- お役立ち記事
- For new leaders in the quality assurance department! A step-by-step guide to effective why-why analysis
月間76,176名の
製造業ご担当者様が閲覧しています*
*2025年3月31日現在のGoogle Analyticsのデータより
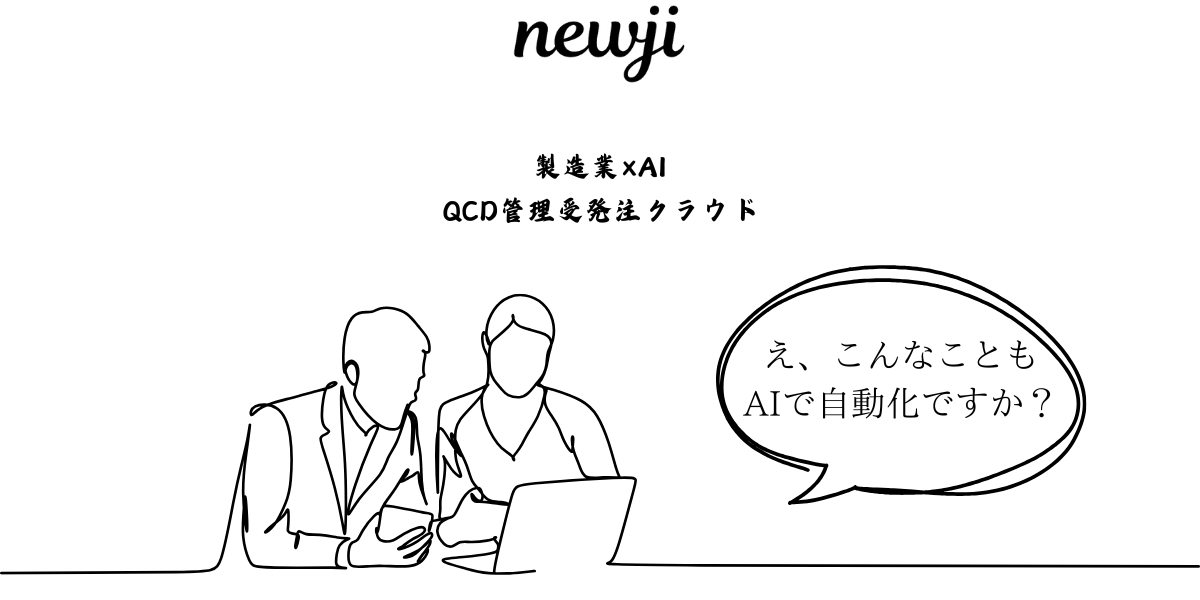
For new leaders in the quality assurance department! A step-by-step guide to effective why-why analysis
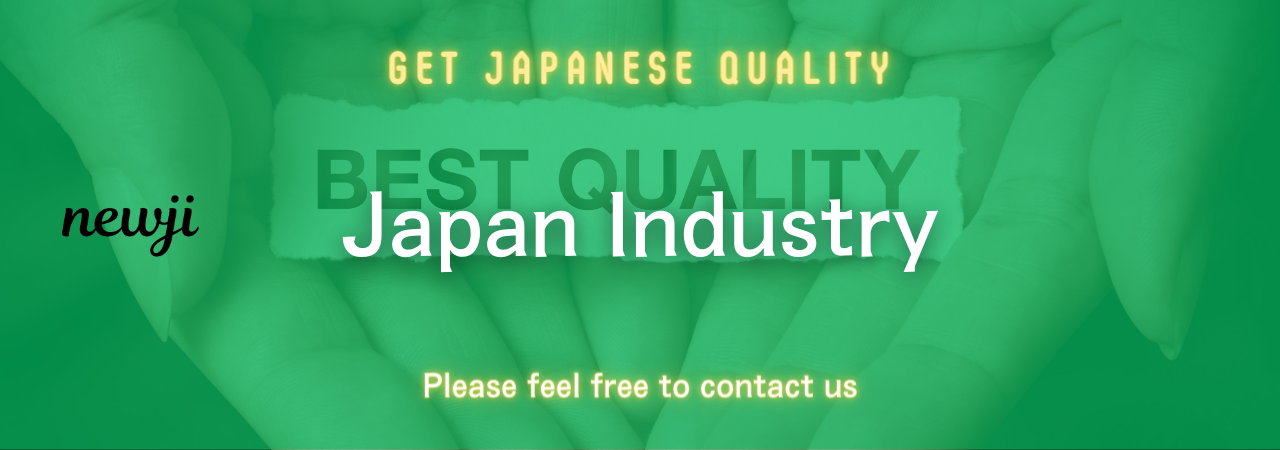
目次
Understanding Why-Why Analysis
Why-Why Analysis is a methodical approach used in identifying the root causes of a problem within a process or system.
As someone stepping into a leadership role in the quality assurance department, understanding this tool is essential.
By addressing the foundational issues, rather than just the symptoms, you can implement effective solutions that prevent recurrence.
Why-Why Analysis Basics
At its core, Why-Why Analysis is simply asking “why” repeatedly until you reach the underlying cause of a problem.
Typically, it involves asking “why” at least five times, though this can vary depending on the complexity of the situation.
This technique is used in various industries to improve processes, enhance quality, and increase productivity.
Step-by-Step Guide to Why-Why Analysis
Following a systematic guide can streamline the process and improve your ability to conduct an effective Why-Why Analysis.
Step 1: Define the Problem
Clearly define and describe the problem at hand.
Before diving into analysis, it’s crucial to have a precise understanding of what you’re investigating.
The more specific the problem statement, the easier it becomes to identify the root causes.
Step 2: Assemble the Team
Quality assurance is rarely an individual task.
Assemble a team with diverse perspectives to brainstorm effectively.
Involve employees from different levels and departments to capture a range of insights and understand the problem from multiple angles.
Step 3: Start the Analysis
Once the problem is defined and the team is ready, begin asking “why” the problem occurred.
Start with the apparent issue and work your way backward, systematically examining each layer.
Step 4: Document Each Response
Every answer to a “why” should be documented meticulously.
These documented responses serve as a trail leading to the root cause and provide valuable reference material for future analyses and audits.
Step 5: Identify the Root Cause
Continue the questioning process until you reach a consensus on the root cause of the problem.
It’s vital to agree as a team on when you’ve adequately identified the fundamental issue.
Applying Why-Why Analysis in Quality Assurance
As a new leader in quality assurance, here’s how you can effectively apply the Why-Why Analysis in your department.
Improving Product Quality
Applying Why-Why Analysis can significantly enhance product quality.
When defects arise, use this tool to determine whether the issue is mechanical, procedural, or human-related.
By correcting the root causes, you ensure consistent output and customer satisfaction.
Streamlining Processes
In quality assurance, inefficiency can lead to delays and increased costs.
By applying Why-Why Analysis, you can identify and eliminate bottlenecks, optimize workflows, and streamline operations.
Enhancing Team Collaboration
Why-Why Analysis promotes teamwork and inclusivity.
By involving team members from various fields, you foster a culture of collaboration and shared responsibility, which can lead to more effective problem-solving and innovation.
Challenges and Tips
While Why-Why Analysis is a powerful tool, some challenges can arise.
Overcoming Subjectivity
One challenge is ensuring objectivity in responses.
To counter this, rely on data and factual evidence whenever possible, and encourage team members to support their assertions with concrete examples.
Addressing Complex Problems
Some problems may have multiple root causes.
In such cases, Why-Why Analysis can become complex.
It might be beneficial to break down the issue into smaller, more manageable components and conduct separate analyses on each.
Ensuring Team Buy-in
Gaining the team’s buy-in can be challenging.
To foster commitment, offer training on Why-Why Analysis and highlight past successes that demonstrate the method’s effectiveness.
Conclusion: Embrace Continuous Improvement
For a new leader in quality assurance, mastering Why-Why Analysis is a vital skill.
It not only resolves current issues but also fosters a culture of continuous improvement and accountability within your team.
By implementing Why-Why Analysis, you leverage a proven tool to enhance overall performance, driving both personal and organizational growth.
資料ダウンロード
QCD管理受発注クラウド「newji」は、受発注部門で必要なQCD管理全てを備えた、現場特化型兼クラウド型の今世紀最高の受発注管理システムとなります。
ユーザー登録
受発注業務の効率化だけでなく、システムを導入することで、コスト削減や製品・資材のステータス可視化のほか、属人化していた受発注情報の共有化による内部不正防止や統制にも役立ちます。
NEWJI DX
製造業に特化したデジタルトランスフォーメーション(DX)の実現を目指す請負開発型のコンサルティングサービスです。AI、iPaaS、および先端の技術を駆使して、製造プロセスの効率化、業務効率化、チームワーク強化、コスト削減、品質向上を実現します。このサービスは、製造業の課題を深く理解し、それに対する最適なデジタルソリューションを提供することで、企業が持続的な成長とイノベーションを達成できるようサポートします。
製造業ニュース解説
製造業、主に購買・調達部門にお勤めの方々に向けた情報を配信しております。
新任の方やベテランの方、管理職を対象とした幅広いコンテンツをご用意しております。
お問い合わせ
コストダウンが利益に直結する術だと理解していても、なかなか前に進めることができない状況。そんな時は、newjiのコストダウン自動化機能で大きく利益貢献しよう!
(β版非公開)