- お役立ち記事
- For mechanical design departments! Optimization approach for structural design considering material mechanics
月間76,176名の
製造業ご担当者様が閲覧しています*
*2025年3月31日現在のGoogle Analyticsのデータより
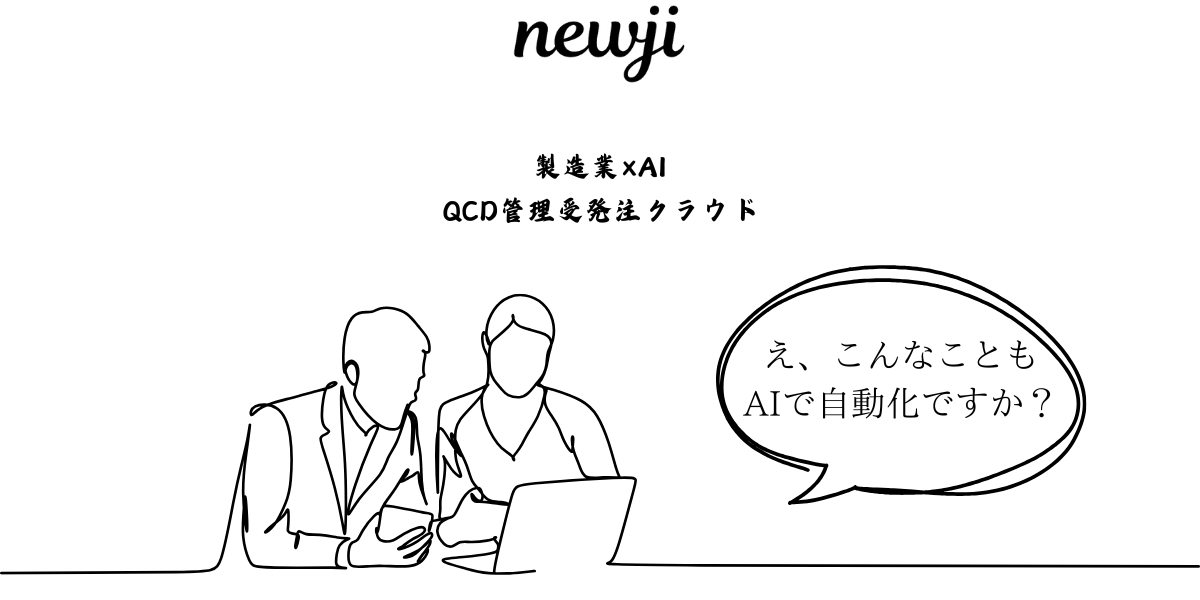
For mechanical design departments! Optimization approach for structural design considering material mechanics
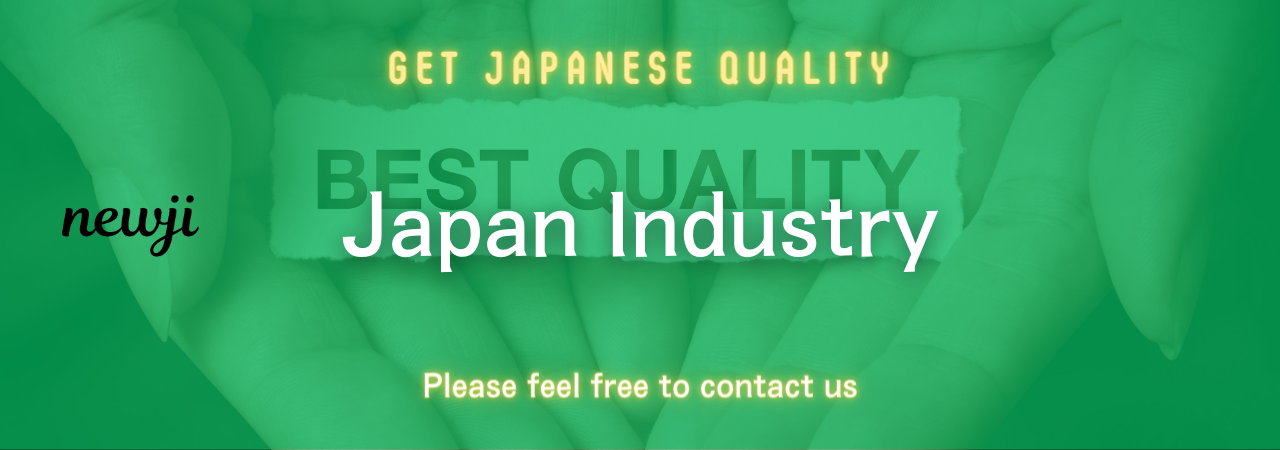
目次
Introduction to Structural Design Optimization
Structural design optimization has become an integral part of mechanical design departments, especially when seeking efficiency and innovation in engineering solutions.
Understanding material mechanics and how they influence the strength, durability, and cost of structures can significantly enhance the final product.
The aim of optimization in this context is to meet specific performance requirements while minimizing resources and reducing weight.
Let’s explore how engineers can apply optimization techniques to structural design, considering the principles of material mechanics.
Understanding Material Mechanics
Material mechanics is a vital field that deals with the behavior of solid materials under various forces, temperatures, and environmental conditions.
It examines how materials deform, break, or endure stresses.
By understanding these properties, designers can select materials that will withstand operational demands without failure.
The fundamental aspects of material mechanics include elasticity, plasticity, and fracture mechanics.
Elasticity refers to a material’s ability to return to its original shape after removing stress.
Plasticity, on the other hand, is the property that allows permanent deformation.
Fracture mechanics focuses on the growth of cracks and material failure.
Each of these factors must be considered during structural design optimization to ensure reliability and performance.
Principles of Structural Design Optimization
The primary goal of structural design optimization is to improve the performance of a structure while optimizing resource use.
This involves finding the best compromise between material use, strength, and cost.
Optimization can be approached through various methods, including iterative testing, computational simulations, and mathematical modeling.
An essential principle in structural design optimization is the trade-off between strength and weight.
Stronger materials are often heavier and more expensive.
Thus, finding an optimal balance is crucial for both functionality and budget.
Using software tools and simulations can aid in visualizing how different materials respond under various conditions.
This allows engineers to predict performance and make well-informed decisions about which materials and designs will work best.
Steps in the Optimization Process
1. **Define Goals and Constraints**: Establish what the design must achieve, including load-bearing requirements, environmental conditions, and material limitations.
2. **Select and Analyze Materials**: Choose materials based on their mechanical properties.
Consider factors such as tensile strength, elasticity, weight, and cost.
3. **Create Initial Designs**: Develop several design concepts using initial material selections.
Each design should meet the basic requirements set out in the first step.
4. **Simulation and Testing**: Utilize computer-aided design (CAD) tools and finite element analysis (FEA) to simulate how each design performs.
Identify weaknesses and areas for improvement.
5. **Iterative Improvement**: Refine the designs based on simulation outcomes.
Make necessary adjustments to materials, shape, or structure.
6. **Cost-Benefit Analysis**: Calculate the costs associated with each design, weighing them against performance improvements.
Choose a design that offers the best value for cost.
Role of Technology in Optimization
Advancements in technology have revolutionized the way structural design optimization is conducted.
With the rise of artificial intelligence (AI) and machine learning, engineers can now predict outcomes with greater accuracy than ever before.
AI-driven software can analyze vast amounts of data to determine the most efficient material combinations and structural designs.
This can result in innovative solutions that may have been overlooked using traditional methods.
Additionally, 3D printing technologies have expanded the possibilities for structural optimization by allowing for rapid prototyping.
Engineers can create physically tangible models and test them under real-world conditions.
This can significantly save time and reduce costs during the design phase.
Environmental Considerations
Modern structural design must also account for environmental impact.
Engineers are increasingly tasked with creating sustainable structures that minimize waste and energy consumption.
Optimizing structural design with recycled materials or sustainable alternatives can contribute to reducing the carbon footprint.
The design phase should include assessing the environmental impact of material choices and the lifecycle assessment of structures.
Challenges in Structural Optimization
Despite its benefits, structural design optimization comes with its own set of challenges.
One primary challenge is accurately predicting human factors, such as operation errors or unexpected usage conditions.
These can introduce variables that affect optimal designs.
Another difficulty is the complexity of material behavior under extreme conditions.
Understanding and predicting material responses during events like earthquakes or high-load situations can be complex.
Finally, balancing multiple conflicting objectives, such as cost, safety, and sustainability, requires careful consideration and sometimes creative compromises.
Conclusion
Incorporating optimization approaches in structural design is crucial for modern mechanical design departments striving for efficiency and innovation.
By considering material mechanics, engineers can create structures that not only meet performance criteria but do so efficiently and cost-effectively.
While technology and tools provide significant support, understanding the fundamental mechanics and maintaining a focus on sustainable practices ensure designs that are robust and environmentally conscious.
Continuous advancements in materials and technologies will further enhance optimization strategies, making it a continuously evolving field.
資料ダウンロード
QCD管理受発注クラウド「newji」は、受発注部門で必要なQCD管理全てを備えた、現場特化型兼クラウド型の今世紀最高の受発注管理システムとなります。
ユーザー登録
受発注業務の効率化だけでなく、システムを導入することで、コスト削減や製品・資材のステータス可視化のほか、属人化していた受発注情報の共有化による内部不正防止や統制にも役立ちます。
NEWJI DX
製造業に特化したデジタルトランスフォーメーション(DX)の実現を目指す請負開発型のコンサルティングサービスです。AI、iPaaS、および先端の技術を駆使して、製造プロセスの効率化、業務効率化、チームワーク強化、コスト削減、品質向上を実現します。このサービスは、製造業の課題を深く理解し、それに対する最適なデジタルソリューションを提供することで、企業が持続的な成長とイノベーションを達成できるようサポートします。
製造業ニュース解説
製造業、主に購買・調達部門にお勤めの方々に向けた情報を配信しております。
新任の方やベテランの方、管理職を対象とした幅広いコンテンツをご用意しております。
お問い合わせ
コストダウンが利益に直結する術だと理解していても、なかなか前に進めることができない状況。そんな時は、newjiのコストダウン自動化機能で大きく利益貢献しよう!
(β版非公開)