- お役立ち記事
- For new employees in the environmental technology department! How to implement clean room technology to improve product quality
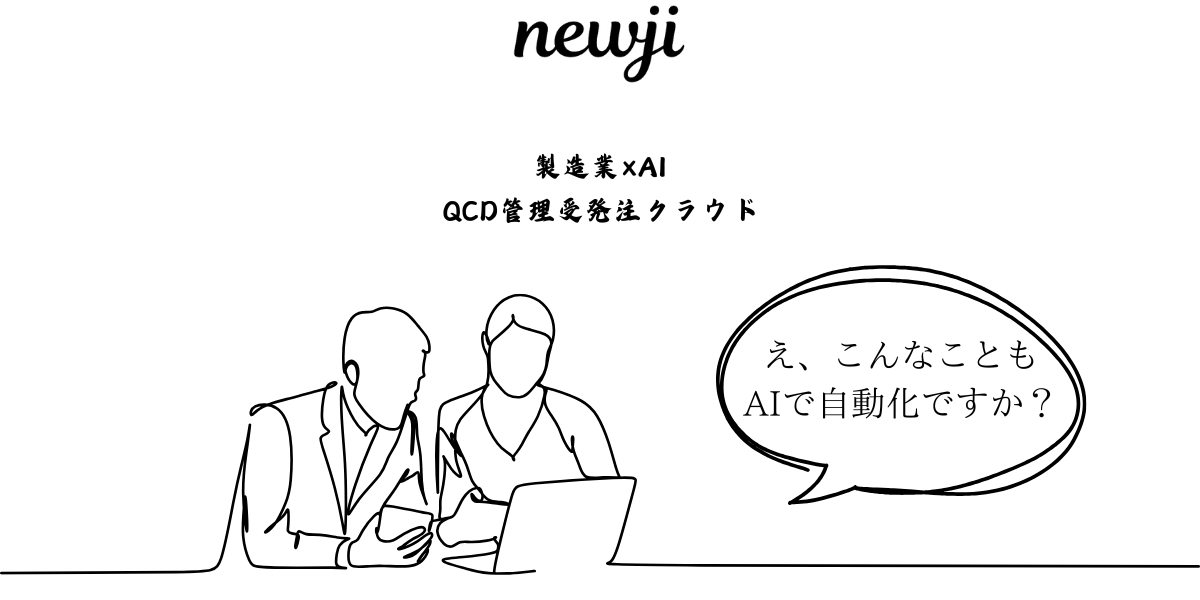
For new employees in the environmental technology department! How to implement clean room technology to improve product quality
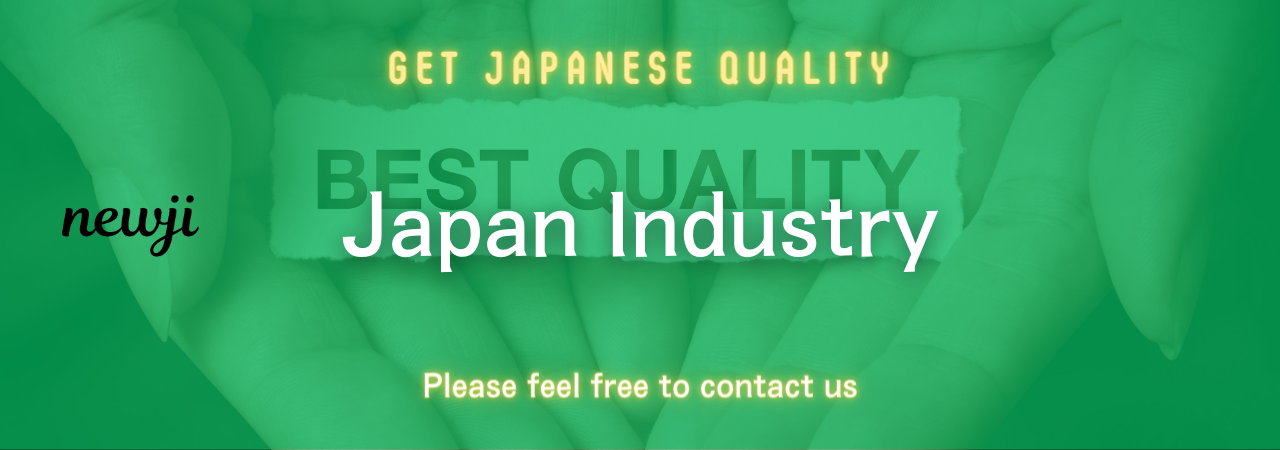
目次
Introduction to Clean Room Technology
Clean room technology is an essential aspect of the environmental technology industry, particularly when it comes to improving product quality.
For new employees in the environmental technology department, understanding how to implement this technology effectively can lead to significant advancements in your work and the products you help create.
Clean rooms are controlled environments with low levels of pollutants such as dust, airborne microbes, aerosol particles, and chemical vapors.
This technology is crucial in industries like pharmaceuticals, electronics, and biotechnology, where even the smallest contamination can compromise product quality and safety.
The Importance of Clean Rooms
In the world of environmental technology, maintaining high product quality is paramount.
Clean rooms ensure that products are manufactured in an environment that minimizes the risk of contamination.
These controlled spaces help prevent defects and maintain the integrity of the manufacturing process.
The use of clean room technology allows companies to adhere to stricter regulatory requirements and meet high consumer expectations.
It also enhances the company’s reputation by demonstrating a commitment to quality and safety.
As a new employee, understanding the role of clean rooms can position you as a valuable asset to your team and organization.
Key Components of Clean Room Technology
Air Filtration Systems
Air filtration systems are at the heart of clean room technology.
These systems control airborne particles by circulating air through high-efficiency particulate air (HEPA) or ultra-low penetration air (ULPA) filters.
This filtration process removes contaminants and ensures the air remains clean.
Temperature and Humidity Control
Maintaining the right temperature and humidity levels is critical in a clean room environment.
These factors can affect static electricity, which may impact sensitive equipment and products.
Clean rooms are equipped with advanced HVAC systems to maintain optimal conditions, ensuring the environment remains conducive to high-quality production.
Personnel and Equipment Protocols
The behavior of personnel and the sterilization of equipment also play crucial roles in maintaining clean room standards.
Personnel must wear appropriate garments to minimize contamination.
Strict protocols ensure that equipment entering the clean room is thoroughly cleaned and sterilized, preventing any potential contamination from external sources.
Steps to Implement Clean Room Technology
Assessment and Design
Before implementing clean room technology, assess the specific needs of your projects and determine what level of cleanliness is required.
Design the clean room layout to accommodate your processes and ensure efficient workflow while maintaining cleanliness standards.
Installation of Equipment
Select and install the appropriate air filtration systems, HVAC controls, and necessary equipment.
Ensure all systems are integrated seamlessly and meet the required specifications.
Regular testing and calibration of equipment are essential for maintaining clean room standards.
Training and Protocol Development
Develop comprehensive training programs for employees to understand clean room protocols.
These should include proper gowning procedures, equipment handling, and cleaning methods to maintain a contaminant-free environment.
Procedures must be clear and strictly adhered to by all personnel working within the clean room.
Monitoring and Maintenance
Once the clean room is operational, continuous monitoring and maintenance are crucial.
This involves regular testing of air quality and environmental conditions to ensure systems function optimally.
Regular maintenance of equipment and facilities is necessary to prevent contamination risks.
Establish a schedule for cleaning and re-certifying the clean room to uphold the highest cleanliness standards.
Advantages of Clean Room Technology
By implementing clean room technology, you ensure higher product quality and consistency, leading to greater customer satisfaction.
This technology helps reduce the likelihood of product recalls or defects, saving costs and upholding the brand’s reputation.
Moreover, clean rooms facilitate innovation by providing a controlled environment for research and development processes.
This controlled setting allows for the experimental production of new products without the risk of contamination.
Challenges and Solutions
Initial Costs
Implementing clean room technology can be expensive due to the cost of equipment and installation.
However, the long-term benefits of improved product quality and reduced defects often outweigh the initial investment.
Ongoing Compliance
Staying compliant with regulatory standards requires continuous monitoring and updates.
Invest in automated systems that provide real-time data on environmental conditions, simplifying compliance efforts.
Personnel Management
Training and managing personnel to adhere to clean room protocols can be challenging.
Regular workshops and certifications ensure employees remain informed and compliant with the latest clean room practices.
Conclusion
For new employees in the environmental technology department, mastering clean room technology is a gateway to enhancing product quality and contributing to the industry’s advancement.
Understanding the key components, implementation steps, and benefits of clean room environments will help you succeed and become an integral part of your organization’s quality assurance efforts.
By prioritizing cleanliness and adhering to protocols, you can play a vital role in producing superior products and maintaining high industry standards.
資料ダウンロード
QCD調達購買管理クラウド「newji」は、調達購買部門で必要なQCD管理全てを備えた、現場特化型兼クラウド型の今世紀最高の購買管理システムとなります。
ユーザー登録
調達購買業務の効率化だけでなく、システムを導入することで、コスト削減や製品・資材のステータス可視化のほか、属人化していた購買情報の共有化による内部不正防止や統制にも役立ちます。
NEWJI DX
製造業に特化したデジタルトランスフォーメーション(DX)の実現を目指す請負開発型のコンサルティングサービスです。AI、iPaaS、および先端の技術を駆使して、製造プロセスの効率化、業務効率化、チームワーク強化、コスト削減、品質向上を実現します。このサービスは、製造業の課題を深く理解し、それに対する最適なデジタルソリューションを提供することで、企業が持続的な成長とイノベーションを達成できるようサポートします。
オンライン講座
製造業、主に購買・調達部門にお勤めの方々に向けた情報を配信しております。
新任の方やベテランの方、管理職を対象とした幅広いコンテンツをご用意しております。
お問い合わせ
コストダウンが利益に直結する術だと理解していても、なかなか前に進めることができない状況。そんな時は、newjiのコストダウン自動化機能で大きく利益貢献しよう!
(Β版非公開)