- お役立ち記事
- For new employees in the production technology department of the medical device manufacturing industry! Basics of molding and processing of ultra-high molecular weight polyethylene
For new employees in the production technology department of the medical device manufacturing industry! Basics of molding and processing of ultra-high molecular weight polyethylene
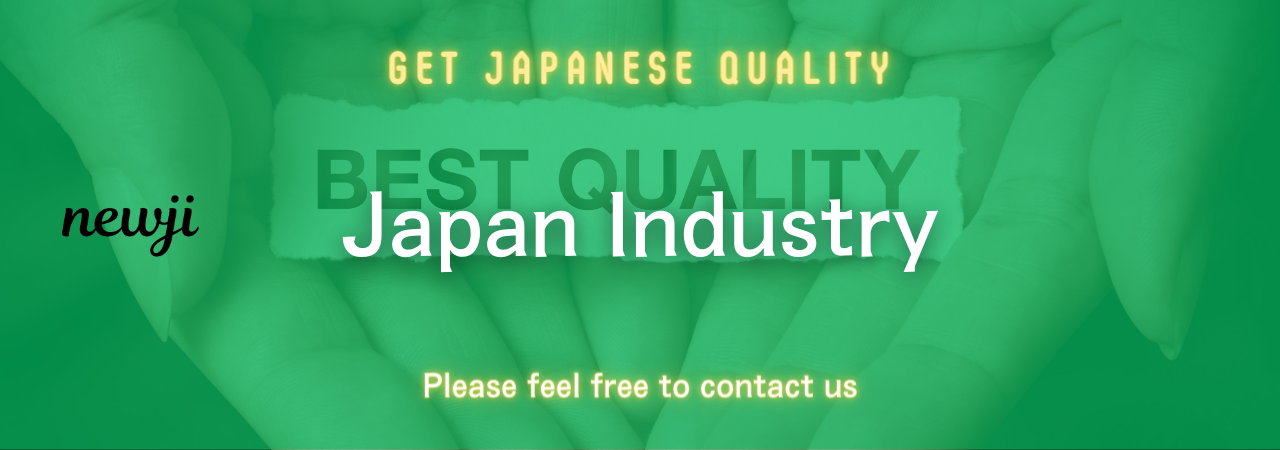
When stepping into the production technology department of the medical device manufacturing industry, understanding the basics of materials like ultra-high molecular weight polyethylene (UHMWPE) is essential. This remarkable polymer plays a crucial role in manufacturing various medical devices. In this article, we will explore the molding and processing of UHMWPE, providing a comprehensive guide for new employees.
目次
What is Ultra-High Molecular Weight Polyethylene?
Ultra-high molecular weight polyethylene (UHMWPE) is a dense and durable type of polyethylene with a molecular weight usually above 3 million g/mol. This material is highly valued in the medical device manufacturing industry due to its outstanding properties such as high impact resistance, excellent wear resistance, and low friction.
UHMWPE is commonly used in medical devices like joint replacements, prosthetics, and implantable devices. Its biocompatibility and resistance to various chemicals make it ideal for such applications where patient safety and product longevity are of utmost importance.
Properties of UHMWPE
High Wear Resistance
One of the most significant properties of UHMWPE is its exceptional wear resistance. This property ensures device longevity and reliability, which is crucial in medical applications where repeated use is common.
Low Friction
UHMWPE offers low friction coefficients, making it smooth and efficient in moving parts, such as joint replacements. This reduces wear and tear on the material and enhances patient comfort.
Biocompatibility
Biocompatibility is critical for medical devices that come into contact with body tissues and fluids. UHMWPE is well tolerated by the human body, making it safe for use in implants and other medical applications.
Molding of UHMWPE
The molding process of UHMWPE is a critical step in manufacturing medical devices, as it influences the final product’s quality, shape, and performance. Here are the primary methods used for molding UHMWPE:
Compression Molding
Compression molding is a popular method for processing UHMWPE. In this process, the polymer powder is placed into a mold cavity and then subjected to heat and pressure. This causes the powder to fuse together into a solid form that matches the shape of the mold.
This technique is beneficial for making large, simple shapes like sheets or rods. It ensures a uniform material density, which is essential for maintaining strength and durability in medical devices.
Ram Extrusion
Ram extrusion is used to produce continuous lengths of UHMWPE, such as rods and tubes. In this process, the polymer powder is fed into a heated chamber and then pushed through a die by a hydraulic ram.
The advantage of ram extrusion is the ability to create long, continuous shapes with consistent properties. This method is often used when precise dimensions are required for medical devices.
Injection Molding
Injection molding is less common for UHMWPE, due to its high viscosity. However, it can be employed with specialized machinery. In this process, the material is melted and injected into a mold under high pressure.
Despite being challenging, injection molding allows for the creation of complex shapes and intricate components, which can be advantageous in developing specialized medical devices.
Processing Techniques for UHMWPE
Processing UHMWPE involves several techniques to enhance its mechanical properties and ensure it meets the required standards for medical use.
Sintering
Sintering is a post-molding process used to enhance the mechanical properties of UHMWPE. The material is heated to just below its melting point, allowing the polymer chains to fuse and crystallize more effectively.
This process improves the strength, wear resistance, and overall durability of UHMWPE, making it suitable for demanding medical applications.
Crosslinking
Crosslinking is a technique used to improve the wear and chemical resistance of UHMWPE. This process involves exposing the polymer to radiation or adding crosslinking agents, resulting in chemical bonds forming between the polymer chains.
Crosslinked UHMWPE is particularly useful in applications such as hip and knee replacements, where long-term wear resistance is critical.
Molecular Orientation
Molecular orientation involves stretching the UHMWPE to align the polymer chains in a specific direction. This technique improves the material’s tensile strength and impact resistance.
In medical devices where high mechanical strength is needed, such as in prosthetics, molecularly oriented UHMWPE offers significant benefits.
Quality Control and Testing
Quality control is a vital component of the UHMWPE molding and processing process. Ensuring the final product meets the required specifications and standards is crucial for patient safety and device efficacy.
Dimensional Accuracy
Dimensional accuracy is assessed to confirm that the molded UHMWPE parts fit precisely as required in medical devices. Precision measurement tools are used to verify the dimensions and tolerances of each component.
Mechanical Testing
Mechanical testing evaluates the strength, wear resistance, and other physical properties of UHMWPE. This includes conducting tensile, compression, and impact tests to ensure the material performs as expected under simulated conditions.
Biocompatibility Testing
Biocompatibility testing is essential for medical devices that will be implanted in or come into contact with the human body. This testing confirms that UHMWPE does not produce any harmful biological responses when used in medical applications.
In conclusion, understanding the molding and processing of ultra-high molecular weight polyethylene is crucial for newcomers in the medical device manufacturing industry. By familiarizing yourself with the properties, molding techniques, processing methods, and quality control measures of UHMWPE, you can contribute to producing reliable and effective medical devices that enhance patient care and safety.
資料ダウンロード
QCD調達購買管理クラウド「newji」は、調達購買部門で必要なQCD管理全てを備えた、現場特化型兼クラウド型の今世紀最高の購買管理システムとなります。
ユーザー登録
調達購買業務の効率化だけでなく、システムを導入することで、コスト削減や製品・資材のステータス可視化のほか、属人化していた購買情報の共有化による内部不正防止や統制にも役立ちます。
NEWJI DX
製造業に特化したデジタルトランスフォーメーション(DX)の実現を目指す請負開発型のコンサルティングサービスです。AI、iPaaS、および先端の技術を駆使して、製造プロセスの効率化、業務効率化、チームワーク強化、コスト削減、品質向上を実現します。このサービスは、製造業の課題を深く理解し、それに対する最適なデジタルソリューションを提供することで、企業が持続的な成長とイノベーションを達成できるようサポートします。
オンライン講座
製造業、主に購買・調達部門にお勤めの方々に向けた情報を配信しております。
新任の方やベテランの方、管理職を対象とした幅広いコンテンツをご用意しております。
お問い合わせ
コストダウンが利益に直結する術だと理解していても、なかなか前に進めることができない状況。そんな時は、newjiのコストダウン自動化機能で大きく利益貢献しよう!
(Β版非公開)