- お役立ち記事
- For new employees in the design department of the auto parts manufacturing industry! Part strength analysis using finite element method (FEM)
月間76,176名の
製造業ご担当者様が閲覧しています*
*2025年3月31日現在のGoogle Analyticsのデータより
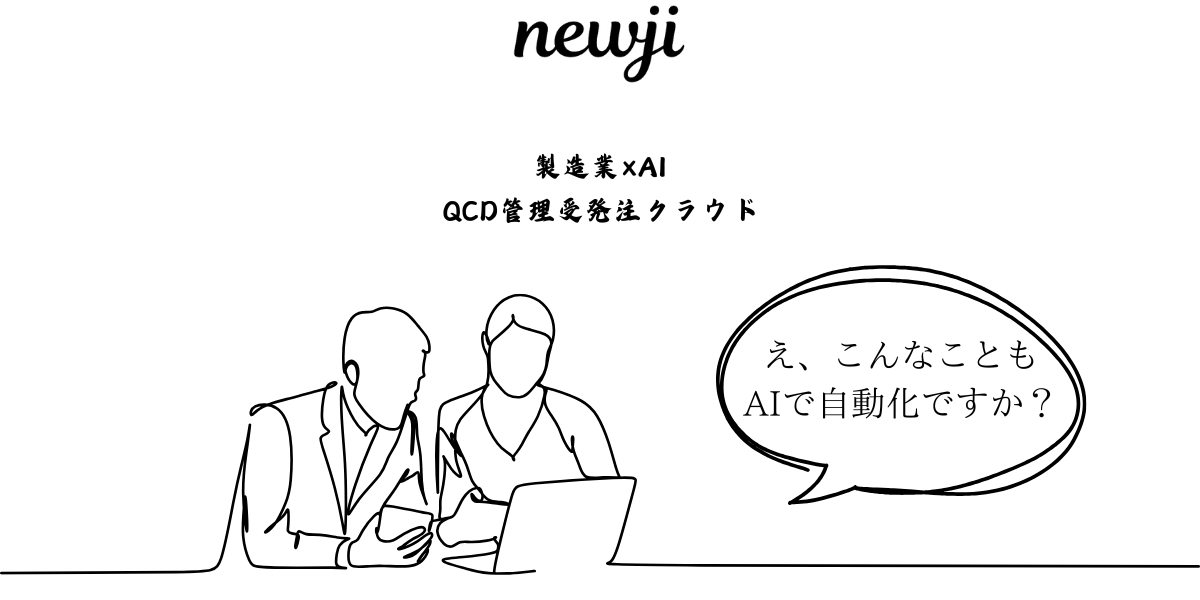
For new employees in the design department of the auto parts manufacturing industry! Part strength analysis using finite element method (FEM)
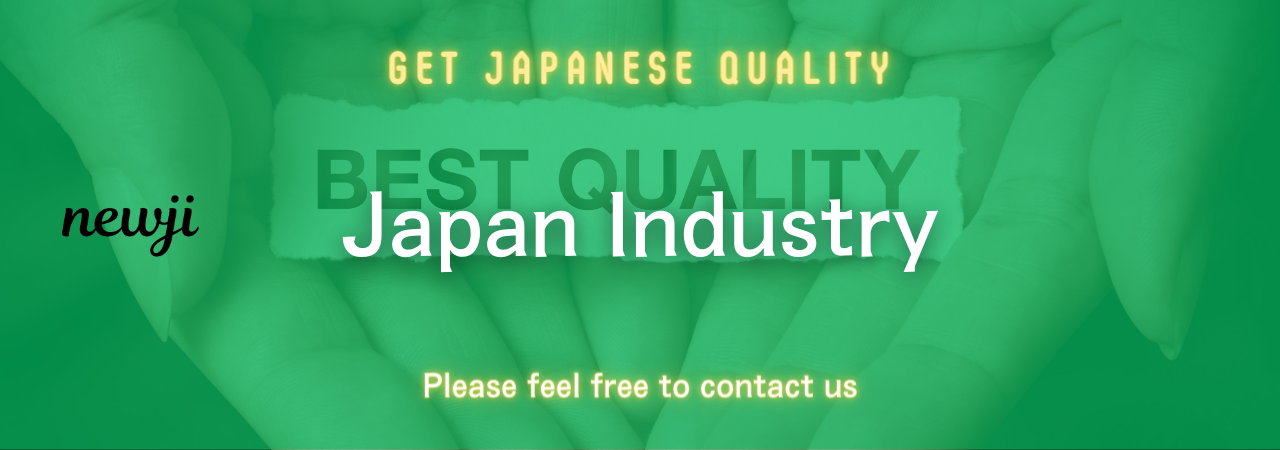
目次
Introduction to Finite Element Method (FEM)
The Finite Element Method, commonly known as FEM, is a powerful numerical tool used for solving complex engineering problems.
It’s particularly helpful in analyzing and predicting the structural behavior of materials and components.
In the context of the auto parts manufacturing industry, FEM is widely used to assess the strength and durability of different parts.
New employees in the design department might wonder why FEM is crucial.
Well, it’s essential because it allows engineers to ensure that every part manufactured meets safety and performance standards.
FEM enables precise calculations of stresses, deformations, and other mechanical properties, helping prevent failure in real-world applications.
Understanding Part Strength Analysis
Part strength analysis is a critical process in design engineering.
It helps in determining whether a component can withstand the loads, stresses, and environmental conditions it will face during its service life.
In the automotive industry, part strength analysis ensures that each component is robust enough to handle the demands of a vehicle’s operation.
When applied using FEM, part strength analysis becomes even more effective, providing accurate and detailed insights.
FEM divides a complex component into smaller, manageable parts called elements.
Each element is analyzed separately to understand how they contribute to the overall strength of the component.
Steps in FEM Analysis
1. Preprocessing
The first step in FEM analysis is preprocessing.
This involves preparing the model for analysis by defining the geometry of the component, selecting the material properties, and applying boundary conditions.
The geometry is broken down into elements and nodes, forming a mesh that simplifies the calculations.
2. Solving
Once the model is prepared, the solving phase begins.
This involves applying the specified loads and constraints to the model.
The FEM software calculates the responses of each element, determining factors like stress, strain, and displacement.
3. Postprocessing
The final step is postprocessing, where the results are interpreted and visualized.
Engineers analyze the data to check for areas with high stress or potential failure points.
This helps in making informed decisions regarding design modifications or improvements.
Benefits of FEM in the Automotive Industry
FEM brings numerous benefits to the automotive industry, making it an indispensable tool for design engineers.
Accurate and Reliable Results
FEM provides precise and accurate results that are essential for ensuring the safety and performance of automotive parts.
It enables engineers to predict how parts will behave under different conditions, reducing the risk of unexpected failures.
Cost and Time Efficiency
By using FEM, engineers can test multiple design iterations without the need for costly and time-consuming physical prototypes.
This speeds up the development process, allowing for quicker time-to-market.
Optimization of Materials
FEM helps in optimizing material usage by identifying areas where materials can be reduced without compromising strength.
This not only reduces costs but also enhances the sustainability of the manufacturing process.
Challenges and Considerations
While FEM is a powerful tool, it does come with its own set of challenges and considerations.
Complexity of Models
Creating accurate FEM models can be complex and time-consuming.
Engineers need to ensure that the mesh is fine enough to capture all critical behaviors without being too dense, which can lead to excessive computation times.
Interpretation of Results
The accuracy of FEM analysis also depends on the engineer’s ability to interpret the results correctly.
Overlooking important data or misinterpreting findings can lead to incorrect conclusions and potential design flaws.
Software Proficiency
Proficiency in FEM software is essential for effective analysis.
Ensuring that new employees receive adequate training on the specific tools and software used in the department is crucial for their success.
Conclusion
For new employees in the design department of the auto parts manufacturing industry, understanding part strength analysis using the Finite Element Method is vital.
FEM provides a comprehensive approach to assessing and enhancing the durability of automotive components.
By following the steps of preprocessing, solving, and postprocessing, engineers can ensure the reliability and safety of the parts they design.
Despite its challenges, the benefits of FEM in terms of accuracy, efficiency, and material optimization make it an invaluable tool in the realm of automotive design.
Proper training and proficiency in FEM techniques will empower new engineers to contribute significantly to innovative and functional automotive solutions.
資料ダウンロード
QCD管理受発注クラウド「newji」は、受発注部門で必要なQCD管理全てを備えた、現場特化型兼クラウド型の今世紀最高の受発注管理システムとなります。
ユーザー登録
受発注業務の効率化だけでなく、システムを導入することで、コスト削減や製品・資材のステータス可視化のほか、属人化していた受発注情報の共有化による内部不正防止や統制にも役立ちます。
NEWJI DX
製造業に特化したデジタルトランスフォーメーション(DX)の実現を目指す請負開発型のコンサルティングサービスです。AI、iPaaS、および先端の技術を駆使して、製造プロセスの効率化、業務効率化、チームワーク強化、コスト削減、品質向上を実現します。このサービスは、製造業の課題を深く理解し、それに対する最適なデジタルソリューションを提供することで、企業が持続的な成長とイノベーションを達成できるようサポートします。
製造業ニュース解説
製造業、主に購買・調達部門にお勤めの方々に向けた情報を配信しております。
新任の方やベテランの方、管理職を対象とした幅広いコンテンツをご用意しております。
お問い合わせ
コストダウンが利益に直結する術だと理解していても、なかなか前に進めることができない状況。そんな時は、newjiのコストダウン自動化機能で大きく利益貢献しよう!
(β版非公開)