- お役立ち記事
- For managers of process technology departments in the semiconductor manufacturing industry! Optimization method for CMP (chemical mechanical polishing) process
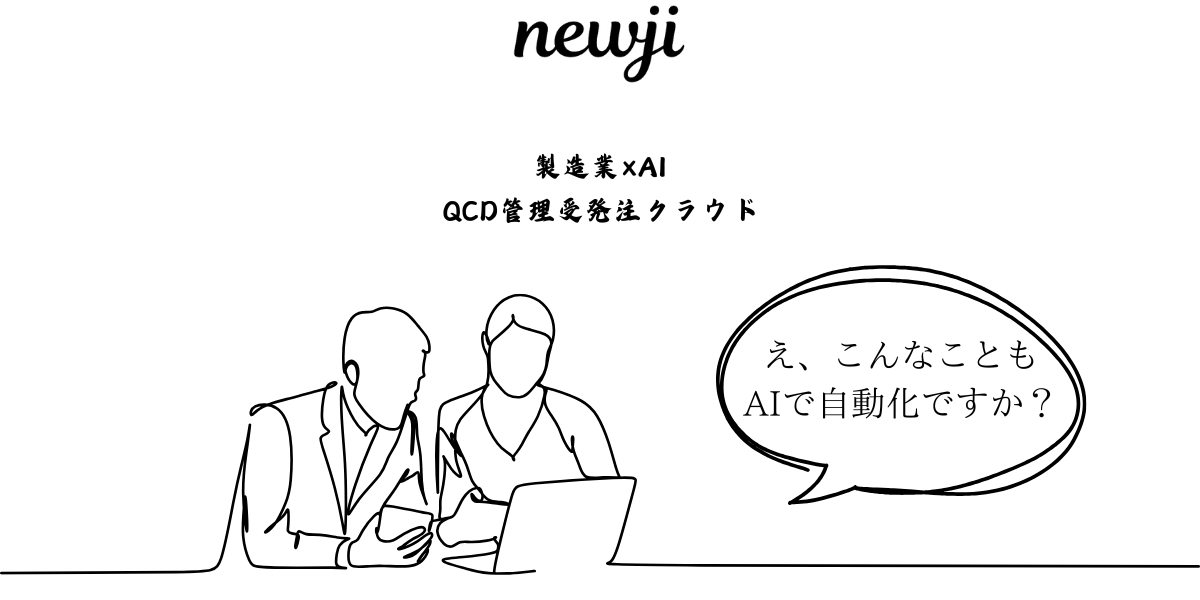
For managers of process technology departments in the semiconductor manufacturing industry! Optimization method for CMP (chemical mechanical polishing) process
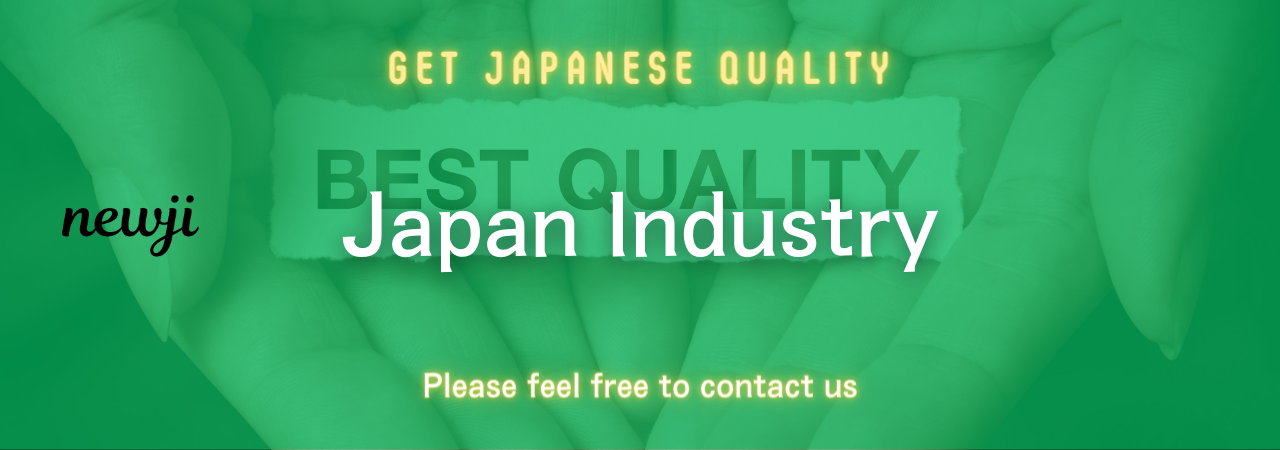
目次
Understanding the CMP Process
The CMP (Chemical Mechanical Polishing) process is an essential step in semiconductor manufacturing.
It is used to planarize, or smooth, the surface of semiconductor wafers.
This process is crucial because it ensures that subsequent layers of materials are applied evenly, which is vital for the performance and reliability of semiconductor devices.
CMP involves both chemical and mechanical actions.
The chemical component typically includes slurries with specific properties that react with the wafer material.
The mechanical component involves physical abrasion using a polishing pad.
Together, these components work to remove excess material and create a flat wafer surface.
Importance of CMP Process Optimization
Optimizing the CMP process is crucial for several reasons.
Firstly, it can significantly improve wafer yield, and ensure higher volumes of functional devices per wafer.
Yield improvements translate directly into lower manufacturing costs and increased profitability.
Secondly, optimization contributes to the reliability of semiconductor devices.
A more uniform and defect-free surface ensures that future layers are applied correctly, reducing the risk of device failure during operation.
Lastly, optimizing this process can lead to reduced consumption of materials and consumables.
This not only decreases costs but also minimizes the environmental footprint of semiconductor manufacturing.
Challenges in CMP Process
Despite its importance, the CMP process presents several challenges.
One of the primary challenges is achieving uniformity across the wafer.
Inconsistencies in slurry distribution, pad pressure, and other variables can lead to uneven surfaces and defects.
Another challenge is the potential for scratching and defects induced by particles from the slurry or pad.
These defects can compromise device yield and performance.
Additionally, the process must be carefully tuned to avoid over-polishing or under-polishing.
Over-polishing can remove too much material, while under-polishing leaves a non-uniform layer that affects subsequent processes.
Optimization Strategies for CMP
Selecting the Right Slurry
One fundamental aspect of optimizing CMP is selecting the appropriate slurry.
The slurry composition should be tailored to the specific materials being polished.
Factors like pH level, particle size, and chemical composition need careful consideration to achieve the best results.
Polishing Pad Selection and Conditioning
The choice of polishing pad is equally important.
Pads come in various materials and designs, each suited for different applications.
Periodic conditioning of the pad helps maintain its effectiveness and prevents glazing, which can reduce its polishing capability.
Process Parameter Control
Controlling process parameters such as downforce, rotational speeds, and slurry flow rate is crucial for achieving optimal results.
Advanced control systems and real-time monitoring can aid in maintaining these parameters within the desired range.
End Point Detection
Implementing an effective endpoint detection system is another optimization strategy.
This system monitors the CMP process in real-time to determine when polishing should stop, thus preventing over-polishing or under-polishing.
Defect Management
Regularly monitoring for defects and implementing strategies to address them is vital.
This can include adjusting slurry composition, optimizing pad conditioning, or fine-tuning process parameters to minimize defects.
Leveraging Technology for CMP Optimization
Data Analytics and Machine Learning
The use of data analytics and machine learning can significantly enhance CMP optimization.
By analyzing historical data, these technologies can identify patterns and predict optimal process settings.
This allows for proactive adjustments and improved process control.
Simulation and Modeling Tools
Simulating the CMP process using advanced modeling tools can help predict the outcome of various parameter changes.
This allows process engineers to test different scenarios without impacting actual production, reducing trial and error.
Future Trends in CMP Process Optimization
Looking forward, the CMP process is expected to continue evolving with technological advancements.
Integration with advanced sensors and IoT devices will enable more precise control and monitoring.
Real-time data collection and feedback loops will become more sophisticated, allowing for even greater levels of optimization.
Furthermore, the development of environmentally-friendly slurries and consumables will be a focus, allowing semiconductor manufacturers to meet sustainability goals without sacrificing performance.
Conclusion
Optimizing the CMP process is paramount for the efficiency, yield, and reliability of semiconductor manufacturing.
By selecting the right consumables, controlling process parameters, leveraging technology, and embracing future trends, managers in process technology departments can enhance their CMP operations.
Continuous improvement and innovation in this area will support not only the current demands of the industry but also its future growth.
資料ダウンロード
QCD調達購買管理クラウド「newji」は、調達購買部門で必要なQCD管理全てを備えた、現場特化型兼クラウド型の今世紀最高の購買管理システムとなります。
ユーザー登録
調達購買業務の効率化だけでなく、システムを導入することで、コスト削減や製品・資材のステータス可視化のほか、属人化していた購買情報の共有化による内部不正防止や統制にも役立ちます。
NEWJI DX
製造業に特化したデジタルトランスフォーメーション(DX)の実現を目指す請負開発型のコンサルティングサービスです。AI、iPaaS、および先端の技術を駆使して、製造プロセスの効率化、業務効率化、チームワーク強化、コスト削減、品質向上を実現します。このサービスは、製造業の課題を深く理解し、それに対する最適なデジタルソリューションを提供することで、企業が持続的な成長とイノベーションを達成できるようサポートします。
オンライン講座
製造業、主に購買・調達部門にお勤めの方々に向けた情報を配信しております。
新任の方やベテランの方、管理職を対象とした幅広いコンテンツをご用意しております。
お問い合わせ
コストダウンが利益に直結する術だと理解していても、なかなか前に進めることができない状況。そんな時は、newjiのコストダウン自動化機能で大きく利益貢献しよう!
(Β版非公開)