- お役立ち記事
- For mid-level employees in the manufacturing operations department! Best practices for efficiently proceeding with 5S activities
For mid-level employees in the manufacturing operations department! Best practices for efficiently proceeding with 5S activities
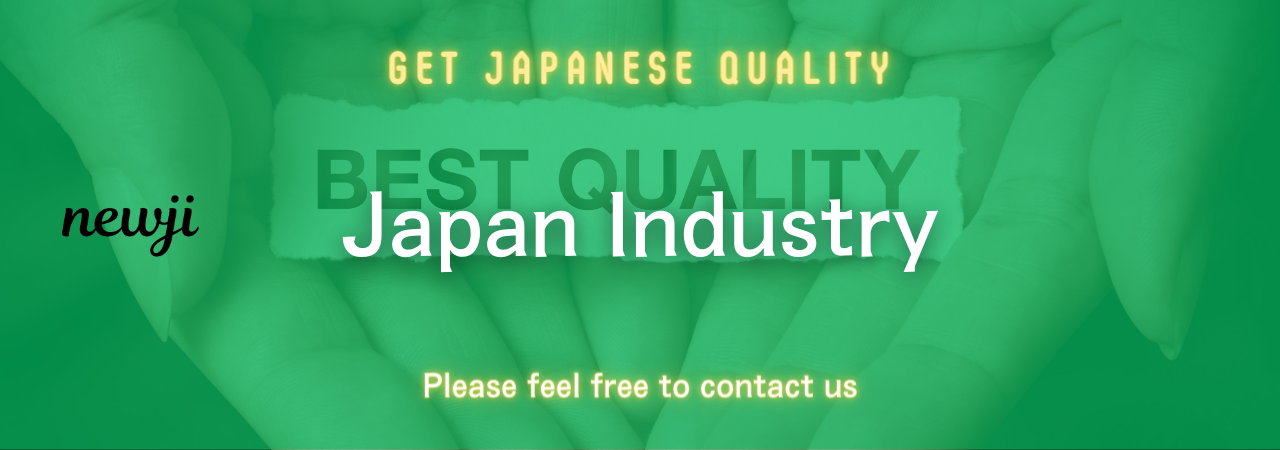
目次
Understanding the Importance of 5S in Manufacturing
5S is a workplace organization method that boosts efficiency and safety in manufacturing environments.
For mid-level employees in the manufacturing operations department, mastering 5S is crucial.
It stands for Sort, Set in Order, Shine, Standardize, and Sustain.
Each step plays a significant role in optimizing work processes and improving productivity.
Let’s delve into why understanding and implementing 5S can make a difference in manufacturing operations.
Sort: Eliminating Clutter and Enhancing Efficiency
The first step in 5S activities is Sorting.
It involves identifying and removing unnecessary items from the workplace.
This action helps reduce clutter, making it easier for employees to focus on essential tasks.
Start by evaluating all tools, materials, and equipment present in the work area.
Determine which items are essential for daily operations and which are redundant.
Encourage regular audits of inventory to prevent the accumulation of unnecessary items.
This practice ensures a clean and organized workspace, leading to increased efficiency.
A clutter-free environment allows for smoother workflow and reduces the time spent searching for tools or materials.
Set in Order: Streamlining Workspace Organization
Once unnecessary items are eliminated, the next step is to Set in Order the remaining essentials.
The goal is to create a logical arrangement that facilitates easy access and flow.
Organize tools and materials in a manner that minimizes movement and maximizes efficiency.
Consider using visual management tools like labels, color coding, and shadow boards.
These tools provide visual cues that help employees quickly identify the location of each item.
A well-organized workspace reduces errors, speeds up processes, and enhances overall safety.
Shine: Maintaining a Clean and Tidy Work Environment
The third step, Shine, emphasizes the importance of cleanliness in the workplace.
Regular cleaning and maintenance ensure that the workspace remains free of dust, debris, and potential hazards.
A clean environment contributes to the well-being of employees and extends the lifespan of equipment.
Implement daily cleaning routines that involve all team members.
Encourage ownership of personal workstations, empowering employees to take pride in maintaining their areas.
Shine not only enhances morale but also prevents equipment malfunctions and production delays.
Standardize: Implementing Consistent Procedures
Standardization is the key to sustaining the improvements made through Sort, Set in Order, and Shine.
This step involves developing standardized procedures and guidelines for maintaining the organization.
Create visual guides, checklists, and standard operating procedures to ensure consistency.
Involve team members in developing these standards, as they provide valuable insights into the work process.
Regularly review and update the procedures to adapt to changes in operations or technology.
Standardization ensures that everyone follows the same practices, reducing variability and improving quality control.
Sustain: Cultivating a Culture of Continuous Improvement
The final step, Sustain, is about creating a culture that embraces continuous improvement and adheres to the 5S principles.
Sustainability involves regular training, audits, and feedback loops to reinforce the practices.
Celebrate small successes and recognize employees who actively contribute to maintaining 5S.
Leadership plays a crucial role in sustaining 5S activities by setting a positive example and fostering a culture of accountability.
Encourage open communication and invite suggestions for improvement from all members of the team.
Sustainability is about embedding 5S into the organization’s culture, ensuring long-term success.
Benefits of Implementing 5S Practices
Embracing 5S activities offers numerous benefits for mid-level employees and the manufacturing operations department.
Improved organization leads to increased efficiency, reducing downtime and production costs.
A safe and clean working environment minimizes accidents and fosters employee well-being and motivation.
Standardized procedures enhance consistency and quality, meeting customer expectations more effectively.
Additionally, 5S practices improve employee satisfaction and engagement, leading to reduced turnover and higher productivity.
Overcoming Challenges in 5S Implementation
Despite its advantages, implementing 5S can pose challenges.
Resistance to change, lack of engagement, and inconsistent practices are common hurdles.
Address these challenges by clearly communicating the benefits of 5S to the team.
Involve employees in the planning and implementation process to gain their buy-in.
Provide regular training and support to help them understand the importance of each step.
Reinforce the significance of 5S through consistent leadership and ongoing communication.
Monitor progress through regular audits and feedback sessions to identify areas for improvement.
By addressing challenges proactively, the manufacturing department can achieve successful 5S implementation.
Conclusion
For mid-level employees in the manufacturing operations department, mastering 5S activities is essential for enhancing efficiency and productivity.
By implementing Sort, Set in Order, Shine, Standardize, and Sustain, you can achieve a well-organized and safe workplace.
The benefits of 5S are evident in improved operational efficiency, reduced wastage, and increased employee morale.
While challenges may arise, a commitment to clear communication, engagement, and leadership will pave the way for successful implementation.
By embracing 5S, the manufacturing operations department contributes to the organization’s overall success, setting the stage for continuous improvement and growth.
資料ダウンロード
QCD調達購買管理クラウド「newji」は、調達購買部門で必要なQCD管理全てを備えた、現場特化型兼クラウド型の今世紀最高の購買管理システムとなります。
ユーザー登録
調達購買業務の効率化だけでなく、システムを導入することで、コスト削減や製品・資材のステータス可視化のほか、属人化していた購買情報の共有化による内部不正防止や統制にも役立ちます。
NEWJI DX
製造業に特化したデジタルトランスフォーメーション(DX)の実現を目指す請負開発型のコンサルティングサービスです。AI、iPaaS、および先端の技術を駆使して、製造プロセスの効率化、業務効率化、チームワーク強化、コスト削減、品質向上を実現します。このサービスは、製造業の課題を深く理解し、それに対する最適なデジタルソリューションを提供することで、企業が持続的な成長とイノベーションを達成できるようサポートします。
オンライン講座
製造業、主に購買・調達部門にお勤めの方々に向けた情報を配信しております。
新任の方やベテランの方、管理職を対象とした幅広いコンテンツをご用意しております。
お問い合わせ
コストダウンが利益に直結する術だと理解していても、なかなか前に進めることができない状況。そんな時は、newjiのコストダウン自動化機能で大きく利益貢献しよう!
(Β版非公開)