- お役立ち記事
- For new employees in the equipment technology department of the auto parts manufacturing industry! Fundamentals of equipment maintenance using reliability engineering
For new employees in the equipment technology department of the auto parts manufacturing industry! Fundamentals of equipment maintenance using reliability engineering
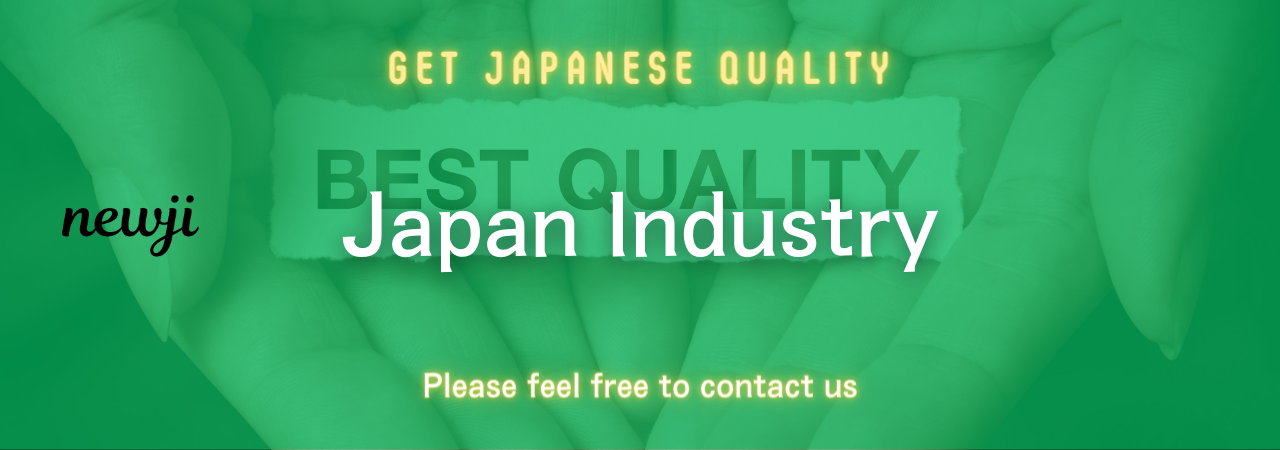
目次
Understanding Reliability Engineering
Reliability engineering is a critical field that aims to ensure equipment and systems perform their intended functions without failure over a specified period.
For new employees in the equipment technology department of the auto parts manufacturing industry, understanding the fundamentals of reliability engineering is essential.
It involves predicting, analyzing, and improving the dependability and performance of machinery and processes.
This knowledge will help you play a vital role in maintaining and enhancing the efficiency of production lines.
Reliability engineering focuses on three main aspects: predicting, measuring, and improving equipment performance.
By applying various statistical and probabilistic methods, reliability engineers can estimate the likelihood and impact of potential failures.
This proactive approach helps in identifying weak points in a system, allowing you to devise strategies to mitigate risks before they occur.
The Importance of Equipment Maintenance
In the auto parts manufacturing industry, equipment maintenance is crucial to ensure smooth operations and prevent costly downtime.
Regular maintenance can significantly extend the lifespan of machinery and reduce the risk of unexpected failures.
As a new employee in the equipment technology department, it is your responsibility to keep equipment functioning efficiently.
Reliability engineering principles can guide you in implementing effective maintenance strategies.
By focusing on preventive and predictive maintenance, you can minimize disruptions in the production process.
Preventive maintenance involves routine checks and servicing of equipment to avoid potential issues, while predictive maintenance uses data and analytics to predict when a machine might fail, allowing for timely intervention.
Key Concepts in Reliability Engineering
To effectively apply reliability engineering in your role, it’s important to grasp some key concepts related to equipment maintenance.
Mean Time Between Failures (MTBF)
MTBF is a reliability metric that measures the average time elapsed between failures of a system or component.
A higher MTBF indicates a more reliable piece of equipment.
By analyzing MTBF data, you can identify equipment that requires attention and prioritize maintenance efforts accordingly.
Failure Mode and Effects Analysis (FMEA)
FMEA is a systematic approach used to identify potential failure modes within a system and assess their impact on overall performance.
This tool helps you prioritize potential risks based on their severity and likelihood, enabling you to address critical issues first.
Implementing FMEA in your maintenance strategy can lead to a deeper understanding of equipment vulnerabilities and guide you in improving system reliability.
Root Cause Analysis (RCA)
When failures do occur, Root Cause Analysis is employed to determine the underlying reasons for a problem.
By understanding the root causes of failures, you can implement corrective measures to prevent future occurrences.
RCA involves gathering data, analyzing patterns, and making decisions to eliminate the root cause effectively.
Implementing Reliability Engineering Practices
Now that you understand the foundational concepts, let’s explore how you can implement reliability engineering practices in your day-to-day tasks.
Data Collection and Analysis
A strong reliability engineering program heavily relies on data collection and analysis.
Collect data on equipment performance, failure rates, and maintenance activities.
Use statistical methods and software tools to analyze this data and extract actionable insights.
Data-driven decision-making will enhance your ability to predict failures and optimize maintenance schedules.
Developing Maintenance Plans
Work with your team to develop comprehensive maintenance plans that incorporate reliability engineering principles.
Design a maintenance schedule that includes both routine checks and predictive maintenance activities.
Aim to balance production demands with maintenance needs to minimize downtime and maximize productivity.
Continuous Improvement
Reliability engineering promotes a culture of continuous improvement.
Regularly review and update maintenance practices based on new insights and data.
Encourage feedback from team members and stay informed about the latest industry trends and technological advancements.
By fostering a mindset of continuous improvement, you can contribute to the long-term success of your department.
The Benefits of Reliability Engineering
Adopting reliability engineering practices yields numerous benefits for both you and your organization in the auto parts manufacturing industry.
Increased Equipment Uptime: Predictive maintenance reduces the likelihood of unexpected breakdowns, ensuring production lines run smoothly.
Cost Savings: By addressing issues proactively, you minimize repair costs and extend the life of equipment, reducing capital expenditures.
Enhanced Safety: Reliable equipment reduces the risk of accidents, fostering a safer working environment for employees.
Improved Quality: Consistent equipment performance contributes to the production of high-quality auto parts that meet industry standards.
Conclusion
As a new employee in the equipment technology department, understanding and applying reliability engineering principles is essential for success.
By focusing on effective maintenance strategies, data analysis, and continuous improvement, you can ensure optimal equipment performance in the auto parts manufacturing industry.
This knowledge will help you play a pivotal role in enhancing productivity, reducing costs, and maintaining high-quality standards.
Embrace the fundamentals of reliability engineering, and you’ll be well-equipped to tackle the challenges and opportunities that lie ahead.
資料ダウンロード
QCD調達購買管理クラウド「newji」は、調達購買部門で必要なQCD管理全てを備えた、現場特化型兼クラウド型の今世紀最高の購買管理システムとなります。
ユーザー登録
調達購買業務の効率化だけでなく、システムを導入することで、コスト削減や製品・資材のステータス可視化のほか、属人化していた購買情報の共有化による内部不正防止や統制にも役立ちます。
NEWJI DX
製造業に特化したデジタルトランスフォーメーション(DX)の実現を目指す請負開発型のコンサルティングサービスです。AI、iPaaS、および先端の技術を駆使して、製造プロセスの効率化、業務効率化、チームワーク強化、コスト削減、品質向上を実現します。このサービスは、製造業の課題を深く理解し、それに対する最適なデジタルソリューションを提供することで、企業が持続的な成長とイノベーションを達成できるようサポートします。
オンライン講座
製造業、主に購買・調達部門にお勤めの方々に向けた情報を配信しております。
新任の方やベテランの方、管理職を対象とした幅広いコンテンツをご用意しております。
お問い合わせ
コストダウンが利益に直結する術だと理解していても、なかなか前に進めることができない状況。そんな時は、newjiのコストダウン自動化機能で大きく利益貢献しよう!
(Β版非公開)