- お役立ち記事
- For managers of production technology departments in the plastic molding industry! In-mold labeling (IML) technology implementation example
For managers of production technology departments in the plastic molding industry! In-mold labeling (IML) technology implementation example
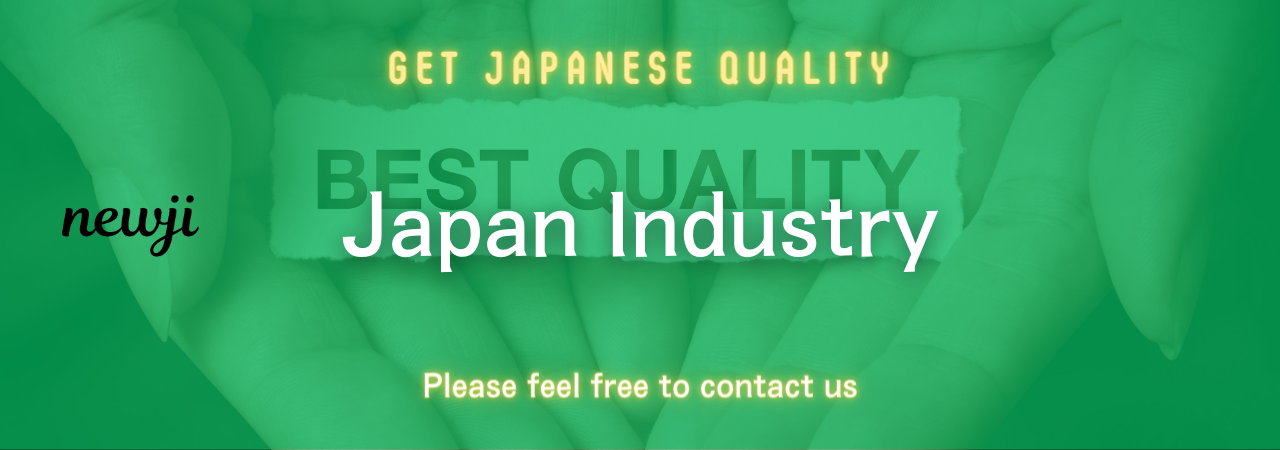
目次
Understanding In-Mold Labeling (IML) Technology
In-mold labeling, commonly referred to as IML, is an innovative process primarily used in the plastic molding industry.
It integrates the labeling process into the manufacturing of containers, offering a seamless, aesthetically pleasing, and durable finish.
By using this technology, labels are fused directly onto plastic containers during the molding process, eliminating the need for post-production labeling.
Unlike traditional labeling methods, which involve sticking labels onto a finished product, IML allows for the label to become an integral part of the product’s surface.
The result is a product that not only looks sleek and professional but also offers enhanced durability and resistance to elements such as moisture and temperature changes.
Benefits of Implementing IML Technology
For production technology managers in the plastic molding industry, understanding and leveraging IML can bring several key advantages.
Reduced Production Time and Costs
One of the primary benefits of adopting IML technology is the potential to reduce production time and costs.
Since labeling is included in the molding process itself, there’s no need for additional labeling steps after production.
This streamlines operations, leading to faster production cycles and lower labor costs.
Enhanced Product Durability
IML provides a high level of durability that traditional labeling cannot match.
The labels become part of the plastic, protecting them from scratches, scuffing, and peeling.
This durability is particularly beneficial for products exposed to harsh environments or frequent handling, ensuring the product maintains its aesthetic appeal over time.
Improved Design Flexibility
With in-mold labeling, the design possibilities are virtually unlimited.
Manufacturers can produce high-quality, detailed, and colorful labels that cover complex surfaces and components.
This flexibility allows for more creative product designs and branding opportunities, which can significantly enhance product shelf appeal and consumer engagement.
Environmental Benefits
IML also offers environmental advantages.
Since the labels are integrated into the product, there’s less waste compared to traditional labeling processes.
The technology supports the use of fully recyclable materials, contributing to greener and more sustainable production practices.
Implementing IML Technology: A Real-Life Example
To illustrate how IML technology can be implemented effectively, let’s look at an example from a company in the plastic container manufacturing sector.
The Challenge
The company, known for producing food-grade plastic containers, faced challenges with their existing labeling process.
They experienced frequent issues with label adhesion and durability, affecting the overall quality and appearance of their products.
Additionally, the time and resources spent on post-production labeling were significant.
The Solution
After evaluating several solutions, the company decided to implement in-mold labeling technology.
They invested in new equipment and collaborated with a supplier to develop custom labels specifically designed for their product range.
The Implementation Process
The transition to IML involved several key steps:
1. **Equipment Upgrades**: The company upgraded their molding machines to accommodate the IML process.
This included installing robotics capable of precisely placing labels into molds before injection.
2. **Material Selection**: They selected label materials that could withstand high temperatures and integrate seamlessly with various plastic resins used in their products.
3. **Training**: Staff underwent extensive training to become proficient in operating the new machinery and overseeing the IML process.
4. **Testing and Iteration**: The company conducted extensive testing to ensure label adhesion and product quality met required standards.
This phase involved refining label design and adjusting molding conditions as necessary.
The Results
The implementation of IML technology led to several positive outcomes for the company:
– **Increased Efficiency**: The integration of labeling into the molding process reduced production times by eliminating post-production labeling steps.
– **Cost Savings**: Streamlined operations resulted in significant labor cost reductions.
– **Improved Product Quality**: The new labeling process produced containers with enhanced durability and aesthetic appeal, attracting positive feedback from customers.
– **Environmental Impact**: The move towards more sustainable labeling practices helped improve the company’s environmental footprint.
Key Considerations for Successful IML Implementation
For managers in the production technology department considering IML, there are several factors to consider:
Assessment of Current Processes
Before implementing IML, it’s crucial to assess current production processes and identify areas where it can deliver the most value.
Investment in Technology
Investing in the right machinery and materials is essential for a successful IML transition.
This may involve significant upfront costs, but the long-term benefits often offset these initial expenditures.
Training and Expertise
Ensuring that your team is well-trained in IML technology and processes is vital.
Continuous learning and development will help maintain efficiency and quality throughout the implementation.
Partnerships with Suppliers
Collaborate with suppliers who can provide specialized labels and guidance tailored to your specific products and production needs.
Conclusion
In-mold labeling technology offers a multitude of benefits for the plastic molding industry.
Its ability to enhance product durability, design flexibility, and sustainability make it an appealing option for forward-thinking companies.
By carefully planning and executing the transition to IML, production technology managers can achieve significant improvements in both operational efficiency and product quality.
資料ダウンロード
QCD調達購買管理クラウド「newji」は、調達購買部門で必要なQCD管理全てを備えた、現場特化型兼クラウド型の今世紀最高の購買管理システムとなります。
ユーザー登録
調達購買業務の効率化だけでなく、システムを導入することで、コスト削減や製品・資材のステータス可視化のほか、属人化していた購買情報の共有化による内部不正防止や統制にも役立ちます。
NEWJI DX
製造業に特化したデジタルトランスフォーメーション(DX)の実現を目指す請負開発型のコンサルティングサービスです。AI、iPaaS、および先端の技術を駆使して、製造プロセスの効率化、業務効率化、チームワーク強化、コスト削減、品質向上を実現します。このサービスは、製造業の課題を深く理解し、それに対する最適なデジタルソリューションを提供することで、企業が持続的な成長とイノベーションを達成できるようサポートします。
オンライン講座
製造業、主に購買・調達部門にお勤めの方々に向けた情報を配信しております。
新任の方やベテランの方、管理職を対象とした幅広いコンテンツをご用意しております。
お問い合わせ
コストダウンが利益に直結する術だと理解していても、なかなか前に進めることができない状況。そんな時は、newjiのコストダウン自動化機能で大きく利益貢献しよう!
(Β版非公開)