- お役立ち記事
- For managers of quality assurance departments in electronic component manufacturing industries! How to enhance product quality using reliability testing
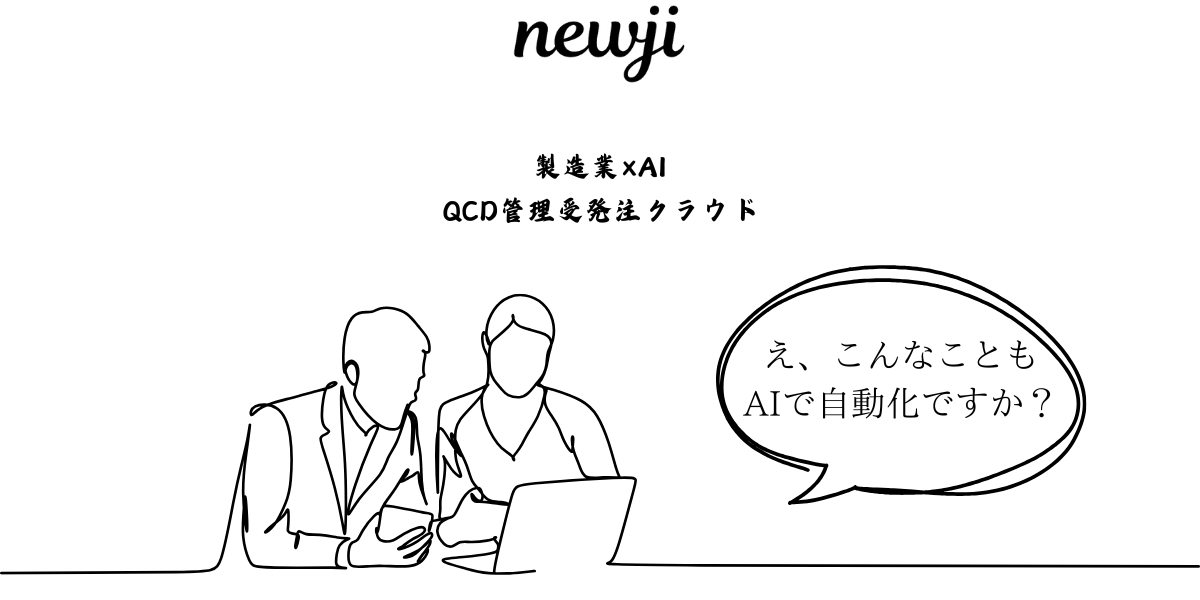
For managers of quality assurance departments in electronic component manufacturing industries! How to enhance product quality using reliability testing
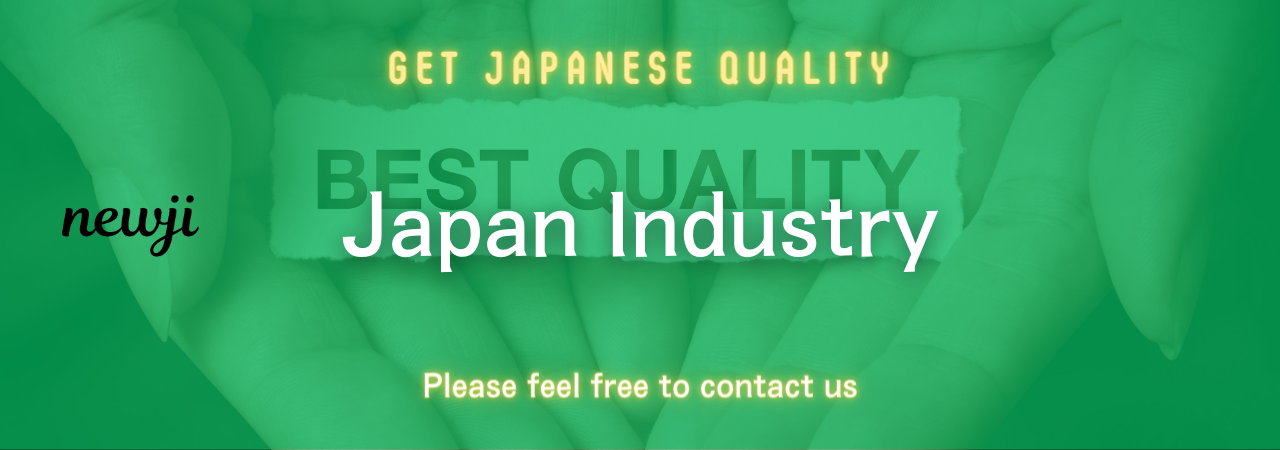
目次
Understanding the Importance of Reliability Testing
For managers of quality assurance departments in electronic component manufacturing industries, ensuring high product quality is a fundamental goal.
One key method to achieve this is through reliability testing.
Reliability testing helps in determining the performance, durability, and lifespan of electronic components.
By simulating real-world conditions, reliability testing can identify potential points of failure before products reach the hands of customers.
This not only safeguards the company’s reputation but also reduces costly recalls and repairs.
Types of Reliability Testing
To enhance product quality, understanding the various types of reliability testing is crucial.
Different tests target different aspects of product performance:
Environmental Testing
Environmental testing subjects components to extreme conditions such as temperature fluctuations, humidity, and altitude.
This process ensures components can withstand varying environments without compromising performance.
Mechanical Testing
Mechanical testing assesses the physical durability of components through vibrations, shock, and impact simulations.
This type of testing identifies weak points that may break under stress or repeated use.
Electrical Testing
Electrical testing evaluates the components’ performance under electrical stress.
This includes testing for voltage, current, and power capacity to ensure components can handle the required electrical load.
Life Testing
Life testing aims to determine the lifespan of a product under normal use conditions.
By running components through repeated cycles, life testing predicts when and how a component might fail.
Implementing Reliability Testing in Quality Assurance
Incorporating reliability testing into the quality assurance process requires a strategic approach.
Here’s how to effectively implement it:
Define Clear Criteria
Before testing begins, establish clear criteria for what constitutes a pass or fail.
These criteria should be based on industry standards, customer expectations, and product specifications.
Develop a Testing Plan
Create a comprehensive testing plan that outlines the type of tests, conditions, and the duration of each test.
The plan should be specific and tailored to the component being tested.
Utilize Advanced Technology
Leverage modern testing equipment and software that can simulate a wide range of conditions accurately.
Advanced technology can provide precise data and insights into potential failure modes.
Analyze and Iterate
Once testing is complete, thoroughly analyze the results to identify trends or recurring issues.
Use this data to iterate and improve the product design and manufacturing process.
Benefits of Reliability Testing
Integrating reliability testing into your quality assurance process offers numerous benefits:
Increased Customer Satisfaction
By ensuring products reliably perform as expected, you enhance customer satisfaction and trust in your brand.
Satisfied customers are more likely to be repeat buyers and recommend your products to others.
Reduced Costs
Investing in reliability testing upfront can significantly reduce costs related to recalls, repairs, and warranty claims.
Early identification of potential failures prevents expensive post-market issues.
Competitive Advantage
High-quality, reliable products give you an edge over competitors.
Customers are more likely to choose a company known for producing dependable products.
Challenges in Reliability Testing
While reliability testing is beneficial, it also presents certain challenges:
Time and Resources
Reliability testing can be time-consuming and resource-intensive.
It requires careful planning to balance thorough testing with product timelines.
Complexity
The complexity of modern electronic components can make testing challenging.
Simulating real-world conditions accurately necessitates skilled personnel and sophisticated technology.
Data Management
The volume of data generated during testing can be overwhelming.
Effective data management systems are needed to organize, store, and analyze this data efficiently.
Conclusion
For managers of quality assurance departments in the electronic component manufacturing industry, reliability testing is an indispensable tool for enhancing product quality.
By understanding the types of reliability testing, implementing them effectively, and addressing challenges, you can ensure your products stand the test of time.
With reliability testing, you not only improve customer satisfaction and reduce costs but also gain a competitive advantage in the market.
資料ダウンロード
QCD調達購買管理クラウド「newji」は、調達購買部門で必要なQCD管理全てを備えた、現場特化型兼クラウド型の今世紀最高の購買管理システムとなります。
ユーザー登録
調達購買業務の効率化だけでなく、システムを導入することで、コスト削減や製品・資材のステータス可視化のほか、属人化していた購買情報の共有化による内部不正防止や統制にも役立ちます。
NEWJI DX
製造業に特化したデジタルトランスフォーメーション(DX)の実現を目指す請負開発型のコンサルティングサービスです。AI、iPaaS、および先端の技術を駆使して、製造プロセスの効率化、業務効率化、チームワーク強化、コスト削減、品質向上を実現します。このサービスは、製造業の課題を深く理解し、それに対する最適なデジタルソリューションを提供することで、企業が持続的な成長とイノベーションを達成できるようサポートします。
オンライン講座
製造業、主に購買・調達部門にお勤めの方々に向けた情報を配信しております。
新任の方やベテランの方、管理職を対象とした幅広いコンテンツをご用意しております。
お問い合わせ
コストダウンが利益に直結する術だと理解していても、なかなか前に進めることができない状況。そんな時は、newjiのコストダウン自動化機能で大きく利益貢献しよう!
(Β版非公開)