- お役立ち記事
- For new employees in the design department of the aircraft parts manufacturing industry! Design strategy for lightweight parts using additive manufacturing (AM)
For new employees in the design department of the aircraft parts manufacturing industry! Design strategy for lightweight parts using additive manufacturing (AM)
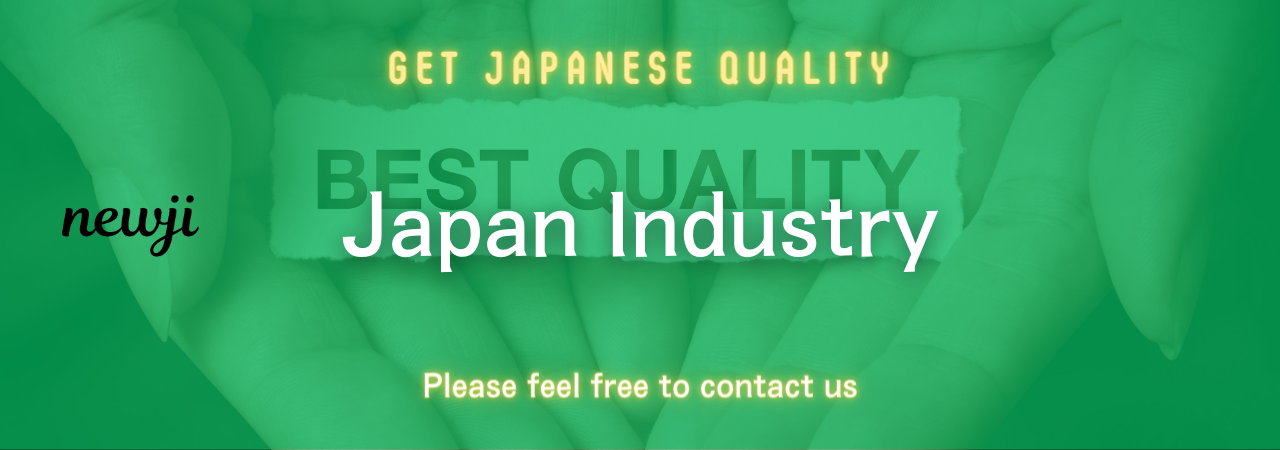
目次
Understanding Additive Manufacturing (AM)
As a new employee in the design department of the aircraft parts manufacturing industry, it is essential to familiarize yourself with the concept of Additive Manufacturing (AM).
AM, commonly known as 3D printing, is a process of creating three-dimensional objects from a digital file.
This innovative technique allows for the construction of complex geometries that are difficult or impossible to achieve with traditional manufacturing methods.
AM works by adding material layer by layer until the final product is achieved.
This process differs from subtractive manufacturing, where materials are removed to shape a part.
The ability to add material only where it is needed makes AM an excellent choice for producing lightweight and efficient aerospace components.
The Importance of Lightweight Design
Lightweight design is a crucial aspect of the aerospace industry.
Reducing the weight of aircraft parts can lead to significant benefits, including improved fuel efficiency, reduced emissions, and enhanced performance.
Every gram saved contributes to lowering the overall weight of the aircraft, leading to substantial economic and environmental advantages.
Manufacturers in the aerospace sector continually strive to create lighter and stronger parts without compromising on safety and durability.
As a new designer, understanding the relationship between weight, strength, and material usage will enable you to innovate and develop compelling solutions using AM.
Materials Used in Additive Manufacturing
When designing lightweight parts using AM, the choice of material is critical.
Several materials are available, each offering distinct properties that can enhance the functionality and performance of aerospace components.
– **Metals**: Titanium and aluminum alloys are commonly used in AM due to their high strength-to-weight ratios and resistance to corrosion.
They are ideal for load-bearing structures where lightweight properties are crucial.
– **Polymers**: High-performance polymers such as PEEK (Polyether Ether Ketone) and Ultem are favored for their lightness and ability to withstand high temperatures.
These materials are often used in non-structural components that require precision and flexibility.
– **Composites**: Combining different materials to form composites can offer unique advantages in terms of strength and weight.
Carbon-fiber-reinforced composites are particularly popular in the aerospace industry due to their exceptional strength and lightweight characteristics.
Design Strategies for Lightweight Parts
Transitioning to AM requires adopting new design strategies that leverage the unique capabilities of this technology.
Here are key strategies to consider in your design process:
Utilize Organic Shapes
One of the primary advantages of AM is the ability to create complex and organic shapes that were previously unattainable.
By embracing designs inspired by nature, you can reduce material usage and enhance structural efficiency.
Organic shapes can distribute stress more evenly and reduce the need for excess material, resulting in lighter and more robust components.
Implement Lattice Structures
Lattice structures are an effective way to minimize weight while maintaining strength.
These structures consist of a network of interconnected lines that form a mesh-like surface.
By varying the density and orientation of the lattice, you can tailor the mechanical properties to specific requirements.
AM allows for precise control over lattice geometry, enabling you to create highly optimized lightweight designs.
Optimize Material Distribution
Topology optimization is a mathematical approach that adjusts material distribution within a part to achieve maximum performance with minimal weight.
By using software tools that simulate different loading conditions, you can determine the optimal distribution of material to satisfy design criteria.
This process can significantly reduce weight and contribute to a more efficient design.
Incorporate Functional Integration
With AM, you can integrate multiple functions into a single component, reducing the need for additional parts and fasteners.
For example, you can design a part that combines structural support with thermal management features, enhancing overall efficiency.
Functional integration not only reduces weight but also simplifies assembly and maintenance processes.
The Role of Simulation and Testing
In the aerospace industry, safety and reliability are paramount.
Designing lightweight parts with AM requires rigorous simulation and testing to ensure they meet stringent performance standards.
Finite Element Analysis (FEA)
Finite Element Analysis (FEA) is a computational technique used to simulate how parts respond to various physical effects such as stress, heat, and vibration.
By creating a detailed model of your design, FEA allows you to predict how the component will perform under real-world conditions.
This helps identify potential weaknesses and optimize the design for strength and efficiency.
Prototyping and Testing
After initial simulations, prototyping is critical for verifying design assumptions and validating performance.
AM allows for rapid prototyping, enabling you to create physical models quickly and cost-effectively.
These prototypes can be tested in realistic scenarios, providing valuable insights into real-world performance and areas for improvement.
Collaboration and Continuous Learning
Finally, success in designing lightweight parts using AM requires collaboration and a commitment to continuous learning.
Engage with colleagues from different departments, such as materials science and manufacturing engineering, to better understand how your design choices impact the overall production process.
Stay informed about the latest advancements in AM and aerospace design by attending conferences, participating in workshops, and joining professional networks.
As you continue to learn and adapt, you will be better equipped to contribute to developing innovative solutions that shape the future of the aerospace industry.
資料ダウンロード
QCD調達購買管理クラウド「newji」は、調達購買部門で必要なQCD管理全てを備えた、現場特化型兼クラウド型の今世紀最高の購買管理システムとなります。
ユーザー登録
調達購買業務の効率化だけでなく、システムを導入することで、コスト削減や製品・資材のステータス可視化のほか、属人化していた購買情報の共有化による内部不正防止や統制にも役立ちます。
NEWJI DX
製造業に特化したデジタルトランスフォーメーション(DX)の実現を目指す請負開発型のコンサルティングサービスです。AI、iPaaS、および先端の技術を駆使して、製造プロセスの効率化、業務効率化、チームワーク強化、コスト削減、品質向上を実現します。このサービスは、製造業の課題を深く理解し、それに対する最適なデジタルソリューションを提供することで、企業が持続的な成長とイノベーションを達成できるようサポートします。
オンライン講座
製造業、主に購買・調達部門にお勤めの方々に向けた情報を配信しております。
新任の方やベテランの方、管理職を対象とした幅広いコンテンツをご用意しております。
お問い合わせ
コストダウンが利益に直結する術だと理解していても、なかなか前に進めることができない状況。そんな時は、newjiのコストダウン自動化機能で大きく利益貢献しよう!
(Β版非公開)