- お役立ち記事
- For new leaders in the equipment maintenance department! How to prevent human error using pokayoke technology
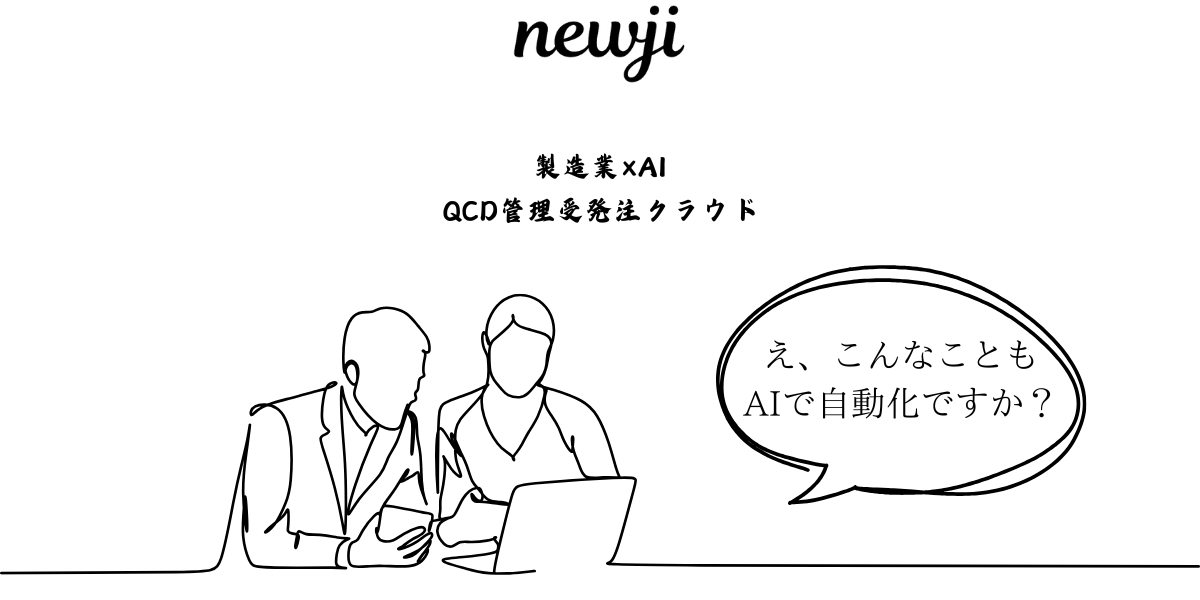
For new leaders in the equipment maintenance department! How to prevent human error using pokayoke technology
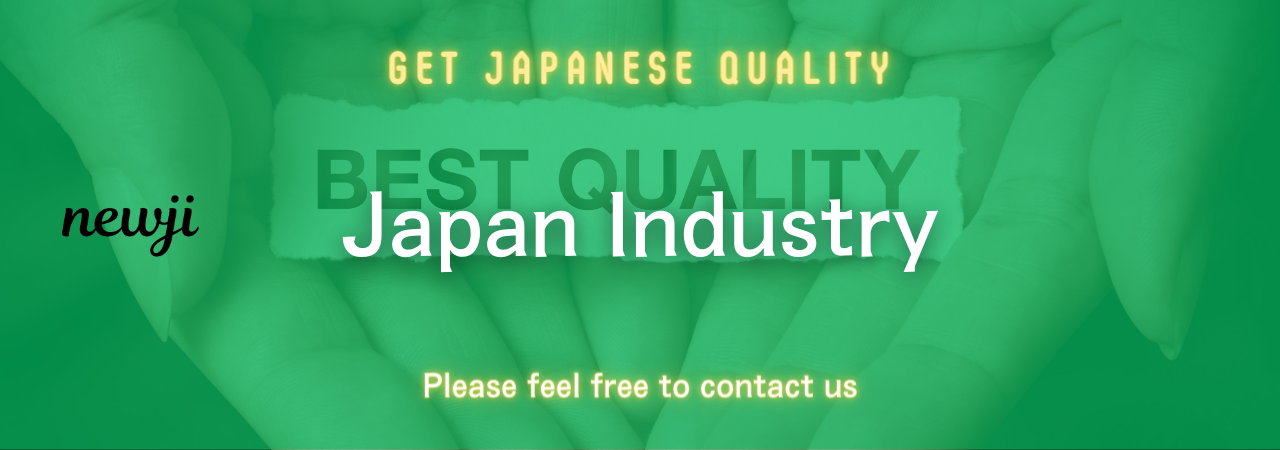
目次
Understanding Pokayoke Technology
Pokayoke, a Japanese term that translates to “mistake-proofing,” is a crucial concept in various industries, especially in equipment maintenance and manufacturing.
This technique aims to eliminate human error by designing processes and systems that prevent mistakes before they occur.
It’s an essential tool for new leaders in the equipment maintenance department, where the stakes of errors can be high and expensive.
At its core, pokayoke involves creating measures that make it difficult, if not impossible, for errors to happen.
These measures are usually integrated into the workflow or equipment to catch mistakes before they affect the final output.
The primary objective is to enhance efficiency and safety without relying solely on human vigilance.
The Importance of Human Error Prevention
Human error is an inevitable aspect of any manual task, influenced by factors such as fatigue, lack of training, or simple oversight.
In equipment maintenance, even a minor error can lead to catastrophic failures, costly repairs, and potential safety hazards.
Therefore, adopting pokayoke in your processes can significantly reduce these risks.
For new leaders, understanding the impact of human error and the role of pokayoke helps set a foundation for a more efficient and error-free department.
Implementing these systems can serve as a proactive approach to managing potential failures and promoting a culture of continuous improvement.
Key Principles of Pokayoke
Pokayoke revolves around three primary principles that help in mistake-proofing:
1. Prevention
Prevention involves designing a process in such a way that it becomes impossible for a mistake to be made.
For example, in a maintenance setting, parts can be designed to fit only in the correct orientation, thereby preventing incorrect assembly.
2. Detection
If prevention isn’t feasible, the next step is to detect errors as they occur.
This can be achieved by integrating sensors or alarms that alert workers to mistakes in real-time, allowing immediate correction before they escalate.
3. Correction
Once an error is detected, the process should have systems in place to correct it quickly.
This might involve automated shutdowns, manual error handling protocols, or visual cues that guide the user to rectify the mistake.
Implementing Pokayoke in Equipment Maintenance
To effectively integrate pokayoke into your equipment maintenance processes, consider a step-by-step approach:
1. Identify Critical Points
Start by analyzing your current processes and identifying points where errors are most likely to occur.
Focus on areas that have historically been problematic or processes that are particularly complex.
2. Understand the Root Causes
Once you’ve pinpointed critical points, delve deeper to understand why these errors happen.
Are they due to a lack of training, inadequate tools, or poor process design?
Knowing the root cause will guide your pokayoke strategy.
3. Design Pokayoke Solutions
Based on your findings, design solutions that either prevent, detect, or correct errors.
Consider implementing physical controls like jigs and fixtures, electronic aids like sensors, and procedural changes that enforce compliance.
4. Test and Refine
Before full-scale implementation, test your pokayoke solutions on a small scale.
Gather feedback from your team and make necessary refinements to ensure the solutions are practical and effective.
5. Train and Educate
Provide comprehensive training to your team on the new systems and processes.
Ensure they understand the purpose behind each pokayoke measure and how it contributes to overall safety and efficiency.
Benefits of Pokayoke in Leadership
Implementing pokayoke in your equipment maintenance department not only reduces errors but also has several benefits that enhance your leadership:
1. Improved Safety
By preventing errors, pokayoke significantly enhances workplace safety, reducing the likelihood of accidents and injuries.
This creates a safer environment for your team and fosters a sense of security and trust.
2. Increased Efficiency
Without frequent interruptions from errors, maintenance processes become more streamlined and efficient.
This can lead to faster turnaround times, improved productivity, and reduced downtime.
3. Cost Savings
Minimizing errors leads to fewer repairs, less waste, and lower overall maintenance costs.
These savings can be allocated to other areas of your department, promoting growth and development.
4. Enhanced Team Morale
A workplace with fewer errors and safety threats is more conducive to high morale and job satisfaction.
Your team members will feel more motivated and engaged when they know their work is valued and supported by robust systems.
Conclusion
For new leaders in the equipment maintenance department, adopting pokayoke technology is a strategic move towards achieving operational excellence.
By understanding and implementing mistake-proofing measures, you can prevent human errors, enhance safety, and improve overall efficiency.
As you embark on this path, remember that pokayoke is not a one-time fix but a continuous improvement process.
Encourage your team to embrace this mindset and contribute ideas for further innovations.
In doing so, you’ll cultivate a proactive, resilient department capable of meeting future challenges head-on.
資料ダウンロード
QCD調達購買管理クラウド「newji」は、調達購買部門で必要なQCD管理全てを備えた、現場特化型兼クラウド型の今世紀最高の購買管理システムとなります。
ユーザー登録
調達購買業務の効率化だけでなく、システムを導入することで、コスト削減や製品・資材のステータス可視化のほか、属人化していた購買情報の共有化による内部不正防止や統制にも役立ちます。
NEWJI DX
製造業に特化したデジタルトランスフォーメーション(DX)の実現を目指す請負開発型のコンサルティングサービスです。AI、iPaaS、および先端の技術を駆使して、製造プロセスの効率化、業務効率化、チームワーク強化、コスト削減、品質向上を実現します。このサービスは、製造業の課題を深く理解し、それに対する最適なデジタルソリューションを提供することで、企業が持続的な成長とイノベーションを達成できるようサポートします。
オンライン講座
製造業、主に購買・調達部門にお勤めの方々に向けた情報を配信しております。
新任の方やベテランの方、管理職を対象とした幅広いコンテンツをご用意しております。
お問い合わせ
コストダウンが利益に直結する術だと理解していても、なかなか前に進めることができない状況。そんな時は、newjiのコストダウン自動化機能で大きく利益貢献しよう!
(Β版非公開)