- お役立ち記事
- For mid-level employees in the equipment maintenance department! How to significantly reduce equipment downtime with TPM activities
For mid-level employees in the equipment maintenance department! How to significantly reduce equipment downtime with TPM activities
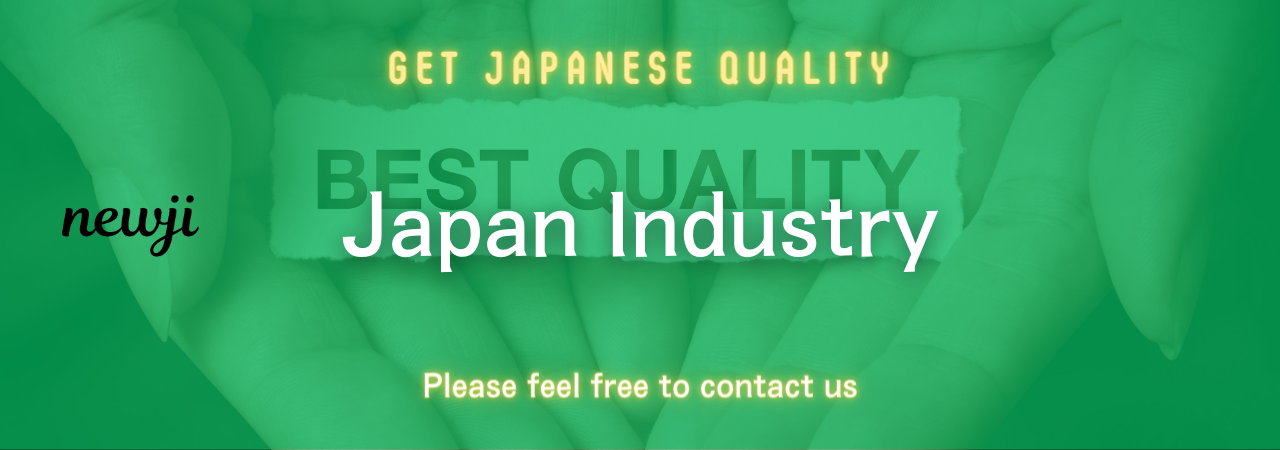
目次
Understanding TPM and Its Importance
Total Productive Maintenance, or TPM, is a systematic approach focused on maintaining and improving the production and quality systems through the machines, equipment, processes, and employees that add value to an organization.
TPM is designed to increase production efficiency by minimizing downtime and improving productivity.
For mid-level employees in the equipment maintenance department, understanding and implementing TPM activities can play a crucial role in reducing equipment downtime significantly.
A reliable equipment maintenance strategy is vital for any company aiming for higher productivity and cost reduction.
TPM pivots on maintenance teams, operators, engineers, and management working together to achieve a cultural change.
The goal is to ensure all employees are committed to machine maintenance and aim to eliminate all machine downtime.
The Core Pillars of TPM
TPM is built around eight pillars, each designed to tackle different aspects of machinery maintenance and efficiency.
Understanding these pillars is the first step in implementing TPM activities effectively.
1. Autonomous Maintenance
Autonomous Maintenance empowers operators to take care of small maintenance tasks, such as cleaning and lubrication.
This ensures equipment is always in top condition and reduces the workload on maintenance teams.
Operators become responsible for their machines, which increases accountability and helps in identifying issues early.
2. Planned Maintenance
Planned Maintenance involves scheduling maintenance tasks to prevent unexpected breakdowns.
By using machine records and historical data, teams can predict when maintenance should occur, reducing sudden downtime.
This proactive approach extends machine life and increases reliability.
3. Focused Improvement
Focused Improvement, also known as Kaizen, is the continuous effort to enhance equipment operation.
Maintenance teams identify specific goals to improve machinery efficiency and reduce losses.
Regular improvement activities lead to substantial gains in productivity and quality.
4. Quality Maintenance
Quality Maintenance focuses on maintaining the conditions to prevent errors and defects.
By maintaining equipment precisely, teams ensure that output quality remains high, reducing rework and waste.
Effective quality maintenance requires attention to detail and dedication to precision operations.
5. Early Equipment Management
Early Equipment Management leverages knowledge gained from past equipment failures and successes.
By involving operators and maintenance staff in the design and installation stages of new equipment, companies can foresee potential issues and implement improvements beforehand.
This foresight results in fewer breakdowns and better overall equipment efficiency.
6. Training and Education
Training and Education is crucial for building a skilled workforce capable of implementing TPM activities.
Providing continuous training ensures that employees are equipped with the knowledge to maintain machines effectively.
Knowledgeable workers are more adept at troubleshooting issues and maintaining optimal equipment performance.
7. Safety, Health, and Environment
The Safety, Health, and Environment pillar ensures that TPM activities do not compromise the well-being of employees or the environment.
Safe working conditions and environmentally friendly practices lead to fewer accidents and enhance the company’s reputation.
Commitment to these standards creates a safer and more productive workplace.
8. TPM in Office Functions
TPM can also be applied to office functions to improve efficiency and productivity in administrative areas.
This includes optimizing processes, reducing waste, and enhancing teamwork in non-manufacturing tasks.
Aligning office functions with TPM principles supports overall organizational goals.
Steps to Implementing TPM
Successfully implementing TPM requires careful planning and execution.
Here are some steps that mid-level employees can take to introduce and integrate TPM activities within their department:
Step 1: Gain Management Support
For TPM to be effective, it must have the support and commitment of management.
Present the benefits of TPM, such as reduced downtime and cost savings, to gain the backing needed to implement changes.
Step 2: Conduct a Pilot Project
Choose a small area or piece of equipment to start with a TPM pilot project.
This allows you to test the effectiveness of TPM and gather data to showcase its impact.
Successful pilot projects can serve as examples to encourage further TPM adoption.
Step 3: Train Employees
Provide comprehensive training for all employees involved in maintenance tasks.
Ensure they understand TPM principles and their roles in maintaining equipment.
An informed team is key to effective maintenance and problem-solving.
Step 4: Establish TPM Teams
Form cross-functional TPM teams that include operators, maintenance staff, and management.
These teams will collaborate to identify areas for improvement and share insights across departments.
Teams that work together promote a culture of continuous improvement.
Step 5: Monitor and Measure
Implement metrics to track the performance of TPM activities.
Monitor downtime, maintenance costs, and equipment efficiency to assess the success of your TPM initiatives.
Regular reviews allow you to make necessary adjustments and celebrate achievements.
Benefits of TPM for Mid-Level Employees
Adopting TPM activities brings numerous advantages for mid-level employees in the equipment maintenance department.
Some of the notable benefits include:
Improved Equipment Reliability
Through planned maintenance and proactive measures, equipment operates more reliably, reducing unexpected shutdowns and delays.
Increased Productivity
Efficient machines mean more productive workdays.
TPM minimizes downtime, allowing the organization to maintain a steady production pace.
Skill Enhancement
Training enhances employees’ skills, making them more proficient at identifying and resolving issues, which adds value to their role.
Reduced Maintenance Costs
Preventive and predictive maintenance reduces repair costs, as issues are addressed before they escalate.
This extends the lifespan of machinery and limits the need for costly replacements.
A Safer Work Environment
With a focus on safety and preventive maintenance, TPM contributes to a safer workplace, reducing the risk of accidents and injuries.
For mid-level employees in equipment maintenance, embracing TPM activities can lead to significant downtime reduction and improved operational efficiency.
By understanding and implementing TPM pillars and strategies, maintenance teams can contribute to a more productive, cost-efficient, and safer working environment.
資料ダウンロード
QCD調達購買管理クラウド「newji」は、調達購買部門で必要なQCD管理全てを備えた、現場特化型兼クラウド型の今世紀最高の購買管理システムとなります。
ユーザー登録
調達購買業務の効率化だけでなく、システムを導入することで、コスト削減や製品・資材のステータス可視化のほか、属人化していた購買情報の共有化による内部不正防止や統制にも役立ちます。
NEWJI DX
製造業に特化したデジタルトランスフォーメーション(DX)の実現を目指す請負開発型のコンサルティングサービスです。AI、iPaaS、および先端の技術を駆使して、製造プロセスの効率化、業務効率化、チームワーク強化、コスト削減、品質向上を実現します。このサービスは、製造業の課題を深く理解し、それに対する最適なデジタルソリューションを提供することで、企業が持続的な成長とイノベーションを達成できるようサポートします。
オンライン講座
製造業、主に購買・調達部門にお勤めの方々に向けた情報を配信しております。
新任の方やベテランの方、管理職を対象とした幅広いコンテンツをご用意しております。
お問い合わせ
コストダウンが利益に直結する術だと理解していても、なかなか前に進めることができない状況。そんな時は、newjiのコストダウン自動化機能で大きく利益貢献しよう!
(Β版非公開)