- お役立ち記事
- For leaders in the design department of the jet nozzle manufacturing industry for cleaning equipment! Designed to maintain uniform spray and durability
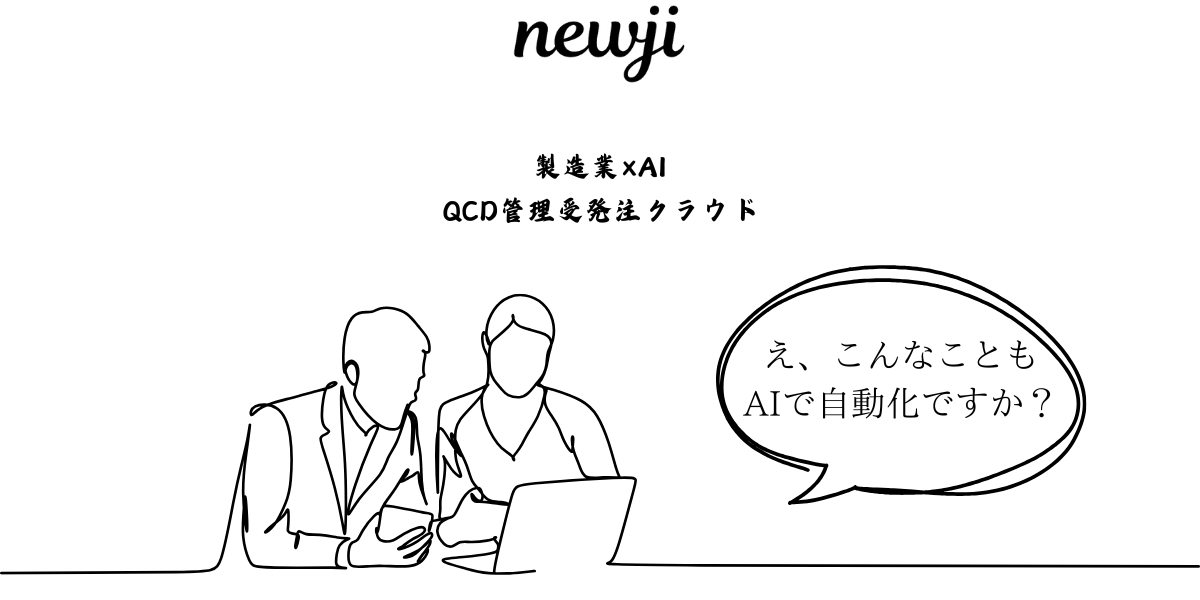
For leaders in the design department of the jet nozzle manufacturing industry for cleaning equipment! Designed to maintain uniform spray and durability
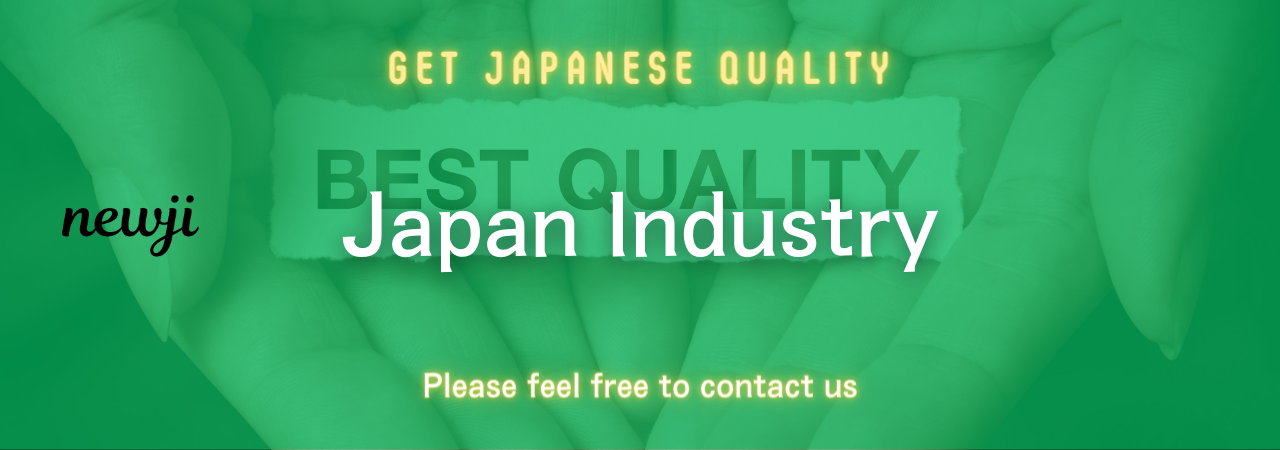
目次
Understanding Jet Nozzle Design
Jet nozzles are a crucial component in cleaning equipment across various industries.
They play a vital role in ensuring efficient and effective cleaning operations by controlling the spray pattern, velocity, and impact force of the cleaning fluid.
For leaders in the design department within the jet nozzle manufacturing industry, understanding the intricacies of jet nozzle design is essential to ensure products meet both performance and durability expectations.
Designs must maintain a balance between delivering a uniform spray and withstanding the rigors of continuous use.
This article delves into the essential considerations in jet nozzle design and how they contribute to maintaining uniform spray characteristics and overall durability.
The Importance of Uniform Spray
Uniform spray is fundamental in any cleaning process.
An even distribution of the cleaning fluid ensures that all areas within the targeted cleaning zone are adequately covered, resulting in more efficient cleaning operations.
For designers, achieving uniform spray requires careful consideration of nozzle parameters, including its shape, size, orifice design, and the angle at which the fluid exits the nozzle.
Factors Affecting Uniform Spray
Several factors need to be taken into account when designing jet nozzles to maintain uniform spray patterns.
Among these, the hydraulic flow rate and pressure, fluid properties, and environmental conditions play significant roles.
The hydraulic flow rate and pressure, in particular, influence the velocity and coverage of the spray.
Manufacturers should conduct extensive testing to fine-tune these parameters, ensuring that the nozzle delivers a consistent and even spray across a wide range of operating conditions.
Orifice Design
The orifice design of a jet nozzle is another critical factor affecting spray uniformity.
The shape and size of the orifice determine the pattern and size of the spray.
An optimal orifice design enables the nozzle to produce a consistent spray pattern, minimizing overspray or underspray, which can lead to inefficient cleaning.
Great detail must be given to the geometry and precision of the nozzle’s orifice design.
Advancements in manufacturing technologies, such as precision machining and 3D printing, offer engineers the ability to design exceptionally accurate and efficient orifices.
Durability in Jet Nozzle Design
While achieving uniform spray is crucial, ensuring that the nozzles are durable enough to withstand prolonged usage without degradation is also essential.
Jet nozzles are exposed to various physical and chemical stresses during operation, which can affect their longevity and performance over time.
Material Selection
Material selection is fundamental in enhancing the durability of jet nozzles.
Materials must be chosen based on their ability to resist wear, corrosion, and chemical damage.
Common materials like stainless steel, ceramics, and high-performance polymers are often used due to their robust properties.
Each material has its pros and cons, and selecting the right material involves balancing the cost against desired performance characteristics.
Stainless steel, for example, offers excellent durability and corrosion resistance but might be cost-prohibitive for certain applications.
Conversely, high-performance polymers may not offer the same level of durability but are lighter and less expensive.
Coatings and Surface Treatments
Coatings and surface treatments can significantly enhance the durability of jet nozzles.
Applying specialized coatings that resist chemical and environmental degradation can extend the lifespan of nozzles and maintain their performance.
These treatments provide an additional layer of protection against abrasive and corrosive substances encountered during cleaning operations.
Engineers must consider the operating environment of the nozzles and choose coatings and treatments that best meet the demands of that environment.
Balancing Design for Optimal Performance
The complexity of jet nozzle design lies in achieving a balance between uniform spray and durability.
A design optimized for one can inadvertently compromise the other if not carefully balanced.
Designers must engage in a multifaceted approach that includes rigorous testing, simulation, and feedback from end-users.
This ensures that the jet nozzles manufactured not only meet but exceed industry standards.
Testing and Simulation
Extensive testing is vital in validating the performance of jet nozzle designs.
Utilizing modern simulation tools allows designers to predict how nozzles will perform under various conditions and make informed decisions.
Testing prototypes in real-world conditions further validates these designs, highlighting areas for improvement before mass production.
Innovative Design Practices
Adopting innovative design practices can also significantly enhance the performance and durability of jet nozzles.
Incorporating features such as self-cleaning capabilities and adjustable spray patterns add value by offering versatility and efficiency.
Innovation should be directed towards improving the ease of maintenance and replacement, reducing downtime, and enhancing the cleaning performance of the equipment.
Conclusion
For leaders in the design department of the jet nozzle manufacturing industry, the challenge lies in creating designs that harmonize uniform spray and durability.
A thoughtful approach to design, considering all aspects from material selection to orifice geometry, is crucial.
Advancements in technology and a commitment to innovation can further enhance the design process, ensuring that jet nozzles meet the diverse and demanding needs of the market.
By focusing on these key areas, manufacturers can produce high-quality jet nozzles that are both resilient and effective, ensuring superior cleaning capabilities for years to come.
資料ダウンロード
QCD調達購買管理クラウド「newji」は、調達購買部門で必要なQCD管理全てを備えた、現場特化型兼クラウド型の今世紀最高の購買管理システムとなります。
ユーザー登録
調達購買業務の効率化だけでなく、システムを導入することで、コスト削減や製品・資材のステータス可視化のほか、属人化していた購買情報の共有化による内部不正防止や統制にも役立ちます。
NEWJI DX
製造業に特化したデジタルトランスフォーメーション(DX)の実現を目指す請負開発型のコンサルティングサービスです。AI、iPaaS、および先端の技術を駆使して、製造プロセスの効率化、業務効率化、チームワーク強化、コスト削減、品質向上を実現します。このサービスは、製造業の課題を深く理解し、それに対する最適なデジタルソリューションを提供することで、企業が持続的な成長とイノベーションを達成できるようサポートします。
オンライン講座
製造業、主に購買・調達部門にお勤めの方々に向けた情報を配信しております。
新任の方やベテランの方、管理職を対象とした幅広いコンテンツをご用意しております。
お問い合わせ
コストダウンが利益に直結する術だと理解していても、なかなか前に進めることができない状況。そんな時は、newjiのコストダウン自動化機能で大きく利益貢献しよう!
(Β版非公開)