- お役立ち記事
- For mid-level employees in the facility management department! Fundamentals of reliability engineering to maximize equipment availability
For mid-level employees in the facility management department! Fundamentals of reliability engineering to maximize equipment availability
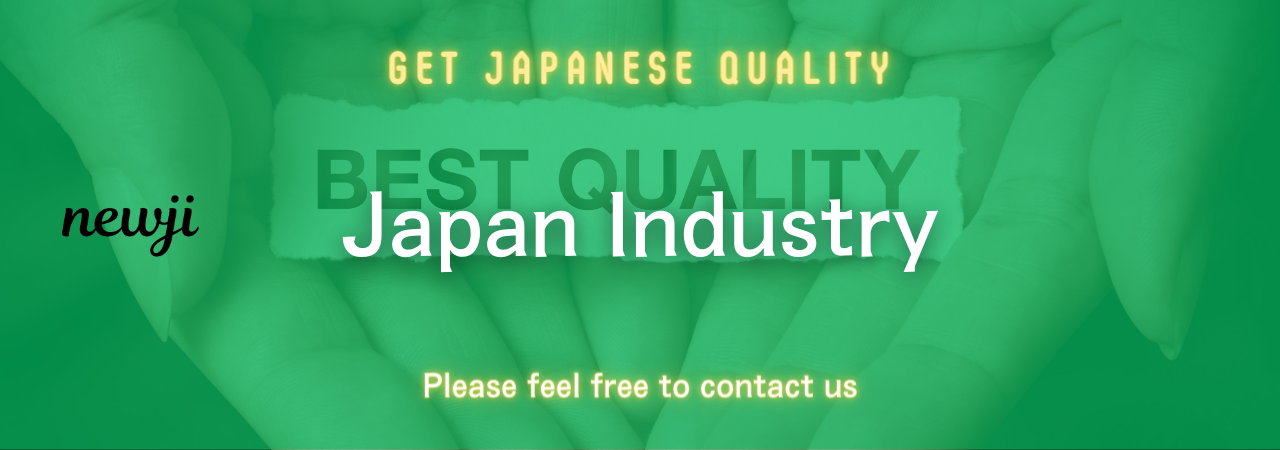
目次
Understanding Reliability Engineering
Reliability engineering is a crucial component in facility management, ensuring that equipment functions optimally and consistently over time.
It involves a set of principles and practices aimed at maximizing equipment availability and minimizing downtime.
For mid-level employees in the facility management department, understanding the fundamentals of reliability engineering is crucial for maintaining efficient operation and enhancing productivity.
Reliability engineering focuses on predicting, analyzing, and enhancing the dependability and performance of equipment.
By employing various techniques, facility managers can identify potential failures and take preemptive actions to mitigate risks.
This proactive approach helps ensure that equipment does not only function but performs reliably throughout its lifecycle.
Key Concepts in Reliability Engineering
Reliability engineering encompasses several key concepts that should be familiar to facility management professionals.
Understanding these concepts will help in effectively applying reliability engineering principles to improve equipment availability.
First, mean time between failures (MTBF) is a critical measure in reliability engineering.
It represents the average time elapsed between successive failures of a system or component.
A higher MTBF indicates greater reliability, meaning the equipment can operate for longer periods without experiencing breakdowns.
Second, mean time to repair (MTTR) is the average time required to repair a failed component or system and restore it to operational condition.
Reducing MTTR is essential in minimizing downtime and maintaining high equipment availability.
Third, failure mode and effects analysis (FMEA) is a systematic process for identifying potential failures in a system, understanding their impacts, and determining corrective actions.
FMEA helps prioritize risks and focus efforts on the most critical areas, enhancing reliability and preventing future breakdowns.
Lastly, reliability-centered maintenance (RCM) is an approach that aims to determine the optimal maintenance strategy to ensure equipment reliability.
RCM involves evaluating the functions of equipment, understanding potential failure modes, and deciding on the most effective maintenance practices to improve performance.
The Importance of Reliability Engineering
For facility managers, incorporating reliability engineering practices is paramount to achieving operational excellence.
Here are some reasons why reliability engineering is important:
1. **Improved Equipment Performance:** By applying reliability engineering principles, facility managers can identify and address performance bottlenecks.
This leads to smoother operations, reduced operational disruptions, and enhanced output efficiency.
2. **Cost Reduction:** Reliability engineering helps minimize costly repairs and replacements by preventing equipment failures.
Implementing effective maintenance strategies saves costs associated with emergency repairs and unplanned downtime.
3. **Higher Equipment Availability:** A proactive approach towards equipment management leads to increased availability.
Improved reliability ensures that equipment is ready and operational whenever needed, supporting seamless facility operations.
4. **Extended Equipment Life:** Reliability engineering practices contribute to extending the service life of equipment.
By maintaining optimal operational conditions and addressing minor issues before they escalate, equipment can last longer and provide better ROI.
Implementing Reliability Engineering
To successfully implement reliability engineering in your facility management department, consider the following steps:
1. **Conduct a Reliability Assessment:** Begin by evaluating the current reliability status of your equipment.
This involves analyzing historical performance data, maintenance records, and failure occurrences to identify patterns and areas for improvement.
2. **Perform FMEA:** Use failure mode and effects analysis to systematically review potential failure points in your equipment.
Prioritize risks and develop action plans to address the most critical issues.
3. **Develop a Maintenance Strategy:** Based on the findings of your reliability assessment and FMEA, establish a comprehensive maintenance strategy.
Consider adopting reliability-centered maintenance to tailor your approach to the specific needs of each piece of equipment.
4. **Implement Predictive Maintenance:** Incorporate predictive maintenance techniques to monitor equipment conditions in real-time.
Utilize advanced technologies such as sensors and data analytics to predict potential failures and address them before they occur.
5. **Continuous Improvement:** Reliability engineering is an ongoing process.
Continuously review the performance of your equipment and adjust strategies as necessary.
Encourage a culture of improvement and empower your team to contribute their insights and suggestions.
Challenges and Considerations
While reliability engineering offers numerous benefits, there are challenges to consider when implementing these practices in facility management:
– **Resource Allocation:** Implementing a robust reliability engineering program requires dedicated resources and investment.
Ensure that your department has the necessary tools, training, and support to facilitate a successful implementation.
– **Data Management:** Analyzing and interpreting data effectively is key to reliability engineering.
Establish systems for capturing and managing data to enable informed decision-making and accurate predictions.
– **Cultural Shift:** Moving towards a reliability-centered approach may require a cultural shift within the organization.
Foster teamwork, open communication, and collaboration to align everyone towards achieving reliability goals.
Conclusion
For mid-level employees in the facility management department, understanding the fundamentals of reliability engineering is instrumental in maximizing equipment availability and optimizing operations.
By embracing concepts such as MTBF, MTTR, FMEA, and reliability-centered maintenance, facility managers can enhance equipment performance, reduce costs, and ensure seamless facility operations.
Implementing reliability engineering practices requires careful planning and execution, but the long-term benefits make it a valuable investment.
Overcoming challenges and fostering a continuous improvement mindset will help your department effectively apply reliability engineering principles and contribute to the overall success of your facility.
資料ダウンロード
QCD調達購買管理クラウド「newji」は、調達購買部門で必要なQCD管理全てを備えた、現場特化型兼クラウド型の今世紀最高の購買管理システムとなります。
ユーザー登録
調達購買業務の効率化だけでなく、システムを導入することで、コスト削減や製品・資材のステータス可視化のほか、属人化していた購買情報の共有化による内部不正防止や統制にも役立ちます。
NEWJI DX
製造業に特化したデジタルトランスフォーメーション(DX)の実現を目指す請負開発型のコンサルティングサービスです。AI、iPaaS、および先端の技術を駆使して、製造プロセスの効率化、業務効率化、チームワーク強化、コスト削減、品質向上を実現します。このサービスは、製造業の課題を深く理解し、それに対する最適なデジタルソリューションを提供することで、企業が持続的な成長とイノベーションを達成できるようサポートします。
オンライン講座
製造業、主に購買・調達部門にお勤めの方々に向けた情報を配信しております。
新任の方やベテランの方、管理職を対象とした幅広いコンテンツをご用意しております。
お問い合わせ
コストダウンが利益に直結する術だと理解していても、なかなか前に進めることができない状況。そんな時は、newjiのコストダウン自動化機能で大きく利益貢献しよう!
(Β版非公開)