- お役立ち記事
- For managers of production technology departments! A guide to effective implementation of automation systems and robotics
For managers of production technology departments! A guide to effective implementation of automation systems and robotics
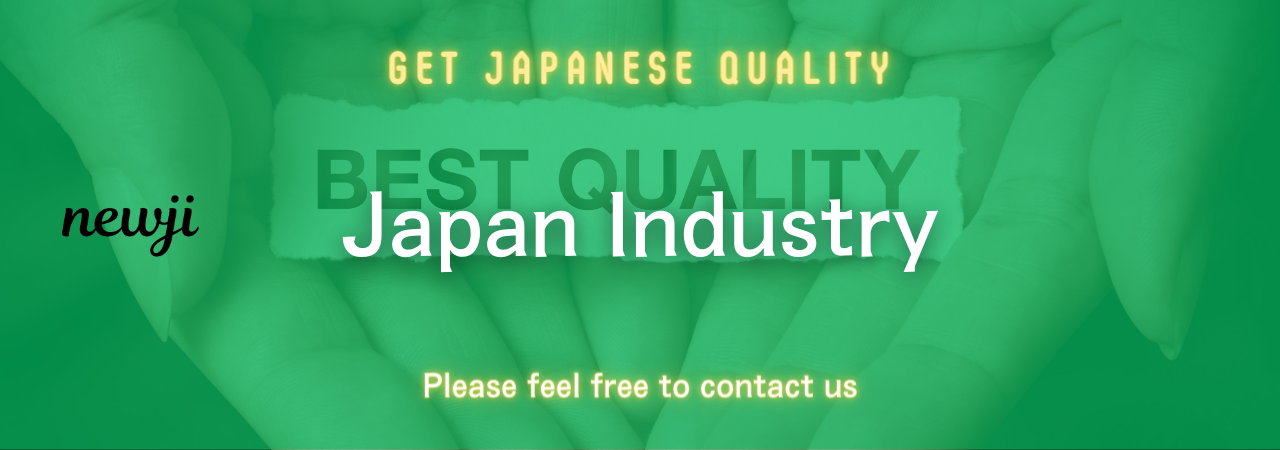
目次
Understanding the Basics of Automation Systems
Automation systems have become integral in modern manufacturing and production environments.
An automation system essentially utilizes technology to control processes and machinery in factories and industries, reducing the need for human intervention.
The implementation of these systems can lead to significant enhancements in efficiency, safety, and accuracy.
To effectively integrate automation systems in production technology, a strong foundational understanding is imperative.
This entails recognizing the various types of automation system applications such as fixed, programmable, and flexible automation.
Fixed automation, also known as hard automation, involves employing specialized equipment to automate a specific task.
This type is excellent for high-volume production with repeatable, distinct steps.
Programmable automation allows for the configuration of equipment to produce different types of products using the same machinery.
This is particularly useful in batch production.
Flexible automation, on the other hand, is geared towards customization, perfect for small batch sizes and frequent product changes.
The Role of Robotics in Modern Production
Robots form a vital part of automation systems, significantly altering how manufacturing processes are conducted.
Robotics enhances production capabilities by performing tasks that may be dangerous, tedious, or time-consuming for human workers.
Understanding the types of robots used—such as industrial robots, collaborative robots, and autonomous mobile robots—can aid managers in deciding the most appropriate application for their specific needs.
Industrial robots are used extensively for tasks like welding, painting, assembly, and material handling.
They are known for their precision and consistent production rates.
Collaborative robots, or cobots, are designed to work alongside humans, offering safety features that allow them to stop when contact is made with an obstruction including humans.
Finally, autonomous mobile robots are utilized for logistics purposes like moving materials within a factory, improving efficiency and productivity.
Benefits of Implementing Automation and Robotics
The integration of automation and robotics in production technology departments presents numerous benefits.
Firstly, it leads to increased efficiency as machines operate continuously without fatigue, unlike human labor.
With an automated setup, production lines can run 24/7, leading to higher outputs.
Secondly, automation systems and robotics increase accuracy and precision by minimizing human error.
Automated processes enhance product quality, resulting in less wastage and improved customer satisfaction.
Furthermore, automation reduces labor costs by replacing manual tasks with technological solutions.
While initial setup may be costly, the long-term savings and increased productivity often outweigh these expenses.
Additionally, safety is another significant benefit.
By delegating hazardous tasks to machines, the workforce’s exposure to potentially dangerous environments is reduced, thereby cutting down on work-related injuries.
Challenges in Implementing Automation and Robotics
Despite the numerous benefits, certain challenges accompany the incorporation of automation systems and robotics in production.
The initial investment required for equipment, installation, and training can be significant and may pose a barrier for some organizations.
Another challenge is the resistance to change within the workforce.
Employees may fear job loss or struggle to adapt to new technologies.
Continuous education and open communication can mitigate these concerns, making transition smoother.
Additionally, technical issues and maintenance requirements can disrupt operations if not managed properly.
Regular maintenance schedules and having a skilled technical team on standby can help prevent or quickly address any hiccups that arise.
Lastly, the pace of change in automation and robotic technology is rapid.
Keeping up with the latest advancements and ensuring compatibility with existing systems is crucial to make the most of investments in technology.
Steps for Effective Implementation
To successfully implement automation systems and robotics, managers should start with a clear strategy.
Begin by conducting a thorough evaluation of the current processes and identifying areas that can benefit most from automation.
It’s essential to set clear objectives and ensure alignment with the organization’s overall goals.
Develop a phased implementation plan to manage the transition smoothly, starting with smaller projects before scaling up.
Training programs for the existing workforce are crucial.
Invest in upskilling employees to work alongside machines, not only to manage them but also to understand their role in the broader production process.
During implementation, secure buy-in from all stakeholders by highlighting the long-term benefits versus the initial outlay.
Regular reviews and updates to the process will ensure that the automation system continues to meet changing demands and remains optimized.
Future Trends in Automation and Robotics
The future of automation systems and robotics is promising, with continuous advancements making these technologies increasingly sophisticated and accessible.
Artificial intelligence and machine learning are paving the way for more responsive and adaptive systems.
These intelligent systems can adjust and optimize operations in real-time, offering further improvements in efficiency and flexibility.
The integration of the Internet of Things (IoT) in manufacturing processes, often referred to as Industry 4.0, is another trend that is set to revolutionize production technology.
IoT enables machines to communicate and make decisions based on data, improving predictive maintenance and reducing downtime.
Moreover, with expanding capabilities, robotics will likely become more prevalent in varied environments, from complex production lines to small-scale operations.
The focus is expected to shift towards creating more collaborative environments where humans and machines work seamlessly together.
In conclusion, embracing automation systems and robotics is no longer optional but a necessity for staying competitive in today’s manufacturing landscape.
By understanding, implementing, and adapting to these technologies, production technology departments can unlock tremendous potential, driving the future of manufacturing innovation.
資料ダウンロード
QCD調達購買管理クラウド「newji」は、調達購買部門で必要なQCD管理全てを備えた、現場特化型兼クラウド型の今世紀最高の購買管理システムとなります。
ユーザー登録
調達購買業務の効率化だけでなく、システムを導入することで、コスト削減や製品・資材のステータス可視化のほか、属人化していた購買情報の共有化による内部不正防止や統制にも役立ちます。
NEWJI DX
製造業に特化したデジタルトランスフォーメーション(DX)の実現を目指す請負開発型のコンサルティングサービスです。AI、iPaaS、および先端の技術を駆使して、製造プロセスの効率化、業務効率化、チームワーク強化、コスト削減、品質向上を実現します。このサービスは、製造業の課題を深く理解し、それに対する最適なデジタルソリューションを提供することで、企業が持続的な成長とイノベーションを達成できるようサポートします。
オンライン講座
製造業、主に購買・調達部門にお勤めの方々に向けた情報を配信しております。
新任の方やベテランの方、管理職を対象とした幅広いコンテンツをご用意しております。
お問い合わせ
コストダウンが利益に直結する術だと理解していても、なかなか前に進めることができない状況。そんな時は、newjiのコストダウン自動化機能で大きく利益貢献しよう!
(Β版非公開)