- お役立ち記事
- For managers of quality control departments in the vacuum pump gasket manufacturing industry! Material that achieves both airtightness and durability
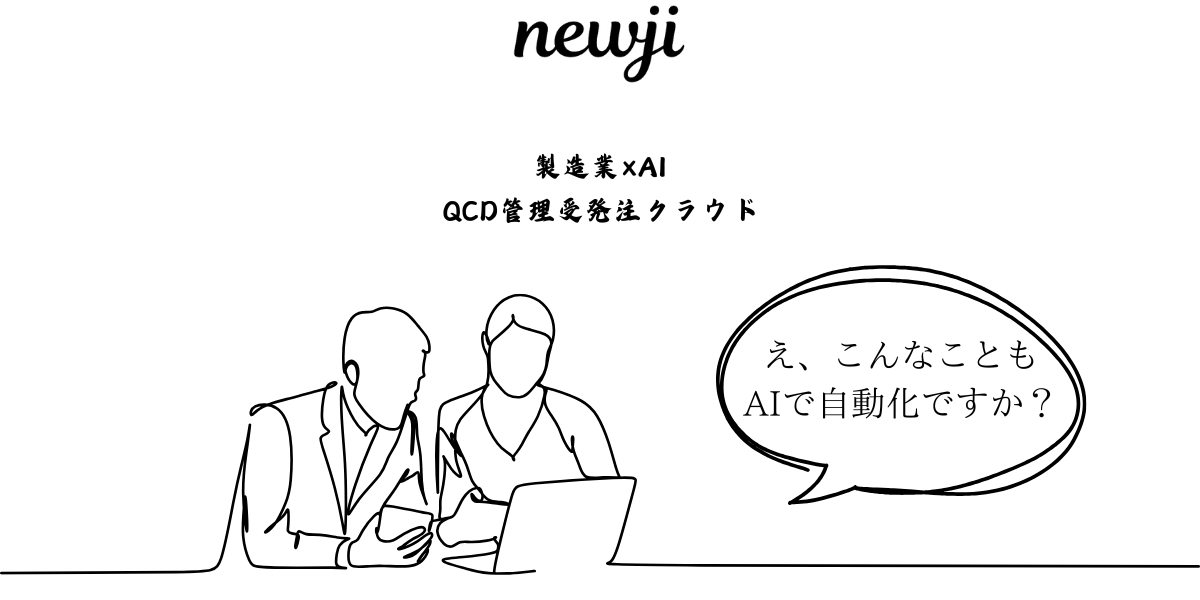
For managers of quality control departments in the vacuum pump gasket manufacturing industry! Material that achieves both airtightness and durability
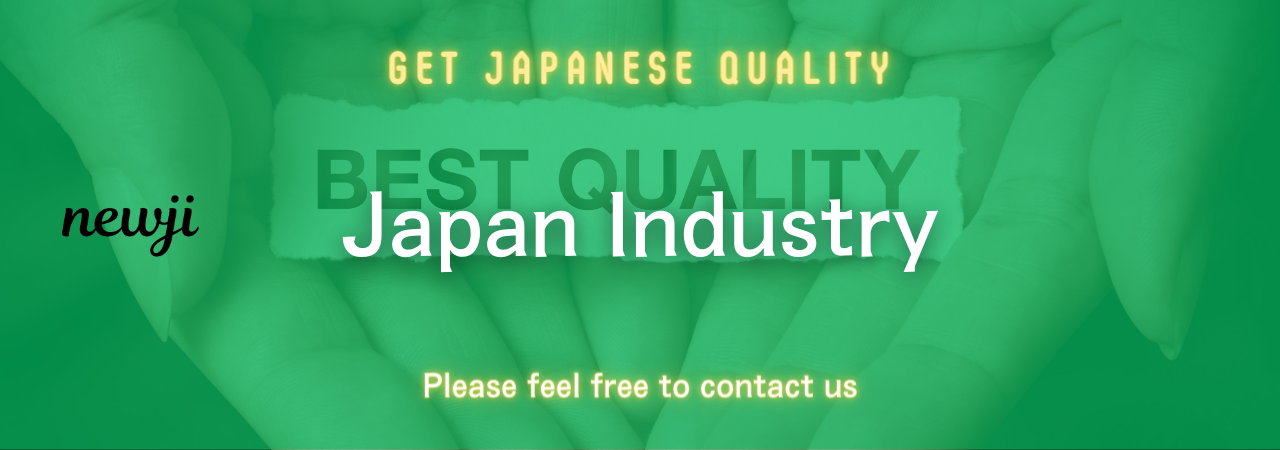
目次
Understanding the Importance of Airtightness and Durability in Vacuum Pump Gaskets
In the vacuum pump gasket manufacturing industry, the quality of your product is crucial to maintaining customer satisfaction and operational efficiency.
In particular, airtightness and durability are key considerations that directly impact the performance of the equipment in which these gaskets are used.
A vacuum pump’s effectiveness relies heavily on its ability to maintain an airtight seal, which is essential for generating the necessary vacuum pressure.
Without proper airtightness, the vacuum pump may fail to function as intended, leading to inefficiencies and equipment failure.
Moreover, durability ensures that gaskets can withstand the demands of industrial applications over extended periods, thus minimizing the need for frequent replacements or maintenance.
For managers of quality control departments, achieving a balance between these two attributes is crucial to delivering a reliable and lasting product.
The Challenges of Balancing Airtightness and Durability
Balancing airtightness and durability in gasket manufacturing presents several challenges.
These challenges arise from the complex interplay of materials, design, and manufacturing processes.
A gasket’s material must possess the inherent properties needed to deliver a tight seal while also offering the resilience to handle environmental conditions, temperature changes, and mechanical stress.
Materials that are too rigid may create an excellent seal but can crack or tear under pressure.
Conversely, materials that are too flexible may lack the necessary sealing efficiency.
For quality control managers, the task is to oversee the selection of materials and design considerations that ensure gaskets meet industry standards for both airtightness and durability.
Material Selection and Testing
A crucial step in achieving the perfect balance of airtightness and durability is selecting the right material.
Common materials used in gasket manufacturing include rubber, silicone, neoprene, and PTFE.
Each of these materials has specific properties suited to different applications and environments.
For example, silicone is known for its excellent temperature resistance and flexibility, making it ideal for high-temperature applications.
However, it may not provide the same level of chemical resistance as PTFE, which excels in corrosive environments.
The choice of material should be informed by the specific requirements of the application, and it is the role of quality control managers to develop a comprehensive understanding of these properties.
Once a suitable material is selected, rigorous testing is needed to ensure that it meets the desired levels of airtightness and durability.
This often involves subjecting prototypes to environmental simulations and stress tests to observe how they perform under various conditions.
Innovative Materials that Achieve Both Goals
Recent advancements in materials science have introduced new options that cater to both airtightness and durability.
Composite materials, for example, combine the strengths of different substances to create gaskets that perform well in various conditions.
These materials can be engineered to provide the necessary seal and withstand challenging environments.
Similarly, reinforced materials, such as those that incorporate fibers, can enhance the structural integrity of the gasket while maintaining flexibility.
These innovations provide quality control managers with new solutions to traditional challenges.
Manufacturing Process Optimization
Besides material selection, the manufacturing process itself plays a crucial role in determining the final product’s quality.
Advanced manufacturing techniques, such as precision molding and die-cutting, ensure that gaskets maintain consistent dimensions and material distribution, which is essential for a reliable seal.
Furthermore, investing in quality control systems throughout the manufacturing process can help detect potential defects early, preventing them from reaching the end user.
Incorporating automated inspection technologies, such as laser measurement and vision systems, can enhance the accuracy of quality checks.
These systems can identify variations as small as a few micrometers, providing assurance that each gasket meets design specifications.
The Role of Quality Control Managers
Quality control managers play a pivotal role in achieving both airtightness and durability in vacuum pump gaskets.
Their responsibilities include overseeing material selection, testing protocols, and manufacturing processes.
They ensure that each step is in compliance with industry standards and customer expectations.
By maintaining a meticulous quality assurance framework, managers can identify potential areas for improvement and implement strategies to mitigate risks.
Continuously evaluating and updating testing procedures is also crucial as new material options and manufacturing technologies emerge.
Adapting to Industry Trends and Customer Needs
As technology advances, the vacuum pump gasket manufacturing industry must evolve to meet new challenges and customer demands.
Emerging trends, such as the push for eco-friendly materials and increased regulatory standards, require quality control managers to stay informed and adaptable.
Understanding the specific needs of your customers and the industries they serve can guide your approach to quality control.
For instance, the automotive industry demands gaskets with exceptionally high durability due to the intense mechanical stress they endure.
Identifying such requirements and tailoring your product to meet them can amplify your competitive advantage.
Conclusion
Achieving both airtightness and durability in vacuum pump gaskets is a complex yet attainable goal.
With the right combination of material selection, testing, manufacturing process optimization, and diligent quality control, it is possible to deliver products that exceed customer expectations.
Quality control managers are at the forefront of this process, guiding their teams to explore innovative solutions and adapt to industry trends.
By doing so, they can ensure that their products remain reliable, efficient, and durable, making a lasting impact in the vacuum pump gasket manufacturing industry.
資料ダウンロード
QCD調達購買管理クラウド「newji」は、調達購買部門で必要なQCD管理全てを備えた、現場特化型兼クラウド型の今世紀最高の購買管理システムとなります。
ユーザー登録
調達購買業務の効率化だけでなく、システムを導入することで、コスト削減や製品・資材のステータス可視化のほか、属人化していた購買情報の共有化による内部不正防止や統制にも役立ちます。
NEWJI DX
製造業に特化したデジタルトランスフォーメーション(DX)の実現を目指す請負開発型のコンサルティングサービスです。AI、iPaaS、および先端の技術を駆使して、製造プロセスの効率化、業務効率化、チームワーク強化、コスト削減、品質向上を実現します。このサービスは、製造業の課題を深く理解し、それに対する最適なデジタルソリューションを提供することで、企業が持続的な成長とイノベーションを達成できるようサポートします。
オンライン講座
製造業、主に購買・調達部門にお勤めの方々に向けた情報を配信しております。
新任の方やベテランの方、管理職を対象とした幅広いコンテンツをご用意しております。
お問い合わせ
コストダウンが利益に直結する術だと理解していても、なかなか前に進めることができない状況。そんな時は、newjiのコストダウン自動化機能で大きく利益貢献しよう!
(Β版非公開)