- お役立ち記事
- For new employees in the quality control department of electronic equipment manufacturing industry! Tips for improving the bonding quality of SMD (surface mount devices)
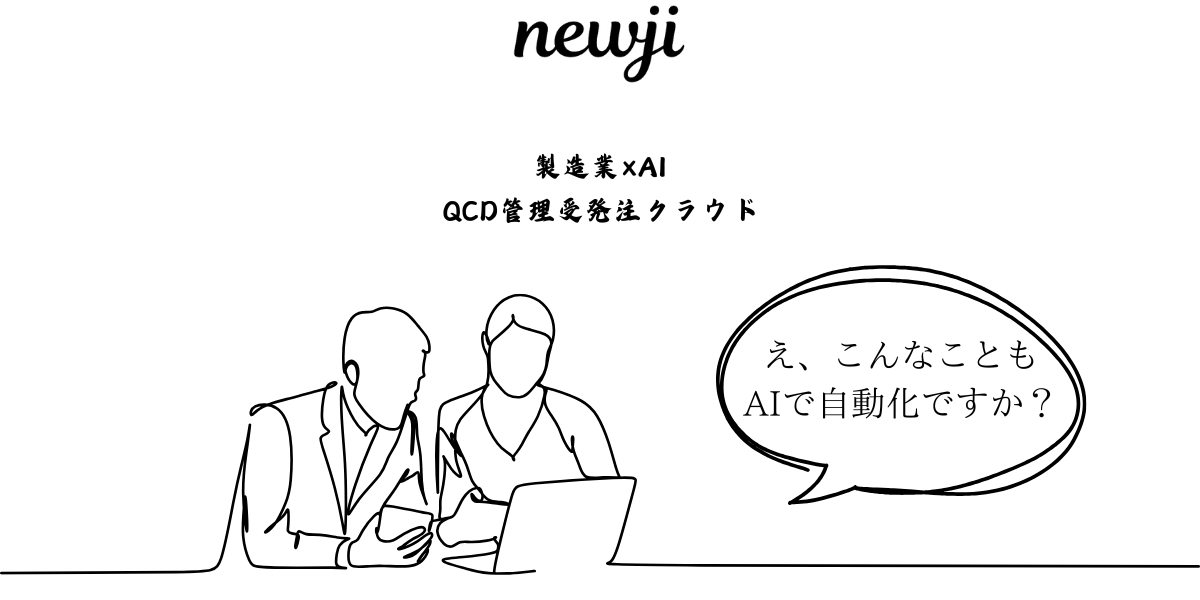
For new employees in the quality control department of electronic equipment manufacturing industry! Tips for improving the bonding quality of SMD (surface mount devices)
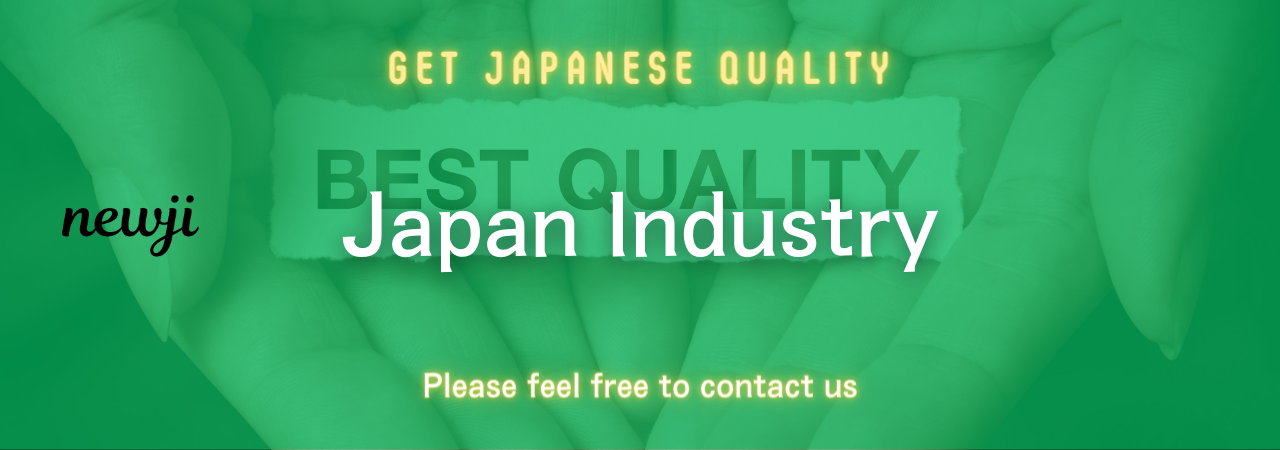
目次
Understanding the Importance of Bonding Quality in SMD
When you step into the quality control department of an electronic equipment manufacturing company, you quickly learn that ensuring the bonding quality of SMDs is crucial.
Surface Mount Devices (SMDs) are fundamental components in electronic assemblies, and their performance is heavily dependent on the quality of the bond between the component and the printed circuit board (PCB).
Good bonding quality ensures reliability and functionality, which is essential for maintaining customer satisfaction and the company’s reputation.
Common Challenges in Bonding SMD
A variety of challenges can arise when dealing with SMD bonding.
The most common issues include insufficient solder, misalignment, and solder bridges.
These problems can lead to poor electrical connections or even complete circuit failure.
Understanding these problems is the first step in improving the bonding quality of SMDs.
Insufficient Solder
Insufficient solder is a frequent challenge and occurs when there is not enough solder to create a secure bond between the SMD and PCB.
This can result in weak joints that are prone to failure.
Regular analysis and adjustments of the soldering process can significantly mitigate this issue.
Misalignment
Misalignment happens when an SMD component is not properly placed on the PCB.
This can lead to incomplete connections and malfunctioning devices.
Implementing precise placement technologies and optimizing the assembly line can help solve alignment issues.
Solder Bridges
Solder bridges occur when excess solder creates an unintended connection between two points.
This can cause short circuits and device failure.
Careful monitoring and control of the soldering process can reduce the incidence of solder bridges.
Tips to Improve Bonding Quality
Now, let’s explore some effective strategies to enhance the bonding quality of SMDs.
These tips will help you tackle the aforementioned challenges head-on.
Invest in Quality Equipment
To achieve good bonding quality, it’s crucial to invest in high-quality equipment.
Modern, precise pick-and-place machines ensure accurate alignment, reducing the risk of misalignment.
Additionally, investing in reliable soldering equipment helps maintain consistent solder application, minimizing issues like insufficient solder and solder bridges.
Regular Calibration and Maintenance
Regular calibration and maintenance of equipment are essential to ensure optimal performance.
Scheduled maintenance checks and timely calibration help machines function correctly, thus improving the bonding quality of SMD components.
This practice also extends the equipment’s lifespan, leading to cost savings in the long run.
Implement Quality Control Processes
Establishing robust quality control processes is crucial for detecting and addressing bonding issues early in the production line.
By implementing rigorous inspections and testing procedures, potential bonding problems can be identified and resolved before products reach the market.
This proactive approach not only improves product quality but also boosts customer trust.
Employee Training and Skill Development
Investing in employee training is vital for improving bonding quality.
Well-trained employees are adept at identifying and correcting bonding issues promptly.
Continuous skill development programs ensure that your team is knowledgeable about the latest techniques and technologies in SMD assembly and quality control.
Optimize Soldering Profiles
Analyzing and optimizing soldering profiles is essential for achieving the right balance.
Adjusting parameters such as temperature, time, and pressure can help in minimizing common bonding problems like insufficient solder and solder bridges.
Experiment with these variables to find the most effective profile for your specific production line.
The Role of Innovation in Bonding Quality
As technology evolves, new innovations are emerging in the electronic manufacturing industry.
Embracing these innovations can significantly enhance the bonding quality of SMDs.
Advanced Inspection Technologies
Advanced inspection technologies, such as automated optical inspection (AOI) and X-ray inspection, provide detailed insights into the SMD bonding process.
These technologies can detect errors that might go unnoticed during manual inspections, allowing for timely corrections and ensuring high bonding quality.
The Use of Advanced Materials
The use of innovative materials in SMD bonding can further improve performance.
Materials with better thermal and electrical properties enhance the reliability and durability of electronic devices, ensuring they meet the highest standards.
Staying updated with emerging materials and incorporating them into your process can give your company an edge.
Continual Improvement and Adaptation
Improving the bonding quality of SMDs is an ongoing process that requires a commitment to continual improvement and adaptation.
Stay informed about industry trends, technologies, and best practices that could influence your production processes.
Regularly review and refine your strategies to address both existing and potential challenges.
By fostering a culture of innovation and quality, you contribute to the overall success of your company and its products.
資料ダウンロード
QCD調達購買管理クラウド「newji」は、調達購買部門で必要なQCD管理全てを備えた、現場特化型兼クラウド型の今世紀最高の購買管理システムとなります。
ユーザー登録
調達購買業務の効率化だけでなく、システムを導入することで、コスト削減や製品・資材のステータス可視化のほか、属人化していた購買情報の共有化による内部不正防止や統制にも役立ちます。
NEWJI DX
製造業に特化したデジタルトランスフォーメーション(DX)の実現を目指す請負開発型のコンサルティングサービスです。AI、iPaaS、および先端の技術を駆使して、製造プロセスの効率化、業務効率化、チームワーク強化、コスト削減、品質向上を実現します。このサービスは、製造業の課題を深く理解し、それに対する最適なデジタルソリューションを提供することで、企業が持続的な成長とイノベーションを達成できるようサポートします。
オンライン講座
製造業、主に購買・調達部門にお勤めの方々に向けた情報を配信しております。
新任の方やベテランの方、管理職を対象とした幅広いコンテンツをご用意しております。
お問い合わせ
コストダウンが利益に直結する術だと理解していても、なかなか前に進めることができない状況。そんな時は、newjiのコストダウン自動化機能で大きく利益貢献しよう!
(Β版非公開)