- お役立ち記事
- For managers of equipment maintenance departments in the steel industry! Safety diagnosis guidelines for high temperature equipment using infrared cameras
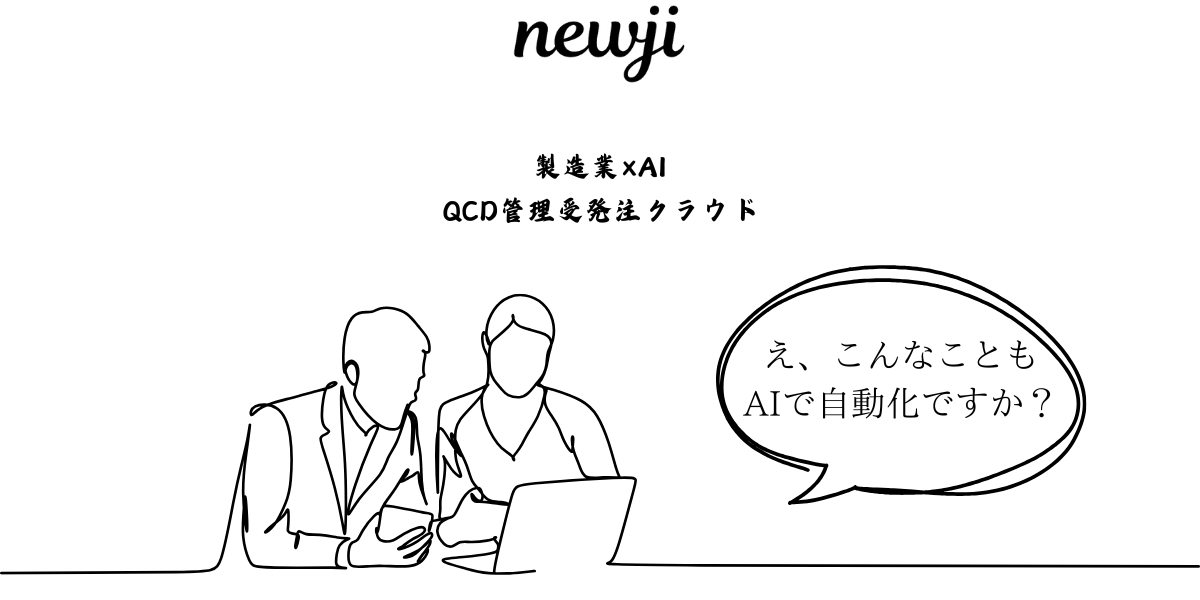
For managers of equipment maintenance departments in the steel industry! Safety diagnosis guidelines for high temperature equipment using infrared cameras
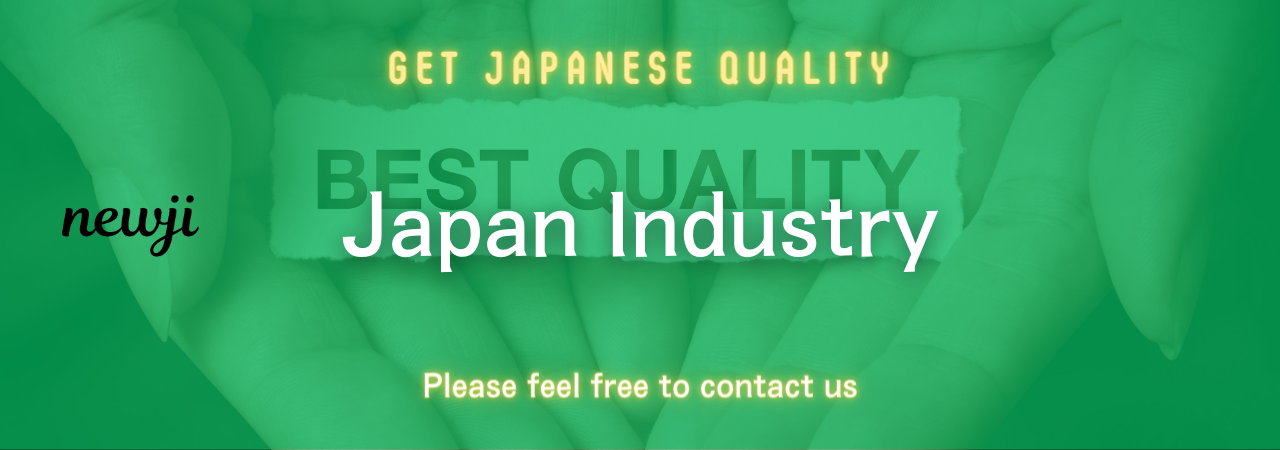
目次
Introduction to Infrared Cameras in Steel Industry
In the steel industry, ensuring the safety and reliability of high temperature equipment is of utmost importance.
High temperature equipment, such as furnaces, boilers, and heat exchangers, operate under extreme conditions and their failure can lead to catastrophic consequences.
To mitigate risks and maintain a safe working environment, equipment maintenance departments adopt various measures and technologies.
One technological advancement that has become essential in the safety diagnosis of high temperature equipment is the use of infrared cameras.
Infrared cameras provide non-contact, real-time thermal imaging of equipment, allowing for the early detection of potential issues.
This enables maintenance teams to take corrective actions before problems escalate, significantly reducing the risk of equipment failure and downtime.
Understanding the Benefits of Infrared Cameras
Infrared cameras offer several advantages over traditional inspection methods.
Firstly, they allow for the inspection of equipment while it is in operation, eliminating the need for shutdowns and preventing production losses.
Secondly, they enable the visualization of temperature differences on the surface of equipment, helping to identify hotspots, insulation failures, and blockages, which are common indicators of potential problems.
In addition, infrared cameras can be used to monitor a wide area in a single scan, providing a comprehensive view of the equipment’s condition.
This is particularly beneficial in industries like steel, where large-scale operations are common.
Furthermore, the data captured by infrared cameras can be documented and analyzed over time, allowing for trend analysis and predictive maintenance.
This helps maintenance managers make informed decisions and allocate resources more efficiently.
Implementing Safety Diagnoses with Infrared Cameras
Implementing a successful safety diagnosis program using infrared cameras involves several steps.
First, maintenance managers must select the right type of infrared camera that suits the specific requirements of their facility.
Factors to consider include the temperature range, resolution, and ease of use of the camera.
Once the appropriate equipment is acquired, staff must be adequately trained in the operation of the infrared cameras.
Training should cover both the technical aspects of using the camera and the interpretation of the thermal images it produces.
Establishing Safety Inspection Protocols
To ensure consistency and reliability in safety diagnosis, it is essential to establish standardized inspection protocols.
These protocols should specify the frequency of inspections, the areas of equipment to be scanned, and the criteria for evaluating thermal images.
Protocols should also include guidelines for documenting and reporting findings, as well as procedures for responding to identified issues.
Analyzing and Interpreting Thermal Images
Interpreting thermal images requires a thorough understanding of the equipment and its normal operating conditions.
Once images are captured, they should be closely analyzed to identify any anomalies or deviations from expected temperature patterns.
Common issues to look for include uneven heat distribution, unexpected hot or cold spots, and rapid changes in temperature.
Addressing Common Challenges in Infrared Safety Diagnosis
While infrared cameras provide an invaluable tool for safety diagnosis, there are challenges that maintenance managers must be prepared to address.
One common challenge is the potential for false readings caused by reflective surfaces, which can skew temperature measurements.
To mitigate this, operators should take multiple readings and focus on consistent patterns rather than individual anomalies.
Environmental factors such as ambient temperature, wind, and dust can also affect the accuracy of thermal imaging.
Therefore, inspections should be conducted under controlled conditions as much as possible to ensure reliable results.
Maintaining Infrared Camera Equipment
Regular maintenance of the infrared cameras themselves is crucial to ensure accurate readings.
This includes routine calibration, cleaning of lenses and sensors, and software updates.
Conclusion: Enhancing Safety in the Steel Industry
For managers of equipment maintenance departments in the steel industry, the implementation of infrared cameras for safety diagnosis offers significant benefits.
These cameras facilitate early detection of potential issues, enable non-contact inspections, and support predictive maintenance strategies.
By adopting infrared technology, maintenance managers can enhance the safety and efficiency of their high temperature equipment operations, ultimately contributing to more reliable and productive industrial processes.
By following the guidelines for implementing infrared safety diagnosis and addressing common challenges, maintenance teams can effectively harness the power of infrared cameras.
This not only improves safety outcomes but also optimizes resource allocation, reduces downtime, and ensures continuous, efficient production in the steel industry.
資料ダウンロード
QCD調達購買管理クラウド「newji」は、調達購買部門で必要なQCD管理全てを備えた、現場特化型兼クラウド型の今世紀最高の購買管理システムとなります。
ユーザー登録
調達購買業務の効率化だけでなく、システムを導入することで、コスト削減や製品・資材のステータス可視化のほか、属人化していた購買情報の共有化による内部不正防止や統制にも役立ちます。
NEWJI DX
製造業に特化したデジタルトランスフォーメーション(DX)の実現を目指す請負開発型のコンサルティングサービスです。AI、iPaaS、および先端の技術を駆使して、製造プロセスの効率化、業務効率化、チームワーク強化、コスト削減、品質向上を実現します。このサービスは、製造業の課題を深く理解し、それに対する最適なデジタルソリューションを提供することで、企業が持続的な成長とイノベーションを達成できるようサポートします。
オンライン講座
製造業、主に購買・調達部門にお勤めの方々に向けた情報を配信しております。
新任の方やベテランの方、管理職を対象とした幅広いコンテンツをご用意しております。
お問い合わせ
コストダウンが利益に直結する術だと理解していても、なかなか前に進めることができない状況。そんな時は、newjiのコストダウン自動化機能で大きく利益貢献しよう!
(Β版非公開)