- お役立ち記事
- For new employees in the quality assurance department of the auto parts manufacturing industry! Fundamentals of APQP and quality control in product development
月間76,176名の
製造業ご担当者様が閲覧しています*
*2025年3月31日現在のGoogle Analyticsのデータより
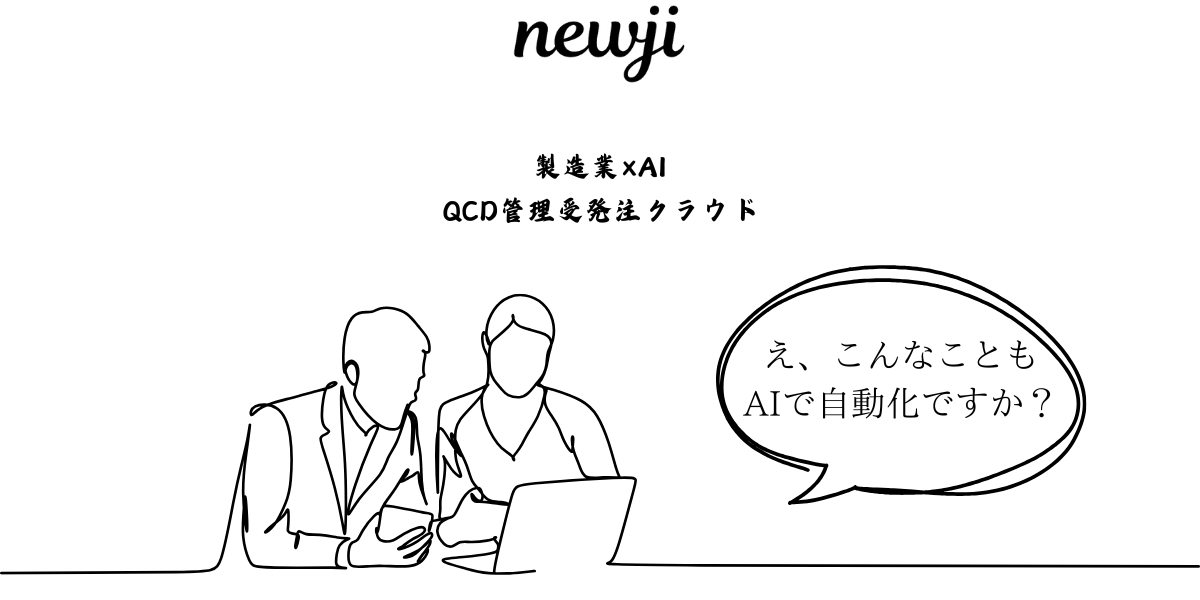
For new employees in the quality assurance department of the auto parts manufacturing industry! Fundamentals of APQP and quality control in product development
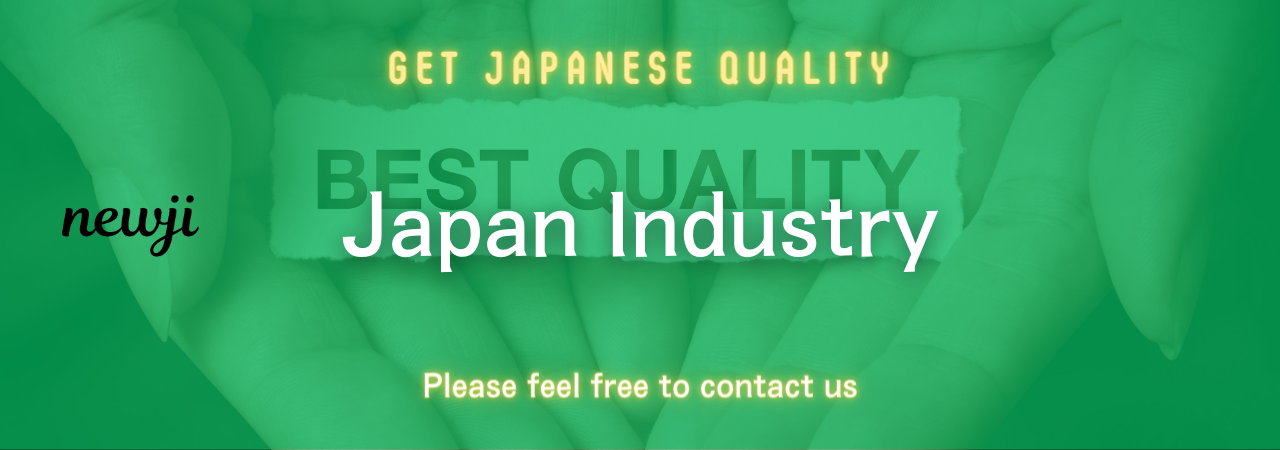
目次
Understanding APQP: A Key Process in Quality Assurance
New employees in the quality assurance department of the auto parts manufacturing industry often encounter the term APQP, or Advanced Product Quality Planning.
APQP is a structured framework used to ensure that a product meets customer needs and expectations.
It involves a series of phases designed to guide teams through the product development process, aiming for high quality and consistency.
The APQP process consists of five main stages: planning, product design and development, process design and development, product and process validation, and production launch.
Each stage requires close attention and collaboration among different departments, including engineering, manufacturing, and quality assurance.
Planning: Setting the Foundation for Success
The planning phase is critical as it lays the groundwork for subsequent stages.
Here, teams identify customer needs and expectations by gathering and analyzing data.
This may involve market research, surveys, and customer feedback.
The goal is to establish what the product should achieve and create a clear product quality objective.
Once customer requirements are defined, a cross-functional team develops a product quality plan.
This plan details the steps necessary to achieve the desired outcomes, including timelines, resources, and responsibilities.
Effective planning ensures that all team members are aligned and working towards common goals.
Product Design and Development
In the product design and development phase, the focus is on translating customer requirements into a tangible product.
Design teams use the information gathered during planning to create detailed product specifications.
This includes selecting materials, determining dimensions, and incorporating safety features.
Additionally, design for manufacturability (DFM) principles are applied to ensure that the product can be manufactured efficiently and cost-effectively.
Teams often utilize computer-aided design (CAD) software to create prototypes and simulate performance under real-world conditions.
Frequent testing and iteration are vital to refining the design and ensuring it meets quality standards before moving on to the next stage.
Process Design and Development
Once the product design is finalized, attention shifts to how the product will be manufactured.
The process design and development phase involves creating and optimizing production processes.
This includes selecting equipment, determining workflow, and establishing quality control measures.
Key considerations during this phase include reducing waste, minimizing variability, and improving production efficiency.
Process engineers work closely with quality assurance teams to implement robust quality control systems.
These systems may involve automated inspections, process checks, and continuous monitoring to ensure that any deviations are quickly identified and corrected.
Product and Process Validation
The validation phase is crucial for verifying that both the product and the manufacturing process meet all required specifications.
During product validation, samples are produced and subjected to rigorous testing.
This involves assessing factors such as performance, durability, and safety under various conditions.
Successful validation confirms that the product meets customer expectations and is ready for mass production.
Similarly, process validation ensures that the manufacturing process consistently produces products of the desired quality.
This often includes conducting trial runs and capability studies to identify any potential issues and implement corrective actions.
Production Launch: Bringing Products to Market
The final stage of APQP is the production launch, where the product is introduced to the market.
Here, the focus is on ramping up production while maintaining high-quality standards.
Successful launch requires detailed planning and coordination among multiple departments.
Teams closely monitor production performance, tracking metrics such as yield rates, defect rates, and customer feedback.
Any issues identified during this phase are addressed promptly to minimize impact on product quality and delivery schedules.
A well-executed launch sets the stage for customer satisfaction and long-term success.
The Role of Quality Control in Product Development
In the auto parts manufacturing industry, quality control (QC) is integral to every stage of product development.
QC involves systematic activities aimed at ensuring product quality and compliance with specifications.
Its primary objective is to prevent defects and ensure customer satisfaction.
Inspection and Testing
Inspection and testing are core components of quality control.
Inspections may occur at various stages of production, from raw material receipt to final product assembly.
These inspections involve visual checks, measurements, and evaluations against established standards.
Testing, on the other hand, assesses the functionality and performance of the product.
This can include stress tests, durability assessments, and performance evaluations under simulated conditions.
Both inspection and testing help identify any deviations from quality standards, allowing teams to take corrective action before products reach customers.
Continuous Improvement
Continuous improvement is a fundamental principle within quality control.
By analyzing data from inspections, tests, and customer feedback, teams can identify trends and areas for improvement.
This often involves using techniques such as root cause analysis, Six Sigma, and lean manufacturing.
The objective is to enhance processes, reduce variability, and optimize product quality over time.
A culture of continuous improvement encourages proactive problem-solving and drives innovation within the organization.
Collaboration and Communication
Effective quality control requires collaboration and communication across departments.
Quality assurance teams work closely with design, engineering, and production teams to align on quality goals and strategies.
Regular meetings, reports, and audits facilitate information sharing and decision-making.
This ensures that all stakeholders are informed about potential issues and can contribute to developing solutions.
Strong collaboration fosters a unified commitment to quality throughout the organization.
Conclusion
As a new employee in the quality assurance department of the auto parts manufacturing industry, understanding APQP and quality control is vital to your role.
By familiarizing yourself with these processes, you’ll be better equipped to contribute to the development of high-quality products.
Remember the importance of each stage in APQP, from planning to production launch, and the role of quality control in maintaining excellence.
With this knowledge, you’ll be prepared to support your team in delivering products that meet and exceed customer expectations.
資料ダウンロード
QCD管理受発注クラウド「newji」は、受発注部門で必要なQCD管理全てを備えた、現場特化型兼クラウド型の今世紀最高の受発注管理システムとなります。
ユーザー登録
受発注業務の効率化だけでなく、システムを導入することで、コスト削減や製品・資材のステータス可視化のほか、属人化していた受発注情報の共有化による内部不正防止や統制にも役立ちます。
NEWJI DX
製造業に特化したデジタルトランスフォーメーション(DX)の実現を目指す請負開発型のコンサルティングサービスです。AI、iPaaS、および先端の技術を駆使して、製造プロセスの効率化、業務効率化、チームワーク強化、コスト削減、品質向上を実現します。このサービスは、製造業の課題を深く理解し、それに対する最適なデジタルソリューションを提供することで、企業が持続的な成長とイノベーションを達成できるようサポートします。
製造業ニュース解説
製造業、主に購買・調達部門にお勤めの方々に向けた情報を配信しております。
新任の方やベテランの方、管理職を対象とした幅広いコンテンツをご用意しております。
お問い合わせ
コストダウンが利益に直結する術だと理解していても、なかなか前に進めることができない状況。そんな時は、newjiのコストダウン自動化機能で大きく利益貢献しよう!
(β版非公開)