- お役立ち記事
- For managers of quality control departments in the manufacturing industry of drying oven filters for automobile paint lines! Heat resistance and dust collection efficiency
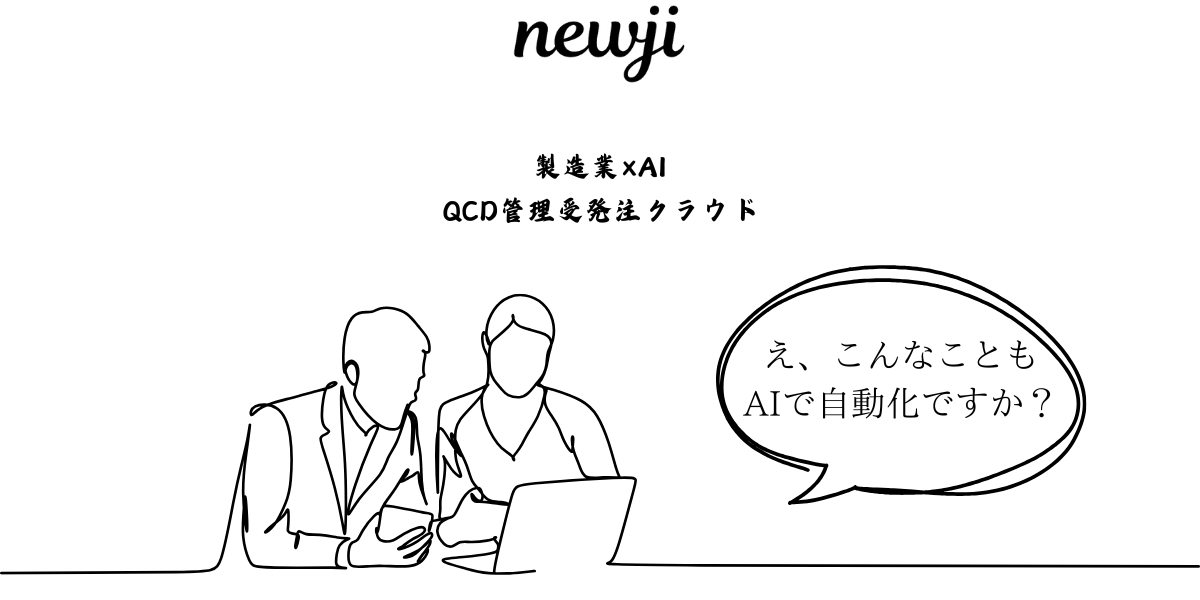
For managers of quality control departments in the manufacturing industry of drying oven filters for automobile paint lines! Heat resistance and dust collection efficiency
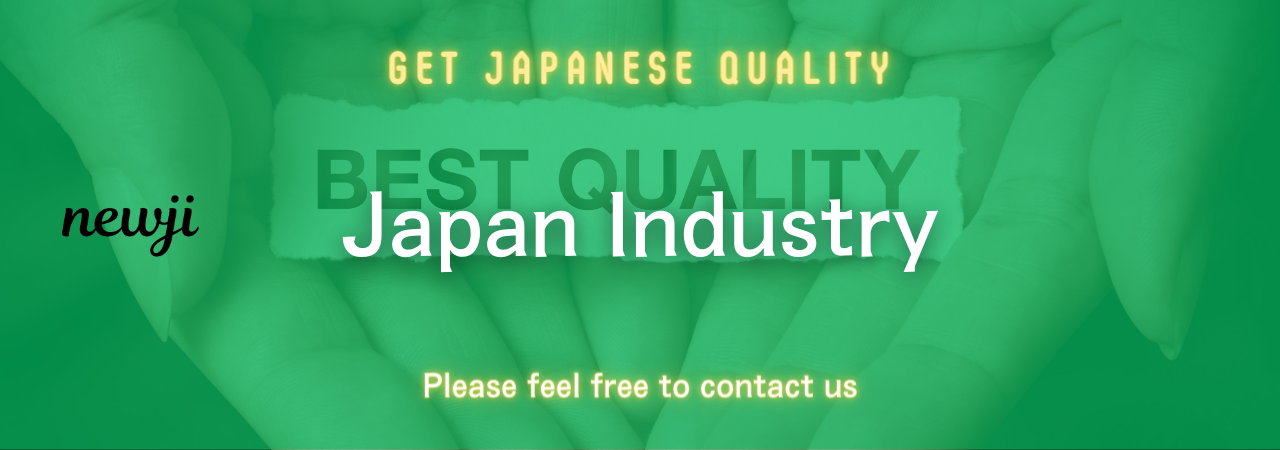
目次
Understanding the Importance of Heat Resistance in Drying Oven Filters
In the manufacturing industry, especially in automobile paint lines, drying oven filters play a crucial role.
These filters are subjected to high temperatures, making heat resistance a critical factor.
For managers of quality control departments, understanding the importance of heat resistance in these filters is essential for ensuring efficient and safe operations.
The performance of drying oven filters is largely dependent on their ability to withstand high temperatures without degrading.
High heat environments can compromise the structural integrity of the filters, leading to potential failures.
When a filter fails due to poor heat resistance, it can result in contamination of the paint line, leading to defects in the finished product.
Thus, focusing on heat resistance is vital for maintaining high-quality standards in manufacturing.
Quality control managers must ensure that the materials used in the filters are capable of withstanding the specific temperature requirements of their applications.
Selecting materials like fiberglass or similar composites, which have a proven track record of performing well at elevated temperatures, can enhance filter durability and performance.
Additionally, regular testing for heat resistance can help in identifying potential issues before they affect production.
Enhancing Heat Resistance for Improved Performance
There are several strategies that can enhance the heat resistance of drying oven filters.
One approach is through the use of advanced materials engineered for high-temperature environments.
These materials are designed to retain their structural integrity even under intense heat, providing reliable performance over extended periods.
Another strategy involves the development of composite filters that utilize multiple layers of materials, each contributing to overall heat resistance.
By combining materials with different properties, these composite filters can achieve superior performance compared to single-material filters.
This multi-layer approach helps in evenly distributing the heat load, reducing the risk of any single layer failing under stress.
Research and development teams in the manufacturing industry are constantly working on innovating filter designs.
They aim to improve heat resistance while maintaining or enhancing other essential attributes like dust collection efficiency.
Collaborations with material scientists and engineers can lead to breakthroughs in filter technology, offering quality control managers new options for improving their production processes.
Dust Collection Efficiency: A Key Factor in Filter Performance
While heat resistance is undoubtedly important, dust collection efficiency is equally critical in drying oven filters for automobile paint lines.
Dust and debris can cause considerable defects in paint jobs, compromising the quality of the final product.
Therefore, quality control managers must prioritize filters that not only withstand high temperatures but also exhibit excellent dust collection capabilities.
Efficient dust collection is achieved through the filter’s ability to capture particles of varying sizes, preventing them from contaminating the paint line.
Advanced filter designs often incorporate high-efficiency filtration media with finely-engineered pore structures.
These designs maximize the surface area available for capture, ensuring even the finest particles are trapped.
Quality control teams should regularly evaluate the dust collection performance of their filters.
This involves using standardized tests to measure the filter’s efficiency in capturing particles at different sizes and concentrations.
Any decrease in dust collection efficiency can signal the need for maintenance, replacement, or upgrading to a more advanced filter design.
Strategies for Optimizing Dust Collection Efficiency
To optimize dust collection efficiency, manufacturers can adopt several approaches.
One effective method is through the use of pleated filters, which significantly increase the surface area for capturing dust.
Pleated filters are capable of handling larger volumes of air, improving the overall efficiency of the filtration process.
Incorporating electrostatic charging into filter media is another way to enhance dust collection.
Electrostatic forces attract particles, significantly improving the capture rate.
This technique is particularly beneficial for capturing smaller particles that may evade traditional mechanical filtration methods.
Regular maintenance and timely replacement of filters are also crucial to maintaining dust collection efficiency.
Over time, filters can become clogged with collected dust, reducing airflow and decreasing their effectiveness.
By implementing a stringent maintenance schedule, quality control managers can ensure their filters continue to operate at optimal efficiency.
Balancing Heat Resistance and Dust Collection Efficiency
In the context of drying oven filters, achieving a balance between heat resistance and dust collection efficiency is essential for optimal performance.
Both these attributes are interdependent, and focusing excessively on one while neglecting the other can lead to suboptimal outcomes.
For instance, emphasizing heat resistance without considering dust collection can result in products being free from heat-induced damage but marred by particulate contamination.
Similarly, prioritizing dust collection alone might leave filters unable to withstand the rigors of high-temperature environments.
Collaborative efforts between different departments within a manufacturing facility can facilitate the development of filters that perform exceptionally on both fronts.
Quality control teams, in particular, can play a vital role in bridging the gap between research, production, and testing to ensure comprehensive performance evaluation.
The Role of Continuous Innovation
As the demand for higher quality products in the automobile industry rises, continuous innovation in drying oven filters becomes imperative.
By investing in research and development, manufacturers can stay ahead of the curve, developing filters that meet the evolving needs of their clients.
Adopting advanced technologies such as computer-aided design and simulation can help in creating filter prototypes that optimize both heat resistance and dust collection.
These tools enable engineers to visualize filter performance under various conditions, providing valuable insights that can be used to refine designs before mass production.
As technology progresses, the integration of smart features into drying oven filters is on the horizon.
Features like real-time monitoring and adaptive filtration systems can offer unprecedented control over filter performance, allowing quality control managers to make data-driven decisions in real-time.
By focusing on both heat resistance and dust collection efficiency and embracing innovation, manufacturers can enhance the quality of their filters, leading to superior paint finishes and improved customer satisfaction.
Quality control managers, in particular, stand at the forefront of ensuring these enhancements translate into tangible benefits on the production line.
資料ダウンロード
QCD調達購買管理クラウド「newji」は、調達購買部門で必要なQCD管理全てを備えた、現場特化型兼クラウド型の今世紀最高の購買管理システムとなります。
ユーザー登録
調達購買業務の効率化だけでなく、システムを導入することで、コスト削減や製品・資材のステータス可視化のほか、属人化していた購買情報の共有化による内部不正防止や統制にも役立ちます。
NEWJI DX
製造業に特化したデジタルトランスフォーメーション(DX)の実現を目指す請負開発型のコンサルティングサービスです。AI、iPaaS、および先端の技術を駆使して、製造プロセスの効率化、業務効率化、チームワーク強化、コスト削減、品質向上を実現します。このサービスは、製造業の課題を深く理解し、それに対する最適なデジタルソリューションを提供することで、企業が持続的な成長とイノベーションを達成できるようサポートします。
オンライン講座
製造業、主に購買・調達部門にお勤めの方々に向けた情報を配信しております。
新任の方やベテランの方、管理職を対象とした幅広いコンテンツをご用意しております。
お問い合わせ
コストダウンが利益に直結する術だと理解していても、なかなか前に進めることができない状況。そんな時は、newjiのコストダウン自動化機能で大きく利益貢献しよう!
(Β版非公開)