- お役立ち記事
- For managers of quality control departments in the centrifuge rotor blade manufacturing industry! Technology to improve corrosion resistance and balance performance
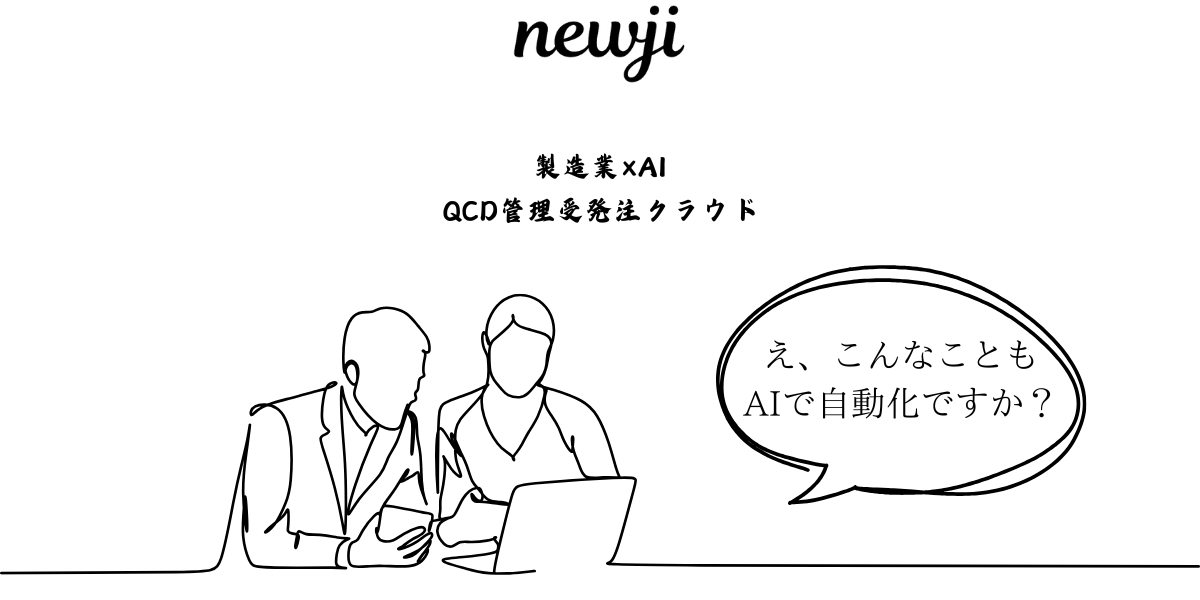
For managers of quality control departments in the centrifuge rotor blade manufacturing industry! Technology to improve corrosion resistance and balance performance
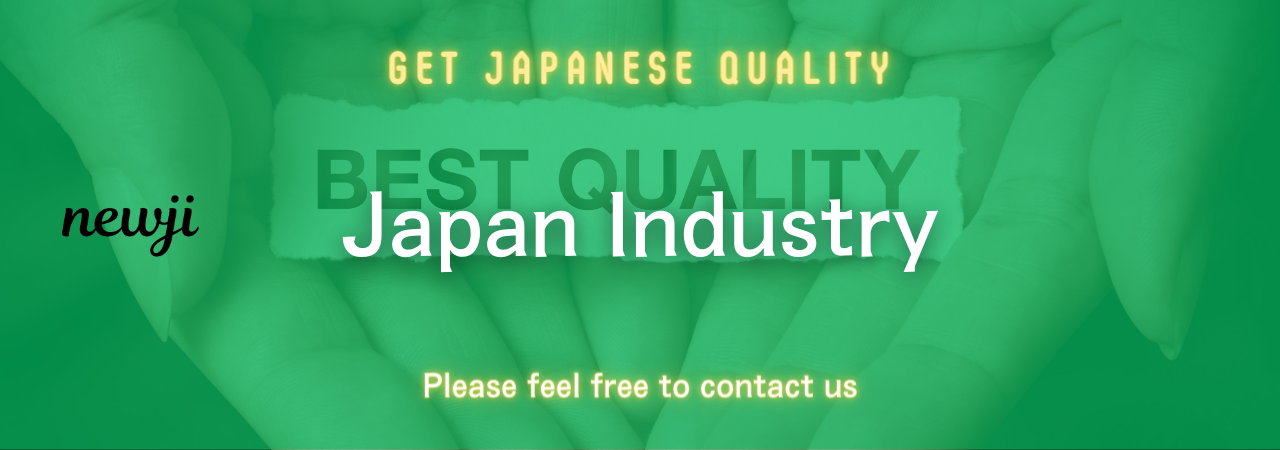
目次
Understanding Corrosion Resistance in Centrifuge Rotor Blades
Centrifuge rotor blades are pivotal components in various industrial processes, where high-speed rotation is essential for separation tasks.
Ensuring their longevity and performance is critical, particularly when they are constantly exposed to corrosive environments.
Corrosion resistance in rotor blades is not just about extending their life but also about maintaining their balance and effective functioning.
Materials used in fabricating centrifuge rotor blades play a crucial role in determining their corrosion resistance.
Commonly used materials include stainless steel, titanium, and carbon fiber composites, each offering different levels of protection against corrosion.
Stainless steel, while popular for its durability, can suffer from rust in extremely harsh environments.
Titanium, on the other hand, provides excellent resistance to corrosion but at a higher manufacturing cost.
Carbon fiber composites offer a good balance between weight, strength, and corrosion resistance, but they may require additional treatments for optimal performance.
Surface Treatments and Coatings
Surface treatments and coatings are technological interventions that have significantly improved the corrosion resistance of centrifuge rotor blades.
These treatments form protective barriers that prevent corrosive substances from damaging the blade’s surface.
Some of the commonly applied coatings include anodizing, powder coating, and specialized paint systems.
Anodizing is an electrochemical process that thickens the natural oxide layer on the surface of metal parts, enhancing their resistance to corrosion.
This is especially beneficial for aluminum and titanium rotor blades.
Powder coating involves applying a dry powder to the blade surface, which is then cured under heat to form a hard protective layer.
This method not only enhances corrosion resistance but also improves the blade’s aesthetic appearance.
Specialized paint systems are also used, comprised of various resins that form a tough protective layer against corrosive agents.
These systems are customizable based on the specific operational environment of the rotor blades, allowing for tailored solutions.
Environmental Considerations
Centrifuge rotor blades are often exposed to chemically aggressive environments, which can accelerate corrosion.
Environmental factors, such as humidity, temperature fluctuations, and exposure to chemicals, must be carefully monitored.
In factories situated in coastal areas, for instance, the high salt concentration in the air can pose a significant risk to rotor blade integrity.
To combat these environmental challenges, regularly scheduled inspections and maintenance are crucial.
Implementing preventative maintenance strategies can help identify early signs of corrosion and address them before they escalate into major issues.
Enhancing Balance Performance in Centrifuge Rotor Blades
Achieving and maintaining balance performance in centrifuge rotor blades is as crucial as ensuring their corrosion resistance.
An imbalanced rotor can lead to increased vibration, noise, and inefficiency, thereby compromising the entire centrifuge system’s function.
The Importance of Precision Manufacturing
Precision manufacturing is at the heart of achieving balance performance.
During production, even the smallest deviations in weight distribution across the rotor blade can lead to significant balance issues.
Advancements in manufacturing technologies, such as computer-aided design (CAD) and computer numerical control (CNC) machining, have facilitated the creation of rotor blades with intricate designs and precise weight distribution.
These high-precision tools allow manufacturers to produce blades that meet the exact specifications required for optimal balance.
Quality control measures, including the use of balancing machines, are employed to verify the rotor blades’ balance before they are installed in centrifuges.
Innovations in Balance Technology
Recent innovations have further enhanced balance technology for rotor blades.
Dynamic balancing systems have been developed to improve balance correction during the operation of the centrifuge.
These systems incorporate sensors and actuators that detect and counterbalance any weight imbalances in real time, minimizing the potential for vibration and noise.
Furthermore, advancements in materials science have led to the development of lightweight composite materials that naturally reduce imbalance.
These materials provide a more uniform weight distribution across the rotor, enhancing balance performance.
Maintenance for Optimal Balance
Regular maintenance plays a critical role in maintaining balance performance.
Operators should routinely check for signs of wear and tear, such as grooves or pits on the blade surfaces.
Any damage can lead to weight discrepancies that may compromise balance.
Additionally, cleaning the rotor blades to remove any accumulated debris is essential, as build-up can contribute to imbalance.
Using gentle cleaning agents and techniques helps preserve both the physical integrity and the balance of the blades.
Conclusion
For managers in the quality control departments of centrifuge rotor blade manufacturing, improving corrosion resistance and balance performance are critical objectives.
Implementing advanced surface coatings and treatments, monitoring environmental factors, utilizing precision manufacturing, and embracing technological innovations are key strategies to enhance these properties.
A proactive approach to maintenance and quality control will ensure that centrifuge rotor blades perform effectively, prolonging their lifespan and optimizing the overall efficiency of industrial processes.
資料ダウンロード
QCD調達購買管理クラウド「newji」は、調達購買部門で必要なQCD管理全てを備えた、現場特化型兼クラウド型の今世紀最高の購買管理システムとなります。
ユーザー登録
調達購買業務の効率化だけでなく、システムを導入することで、コスト削減や製品・資材のステータス可視化のほか、属人化していた購買情報の共有化による内部不正防止や統制にも役立ちます。
NEWJI DX
製造業に特化したデジタルトランスフォーメーション(DX)の実現を目指す請負開発型のコンサルティングサービスです。AI、iPaaS、および先端の技術を駆使して、製造プロセスの効率化、業務効率化、チームワーク強化、コスト削減、品質向上を実現します。このサービスは、製造業の課題を深く理解し、それに対する最適なデジタルソリューションを提供することで、企業が持続的な成長とイノベーションを達成できるようサポートします。
オンライン講座
製造業、主に購買・調達部門にお勤めの方々に向けた情報を配信しております。
新任の方やベテランの方、管理職を対象とした幅広いコンテンツをご用意しております。
お問い合わせ
コストダウンが利益に直結する術だと理解していても、なかなか前に進めることができない状況。そんな時は、newjiのコストダウン自動化機能で大きく利益貢献しよう!
(Β版非公開)