- お役立ち記事
- For new employees in the design department of the auto parts manufacturing industry! Part strength analysis using finite element method (FEM)
For new employees in the design department of the auto parts manufacturing industry! Part strength analysis using finite element method (FEM)
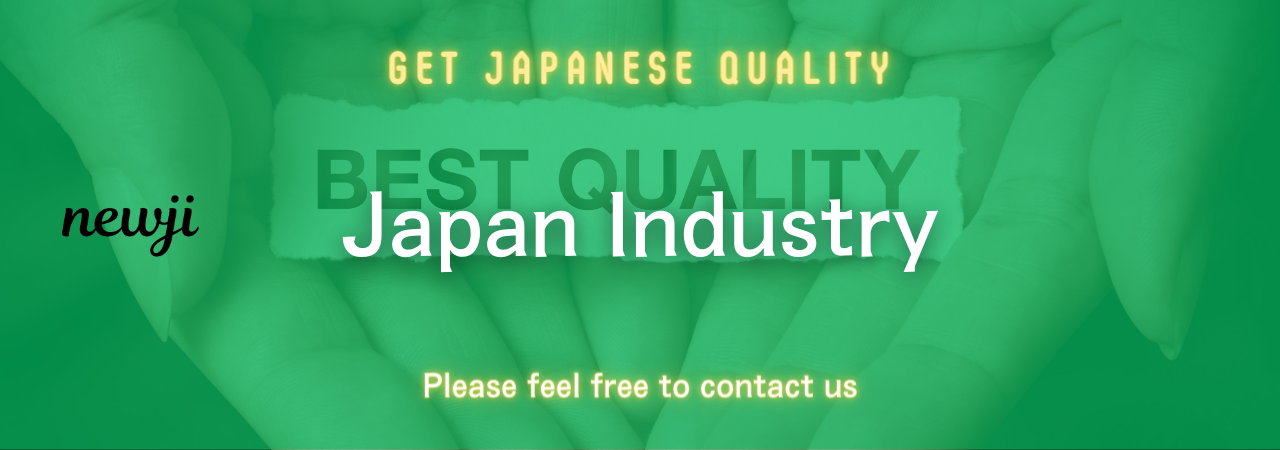
目次
Understanding Part Strength Analysis
When you join the design department of the auto parts manufacturing industry, one of the key tasks you’ll encounter is part strength analysis.
This is a crucial process that ensures the components you’re developing can withstand the demands of their environment without failure.
The technique most commonly used in this analysis is the Finite Element Method, often abbreviated as FEM.
But what exactly does FEM involve, and why is it so important in our industry?
The purpose of FEM is to predict how parts will react under various physical forces.
By using this method, designers can simulate real-world conditions and identify potential weaknesses in a part before it goes into production.
This is incredibly beneficial for ensuring safety, reliability, and cost-effectiveness.
What is the Finite Element Method?
The Finite Element Method is a powerful computational technique used to approximate solutions to complex structural, fluid, and thermal problems.
In the context of auto parts, it allows engineers to simulate how each component will behave under stress, strain, and thermal conditions.
To put it simply, FEM breaks down a physical object into a finite number of small elements, such as triangles or squares.
These elements are connected at points, or nodes, to form a mesh.
By applying known equations of motion and physical laws to this mesh, engineers can predict how the object will react to various forces.
The Importance of FEM in Auto Parts Manufacturing
In auto parts manufacturing, the strength and durability of parts are non-negotiable.
Vehicles must be reliable and safe, and any failure in parts could lead to serious consequences.
FEM helps ensure that components are robust enough to handle stressors such as weight, speed, temperature changes, and vibrations over time.
Using FEM, engineers can optimize materials and designs before production begins.
This means potential issues can be identified and resolved early in the process, saving both time and money.
It also allows for more innovative designs, as engineers can experiment with different materials and shapes in the virtual space.
Steps in Part Strength Analysis Using FEM
The process of performing a strength analysis using FEM involves several critical steps:
1. Defining the Problem
The first step is to define the problem you are trying to solve.
This involves understanding the requirements the part must meet and the conditions it will face.
You will need to gather all necessary information, such as material properties, geometrical data, and the types of loads your component will encounter.
2. Developing the Model
Once the problem is defined, you begin creating a detailed model of the part.
This model is but a simplification of the real component.
In this phase, the geometry is divided into finite elements, and a mesh is developed.
3. Applying Loads and Boundary Conditions
Next, specify the loads and boundary conditions the part will experience.
Loads can include forces, pressure, or thermal effects, while boundary conditions define how the part is supported or connected to other components.
4. Solving the Equations
With the model, loads, and conditions defined, the next step is to use software to solve the equations that describe the behavior of each element.
The solution will provide estimates for various performance metrics, like stress distribution and deformation.
5. Interpreting Results
Finally, analyze and interpret the results.
Examine for any areas of high stress or potential failure.
If weakness or inefficiency is found, adjustments can be made to the design and the analysis process can be repeated to find the optimal design.
Benefits of Using FEM for New Employees
For new employees in the design department, utilizing FEM offers substantial benefits:
Hands-On Learning
By applying FEM, you immerse yourself in the practical aspects of design, learning how theoretical knowledge applies to real-world applications.
Innovation and Creativity
FEM provides a sandbox where you can experiment with different materials and designs without the cost of creating physical prototypes.
Problem-Solving Skills
Regularly using FEM enhances your problem-solving skills.
You will develop a deeper understanding of material behavior and design, which is essential for creating effective and efficient auto parts.
Conclusion
In conclusion, part strength analysis using the Finite Element Method is an integral part of the automotive design process.
As a new employee in the design department, mastering this technique will empower you to contribute significantly to your team’s success.
You’ll ensure that the parts you help design are safe, reliable, and efficient, paving the way for an exciting career in auto parts manufacturing.
資料ダウンロード
QCD調達購買管理クラウド「newji」は、調達購買部門で必要なQCD管理全てを備えた、現場特化型兼クラウド型の今世紀最高の購買管理システムとなります。
ユーザー登録
調達購買業務の効率化だけでなく、システムを導入することで、コスト削減や製品・資材のステータス可視化のほか、属人化していた購買情報の共有化による内部不正防止や統制にも役立ちます。
NEWJI DX
製造業に特化したデジタルトランスフォーメーション(DX)の実現を目指す請負開発型のコンサルティングサービスです。AI、iPaaS、および先端の技術を駆使して、製造プロセスの効率化、業務効率化、チームワーク強化、コスト削減、品質向上を実現します。このサービスは、製造業の課題を深く理解し、それに対する最適なデジタルソリューションを提供することで、企業が持続的な成長とイノベーションを達成できるようサポートします。
オンライン講座
製造業、主に購買・調達部門にお勤めの方々に向けた情報を配信しております。
新任の方やベテランの方、管理職を対象とした幅広いコンテンツをご用意しております。
お問い合わせ
コストダウンが利益に直結する術だと理解していても、なかなか前に進めることができない状況。そんな時は、newjiのコストダウン自動化機能で大きく利益貢献しよう!
(Β版非公開)