- お役立ち記事
- For new leaders in the design department of electronics manufacturing industry! Fundamentals and success stories of DFM (Design for Manufacturability)
For new leaders in the design department of electronics manufacturing industry! Fundamentals and success stories of DFM (Design for Manufacturability)
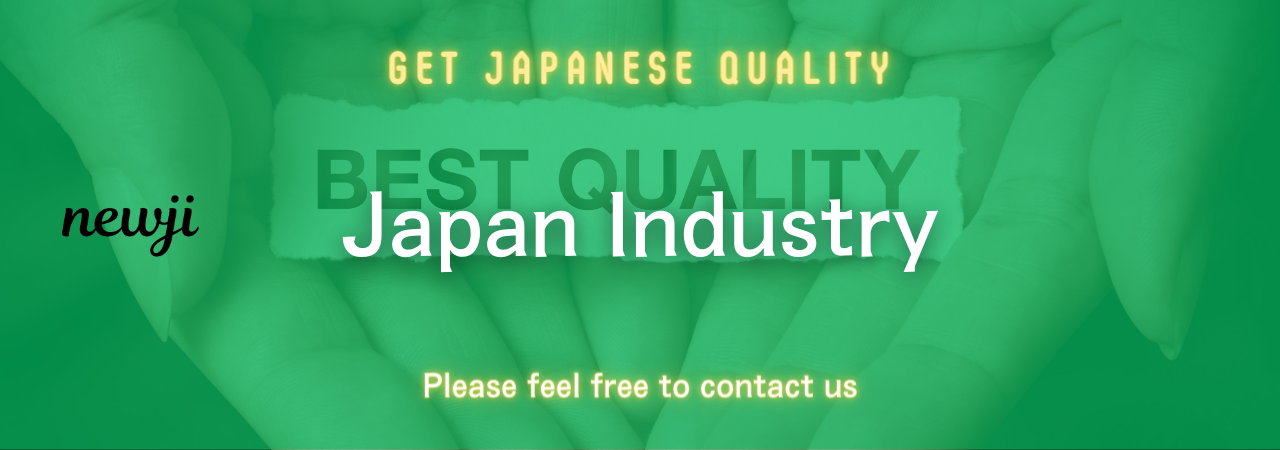
目次
Understanding DFM: A Tool for New Design Leaders
Design for Manufacturability, commonly known as DFM, is an essential principle in the electronics manufacturing industry.
If you’re a new leader in the design department, this concept is crucial for your team’s success.
DFM is about creating designs that are not only functional but also easy and cost-effective to manufacture.
In the world of electronics, where precision and efficiency are key, incorporating DFM in your workflow can make a substantial difference.
As a leader, understanding and implementing DFM strategies will not only streamline production but can also significantly contribute to cost savings.
This approach emphasizes collaboration between the design and manufacturing teams from the onset of a project.
By aligning these two critical phases, potential manufacturing issues can be identified and addressed early on, saving time and resources in the long run.
The Importance of DFM in Electronics Manufacturing
In electronics manufacturing, even minor errors in the design phase can lead to substantial issues downstream.
This is where DFM becomes a game-changer.
Integrating DFM into your design process helps ensure that your products are produced with optimum quality while minimizing waste, defects, and production delays.
By focusing on DFM, your department can achieve higher product reliability and performance.
The primary goal is to simplify the design, making it easier to produce without compromising on quality.
This involves selecting appropriate materials, ensuring components are easily accessible, and designing with the capabilities of manufacturing equipment in mind.
Moreover, DFM encourages teamwork across various departments.
By fostering communication between design and manufacturing, there can be a shared understanding of production constraints and possibilities.
This leads to more informed decisions and innovative solutions that benefit the entire operation.
Key Principles of DFM for New Leaders
As a new leader in the design department, it is important to familiarize yourself with the key principles of DFM to guide your team effectively.
These principles include:
Simplification
A streamlined, straightforward design is often easier to produce.
Complex designs can increase the risk of errors and require additional resources, which can inflate costs and time.
Standardization
Using standard components and materials wherever possible reduces the need for specialized tools or processes.
This can lead to more efficient production and easier sourcing.
Design for Assembly
Ensure that your design facilitates easy and efficient assembly.
Components should fit together seamlessly, minimizing the need for adjustments or rework during assembly.
Process and Material Selection
Choose processes and materials that are compatible with the manufacturing capabilities available.
Consider factors like availability, cost, and the environmental impact of materials.
Success Stories: Real-World Applications of DFM
To grasp the practical impact of DFM, let’s look at some real-world success stories.
These examples illustrate how businesses have leveraged DFM principles to their advantage:
Case Study 1: Streamlined Smart Device Production
A leading smart device manufacturer faced recurring assembly issues that led to costly production delays.
By implementing DFM strategies, the company simplified its product design, reducing the number of components and interfaces.
This change not only accelerated assembly time but also improved product reliability, leading to a notable increase in customer satisfaction.
Case Study 2: Cost Reduction in Automotive Electronics
An automotive electronics company sought ways to cut costs without compromising on performance.
By adopting DFM practices, the design team collaborated closely with suppliers and production engineers.
They standardized on certain components which led to bulk purchasing discounts and reduced production complexity.
The result was a significant reduction in manufacturing costs, which allowed the company to allocate resources to other strategic areas.
Case Study 3: Optimized PCB Design
A printed circuit board (PCB) manufacturer encountered high defect rates due to intricate design specifications.
The introduction of DFM techniques enabled them to re-evaluate their design rules, focusing on manufacturability.
With modifications that emphasized simplicity and consistency with manufacturing capabilities, defect rates plummeted, improving overall throughput and reducing scrap costs.
Steps to Implementing DFM in Your Team
Integrating DFM into your design department requires a strategic approach.
Here are some key steps to successfully implement DFM:
Educate Your Team
Ensure your team understands the importance and benefits of DFM.
Regular training sessions and workshops can help them grasp the core concepts and apply these principles effectively in their projects.
Encourage Cross-Department Collaboration
Promote a culture of collaborative problem-solving between design, engineering, and manufacturing departments.
Facilitating regular meetings and open communication channels will aid in addressing potential issues early.
Evaluate and Adapt
Continuously evaluate the manufacturing process to identify areas for improvement.
Be open to adapting designs based on feedback from production teams to achieve better manufacturability.
Utilize DFM Software Tools
Leverage DFM software tools to analyze designs for manufacturability issues before production begins.
These tools can provide valuable insights and recommendations, helping identify potential challenges in advance.
Conclusion
For new leaders in the design department of the electronics manufacturing industry, mastering DFM is a crucial step towards success.
Embracing DFM principles can lead to enhanced product quality, reduced costs, and improved collaboration across departments.
By understanding the key principles and learning from real-world applications, you can effectively guide your team to create innovative, manufacturable designs that meet the demands of this rapidly evolving industry.
資料ダウンロード
QCD調達購買管理クラウド「newji」は、調達購買部門で必要なQCD管理全てを備えた、現場特化型兼クラウド型の今世紀最高の購買管理システムとなります。
ユーザー登録
調達購買業務の効率化だけでなく、システムを導入することで、コスト削減や製品・資材のステータス可視化のほか、属人化していた購買情報の共有化による内部不正防止や統制にも役立ちます。
NEWJI DX
製造業に特化したデジタルトランスフォーメーション(DX)の実現を目指す請負開発型のコンサルティングサービスです。AI、iPaaS、および先端の技術を駆使して、製造プロセスの効率化、業務効率化、チームワーク強化、コスト削減、品質向上を実現します。このサービスは、製造業の課題を深く理解し、それに対する最適なデジタルソリューションを提供することで、企業が持続的な成長とイノベーションを達成できるようサポートします。
オンライン講座
製造業、主に購買・調達部門にお勤めの方々に向けた情報を配信しております。
新任の方やベテランの方、管理職を対象とした幅広いコンテンツをご用意しております。
お問い合わせ
コストダウンが利益に直結する術だと理解していても、なかなか前に進めることができない状況。そんな時は、newjiのコストダウン自動化機能で大きく利益貢献しよう!
(Β版非公開)