- お役立ち記事
- For leaders in the design department of the pharmaceutical manufacturing industry! Product design optimization using CAE analysis
For leaders in the design department of the pharmaceutical manufacturing industry! Product design optimization using CAE analysis
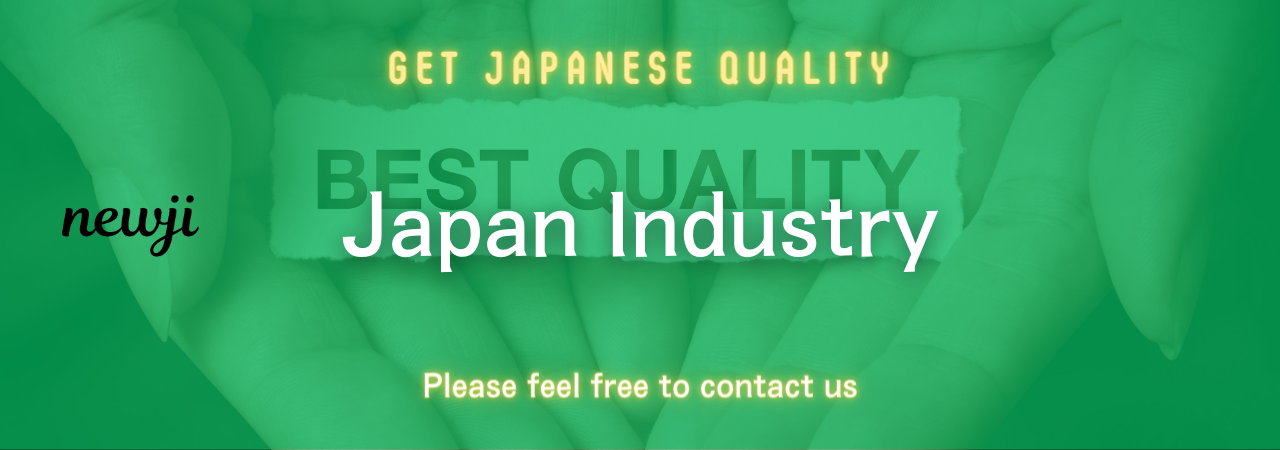
目次
Understanding CAE Analysis in Pharmaceutical Product Design
The field of pharmaceutical manufacturing is continuously evolving.
This evolution demands that design departments remain at the forefront of innovation, ensuring that high-quality products reach the market efficiently.
One of the key tools aiding design optimization in the industry is Computer-Aided Engineering (CAE) analysis.
CAE analysis plays a significant role in minimizing errors, reducing costs, and speeding up the design process.
AEA analysis refers to the use of computer software to simulate performance, analyze scenarios, and refine designs before physical prototypes are made.
This method accelerates the design process by allowing designers to virtually test different scenarios and identify potential issues early in the development phase.
For leaders in the design department of pharmaceutical manufacturing, understanding and implementing CAE analysis is critical for optimizing product design.
The Importance of CAE in Product Design
Pharmaceutical products must meet strict regulatory standards and undergo rigorous testing before they reach consumers.
This makes the optimization of product design crucial.
CAE analysis allows design teams to accurately predict how a product will behave under various conditions, thereby ensuring that the products are both effective and safe.
With CAE analysis, the design department can simulate different environments and stressors that a product might encounter during its lifecycle.
For instance, it can predict how a drug capsule might dissolve under varying conditions or how a medical device might perform under stress.
This ability to simulate and predict outcomes before physical testing reduces the number of iterations needed to reach a final design and helps avoid costly errors.
Benefits of Using CAE Analysis
Cost Reduction
One of the most significant advantages of integrating CAE analysis into the design process is the reduction in costs.
By simulating products digitally, companies can cut down on the resources spent on physical prototypes.
This reduction in prototype development leads to substantial cost savings, allowing funds to be allocated more efficiently across other critical areas of production.
Speeding Up the Design Process
Traditional product development processes can be lengthy, especially in a sector as heavily regulated as pharmaceuticals.
CAE analysis accelerates this process by providing immediate feedback on design and performance.
Designers can quickly iterate and refine products without waiting for physical prototypes to be constructed and tested.
Enhanced Product Performance
Through simulation, CAE analysis helps in fine-tuning the product design by identifying weaknesses or inefficiencies early on.
By addressing these issues at the design stage, the final products perform better, are safer for consumers, and are more likely to exceed regulatory expectations.
Implementing CAE in the Design Workflow
Leaders in pharmaceutical design departments must effectively integrate CAE analysis into their workflow to fully reap the benefits.
This integration requires strategic planning and a clear understanding of both the capabilities of CAE software and the specific needs of their design projects.
Investing in the Right Tools
Choosing the right CAE tools is crucial for successful implementation.
The chosen software should be capable of handling complex simulations and be user-friendly enough for the design team to adopt smoothly.
It’s also vital to ensure the software is regularly updated and supported, keeping pace with evolving industry requirements.
Training and Development
To maximize the utility of CAE tools, the design team should receive adequate training.
This training should not only cover how to use the software but also emphasize the importance of analysis in achieving design optimization.
Leaders should encourage continuous learning, enabling the team to stay updated with the latest trends and techniques in CAE analysis.
Collaboration Across Departments
The successful integration of CAE analysis should facilitate collaboration between design, engineering, and manufacturing departments.
By working together, these teams can provide valuable insights that lead to more innovative and efficient product designs.
Additionally, fostering interdepartmental communication helps ensure that the design meets all necessary compliance requirements and stakeholder expectations.
Overcoming Challenges in CAE Implementation
Implementing CAE analysis in the design department comes with its challenges.
One of the most common issues is the initial cost of setting up CAE technology, which can be prohibitive for some organizations.
However, when viewed as a long-term investment, the benefits often outweigh the costs.
Another challenge is the potential resistance to change from staff used to traditional design processes.
Leaders need to clearly communicate the advantages of CAE analysis and provide support to help ease the transition.
Finally, data management is crucial when using CAE analysis.
Companies must ensure that data is accurate, current, and secured, as incorrect or outdated data can compromise the simulation results.
Implementing robust data management systems and practices is essential to overcoming this hurdle.
Conclusion
For leaders in the pharmaceutical manufacturing industry, incorporating CAE analysis into the design department is key to optimizing product design.
Through the use of powerful simulations, CAE analysis offers significant cost savings, speeds up the design process, and improves the overall quality and performance of products.
By investing in the right tools and fostering a culture of continuous learning and collaboration, design departments can harness CAE analysis to stay competitive and innovative in a demanding industry.
資料ダウンロード
QCD調達購買管理クラウド「newji」は、調達購買部門で必要なQCD管理全てを備えた、現場特化型兼クラウド型の今世紀最高の購買管理システムとなります。
ユーザー登録
調達購買業務の効率化だけでなく、システムを導入することで、コスト削減や製品・資材のステータス可視化のほか、属人化していた購買情報の共有化による内部不正防止や統制にも役立ちます。
NEWJI DX
製造業に特化したデジタルトランスフォーメーション(DX)の実現を目指す請負開発型のコンサルティングサービスです。AI、iPaaS、および先端の技術を駆使して、製造プロセスの効率化、業務効率化、チームワーク強化、コスト削減、品質向上を実現します。このサービスは、製造業の課題を深く理解し、それに対する最適なデジタルソリューションを提供することで、企業が持続的な成長とイノベーションを達成できるようサポートします。
オンライン講座
製造業、主に購買・調達部門にお勤めの方々に向けた情報を配信しております。
新任の方やベテランの方、管理職を対象とした幅広いコンテンツをご用意しております。
お問い合わせ
コストダウンが利益に直結する術だと理解していても、なかなか前に進めることができない状況。そんな時は、newjiのコストダウン自動化機能で大きく利益貢献しよう!
(Β版非公開)