- お役立ち記事
- For managers of quality assurance departments in the folding chair manufacturing industry! Design criteria for achieving both weight reduction and load capacity
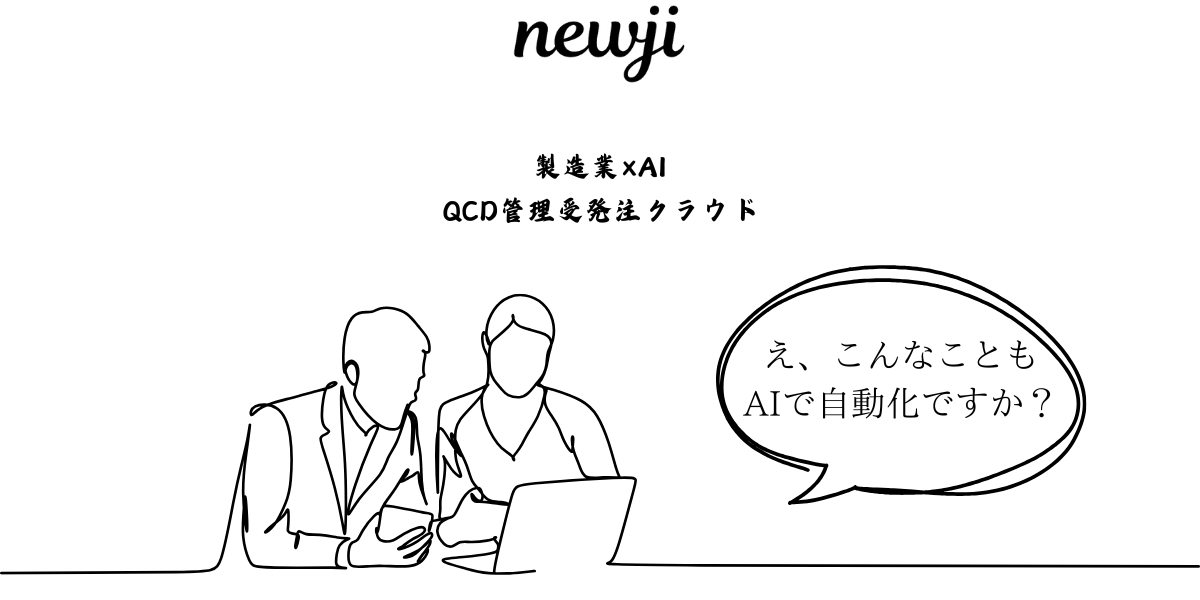
For managers of quality assurance departments in the folding chair manufacturing industry! Design criteria for achieving both weight reduction and load capacity
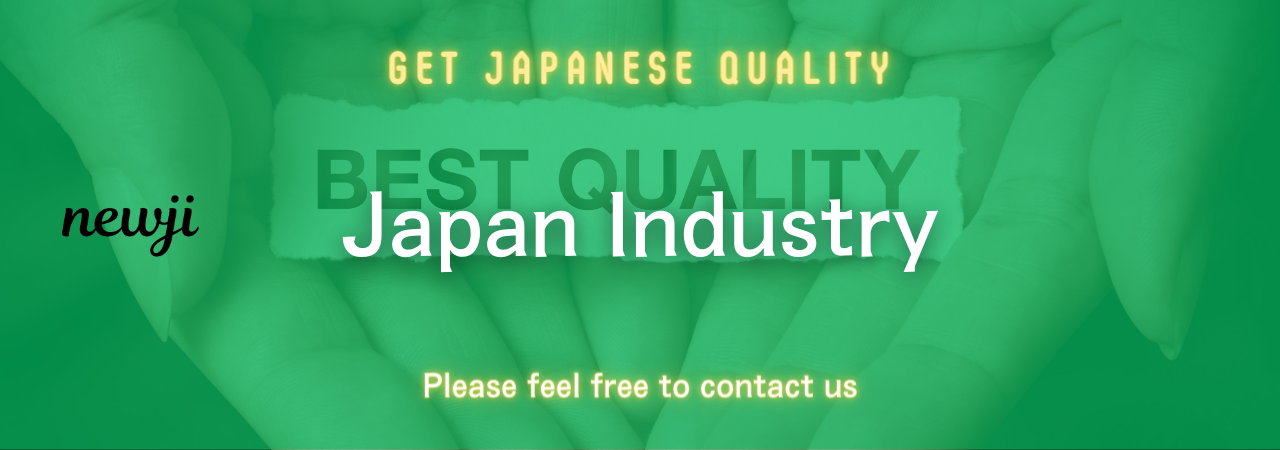
目次
Understanding the Importance of Design Criteria
In the world of folding chair manufacturing, maintaining a balance between weight reduction and load capacity is crucial.
Quality assurance managers play a pivotal role in ensuring these criteria are met while maintaining product integrity.
Design criteria are established guidelines that influence every stage of a product’s lifecycle, from conception to market release.
These criteria dictate the materials used, the manufacturing process, and ultimately, the end-user’s experience.
For folding chairs, achieving both weight reduction and load capacity without compromising on either can set a product apart in a competitive market.
Balancing Weight and Strength in Folding Chairs
The folding chair industry often faces the challenge of creating lightweight products that do not compromise on strength and durability.
Consumers seek portable, easy-to-carry options that provide reliable support.
The design criteria must therefore focus on innovative solutions that meet these demands.
Lightweight materials such as aluminum or advanced polymers can be utilized, but must be carefully selected to ensure they still meet the necessary load capacity standards.
Designers must consider the trade-offs between weight and strength, often using reinforcement techniques or composite materials to achieve the perfect balance.
Materials Selection for Optimal Performance
Materials selection is paramount when striving to meet design criteria for weight reduction and load capacity.
Metals such as aluminum are popular for their lightweight and robust nature.
However, advanced materials like carbon fiber composites or high-strength polypropylene offer similar benefits with potential for greater innovation.
Each material comes with its own set of properties; metals might offer higher durability, whereas polymers could provide better flexibility and weight reduction.
Quality assurance managers must ensure that the chosen material does not only meet the necessary mechanical strength but is also cost-effective for production.
Innovative Design Approaches
Design innovation is essential for developing folding chairs that are both lightweight and strong.
One method is to incorporate hollow structures in the design, reducing material usage while maintaining load capacity.
Another approach involves the use of reinforced joints and supports, distributing weight more effectively and preventing stress concentration on single components.
Advanced computer-aided design (CAD) software now allows for simulations that optimize these design features, ensuring they meet required standards before physical prototypes are even constructed.
Testing and Simulation
Testing and simulation play a significant role in the design and manufacturing process.
Before any folding chair reaches the consumer, it undergoes rigorous testing phases.
These include load-bearing tests, wear and tear assessments, and durability trials to ensure they meet stringent quality standards and safety regulations.
Simulation software can predict product behavior under different conditions, allowing for immediate adjustments and enhancements without the need for multiple physical prototypes.
This not only reduces the time-to-market but ensures that the final product adheres to the desired design criteria.
Ensuring Compliance with Industry Standards
Industry standards are in place to guarantee that folding chairs can safely and effectively fulfill their purpose.
Quality assurance managers must be well-versed in these standards to ensure compliance throughout the design and manufacturing process.
This often involves significant documentation and verification steps, as well as constant liaising with engineering departments to confirm that all aspects of the chair meet safety and quality benchmarks.
Non-compliance can result in product recalls, legal issues, and damaged business reputations, making adherence to standards mandatory.
Consumer Expectations and Market Trends
Understanding consumer expectations and market trends is vital for staying competitive.
Today’s consumers demand products that are not only functional but also aesthetically appealing.
They expect chairs that offer comfort, portability, and long-lasting durability.
Keeping abreast of these expectations can help quality assurance managers fine-tune their design criteria to create products that align with current market demands.
Incorporating sustainable and eco-friendly materials can also appeal to increasingly environmentally-conscious consumers.
Working Closely with Cross-Functional Teams
Collaboration across departments is essential for successfully meeting design criteria.
Quality assurance managers must frequently coordinate with researchers, designers, engineers, and marketing teams.
This ensures that every team involved in the product’s lifecycle is aligned with the desired outcomes.
Cross-department feedback can offer valuable insights, allowing for the refinement of designs and processes to achieve optimal results.
Conclusion
For quality assurance managers in the folding chair manufacturing sector, adhering to design criteria for weight reduction and load capacity is a complex but essential task.
By carefully selecting materials, embracing innovative design, and ensuring compliance with industry standards, it is possible to produce chairs that meet consumer expectations and excel in the marketplace.
With a focus on collaboration and continual improvement, quality assurance departments can lead the way in creating products that combine practicality, durability, and modern appeal.
資料ダウンロード
QCD調達購買管理クラウド「newji」は、調達購買部門で必要なQCD管理全てを備えた、現場特化型兼クラウド型の今世紀最高の購買管理システムとなります。
ユーザー登録
調達購買業務の効率化だけでなく、システムを導入することで、コスト削減や製品・資材のステータス可視化のほか、属人化していた購買情報の共有化による内部不正防止や統制にも役立ちます。
NEWJI DX
製造業に特化したデジタルトランスフォーメーション(DX)の実現を目指す請負開発型のコンサルティングサービスです。AI、iPaaS、および先端の技術を駆使して、製造プロセスの効率化、業務効率化、チームワーク強化、コスト削減、品質向上を実現します。このサービスは、製造業の課題を深く理解し、それに対する最適なデジタルソリューションを提供することで、企業が持続的な成長とイノベーションを達成できるようサポートします。
オンライン講座
製造業、主に購買・調達部門にお勤めの方々に向けた情報を配信しております。
新任の方やベテランの方、管理職を対象とした幅広いコンテンツをご用意しております。
お問い合わせ
コストダウンが利益に直結する術だと理解していても、なかなか前に進めることができない状況。そんな時は、newjiのコストダウン自動化機能で大きく利益貢献しよう!
(Β版非公開)