- お役立ち記事
- For operators in the precision machinery industry! Key points for gear cutting of helical gears and maintaining accuracy
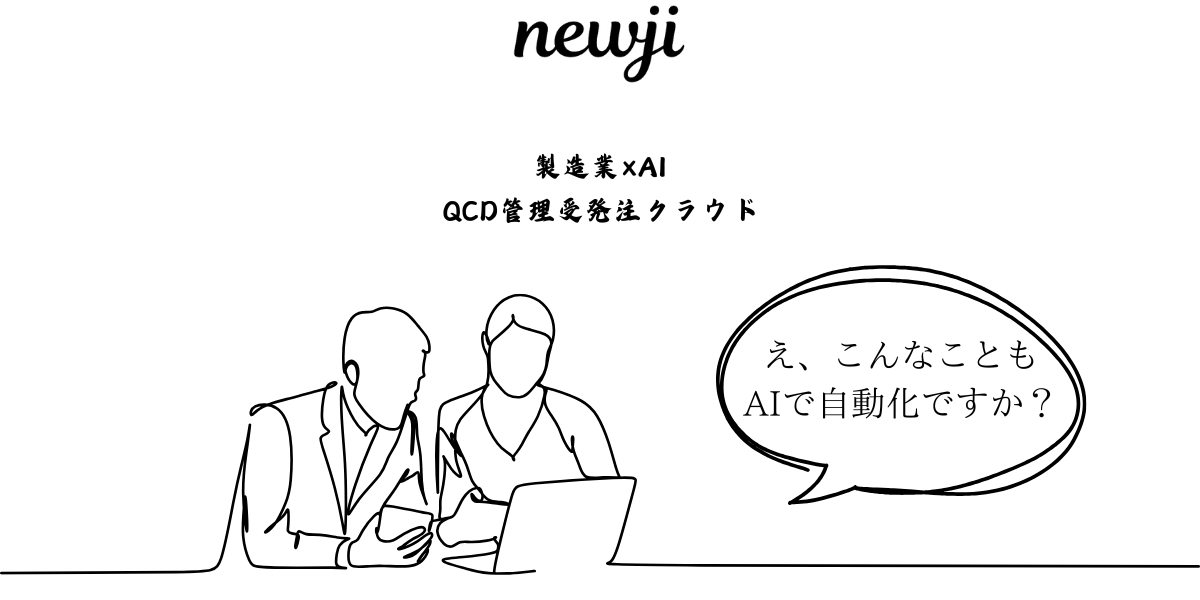
For operators in the precision machinery industry! Key points for gear cutting of helical gears and maintaining accuracy
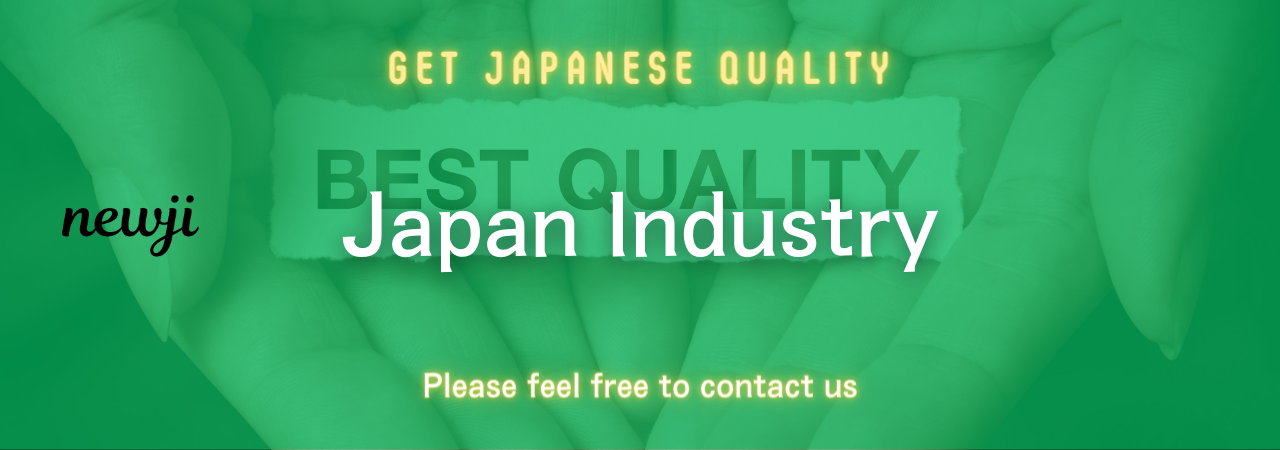
Understanding Helical Gears
Helical gears are a type of gear whose teeth are set at an angle relative to the axis of rotation.
Unlike spur gears, which have straight teeth, the angled teeth of helical gears engage more gradually, ensuring smoother and quieter operation.
This characteristic often makes helical gears preferable in applications where noise and efficiency are critical factors.
Helical gears are commonly used in automotive transmissions, elevators, and conveyor systems due to their ability to handle higher loads and operate at higher speeds than spur gears.
Their design allows for more teeth to be in contact during rotation, distributing the load more evenly across each gear tooth.
However, this also introduces complexities during the manufacturing process.
The Importance of Precision in Gear Cutting
Precision is critical in the gear cutting process, particularly for helical gears.
The complexity of the angled teeth means deviations or errors can lead to increased wear and tear, noise, and even mechanical failure.
For this reason, maintaining high precision and accuracy throughout the manufacturing process is essential to ensure optimal gear performance.
Precision in gear cutting starts from the material selection, machine settings, right down to the tools used.
These factors collectively influence the final product’s dimensional accuracy and surface finish.
As an operator, understanding these nuances helps in minimizing errors and improving the quality of the gears produced.
Key Points for Gear Cutting
Here are several key points to ensure successful gear cutting of helical gears:
Selecting the Right Material
The choice of material impacts everything from the durability of the gear to the precision during cutting.
Common materials for helical gears include steel, brass, bronze, and plastics.
Each material has distinct properties that affect the gear’s performance and lifespan.
Ensuring high-quality and consistent material is foundational for precision gear cutting.
Correct Machine Setup
Accurate machine setup is crucial.
This involves configuring the machine parameters based on the gear specifications such as helix angle, module, and face width.
Operators should ensure the machine is well-maintained and calibrate tools before use.
This minimizes potential errors arising due to machine faults.
Tool Selection and Maintenance
Choosing the right cutting tools is integral to the quality of the helical gear.
The tools need to be sharp and made from materials suited to the gear material.
Regular maintenance and inspections of the tools are necessary to maintain their performance.
Worn or damaged tools can result in poor quality cuts, leading to inaccuracies in gear production.
Monitoring and Quality Control
Continuous monitoring during the gear cutting process helps in early detection of deviations.
Using advanced measurement tools and techniques provides real-time data for operators to make informed adjustments.
Additionally, implementing a robust quality control process ensures that each gear meets the required specifications.
Inspections using coordinate measuring machines (CMM) or gear measuring instruments guarantee the accuracy of the gear dimensions and tooth profiles.
Maintaining Accuracy in Helical Gear Production
Accuracy is maintained through a combination of technology, skilled operators, and quality materials.
Here are some strategies to enhance accuracy in production:
Investing in Technology
Advanced CNC machining centers are often used in helical gear production due to their precision and versatility.
Digitally controlled machines can execute complex cuts with high accuracy.
Investing in such technologies, although costly, is beneficial in the long run for producing high-quality gears.
Training and Skill Development
Well-trained operators are invaluable in ensuring precision.
Continual training programs and workshops help operators stay updated with the latest techniques and technologies in gear cutting.
A skilled workforce is adept at troubleshooting and can make quick adjustments to maintain production accuracy.
Implementing Comprehensive Checks
Regular checks and balancing procedures must be in place to maintain accuracy.
This involves periodically recalibrating machines and tools and conducting random inspections throughout the manufacturing batches.
Using statistical process control (SPC) for monitoring key variables ensures the process remains within the defined control limits.
Conclusion
In the precision machinery industry, the production of helical gears requires careful adherence to process parameters to maintain accuracy.
Understanding the inherent complexities of helical gears, combined with selecting the right materials, tools, and adopting technology advances, forms the bedrock of creating high-quality products.
By focusing on these key areas, operators can significantly improve the performance and longevity of helical gears, ensuring they meet the rigorous demands of modern applications.
資料ダウンロード
QCD調達購買管理クラウド「newji」は、調達購買部門で必要なQCD管理全てを備えた、現場特化型兼クラウド型の今世紀最高の購買管理システムとなります。
ユーザー登録
調達購買業務の効率化だけでなく、システムを導入することで、コスト削減や製品・資材のステータス可視化のほか、属人化していた購買情報の共有化による内部不正防止や統制にも役立ちます。
NEWJI DX
製造業に特化したデジタルトランスフォーメーション(DX)の実現を目指す請負開発型のコンサルティングサービスです。AI、iPaaS、および先端の技術を駆使して、製造プロセスの効率化、業務効率化、チームワーク強化、コスト削減、品質向上を実現します。このサービスは、製造業の課題を深く理解し、それに対する最適なデジタルソリューションを提供することで、企業が持続的な成長とイノベーションを達成できるようサポートします。
オンライン講座
製造業、主に購買・調達部門にお勤めの方々に向けた情報を配信しております。
新任の方やベテランの方、管理職を対象とした幅広いコンテンツをご用意しております。
お問い合わせ
コストダウンが利益に直結する術だと理解していても、なかなか前に進めることができない状況。そんな時は、newjiのコストダウン自動化機能で大きく利益貢献しよう!
(Β版非公開)