- お役立ち記事
- For new employees in the equipment management department of the steel industry! Fundamentals of wear diagnosis by lubricating oil analysis
月間76,176名の
製造業ご担当者様が閲覧しています*
*2025年3月31日現在のGoogle Analyticsのデータより
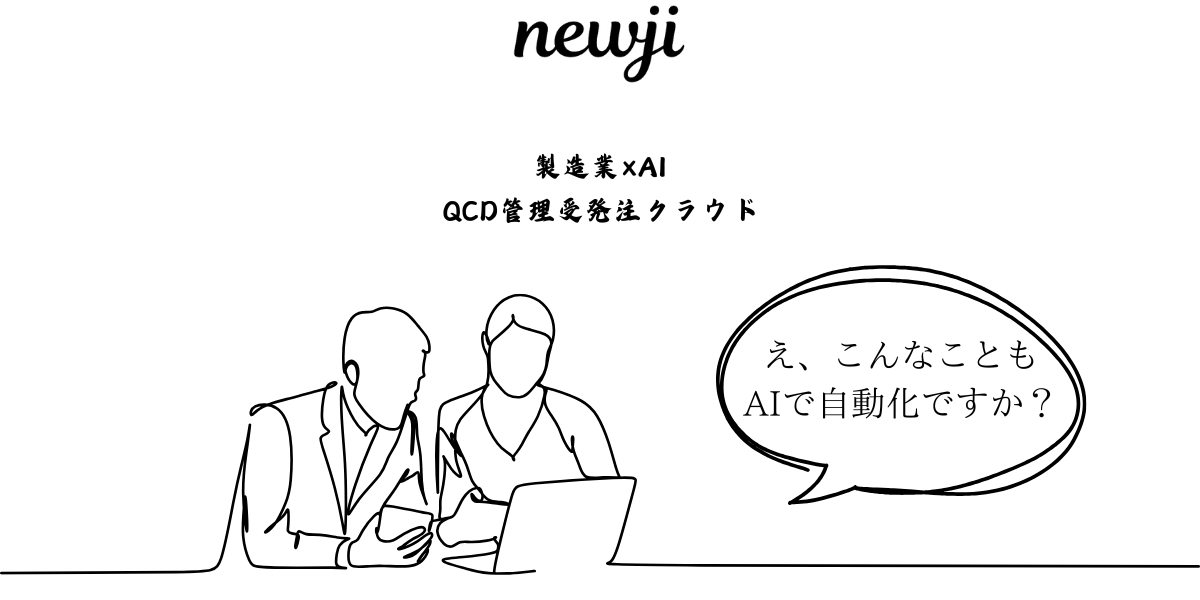
For new employees in the equipment management department of the steel industry! Fundamentals of wear diagnosis by lubricating oil analysis
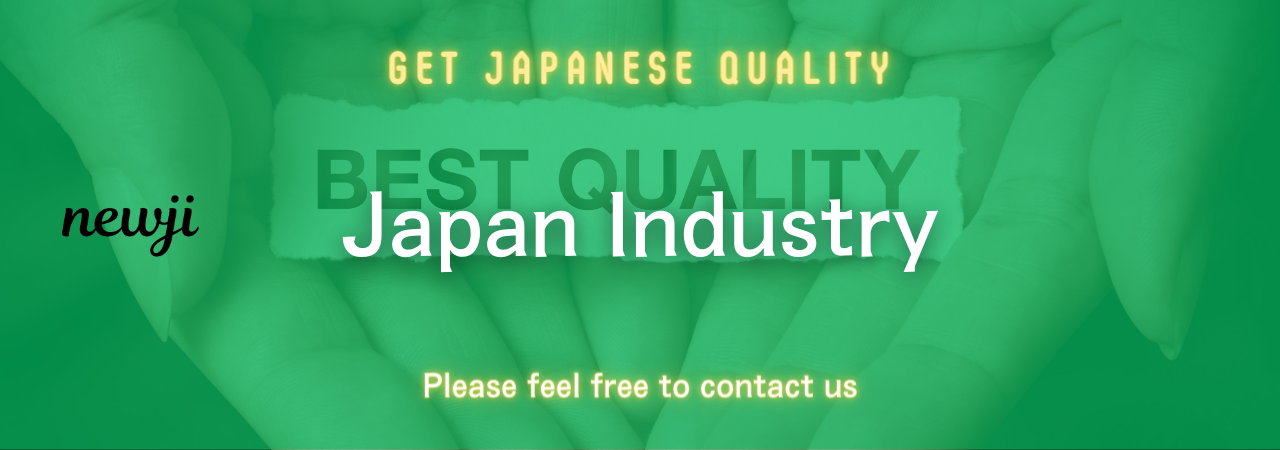
目次
Understanding Wear Diagnosis in Equipment Management
As a new employee in the equipment management department of the steel industry, understanding wear diagnosis is crucial for ensuring the longevity and efficiency of machinery.
One of the key methods in wear diagnosis is through lubricating oil analysis.
This technique not only helps in predicting potential failures but also in extending the life of the equipment.
Learning the basics of lubricating oil analysis will be an important part of your role in maintaining seamless operations.
What is Wear Diagnosis?
Wear diagnosis involves monitoring and managing the condition of machinery components to prevent unplanned downtime.
In the steel industry, where machinery operates under high pressure and temperature, regular wear diagnosis is essential to maintain operational efficiency.
By detecting wear at an early stage, interventions can be planned to avoid costly repairs or replacements.
Importance of Lubricating Oil Analysis
Lubricating oil plays a vital role in minimizing friction between moving parts of machinery.
However, over time, this oil can become contaminated or degraded, potentially leading to increased wear or damage to equipment.
Lubricating oil analysis helps identify the condition of the oil and the machinery it lubricates.
This analysis provides insights into the presence of contaminants, the level of oil degradation, and the wear particles within the equipment.
By regularly analyzing the oil, you can ensure the equipment operates smoothly and prevent early wear and tear.
Main Components of Oil Analysis
Oil analysis focuses on several key components:
1. **Viscosity:** This is the oil’s resistance to flow. It reflects how well the oil can create a film between moving parts. Changes in viscosity can indicate oil degradation or contamination.
2. **Contaminants:** These include dirt, water, or soot, which can enter the oil system. Contaminants can accelerate wear by creating additional friction or corrosion.
3. **Wear Metals:** The presence of metal particles in the oil can indicate wear on specific components such as bearings, gears, or pistons.
Procedures for Conducting Oil Analysis
To conduct an effective lubricating oil analysis, it’s important to follow a systematic approach:
1. **Sampling:** Collect a sample of the lubricating oil from the equipment following the proper procedures to avoid contamination.
2. **Testing:** Send the sample to a laboratory for testing. The tests typically include checking for viscosity, contamination, and wear metal presence.
3. **Evaluation:** Review the test results to evaluate the condition of the oil and machinery.
4. **Action Plan:** Based on the findings, decide whether the oil needs to be changed, the machinery requires maintenance, or further investigation is needed.
Common Analytical Techniques
Several analytical techniques are used for lubricating oil analysis, including:
– **Spectroscopy:** Identifies and measures wear metals and contaminants.
– **Fourier Transform Infrared Analysis (FTIR):** Monitors oil degradation and contamination levels.
– **Particle Count Testing:** Determines the number of wear particles in the oil to assess the extent of wear.
These techniques are essential in building a detailed understanding of the operational health of machinery.
Benefits of Regular Oil Analysis
Performing regular oil analysis brings numerous benefits to the equipment management process:
– **Extended Equipment Life:** By preventing excessive wear, machinery life is extended, reducing the need for replacements.
– **Cost Efficiency:** Early detection of potential issues helps in preventing costly repairs and lowering operational downtime.
– **Informed Decision-Making:** Data obtained from oil analysis allows for more informed decisions on maintenance schedules and oil change frequencies.
– **Environmental Stewardship:** By optimizing oil usage, there is a reduced environmental impact due to less waste production.
Implementing Effective Oil Analysis Programs
To be successful in your role, implementing an effective lubricating oil analysis program is key:
– **Regular Scheduling:** Establish and adhere to a regular schedule for oil sampling and analysis.
– **Training:** Stay informed with ongoing training and updates on the latest oil analysis technologies and techniques.
– **Documentation:** Keep thorough records of oil analysis results and maintenance activities for better tracking and decision-making.
– **Communication:** Ensure clear communication with team members and supervisors to align on maintenance strategies.
Conclusion
Understanding the fundamentals of wear diagnosis through lubricating oil analysis is essential for equipment management in the steel industry.
As a new employee, familiarizing yourself with these concepts will empower you to ensure that all machinery operates efficiently, minimizing both costs and downtime.
With regular analysis and a proactive approach, you will contribute significantly to the overall productivity of your organization.
資料ダウンロード
QCD管理受発注クラウド「newji」は、受発注部門で必要なQCD管理全てを備えた、現場特化型兼クラウド型の今世紀最高の受発注管理システムとなります。
ユーザー登録
受発注業務の効率化だけでなく、システムを導入することで、コスト削減や製品・資材のステータス可視化のほか、属人化していた受発注情報の共有化による内部不正防止や統制にも役立ちます。
NEWJI DX
製造業に特化したデジタルトランスフォーメーション(DX)の実現を目指す請負開発型のコンサルティングサービスです。AI、iPaaS、および先端の技術を駆使して、製造プロセスの効率化、業務効率化、チームワーク強化、コスト削減、品質向上を実現します。このサービスは、製造業の課題を深く理解し、それに対する最適なデジタルソリューションを提供することで、企業が持続的な成長とイノベーションを達成できるようサポートします。
製造業ニュース解説
製造業、主に購買・調達部門にお勤めの方々に向けた情報を配信しております。
新任の方やベテランの方、管理職を対象とした幅広いコンテンツをご用意しております。
お問い合わせ
コストダウンが利益に直結する術だと理解していても、なかなか前に進めることができない状況。そんな時は、newjiのコストダウン自動化機能で大きく利益貢献しよう!
(β版非公開)