leaders in the design department of the foundry ceramic mold manufacturing industry! Molding technology that achieves both high precision and heat resistance
月間76,176名の
製造業ご担当者様が閲覧しています*
*2025年3月31日現在のGoogle Analyticsのデータより
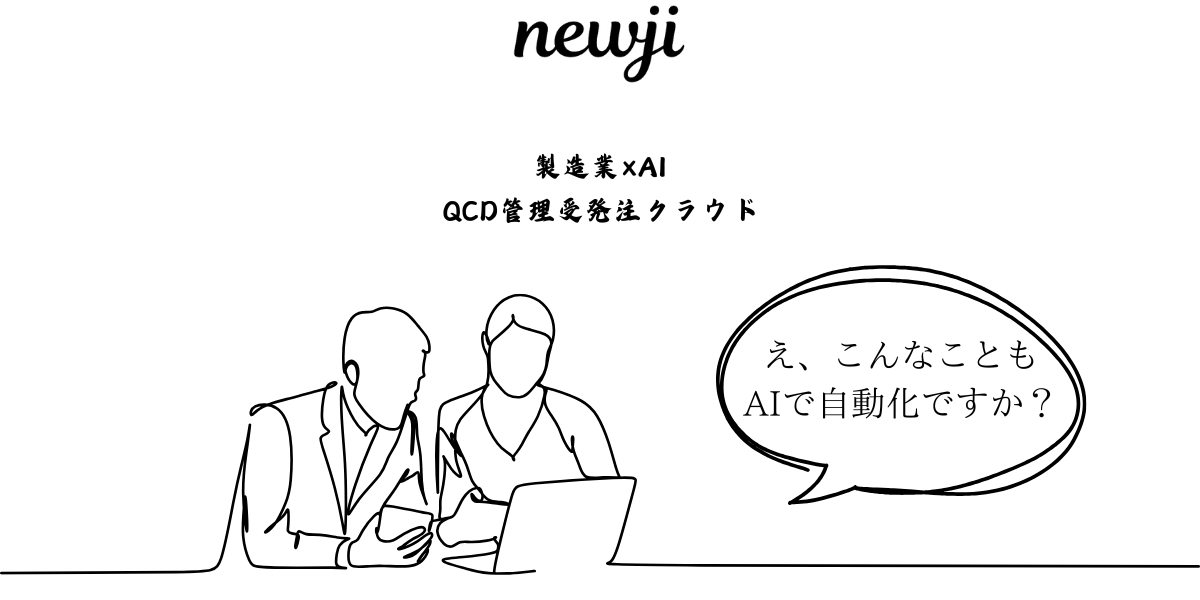
For leaders in the design department of the foundry ceramic mold manufacturing industry! Molding technology that achieves both high precision and heat resistance
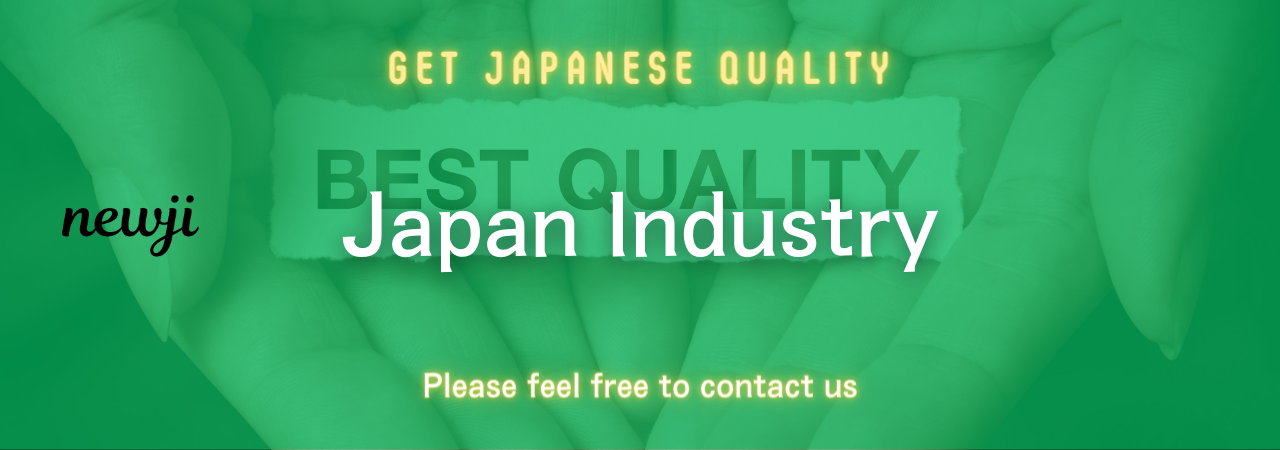
目次
Understanding the Basics of Molding Technology
The foundry ceramic mold manufacturing industry relies on advanced molding technology to produce high-quality, precise, and heat-resistant molds.
At its core, molding technology involves creating a unique mold design that can withstand the high temperatures of metal casting while maintaining strict dimensional accuracy.
The Role of Ceramic Molds
Ceramic molds are a critical component in the foundry industry.
Unlike other materials, ceramics offer superior heat resistance, making them ideal for casting metals at high temperatures.
Moreover, ceramic molds provide exceptional dimensional stability, ensuring that the final cast product meets the desired specifications.
High Precision in Ceramic Molding
Achieving high precision in ceramic mold manufacturing requires a thorough understanding of the materials and processes involved.
Precision is not just about accuracy but also about consistency, which is vital for ensuring that each cast product is identical.
Material Selection
Choosing the right materials is the first step in achieving high precision.
The composition of the ceramic must be carefully selected to ensure optimal performance under specific casting conditions.
Factors such as thermal expansion, mold strength, and permeability must be considered.
Advanced Molding Techniques
Employing advanced molding techniques can significantly enhance precision.
Techniques such as 3D printing and computer-aided design (CAD) allow for the creation of complex mold geometries with high accuracy.
These technologies also reduce human error, leading to more consistent results.
Ensuring Heat Resistance
Heat resistance is another critical factor in the performance of ceramic molds.
A mold that lacks heat resistance can lead to defects in the cast product.
Here are some ways to ensure that ceramic molds remain stable at high temperatures.
Additives and Coatings
Adding specific compounds or coatings to the ceramic material can enhance its heat resistance.
For instance, zirconium silicate coatings increase the refractoriness of the ceramic mold, enabling it to withstand extreme temperatures without deformation.
Optimizing Mold Design
The design of the mold itself can contribute to improved heat resistance.
Incorporating features such as cooling channels or heat sinks can help manage the thermal load, preventing overheating and maintaining structural integrity.
Challenges and Solutions in Molding Technology
The foundry ceramic mold manufacturing industry faces several challenges in balancing high precision with heat resistance.
However, understanding these challenges allows for the development of effective solutions.
Handling Material Limitations
Ceramic materials can be brittle, leading to the risk of cracking or breaking during the casting process.
To address this, manufacturers often explore composite materials or reinforce ceramic molds with metal frameworks for added durability.
Minimizing Casting Defects
Defects such as shrinkage, gas porosity, and surface roughness can undermine the quality of the cast product.
Implementing strict quality control measures and adopting advanced analytical tools can help identify potential defects early in the process, allowing for timely corrections.
Future Trends in Ceramic Molding Technology
The future of molding technology in the foundry ceramic mold manufacturing industry holds promise for even greater advancements.
Continuous research and innovation are driving the development of new materials and techniques that enhance both precision and heat resistance.
Exploring New Materials
Researchers are exploring new ceramic composites that offer improved thermal and mechanical properties.
Nanotechnology, in particular, presents exciting possibilities for creating materials with enhanced performance at the nanoscale level.
Automation and Digitalization
The adoption of automation and digitalization is transforming the industry.
Smart manufacturing systems and IoT-enabled devices allow for real-time monitoring and control of the molding process, leading to higher efficiency and lower production costs.
In conclusion, leaders in the design department of the foundry ceramic mold manufacturing industry must stay abreast of the latest developments in molding technology.
By understanding the intricacies of material selection, designing for precision, and enhancing heat resistance, they can achieve the dual goals of producing molds that are both high precision and heat resistant.
As the industry evolves, leveraging advancements in materials science and digital technology will be key to staying competitive and meeting the demands of future casting applications.
資料ダウンロード
QCD管理受発注クラウド「newji」は、受発注部門で必要なQCD管理全てを備えた、現場特化型兼クラウド型の今世紀最高の受発注管理システムとなります。
ユーザー登録
受発注業務の効率化だけでなく、システムを導入することで、コスト削減や製品・資材のステータス可視化のほか、属人化していた受発注情報の共有化による内部不正防止や統制にも役立ちます。
NEWJI DX
製造業に特化したデジタルトランスフォーメーション(DX)の実現を目指す請負開発型のコンサルティングサービスです。AI、iPaaS、および先端の技術を駆使して、製造プロセスの効率化、業務効率化、チームワーク強化、コスト削減、品質向上を実現します。このサービスは、製造業の課題を深く理解し、それに対する最適なデジタルソリューションを提供することで、企業が持続的な成長とイノベーションを達成できるようサポートします。
製造業ニュース解説
製造業、主に購買・調達部門にお勤めの方々に向けた情報を配信しております。
新任の方やベテランの方、管理職を対象とした幅広いコンテンツをご用意しております。
お問い合わせ
コストダウンが利益に直結する術だと理解していても、なかなか前に進めることができない状況。そんな時は、newjiのコストダウン自動化機能で大きく利益貢献しよう!
(β版非公開)