- お役立ち記事
- For mid-level employees in the facility management department! A method to maximize equipment availability using reliability engineering
月間76,176名の
製造業ご担当者様が閲覧しています*
*2025年3月31日現在のGoogle Analyticsのデータより
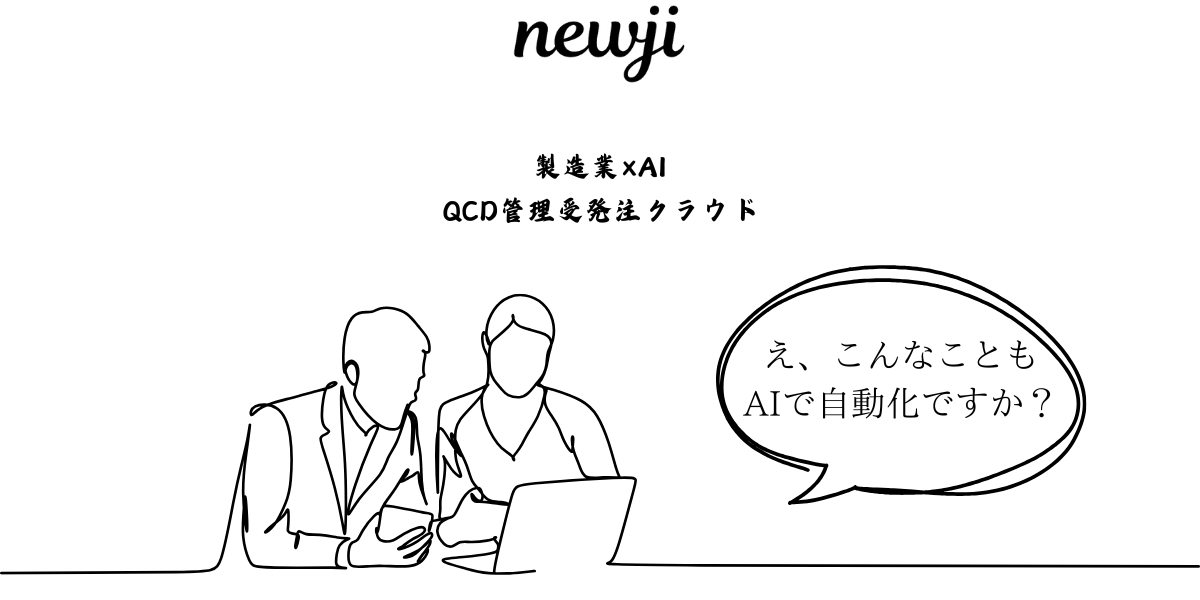
For mid-level employees in the facility management department! A method to maximize equipment availability using reliability engineering
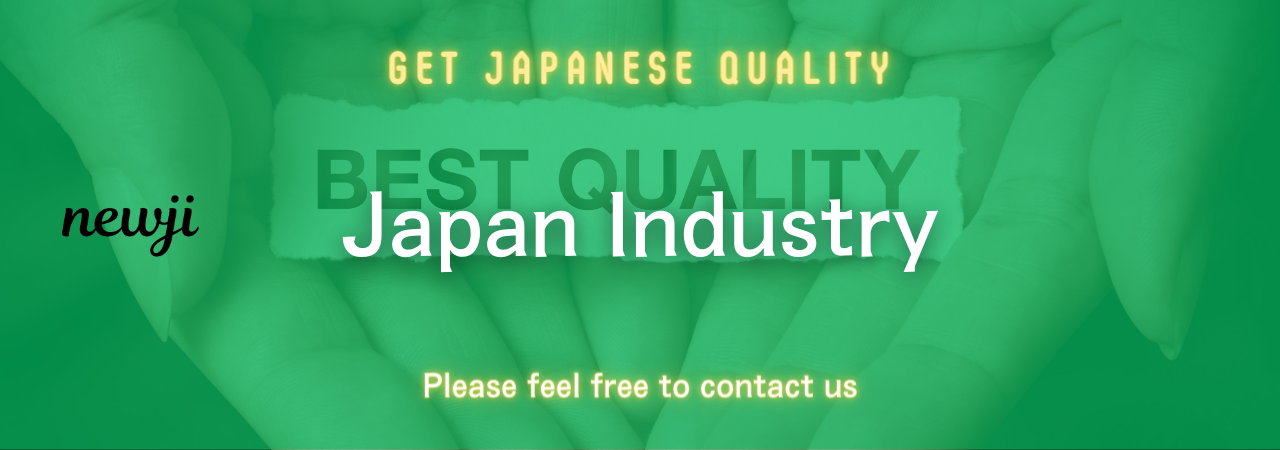
目次
Understanding Reliability Engineering
Reliability engineering is a key discipline within facility management that focuses on ensuring that equipment performs its required functions without failure for a specified period of time.
For mid-level employees in the facility management department, understanding and applying reliability engineering can maximize equipment availability, reduce downtime, and increase overall productivity.
Reliability engineering involves applying analytical techniques to predict failures, prevent them, and efficiently manage maintenance schedules.
These techniques can help identify potential failures before they occur, allowing for proactive measures.
In the world of facility management, the goal is to have equipment functioning at optimal levels with the least amount of interruptions.
The Importance of Equipment Availability
Equipment availability is critical because it directly impacts an organization’s ability to meet production targets and maintain operational efficiency.
When equipment fails or is unavailable, it can cause delays that have a ripple effect throughout the organization.
Mid-level employees must focus on maintaining high equipment availability by employing strategies that reduce downtime.
Reliability engineering helps ensure that machinery and equipment are reliable, reducing the likelihood of unexpected failures.
By improving the reliability of equipment, facility managers can increase its availability, thus ensuring continuous and efficient operations.
Analyzing Equipment Performance
The first step in maximizing equipment availability through reliability engineering is to analyze current equipment performance.
This involves gathering data on equipment usage, failure rates, and downtime incidents.
Data collection tools such as sensors, IoT devices, and maintenance management software can help in gathering accurate and real-time data.
After collecting the data, mid-level employees can analyze it to identify patterns or trends that may indicate potential reliability issues.
By understanding these patterns, facility managers can make informed decisions about required interventions that could enhance equipment reliability.
Preventive Maintenance Strategies
Preventive maintenance is a strategy that involves regular, planned maintenance activities to prevent equipment failures.
One effective approach is to create a preventive maintenance schedule based on the collected data and analysis performed during the performance analysis phase.
The schedule should include tasks such as inspections, lubrication, adjustments, and parts replacements.
Regularly implementing such a schedule can ensure that equipment is kept in optimal condition, reducing the risk of unexpected failures.
Moreover, preventive maintenance helps extend the lifespan of equipment, leading to long-term cost savings for the organization.
Predictive Maintenance with Reliability Engineering
Predictive maintenance is another approach that can help maximize equipment availability.
Unlike preventive maintenance, which is time-based, predictive maintenance uses real-time data and analytics to forecast when equipment might fail.
This allows facility managers to take action just before a failure is likely to occur, thus preventing unexpected breakdowns.
To implement predictive maintenance, mid-level facility management employees can make use of advanced technologies such as machine learning algorithms, artificial intelligence, and IoT sensors.
These technologies enable the analysis of real-time data on equipment conditions and predict potential issues before they result in failure.
Predictive maintenance not only improves reliability but also optimizes maintenance schedules and resource allocation, ultimately reducing maintenance costs.
Implementation of Reliability-Centered Maintenance (RCM)
Reliability-Centered Maintenance (RCM) is a systematic approach that aims to determine the maintenance requirements of equipment based on its criticality.
The goal of RCM is to identify and implement maintenance strategies that manage risks, optimize resources, and maintain equipment performance.
For mid-level employees, implementing RCM involves a series of steps, including:
1. Determining the functions and performance standards of the equipment.
2. Identifying failure modes that can affect these functions.
3. Analyzing the effects and consequences of these failures.
4. Selecting appropriate maintenance strategies and tasks to prevent or mitigate the failure modes.
RCM allows for a customized maintenance approach that is tailored to the specific needs and operational conditions of each piece of equipment.
Root Cause Analysis for Continuous Improvement
Incorporating root cause analysis into reliability engineering practices can help mid-level employees in facility management improve equipment reliability continuously.
Root cause analysis involves identifying the underlying reasons for equipment failures to prevent recurrence.
Whenever a failure occurs, conducting a thorough root cause analysis is crucial to understand what led to the breakdown.
Once the root cause is identified, corrective actions can be implemented, and similar failures can be prevented in the future.
Regularly applying root cause analysis not only improves equipment reliability but also fosters a culture of continuous improvement within the organization.
Leveraging Technology for Enhanced Equipment Availability
Technology plays a significant role in implementing reliability engineering techniques in facility management.
For mid-level employees, leveraging technology means utilizing advanced tools and platforms to enhance equipment availability.
Some technology tools that can be used include:
– Computerized Maintenance Management Systems (CMMS)
– Internet of Things (IoT) for real-time monitoring
– Machine learning and artificial intelligence for predictive analytics
– Advanced data analytics platforms for performance analysis
These tools provide insights into equipment performance and maintenance needs, allowing for data-driven decision-making.
By embracing technology, facility managers can create more efficient, responsive, and reliable maintenance processes.
Training and Skill Development
To effectively implement reliability engineering practices, mid-level employees in the facility management department must have the right skills and training.
Investing in training programs that focus on reliability engineering principles, predictive maintenance technologies, and data analysis can empower employees to effectively manage equipment availability.
Skill development will ensure that employees can efficiently use the tools and technologies required to monitor, analyze, and maintain equipment performance.
Continuous learning and development can lead to a more knowledgeable and capable workforce, resulting in improved equipment reliability and availability.
Conclusion
For mid-level employees in the facility management department, applying reliability engineering techniques is key to maximizing equipment availability.
By understanding equipment performance, employing preventive and predictive maintenance strategies, and leveraging technology, facility managers can significantly enhance operational efficiency.
Reliability engineering not only helps reduce downtime and maintenance costs but also extends the lifespan of equipment.
Through continuous improvement efforts such as root cause analysis and training, mid-level employees can contribute meaningfully to achieving high reliability and availability in their facilities.
資料ダウンロード
QCD管理受発注クラウド「newji」は、受発注部門で必要なQCD管理全てを備えた、現場特化型兼クラウド型の今世紀最高の受発注管理システムとなります。
ユーザー登録
受発注業務の効率化だけでなく、システムを導入することで、コスト削減や製品・資材のステータス可視化のほか、属人化していた受発注情報の共有化による内部不正防止や統制にも役立ちます。
NEWJI DX
製造業に特化したデジタルトランスフォーメーション(DX)の実現を目指す請負開発型のコンサルティングサービスです。AI、iPaaS、および先端の技術を駆使して、製造プロセスの効率化、業務効率化、チームワーク強化、コスト削減、品質向上を実現します。このサービスは、製造業の課題を深く理解し、それに対する最適なデジタルソリューションを提供することで、企業が持続的な成長とイノベーションを達成できるようサポートします。
製造業ニュース解説
製造業、主に購買・調達部門にお勤めの方々に向けた情報を配信しております。
新任の方やベテランの方、管理職を対象とした幅広いコンテンツをご用意しております。
お問い合わせ
コストダウンが利益に直結する術だと理解していても、なかなか前に進めることができない状況。そんな時は、newjiのコストダウン自動化機能で大きく利益貢献しよう!
(β版非公開)