- お役立ち記事
- For operators in the glass product manufacturing industry! Fundamentals of raw material mixing and quality control on float glass production lines
月間76,176名の
製造業ご担当者様が閲覧しています*
*2025年3月31日現在のGoogle Analyticsのデータより
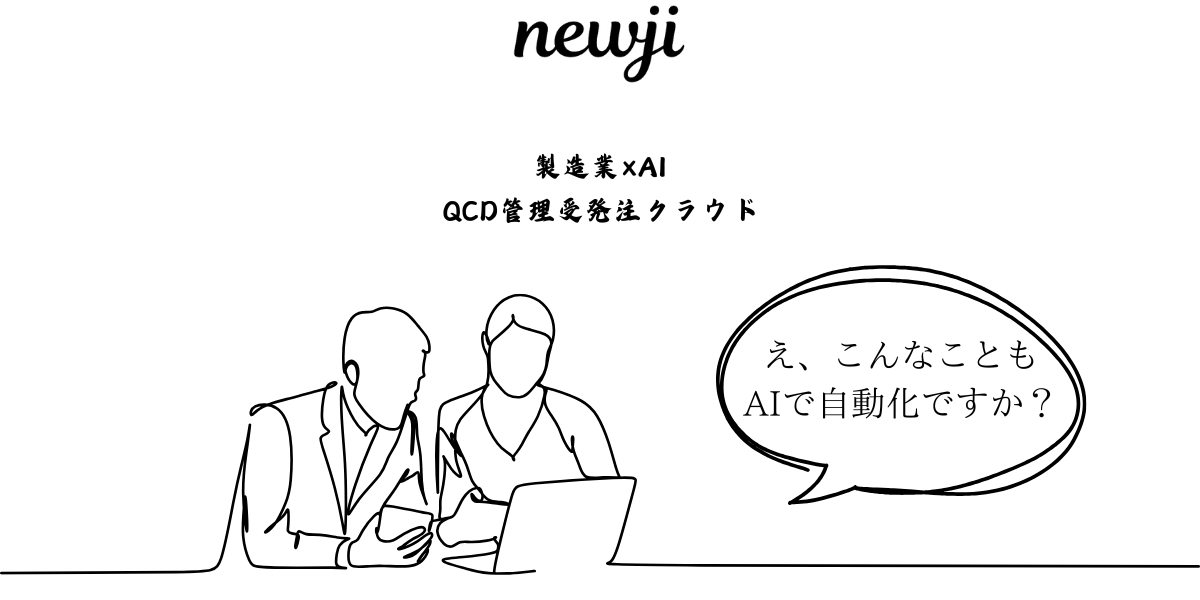
For operators in the glass product manufacturing industry! Fundamentals of raw material mixing and quality control on float glass production lines
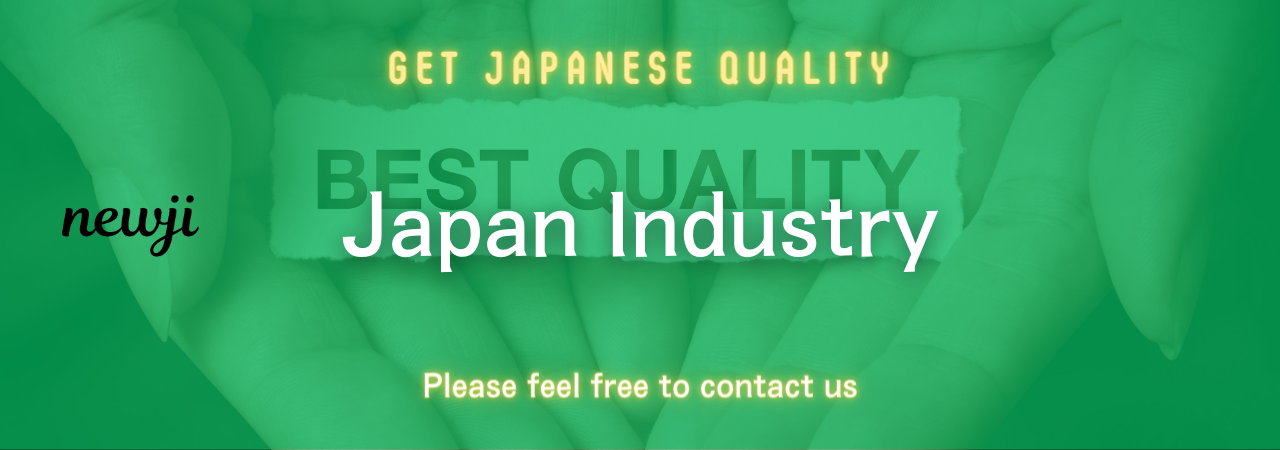
目次
Introduction to Float Glass Production
The glass manufacturing industry is a crucial component of modern construction, technology, and various other sectors.
Float glass, in particular, constitutes a significant portion of this industry due to its versatility and widespread applicability.
This article delves into the essentials of raw material mixing and quality control for float glass production, offering a clearer understanding for operators in this domain.
Understanding Float Glass
Float glass, known for its smooth and distortion-free surface, is created by floating molten glass on a bed of molten tin.
This process allows for uniform thickness and clarity, making it ideal for windows, mirrors, and glazing in buildings.
Key Components of Float Glass
The primary ingredients of float glass include silica sand, soda ash, limestone, and dolomite.
Each component plays a crucial role:
– Silica sand is the main ingredient, providing the necessary silicon dioxide required for glass formation.
– Soda ash reduces the melting point of sand, making it workable at lower temperatures.
– Limestone and dolomite introduce calcium and magnesium, helping to stabilize the glass structure.
The Importance of Raw Material Mixing
Ensuring the right mix of raw materials is critical in producing high-quality float glass.
The proportions and purity of these materials determine the quality and attributes of the final product.
Precision in Mixing
Accurate measurement and homogenization of raw materials are vital.
Careless mixing can lead to defects in the glass such as bubbles, striations, or improper thickness.
By using automated batching systems, manufacturers can ensure consistency in the mix, reducing the potential for human error.
Quality of Raw Materials
The purity of raw materials directly impacts the quality of the float glass.
Contaminants in silica, such as iron, can cause discoloration and affect transparency.
Thus, regular inspections and quality checks of raw materials are necessary to uphold production standards.
Quality Control on Float Glass Production Lines
Quality control is integral during every stage of float glass manufacturing to meet industry standards and ensure customer satisfaction.
Inspection and Monitoring
Continuous monitoring of the production process is essential.
Operators should oversee the melting, forming, annealing, and cutting stages to detect and correct any abnormalities.
Advanced technologies such as infrared cameras and sensors can aid in monitoring the furnace temperature and the molten glass surface.
Defect Detection
Defects such as inclusions, surface scratches, or tint variations need to be identified and addressed promptly.
Non-destructive testing methods, like ultrasonic and optical scanners, assist in detecting imperfections without damaging the glass.
Consistency in Thickness
Maintaining a consistent thickness is crucial for not only aesthetic but also functional reasons, particularly when it comes to safety and structural integrity.
Laser measuring tools and automated cutters help achieve precise thickness throughout the entire float glass sheet.
The Role of Skilled Operators
The expertise of personnel in the production line cannot be overstated.
Operators must be adept in both the technology and the manual oversight required in float glass manufacturing.
Ongoing Training and Skill Development
Continuous training programs are necessary for operators to stay updated with the latest technologies and methodologies.
These training sessions should cover both theoretical and practical aspects, ensuring that operators can efficiently handle equipment and troubleshoot issues.
Team Collaboration
A well-coordinated team enhances the production flow and quality control.
Operators need to communicate effectively with each other and with other departments, such as maintenance and logistics, to ensure seamless operations.
Advancements in Float Glass Technology
The float glass industry constantly evolves with advancements in technology aiming to enhance efficiency and product quality.
Sustainable Practices
Incorporating eco-friendly practices, such as recycling cullet (rejected glass waste), reduces the environmental impact and raw material costs.
This not only benefits the environment but also improves operational efficiency and profitability.
Automation and Digitalization
The integration of automation in production processes increases precision, reduces human error, and improves safety.
Digital platforms for monitoring and controlling production ensure better data management and decision-making.
Conclusion
Producing float glass involves meticulous attention to raw material mixing and stringent quality control measures.
For operators in the glass manufacturing industry, understanding these fundamentals helps in maintaining high standards of production and meeting market demands.
With ongoing training, skill enhancement, and embracing new technologies, the industry can continue to innovate and produce superior quality glass products.
資料ダウンロード
QCD管理受発注クラウド「newji」は、受発注部門で必要なQCD管理全てを備えた、現場特化型兼クラウド型の今世紀最高の受発注管理システムとなります。
ユーザー登録
受発注業務の効率化だけでなく、システムを導入することで、コスト削減や製品・資材のステータス可視化のほか、属人化していた受発注情報の共有化による内部不正防止や統制にも役立ちます。
NEWJI DX
製造業に特化したデジタルトランスフォーメーション(DX)の実現を目指す請負開発型のコンサルティングサービスです。AI、iPaaS、および先端の技術を駆使して、製造プロセスの効率化、業務効率化、チームワーク強化、コスト削減、品質向上を実現します。このサービスは、製造業の課題を深く理解し、それに対する最適なデジタルソリューションを提供することで、企業が持続的な成長とイノベーションを達成できるようサポートします。
製造業ニュース解説
製造業、主に購買・調達部門にお勤めの方々に向けた情報を配信しております。
新任の方やベテランの方、管理職を対象とした幅広いコンテンツをご用意しております。
お問い合わせ
コストダウンが利益に直結する術だと理解していても、なかなか前に進めることができない状況。そんな時は、newjiのコストダウン自動化機能で大きく利益貢献しよう!
(β版非公開)