- お役立ち記事
- For new employees in the equipment management department of the pharmaceutical manufacturing industry! Basics of GMP-compliant equipment maintenance
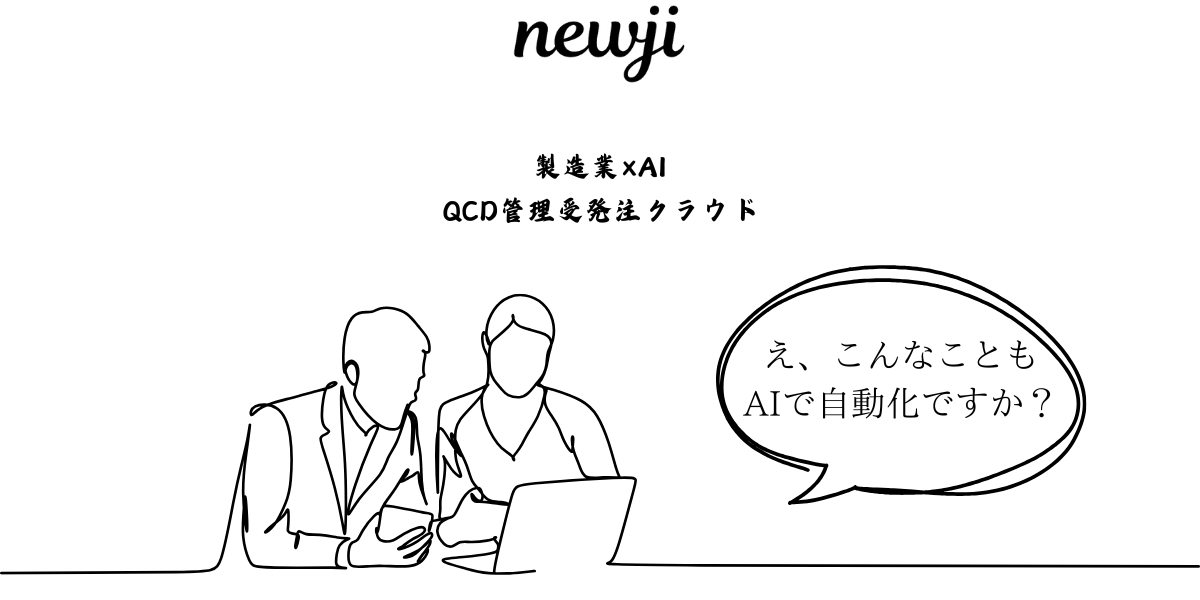
For new employees in the equipment management department of the pharmaceutical manufacturing industry! Basics of GMP-compliant equipment maintenance
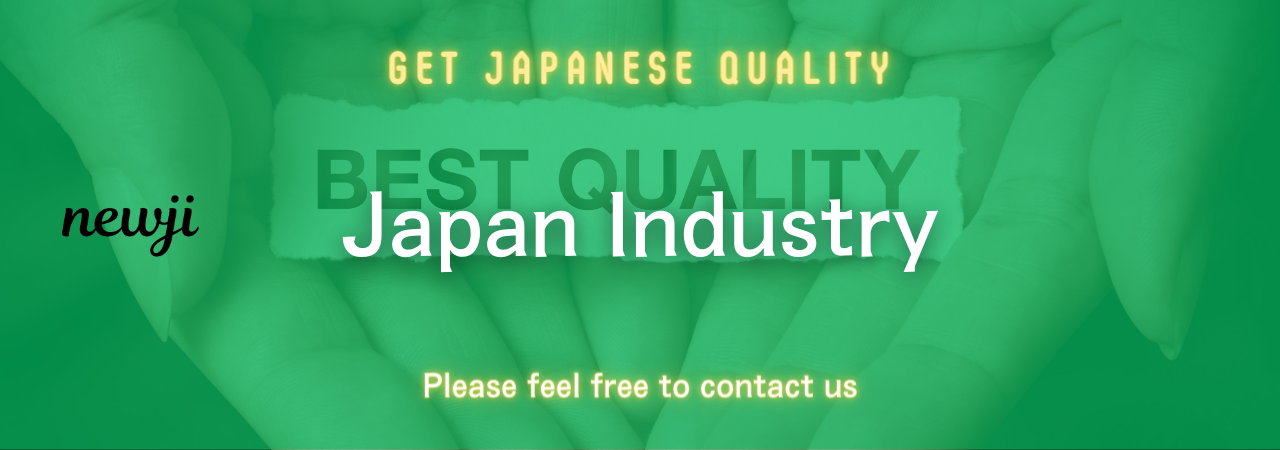
目次
Introduction to GMP
Welcome to the world of pharmaceutical manufacturing, particularly to the equipment management department!
As a new employee, you’ll quickly learn that maintaining equipment isn’t just about turning wrenches and oiling machines. It’s about ensuring safety, efficiency, and compliance with various regulations.
One of the most critical standards you’ll deal with is the Good Manufacturing Practice, or GMP.
GMP is a system designed to ensure that products are consistently produced and controlled according to quality standards.
It is crucial in the pharmaceutical industry to minimize the risks involved in any production that cannot be eliminated through testing the final product.
What is GMP Compliance?
GMP compliance involves adhering to guidelines that advise manufacturers on the quality and purity of their products.
These guidelines are set by regulatory agencies, such as the U.S. Food and Drug Administration (FDA) and other global entities.
The purpose is to safeguard consumers by ensuring products are safe and effective.
For those working in equipment management, compliance includes ensuring that all equipment is properly installed, maintained, and operated.
This helps prevent contamination, equipment failure, or other issues that could impact the quality of a pharmaceutical product.
According to GMP: What Does Maintenance Include?
Maintenance under GMP isn’t just about keeping machines running.
It includes a series of checks, inspections, and procedures aligned with legal guidelines to ensure everything runs smoothly.
The goal is to guarantee that any issues are identified quickly and rectified without disrupting production.
Key Principles of GMP for Equipment Maintenance
1. Documentation
Documentation is one of the pillars of GMP.
Everything related to equipment maintenance needs to be recorded, from regular checks to repairs and procedural changes.
This creates an audit trail, ensuring all processes can be reviewed for compliance reasons.
By maintaining meticulous records, you ensure transparency and accountability within the manufacturing process.
2. Standard Operating Procedures (SOPs)
SOPs are detailed, written instructions to achieve uniformity in the performance of specific functions.
They are essential for training new employees and providing a reference to ensure equipment is handled consistently and correctly.
Adhering to SOPs minimizes deviation, which could otherwise lead to non-compliance with GMP standards.
3. Calibration and Validation
Calibration ensures that equipment performs accurately within its specified parameters.
It’s critical that all measurement instruments are serviced regularly to maintain precision.
Validation, on the other hand, confirms that equipment performs its intended functions consistently.
Both processes require close attention to detail to ensure compliance with GMP requirements.
The Role of Preventive Maintenance
Preventive maintenance is a proactive approach that involves regular operations to prevent equipment breakdown before it occurs.
This includes scheduled inspections, servicing, and parts replacement to avoid unplanned downtime.
By following a preventative maintenance schedule, you ensure equipment runs at its optimum level, further complying with GMP standards.
1. Risk Assessment
Conducting risk assessments allows you to prioritize maintenance tasks based on the potential impact of equipment failure.
By understanding weak spots and possible points of failure, you can focus resources on the most critical equipment.
This targeted approach ensures that your efforts are always contributing to maintaining compliance.
2. Training and Communication
Effective maintenance also involves regular training sessions for staff.
Technicians and operators need to understand the importance of GMP compliance and how their roles contribute to achieving it.
Clear communication between departments ensures everyone is on the same page and can quickly address issues as they arise.
The Importance of Cleanliness and Hygiene
In the pharmaceutical industry, cleanliness and hygiene are pivotal.
Contaminants can easily compromise product quality, making cleanliness an integral part of GMP compliance.
Regular cleaning schedules and strict hygiene protocols need to be followed meticulously to prevent contamination risks.
1. Clean-in-Place (CIP) Procedures
CIP is used to clean the interior surfaces of pipes, vessels, process equipment, and associated fittings, without disassembly.
These systems are critical as they offer a methodical approach to hygiene that complies with GMP guidelines.
2. Personal Cleanliness
Personal hygiene of equipment handlers must also meet stringent standards.
Ensuring everyone understands and follows these rules is crucial to maintaining the integrity of both the equipment and the final product.
Challenges and Solutions in GMP Equipment Maintenance
Equipment management in pharmaceuticals is not without its challenges.
Equipment wears down, technology evolves, and standards may change.
Remaining compliant requires ongoing education and flexibility.
Being prepared to adapt and innovate in equipment practices is necessary to maintain GMP standards.
1. Keeping Up with Technological Advancements
New technologies present opportunities and challenges.
Keeping equipment up-to-date with technological advances can lead to more efficient and compliant processes.
However, integrating new technology requires training and updating SOPs.
2. Adapting to Regulatory Changes
Regulatory standards can change, and when they do, it can affect how equipment must be managed.
Staying informed of changes and updating practices accordingly is crucial to remain compliant.
Conclusion
Joining the equipment management department in the pharmaceutical industry provides a unique opportunity to ensure the highest standards of product quality and safety.
Understanding and implementing GMP guidelines in equipment maintenance is fundamental in achieving both compliance and operational success.
By focusing on proper documentation, preventive maintenance, and continuous education, you can contribute significantly to producing safe and effective pharmaceutical products.
Welcome aboard! Your role is vital to the overarching goal of delivering high standards of healthcare to the world.
資料ダウンロード
QCD調達購買管理クラウド「newji」は、調達購買部門で必要なQCD管理全てを備えた、現場特化型兼クラウド型の今世紀最高の購買管理システムとなります。
ユーザー登録
調達購買業務の効率化だけでなく、システムを導入することで、コスト削減や製品・資材のステータス可視化のほか、属人化していた購買情報の共有化による内部不正防止や統制にも役立ちます。
NEWJI DX
製造業に特化したデジタルトランスフォーメーション(DX)の実現を目指す請負開発型のコンサルティングサービスです。AI、iPaaS、および先端の技術を駆使して、製造プロセスの効率化、業務効率化、チームワーク強化、コスト削減、品質向上を実現します。このサービスは、製造業の課題を深く理解し、それに対する最適なデジタルソリューションを提供することで、企業が持続的な成長とイノベーションを達成できるようサポートします。
オンライン講座
製造業、主に購買・調達部門にお勤めの方々に向けた情報を配信しております。
新任の方やベテランの方、管理職を対象とした幅広いコンテンツをご用意しております。
お問い合わせ
コストダウンが利益に直結する術だと理解していても、なかなか前に進めることができない状況。そんな時は、newjiのコストダウン自動化機能で大きく利益貢献しよう!
(Β版非公開)