- お役立ち記事
- For new employees in the product quality department! Basics and practical methods of quality function deployment (QFD)
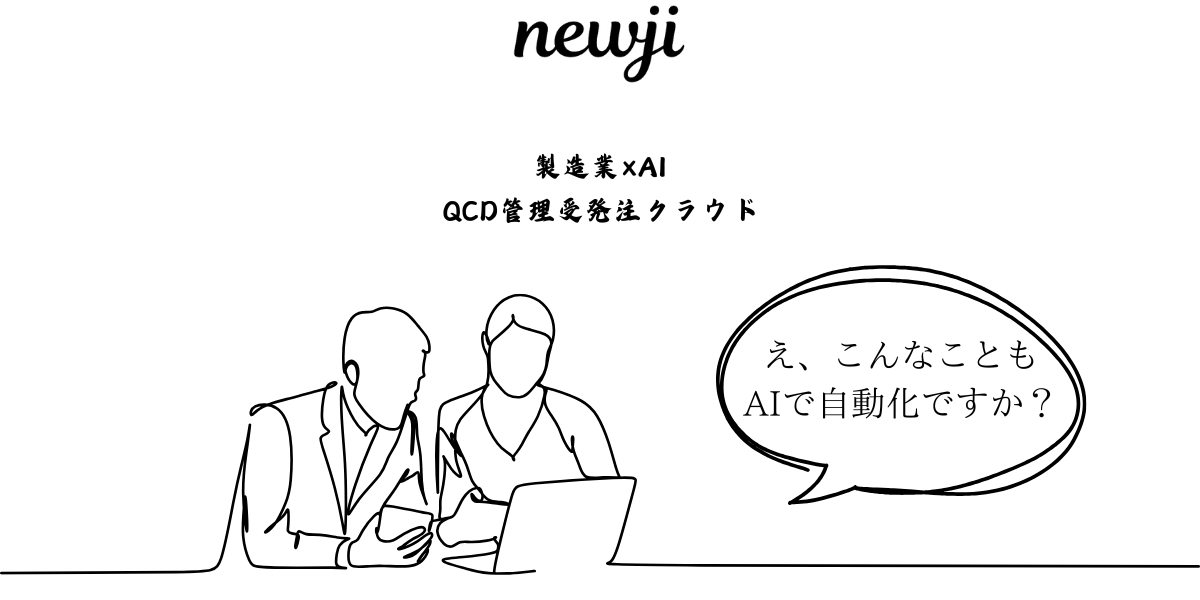
For new employees in the product quality department! Basics and practical methods of quality function deployment (QFD)
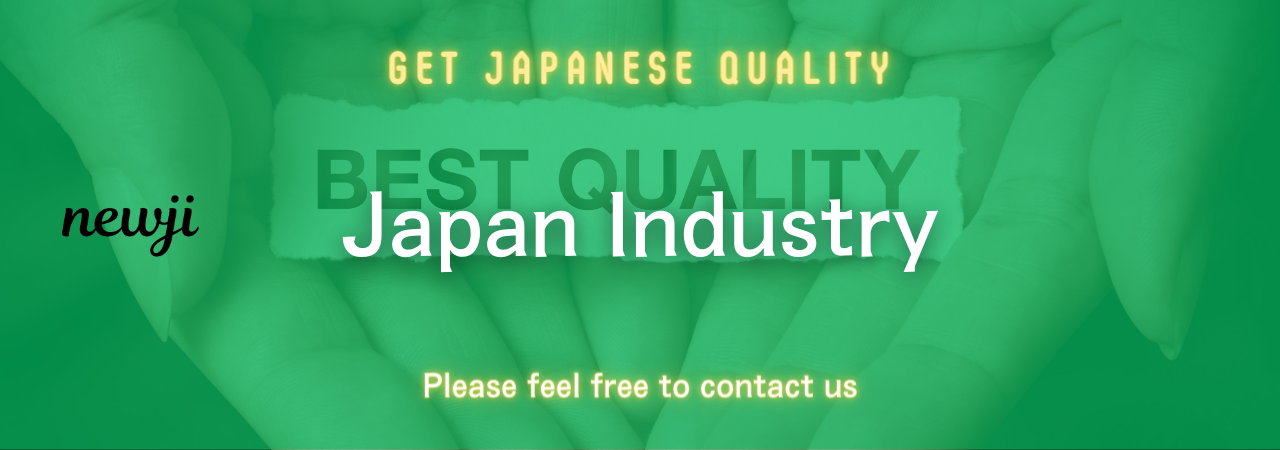
目次
Understanding Quality Function Deployment (QFD)
Quality Function Deployment (QFD) is a comprehensive process used to ensure that the voice of the customer is heard and translated into quality characteristics that a product or service should have.
For new employees in the product quality department, it’s crucial to understand the basics and practical methods of QFD, as it plays a significant role in defining the standards and expectations of customers.
QFD helps in bridging the gap between what customers desire and what a company can produce.
It involves capturing customer requirements, prioritizing them, and turning these requirements into specific plans to produce products that meet these expectations.
Through QFD, teams can design quality into the product from the beginning rather than checking it at the end of the production process.
The Basics of Quality Function Deployment
The Purpose of QFD
The primary aim of QFD is to transform customer needs into engineering characteristics for a product or service.
It ensures that customer satisfaction is prioritized, which in turn can increase competitiveness and success for your product.
With QFD, companies can minimize production costs and reduce the time taken to market while ensuring high-level quality output.
This structured approach helps in clearly understanding what the customer wants and how to achieve it.
The Four Phases of QFD
QFD typically involves four main phases:
1. **Product Planning (House of Quality):** This phase focuses on identifying customer needs and converting them into product specifications.
The House of Quality is a popular tool used in this phase, where a matrix displays relationships between customer requirements and the company’s capabilities to meet those needs.
2. **Product Design:** Once the product characteristics are defined, this phase focuses on designing the product elements that meet these characteristics.
It involves developing the technical characteristics needed for the parts or materials that will eventually make up the final product.
3. **Process Planning:** This phase involves detailing the manufacturing and assembly processes that will produce the designed product.
It ensures that the processes are able to consistently produce the desired quality and performance.
4. **Process Control/Quality Control:** The final phase involves monitoring the production processes to detect any deviations from the quality standards defined.
It includes implementing measures to ensure quality targets are consistently met during the production stage.
Practical Methods in QFD Implementation
Building the House of Quality
To effectively utilize QFD, building the House of Quality is an integral step.
This involves creating a diagram or matrix to visualize the relationship between customer requirements and the company’s ability to meet these needs.
– **Identify Customer Needs:** Start by gathering extensive data about customer requirements through surveys, feedback, interviews, and focus groups.
These inputs represent what customers expect from the product.
– **Prioritize Needs:** Once the needs are collected, they should be prioritized based on their importance to the customer.
This can be determined through methods like ranking or rating techniques, providing a clear focus on what needs to be addressed first.
– **Establish Technical Requirements:** Identify the features and technical specifications necessary to meet customer needs.
These are often product attributes that can be quantitatively measured.
– **Analyze Relationships:** Use the relationship matrix to clarify how each technical requirement will satisfy customer needs.
Assess the strength of these relationships to determine the most impactful technical aspects for development.
Interdepartmental Collaboration
Implementing QFD successfully requires collaboration across various departments within an organization.
From marketing to engineering, every team should provide input and expertise.
– **Marketing Team’s Role:** They should provide insights into customer demographics, preferences, and trends that inform product development.
– **Design and Engineering Teams:** These teams transform the focused customer requirements into tangible design criteria and specifications.
– **Manufacturing Team:** This team ensures that the developed product can be produced practically and consistently while adhering to the defined quality standards.
QFD Software Tools
Using software tools can significantly enhance the QFD process, making it more efficient and less prone to human error.
Several software solutions are available to facilitate building the House of Quality and managing the QFD lifecycle.
– **Ease of Data Handling:** Software tools streamline data entry and analysis, allowing teams to easily update customer requirements and technical specifications.
– **Visualization and Reporting:** These tools provide clear visualizations and standard reports, which are essential for effective communication between teams and stakeholders.
– **Scalability:** As a project grows in complexity, software tools help manage and track changes, ensuring that every aspect of the QFD process is maintained accurately.
The Benefits of Mastering QFD
For new employees in the product quality department, mastering QFD offers numerous benefits.
It provides a deeper understanding of how to create products that truly resonate with customers.
By internalizing QFD principles, new team members can contribute to:
– **Enhanced Customer Satisfaction:** Products that align closely with customer needs and expectations lead to higher levels of satisfaction and loyalty.
– **Reduced Development Time and Cost:** By focusing efforts based on prioritized customer needs, companies can avoid overdesign and unnecessary features, cutting down development time and associated costs.
– **Improved Team Collaboration:** QFD’s structured approach encourages communication and collaboration across departments, reducing the potential for siloed efforts and fostering a more unified team environment.
In conclusion, understanding and implementing QFD is crucial for anyone involved in product quality assurance.
By focusing on the customer and systematically translating their needs into actionable design criteria, new employees can play an integral role in delivering top-quality products that thrive in the market.
資料ダウンロード
QCD調達購買管理クラウド「newji」は、調達購買部門で必要なQCD管理全てを備えた、現場特化型兼クラウド型の今世紀最高の購買管理システムとなります。
ユーザー登録
調達購買業務の効率化だけでなく、システムを導入することで、コスト削減や製品・資材のステータス可視化のほか、属人化していた購買情報の共有化による内部不正防止や統制にも役立ちます。
NEWJI DX
製造業に特化したデジタルトランスフォーメーション(DX)の実現を目指す請負開発型のコンサルティングサービスです。AI、iPaaS、および先端の技術を駆使して、製造プロセスの効率化、業務効率化、チームワーク強化、コスト削減、品質向上を実現します。このサービスは、製造業の課題を深く理解し、それに対する最適なデジタルソリューションを提供することで、企業が持続的な成長とイノベーションを達成できるようサポートします。
オンライン講座
製造業、主に購買・調達部門にお勤めの方々に向けた情報を配信しております。
新任の方やベテランの方、管理職を対象とした幅広いコンテンツをご用意しております。
お問い合わせ
コストダウンが利益に直結する術だと理解していても、なかなか前に進めることができない状況。そんな時は、newjiのコストダウン自動化機能で大きく利益貢献しよう!
(Β版非公開)