- お役立ち記事
- For new leaders in equipment management departments in the steel industry! How to leverage TPM activities to improve equipment reliability
月間76,176名の
製造業ご担当者様が閲覧しています*
*2025年3月31日現在のGoogle Analyticsのデータより
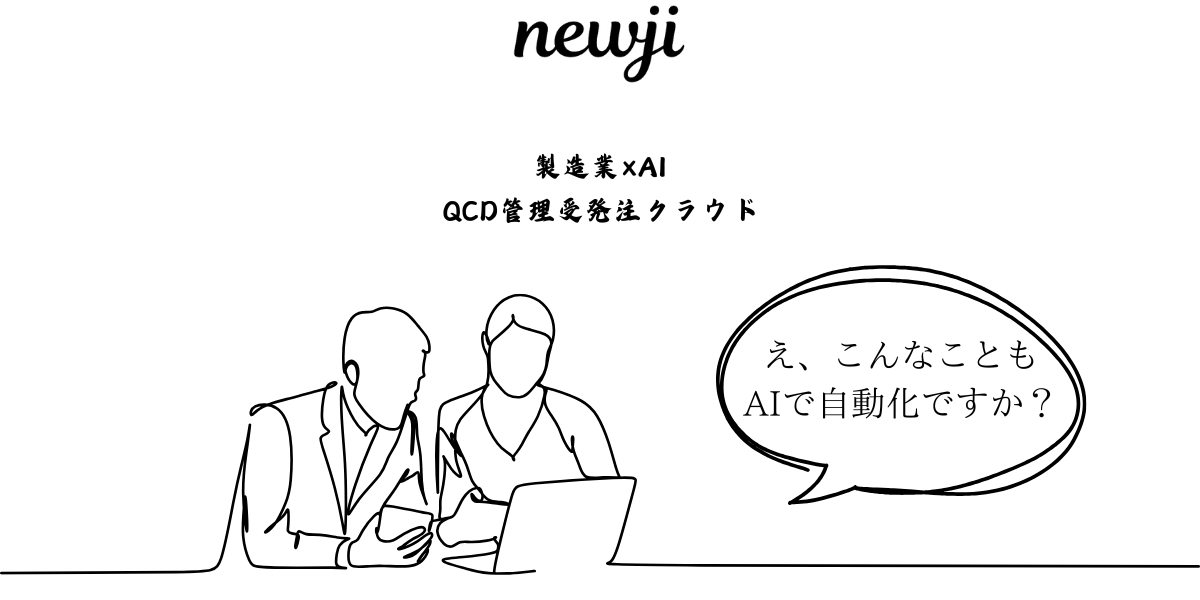
For new leaders in equipment management departments in the steel industry! How to leverage TPM activities to improve equipment reliability
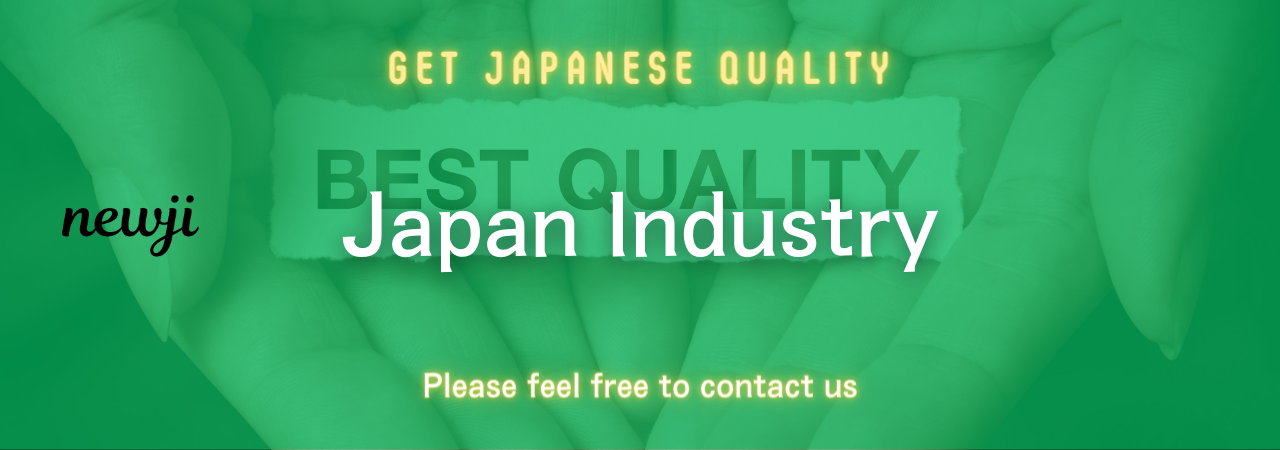
目次
Introduction to TPM Activities
Total Productive Maintenance (TPM) is a proactive and holistic approach to equipment management that is widely used in the steel industry and beyond.
It aims to maximize equipment efficiency and reliability, with the goal of improving overall productivity.
For new leaders in equipment management departments, understanding how to effectively leverage TPM activities can lead to notable improvements in operational performance.
TPM is built on the foundation of proactive and preventive maintenance, bringing together various teams across the organization to ensure that equipment failures are minimized, if not eliminated.
It encourages collaboration between operators, maintenance personnel, and management to enhance equipment reliability and extend its lifecycle.
This approach helps to address the root causes of equipment issues rather than just treating the symptoms.
The Pillars of TPM
TPM is structured around several key pillars, each contributing to equipment reliability in unique ways.
Understanding these pillars is crucial for new leaders looking to implement or enhance TPM activities.
1. Autonomous Maintenance
Autonomous Maintenance involves empowering operators to take on basic maintenance tasks.
Rather than relying solely on specialized maintenance personnel, operators are trained to conduct routine checks, clean machines, and perform minor repairs.
This engagement not only increases the sense of ownership among operators but also reduces the response time to potential issues.
Regular inspections by the operators can help in early detection of abnormalities, ensuring that any potential failures are addressed before they escalate into significant problems.
New leaders should foster an environment where operators are encouraged and supported in adopting these responsibilities.
2. Planned Maintenance
Planned Maintenance is all about scheduling regular maintenance tasks based on time elapsed or operating output, rather than responding only when equipment breaks down.
This proactive strategy helps to avoid unscheduled downtime and ensures optimal equipment performance.
New leaders should work closely with their teams to develop and adhere to a detailed maintenance schedule.
This involves analyzing equipment data to predict potential failures and plan maintenance tasks accordingly.
3. Focused Improvement
Focused Improvement teams work collaboratively to tackle specific problems related to equipment inefficiencies.
These teams analyze underlying issues, brainstorm solutions, and implement changes to improve performance.
For new leaders, facilitating such teams means actively engaging with various departments to identify areas needing improvement.
Encouraging a culture of continuous improvement and recognizing team achievements can lead to significant advancements in equipment reliability.
4. Training and Education
Training and Education ensure that all personnel involved in equipment management have the necessary skills and knowledge.
This pillar emphasizes the importance of ongoing learning and capacity building to keep up with technological advances and new industry practices.
New leaders should prioritize creating comprehensive training programs tailored to the needs of their team members.
These programs should focus on developing technical skills as well as fostering an understanding of TPM principles.
5. Quality Maintenance
Quality Maintenance involves integrating quality assurance into equipment management processes.
It focuses on preventing defects and ensuring that equipment functions as intended, contributing to the overall product quality.
Leaders should emphasize the importance of maintaining equipment in a manner that upholds product quality standards.
This entails stringent testing and quality control measures to identify areas of improvement.
6. The Role of Safety, Health, and Environment (SHE)
SHE plays a critical role in TPM by ensuring that equipment management practices are aligned with safety, health, and environmental regulations.
It aims to create a safe and sustainable working environment while minimizing risks associated with equipment operations.
New leaders must prioritize SHE policies, integrating them into every aspect of TPM activities.
This includes conducting regular safety audits, providing appropriate safety training, and promoting a culture where safety is part of everyday activities.
Implementing TPM in Equipment Management
New leaders looking to leverage TPM must begin by fostering a culture that supports this maintenance approach.
This starts with securing executive management support to ensure the necessary resources and commitment.
Begin with training and education.
Equip your team with the fundamental knowledge of TPM principles and practical skills they need.
Ensure that training programs are continuous, adapting to new challenges and technological advancements.
Engage cross-functional teams.
TPM is most effective when there is collaboration across various departments.
Form improvement teams that bring together operators, maintenance personnel, and engineers, so that all perspectives contribute towards enhancing equipment reliability.
Leverage data and technology.
Modern solutions, such as IoT-based sensors, can provide real-time data to predict equipment failures.
Encouraging your team to utilize data analytics will lead to informed decision-making and proactive maintenance actions.
Encourage a proactive maintenance culture by setting clear objectives and celebrating successes.
Share results and recognize individuals or teams who contribute to TPM improvements.
Reward initiatives that demonstrate cost savings, improved uptime, or enhanced safety.
Conclusion
For new leaders in equipment management departments within the steel industry, embracing TPM activities is a vital step towards improving equipment reliability and achieving operational excellence.
By understanding the core pillars of TPM and implementing them strategically, leaders can drive significant advancements in maintenance processes.
Promoting a culture of ownership, continuous improvement, and proactive maintenance will result in increased equipment uptime, reduced maintenance costs, and a safer working environment.
TPM provides the tools and framework necessary to transition from reactive maintenance to a more efficient, forward-thinking approach, ultimately benefiting the entire organization.
資料ダウンロード
QCD管理受発注クラウド「newji」は、受発注部門で必要なQCD管理全てを備えた、現場特化型兼クラウド型の今世紀最高の受発注管理システムとなります。
ユーザー登録
受発注業務の効率化だけでなく、システムを導入することで、コスト削減や製品・資材のステータス可視化のほか、属人化していた受発注情報の共有化による内部不正防止や統制にも役立ちます。
NEWJI DX
製造業に特化したデジタルトランスフォーメーション(DX)の実現を目指す請負開発型のコンサルティングサービスです。AI、iPaaS、および先端の技術を駆使して、製造プロセスの効率化、業務効率化、チームワーク強化、コスト削減、品質向上を実現します。このサービスは、製造業の課題を深く理解し、それに対する最適なデジタルソリューションを提供することで、企業が持続的な成長とイノベーションを達成できるようサポートします。
製造業ニュース解説
製造業、主に購買・調達部門にお勤めの方々に向けた情報を配信しております。
新任の方やベテランの方、管理職を対象とした幅広いコンテンツをご用意しております。
お問い合わせ
コストダウンが利益に直結する術だと理解していても、なかなか前に進めることができない状況。そんな時は、newjiのコストダウン自動化機能で大きく利益貢献しよう!
(β版非公開)