- お役立ち記事
- For managers of quality assurance departments in the medical device manufacturing industry! How to implement a risk-based approach in accordance with ISO13485
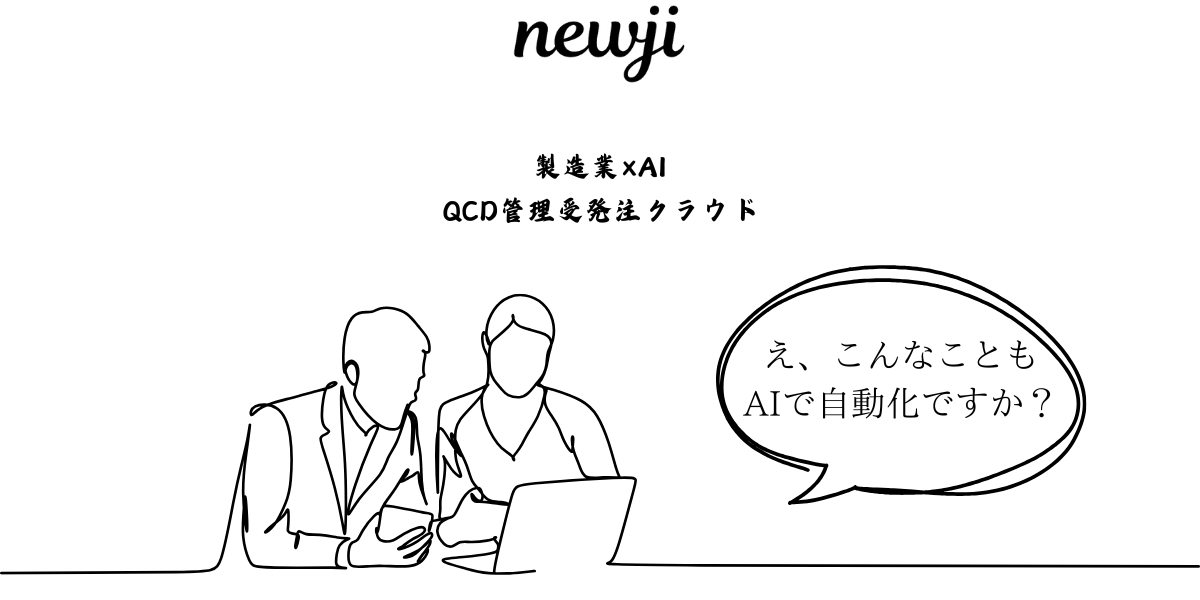
For managers of quality assurance departments in the medical device manufacturing industry! How to implement a risk-based approach in accordance with ISO13485
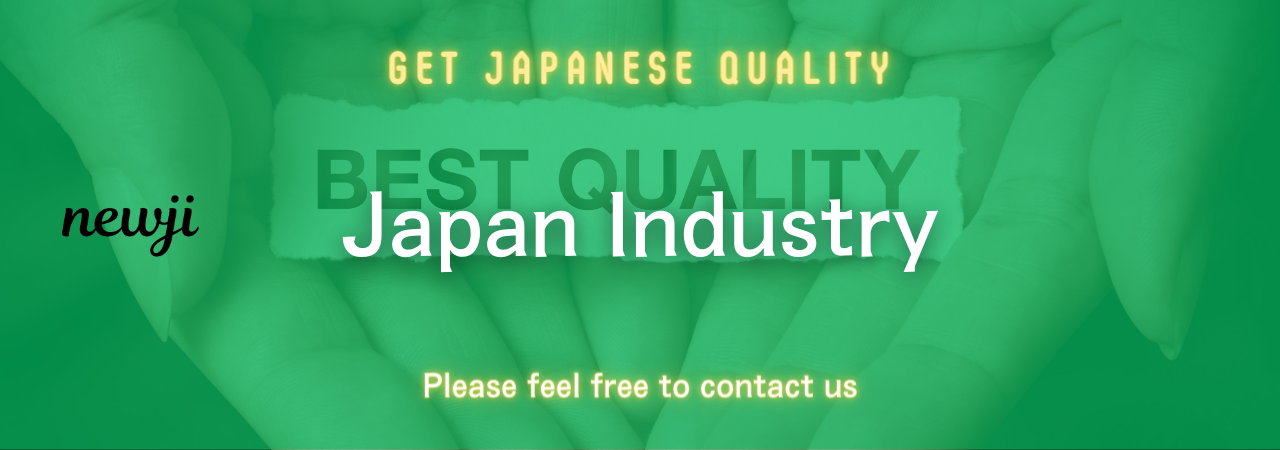
目次
Understanding the Risk-Based Approach
In the medical device manufacturing industry, ensuring the quality and safety of products is paramount.
ISO 13485, the internationally recognized standard for medical device quality management systems, emphasizes the importance of a risk-based approach.
But what exactly does a risk-based approach mean?
At its core, a risk-based approach involves identifying potential risks in the production and lifecycle of medical devices and implementing measures to mitigate these risks.
This is crucial to ensure that devices are safe and effective for end-users.
By focusing on understanding and managing risks, companies can prioritize resources efficiently, ensuring compliance with ISO 13485 standards.
The Importance of a Risk-Based Approach in ISO 13485
Incorporating a risk-based approach into quality management processes is not just about compliance; it’s about improving the overall quality of products.
This approach helps organizations identify what could potentially go wrong and prepares them to mitigate or eliminate these risks.
This preemptive planning is essential to prevent costly recalls, rework, and potential harm to patients or users.
Furthermore, a systematic risk-based approach helps in making informed decisions during design, production, and even post-market activities.
This ensures that practitioners in the quality assurance departments are equipped to handle unforeseen circumstances proactively.
Step 1: Risk Identification
The first step in implementing a risk-based approach is identifying potential risks associated with the medical device.
This involves a comprehensive review of the product’s design, component materials, manufacturing process, and even the external environment in which it will be used.
It is essential to gather a cross-functional team during this stage, including design engineers, manufacturing experts, and quality assurance professionals.
This team will work together to anticipate where things could potentially go wrong and what factors could lead to failure.
Tools such as Failure Modes and Effects Analysis (FMEA) and Hazard Analysis and Critical Control Points (HACCP) can be helpful in this process.
Step 2: Risk Assessment
Once potential risks have been identified, the next step is to assess their severity and likelihood.
This involves evaluating how often a risk might occur and what its impact would be on the product and end-user if it did occur.
The outcome of this risk assessment is a prioritized list of risks that need to be addressed.
It is important to engage experienced personnel who understand the nuances of both the device and its intended use.
Accurate risk assessment helps in determining which risks require the most immediate attention and resources.
Step 3: Risk Control
After assessing the risks, it’s time to put control measures in place.
Risk control strategies might include redesigning elements of the product, adjusting the manufacturing process, or enhancing quality checks at critical stages.
The objective here is to either reduce the severity of the risk, minimize its likelihood, or ideally, eliminate it altogether.
Continuous monitoring during the manufacturing process is essential to ensure that control measures are effectively implemented.
Regular audits and reviews of the control processes reinforce their effectiveness and ensure ongoing compliance with ISO 13485 requirements.
Integrating Risk Management into Quality Systems
For successful implementation, risk management should be an integral part of your quality management system.
This means aligning risk management processes with existing quality assurance procedures.
Policies and procedures should be documented, ensuring that all team members understand their roles in maintaining a risk-based approach.
Training plays a pivotal role here.
Regular workshops and training sessions will keep the team updated on any changes in risk management practices and new regulations in the medical device industry.
This continuous learning environment fosters a culture of quality and safety.
Utilizing Technology
Modern technology can aid significantly in risk-based approaches.
There are software solutions available that facilitate comprehensive risk management, from identification to continuous monitoring.
These technologies can automate many manual tasks, reducing the likelihood of human error and allowing teams to focus on critical decision-making areas.
Using data analytics, teams can gain insights into trends and potential problem areas, further enhancing the efficacy of their risk management strategies.
Benefits of a Risk-Based Approach
There are numerous benefits to implementing a risk-based approach in accordance with ISO 13485.
By proactively identifying and mitigating risks, manufacturers can reduce the likelihood of recalls and product failures, protecting both the brand and the consumer.
Additionally, by aligning resources with areas of greatest risk, organizations can optimize efficiency and reduce waste.
This approach also ensures compliance with regulatory standards, increasing marketability and stakeholder confidence.
Moreover, with risks managed appropriately, employees can work in a more predictable environment, increasing job satisfaction and retention.
Continuous Improvement
Lastly, embracing a risk-based approach is not a one-time action but a commitment to continuous improvement.
Regularly revisiting risk assessments and control strategies ensures that the quality management system remains dynamic and responsive to new challenges.
Feedback loops from post-market surveillance and customer feedback can be valuable in refining the risk management process.
By committing to regular audits and updates, companies can ensure that they are not only compliant but are also leaders in quality assurance in the medical device manufacturing industry.
Implementing a risk-based approach under ISO 13485 requires dedication and collaboration.
However, the benefits, both in terms of safety and operational efficiency, are substantial.
By fostering a culture of quality and risk awareness, organizations can confidently face industry challenges and deliver innovative, safe, and effective medical devices.
資料ダウンロード
QCD調達購買管理クラウド「newji」は、調達購買部門で必要なQCD管理全てを備えた、現場特化型兼クラウド型の今世紀最高の購買管理システムとなります。
ユーザー登録
調達購買業務の効率化だけでなく、システムを導入することで、コスト削減や製品・資材のステータス可視化のほか、属人化していた購買情報の共有化による内部不正防止や統制にも役立ちます。
NEWJI DX
製造業に特化したデジタルトランスフォーメーション(DX)の実現を目指す請負開発型のコンサルティングサービスです。AI、iPaaS、および先端の技術を駆使して、製造プロセスの効率化、業務効率化、チームワーク強化、コスト削減、品質向上を実現します。このサービスは、製造業の課題を深く理解し、それに対する最適なデジタルソリューションを提供することで、企業が持続的な成長とイノベーションを達成できるようサポートします。
オンライン講座
製造業、主に購買・調達部門にお勤めの方々に向けた情報を配信しております。
新任の方やベテランの方、管理職を対象とした幅広いコンテンツをご用意しております。
お問い合わせ
コストダウンが利益に直結する術だと理解していても、なかなか前に進めることができない状況。そんな時は、newjiのコストダウン自動化機能で大きく利益貢献しよう!
(Β版非公開)