- お役立ち記事
- For new managers in the factory management department! Introduction of 5S activities and how to proceed with continuous improvement
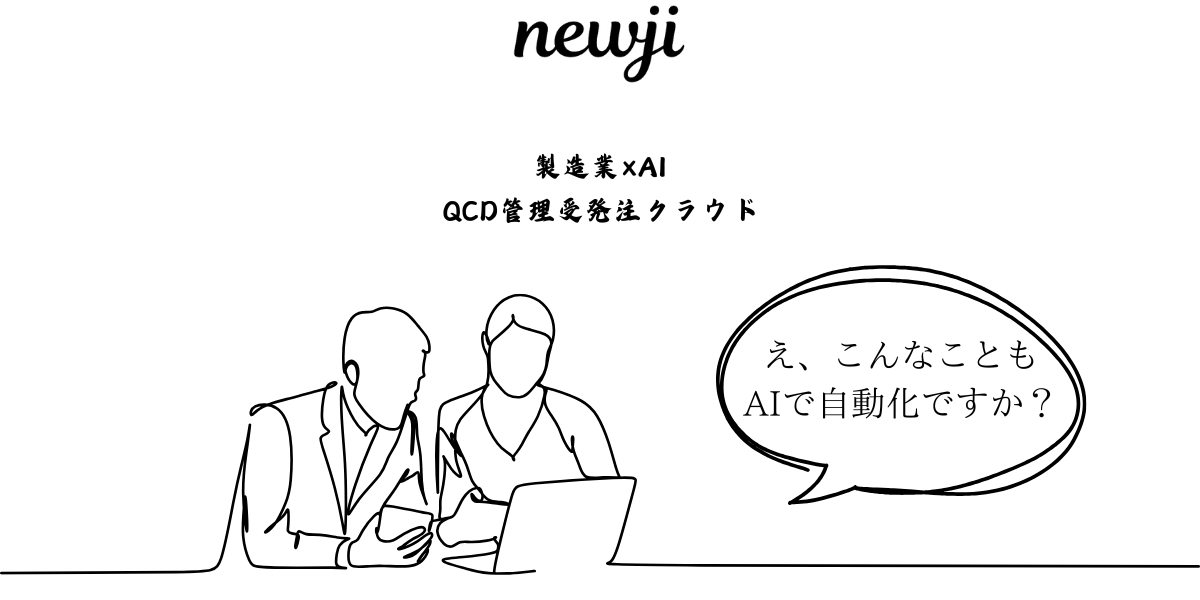
For new managers in the factory management department! Introduction of 5S activities and how to proceed with continuous improvement
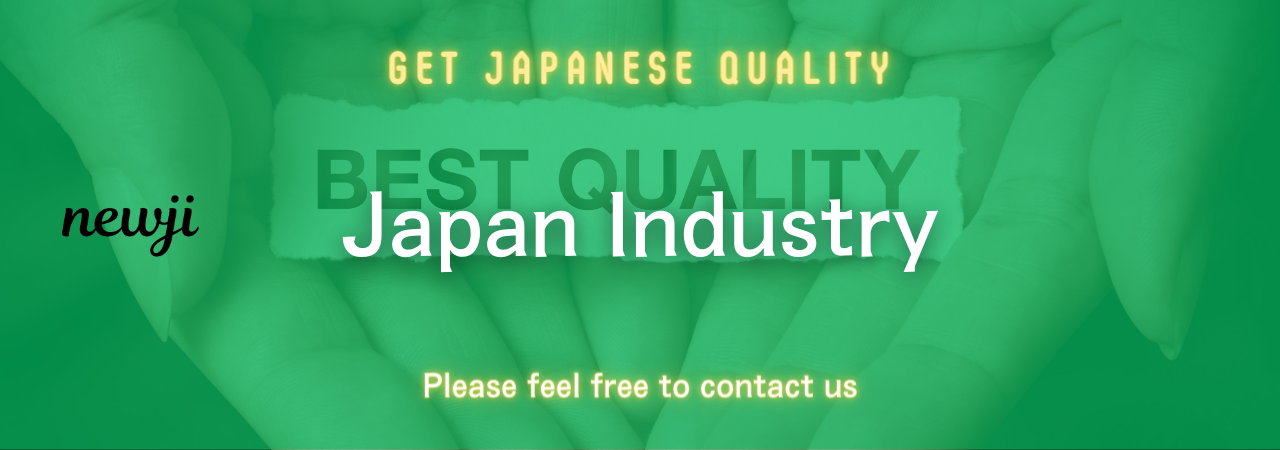
目次
Understanding 5S Activities in Factory Management
As a new manager in the factory management department, you’re about to embark on an exciting journey toward enhancing productivity and efficiency in your workplace.
One of the fundamental techniques to master is the concept of 5S activities.
These activities form the backbone of continuous improvement and are essential for maintaining a streamlined and effective work environment.
The 5S methodology consists of five Japanese words: Seiri, Seiton, Seiso, Seiketsu, and Shitsuke.
Translated to English, they mean Sort, Set in order, Shine, Standardize, and Sustain.
By understanding each of these components, you’ll gain valuable insights into how to implement and sustain a productive workspace.
Seiri (Sort)
The first step, Seiri or Sort, involves examining everything in the workplace and distinguishing between what is necessary and unnecessary.
This process is crucial for eliminating clutter and making room for what truly matters.
Begin by conducting a thorough assessment of all items, tools, and equipment in the factory.
Determine what’s essential for daily operations and remove any redundant or outdated materials.
This helps in reducing workplace accidents, saving space, and enhancing efficiency.
Seiton (Set in Order)
After sorting and decluttering, the next step is to Set in order, which means organizing necessary items for easy access and use.
This part of 5S focuses on ensuring that everything has a designated place, making sure tools and equipment are readily available when needed.
Implementing Seiton involves labeling, color-coding, and arranging items in a logical sequence.
This not only improves efficiency but also aids in reducing time wasted in searching for items.
Create visual cues or floor markings to indicate where each item belongs, so everyone knows where to find and return them.
Seiso (Shine)
Seiso, or Shine, emphasizes the importance of maintaining cleanliness and tidiness in the workplace.
A clean environment not only promotes safety but also boosts morale and productivity.
Encourage regular cleaning routines, ensuring that workspaces, tools, and equipment are in pristine condition.
Establish cleaning schedules and assign responsibilities to team members.
By making it a habitual routine, cleanliness becomes an integral part of daily operations, leading to a more professional and welcoming environment.
Seiketsu (Standardize)
Standardizing procedures and practices is the fourth step of 5S, known as Seiketsu.
The goal is to create uniformity and consistency across all processes, making it easier to maintain the newly organized state.
Develop standard operating procedures (SOPs) for tasks and cleaning routines.
Training employees on these standards is crucial, as it ensures everyone is on the same page.
Use visual aids like charts, diagrams, or digital tools to reinforce the standardized procedures, making adherence easier and more intuitive.
Shitsuke (Sustain)
The final step, Shitsuke or Sustain, focuses on maintaining and continuing the improvements made.
This step is essential for preventing a return to the previous state of disorganization.
Cultivate a culture that supports continuous improvement, encouraging employees to actively participate in maintaining the 5S activities.
Regular audits and reviews are necessary to ensure compliance and identify areas for further enhancement.
Recognizing and rewarding employees who contribute significantly to sustaining the 5S efforts can also foster motivation and long-term adherence.
The Benefits of 5S Activities
Implementing 5S activities in the factory management department offers numerous benefits that go beyond mere organization.
By creating a clean and orderly environment, these activities boost productivity, enhance safety, and improve employee morale.
Efficiency is increased as less time is spent on searching for items, and clearer workspaces make it easier to focus on tasks.
In addition, 5S activities contribute to cost savings.
With reduced waste, optimized use of space, and fewer errors, the operational costs of the factory decrease.
The streamlined processes and clear organization also support faster response times and adaptability to changes, making the factory more competitive in the market.
How to Proceed with Continuous Improvement
Continuous improvement is a critical aspect of maintaining the benefits achieved through 5S activities.
Here are a few steps to help you along the way:
Involve Employees
Engage employees at all levels in the continuous improvement process.
Their involvement and feedback can provide valuable insights into how processes can be further optimized.
Encourage open communication and create an environment where suggestions for improvements are welcomed and considered.
Set Clear Goals
Define clear, achievable goals for improvement that align with the company’s objectives.
These should include specific metrics to measure progress and success.
Regularly review and adjust these goals to ensure they remain relevant and challenging.
Provide Training and Resources
Ensure that employees have access to appropriate training and resources required to contribute effectively to continuous improvement efforts.
Keeping them up-to-date with industry trends and best practices also helps in sustaining the momentum of improvement.
Review and Reflect
Conduct periodic reviews of the 5S activities and overall performance.
Reflect on successes and areas needing improvement.
Utilize data and analytics to make informed decisions and further refine strategies.
Conclusion
As a new manager in the factory management department, implementing and working with 5S activities is a powerful way to drive productivity and efficiency.
By understanding and embracing each component of the 5S methodology, you set your team up for success and continuous improvement.
Remember to involve employees, set clear goals, provide necessary resources, and regularly review progress.
This will ensure a sustained culture of improvement in your factory, leading to better outcomes and a more engaging work environment.
資料ダウンロード
QCD調達購買管理クラウド「newji」は、調達購買部門で必要なQCD管理全てを備えた、現場特化型兼クラウド型の今世紀最高の購買管理システムとなります。
ユーザー登録
調達購買業務の効率化だけでなく、システムを導入することで、コスト削減や製品・資材のステータス可視化のほか、属人化していた購買情報の共有化による内部不正防止や統制にも役立ちます。
NEWJI DX
製造業に特化したデジタルトランスフォーメーション(DX)の実現を目指す請負開発型のコンサルティングサービスです。AI、iPaaS、および先端の技術を駆使して、製造プロセスの効率化、業務効率化、チームワーク強化、コスト削減、品質向上を実現します。このサービスは、製造業の課題を深く理解し、それに対する最適なデジタルソリューションを提供することで、企業が持続的な成長とイノベーションを達成できるようサポートします。
オンライン講座
製造業、主に購買・調達部門にお勤めの方々に向けた情報を配信しております。
新任の方やベテランの方、管理職を対象とした幅広いコンテンツをご用意しております。
お問い合わせ
コストダウンが利益に直結する術だと理解していても、なかなか前に進めることができない状況。そんな時は、newjiのコストダウン自動化機能で大きく利益貢献しよう!
(Β版非公開)