- お役立ち記事
- For new employees in the chemical reactor gas seal manufacturing industry! Material selection to maintain high airtightness and chemical resistance
For new employees in the chemical reactor gas seal manufacturing industry! Material selection to maintain high airtightness and chemical resistance
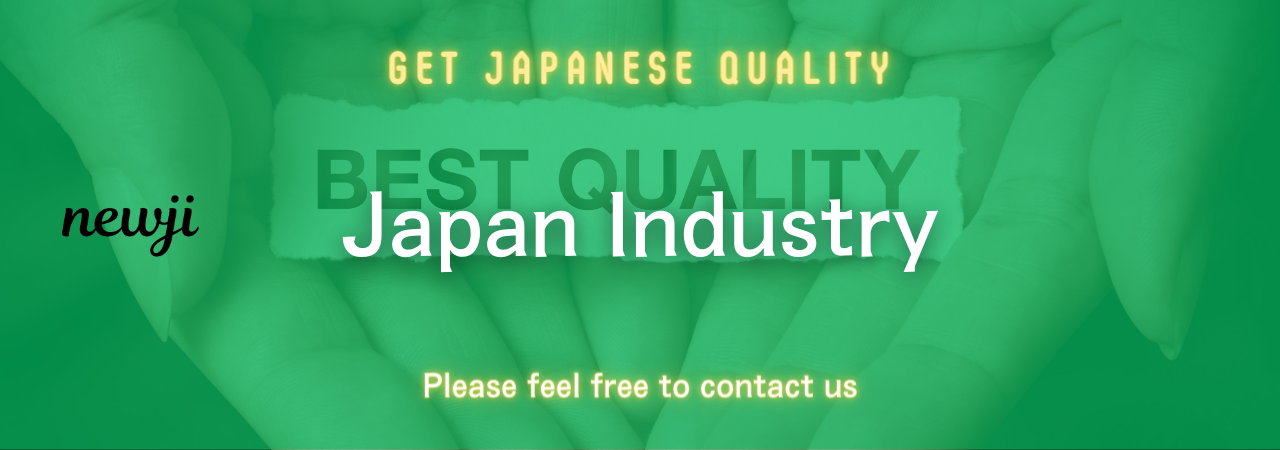
目次
Introduction to Material Selection for Gas Seals
Welcome to the intriguing world of chemical reactor gas seal manufacturing!
As a new employee in this industry, one of the most critical tasks you’ll tackle is choosing the right materials for gas seals.
The success of these seals hinges on their ability to maintain high airtightness and resist harsh chemical environments.
In this article, we’ll delve into the essential factors to consider when selecting materials for gas seals, ensuring they perform optimally and last longer.
Understanding Gas Seals
Before diving into material selection, let’s briefly understand what gas seals are and their role in chemical reactors.
Gas seals are critical components designed to prevent the leakage of gases from reactors, ensuring safety and efficiency in chemical processes.
They are typically used in pumps, compressors, and other rotating equipment, making them integral to maintaining the integrity of chemical systems.
Importance of Airtightness and Chemical Resistance
In a chemical reactor, airtightness is paramount to preventing hazardous gas leaks that can lead to safety hazards and production losses.
Simultaneously, chemical resistance ensures that the material can withstand the corrosive nature of the substances it encounters during its lifespan.
Both these attributes are crucial for gas seals, influencing the choice of material significantly.
Choosing Materials with High Airtightness
Selecting materials that provide high airtightness involves understanding the molecular structure and physical properties of potential candidates.
The fewer the imperfections in a material’s structure, the better it will perform.
Materials known for their airtight properties include:
– Elastomers: Known for their flexibility and tight sealing capabilities, elastomers like Viton and Nitrile are popular choices for gas seals.
They can accommodate slight movements and maintain airtightness under varying pressures.
– Polytetrafluoroethylene (PTFE): Often used for its low friction and excellent sealability, PTFE is ideal for applications requiring a non-reactive surface.
– Graphite: This material is prevalent in high-temperature applications due to its robust sealing properties and stability under extreme conditions.
Materials Known for Chemical Resistance
Chemical resistance is equally important, especially in environments where seals are exposed to aggressive substances.
The following materials are recognized for their excellent chemical resistance:
– Fluoroelastomers (FKM): FKM materials, such as Viton, provide outstanding resistance to a wide range of chemicals, making them suitable for harsh industrial applications.
– Perfluoroelastomers (FFKM): These materials can withstand the most corrosive environments and high temperatures, providing superior chemical resistance and thermal stability.
– Metals: Certain metals, like stainless steel and Hastelloy, offer excellent chemical resistance and structural integrity, often used in applications where elastomers may not suffice.
Factors Influencing Material Selection
When choosing materials for gas seals, several factors must be considered to ensure the best performance:
Operating Conditions
Understanding the specific operating conditions is crucial.
This includes temperature, pressure, and the types of chemicals encountered in the process.
Materials should be selected based on their ability to perform reliably under these conditions.
Compatibility with Process Fluids
Compatibility with the fluids in the system is essential to avoid degradation and ensure longevity.
Consider the chemical composition of both the process fluids and potential seal materials.
Temperature Resilience
Temperature fluctuations can significantly impact the performance of gas seals.
Materials must maintain their integrity and sealing ability across the expected temperature range.
Durability and Wear Resistance
In environments where gas seals face constant movement or abrasion, durability, and wear resistance are critical factors.
Materials should be robust enough to withstand physical stresses without compromising performance.
Balancing Cost and Performance
While it’s tempting to opt for the most advanced material, balancing cost and performance is crucial.
High-performance materials often come at a higher cost.
An effective strategy involves assessing the long-term benefits of investing in more expensive materials versus the potential maintenance and replacement costs of cheaper alternatives.
Testing Your Material Choice
Before finalizing your material choice, rigorous testing must be conducted to ensure the selected material meets the necessary performance standards.
This includes testing for sealability, chemical resistance, and endurance under simulated operating conditions.
Collaborating with experienced engineers or material scientists can provide valuable insights during this phase.
Staying Abreast with Industry Innovations
The chemical reactor gas seal manufacturing industry continually evolves, with new materials and technologies emerging.
Staying informed about these advancements can offer opportunities for improving seal performance and efficiency.
Participation in industry seminars, workshops, and joining professional networks can aid in keeping up with the latest trends.
Conclusion
As a new employee entering the chemical reactor gas seal manufacturing industry, understanding material selection is fundamental.
Prioritizing airtightness and chemical resistance will ensure the reliability and safety of the systems you work with.
By carefully assessing the factors affecting material choice and balancing cost against performance, you can contribute significantly to the success of your organization and the broader field.
Whether choosing elastomers, metals, or advanced polymers, informed decisions will enable you to excel in this critical aspect of reactor design and maintenance.
Welcome to a dynamic and essential industry where your contributions matter!
資料ダウンロード
QCD調達購買管理クラウド「newji」は、調達購買部門で必要なQCD管理全てを備えた、現場特化型兼クラウド型の今世紀最高の購買管理システムとなります。
ユーザー登録
調達購買業務の効率化だけでなく、システムを導入することで、コスト削減や製品・資材のステータス可視化のほか、属人化していた購買情報の共有化による内部不正防止や統制にも役立ちます。
NEWJI DX
製造業に特化したデジタルトランスフォーメーション(DX)の実現を目指す請負開発型のコンサルティングサービスです。AI、iPaaS、および先端の技術を駆使して、製造プロセスの効率化、業務効率化、チームワーク強化、コスト削減、品質向上を実現します。このサービスは、製造業の課題を深く理解し、それに対する最適なデジタルソリューションを提供することで、企業が持続的な成長とイノベーションを達成できるようサポートします。
オンライン講座
製造業、主に購買・調達部門にお勤めの方々に向けた情報を配信しております。
新任の方やベテランの方、管理職を対象とした幅広いコンテンツをご用意しております。
お問い合わせ
コストダウンが利益に直結する術だと理解していても、なかなか前に進めることができない状況。そんな時は、newjiのコストダウン自動化機能で大きく利益貢献しよう!
(Β版非公開)