- お役立ち記事
- For process engineers in the semiconductor manufacturing industry! Optimization of CMP (Chemical Mechanical Polishing) slurry management and process control
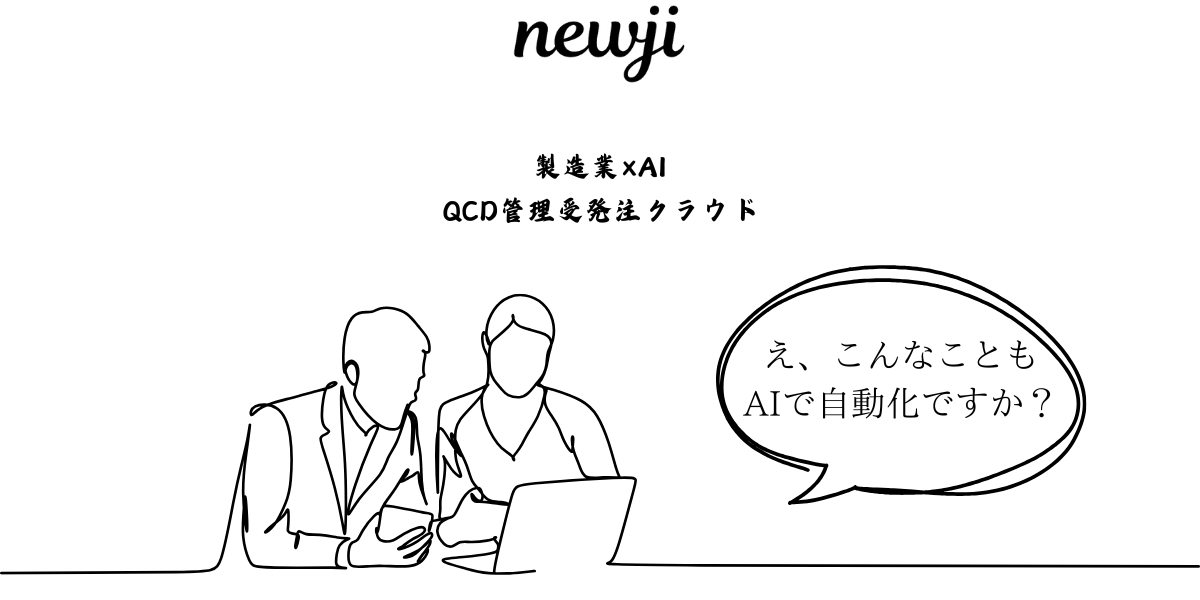
For process engineers in the semiconductor manufacturing industry! Optimization of CMP (Chemical Mechanical Polishing) slurry management and process control
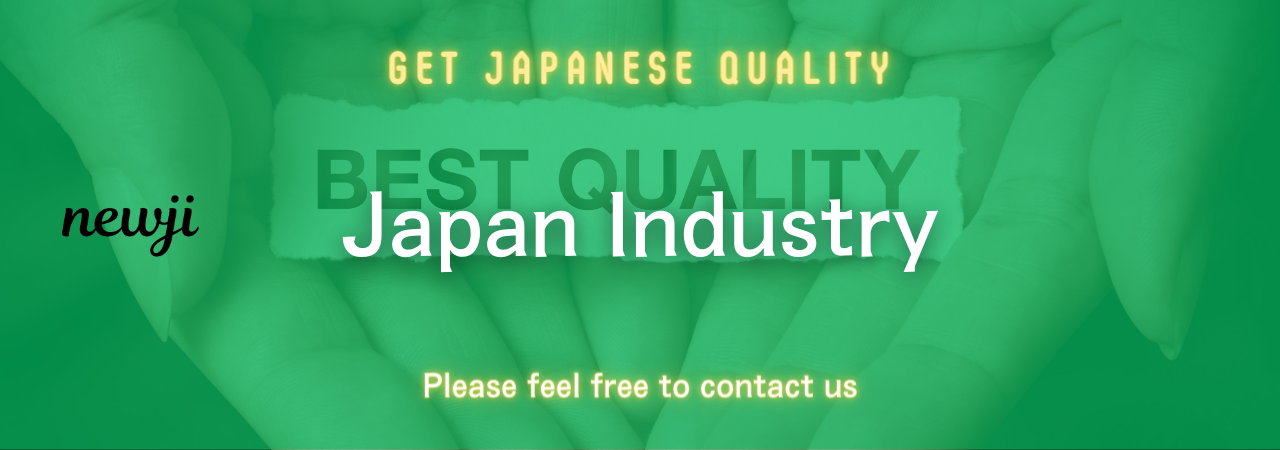
目次
Understanding Chemical Mechanical Polishing (CMP)
Chemical Mechanical Polishing, commonly known as CMP, is an essential process in the semiconductor manufacturing industry.
It is primarily used to achieve a smooth and level surface on semiconductor wafers, which is crucial for further processing steps.
CMP combines chemical and mechanical forces to remove material from the surface of a wafer.
The process involves the use of a slurry, which contains abrasive particles and reactive chemicals, and a polishing pad.
As the wafer makes contact with the rotating pad, the slurry facilitates the removal of unwanted material, resulting in a polished surface.
The Role of CMP Slurry in Semiconductor Manufacturing
The slurry used in CMP is pivotal to the process’s success.
It influences both the rate of material removal and the quality of the polished surface.
Slurries are carefully formulated to optimize the balance between chemical and mechanical actions during polishing.
The abrasive particles help physically remove material, while the chemicals in the slurry react with the wafer surface to aid in material breakdown.
Managing the slurry composition and application is crucial for maintaining consistent wafer quality and process repeatability.
Components of CMP Slurry
CMP slurries consist of several key components:
1. **Abrasive Particles:** These are typically made of materials like silica or alumina, providing the mechanical action needed for material removal.
2. **Chemical Agents:** These can include oxidizers, pH adjusters, or corrosion inhibitors, each playing a specific role in the chemical aspect of the process.
3. **Counter-ions:** Added to maintain the stability of the slurry.
4. **Deionized Water:** Serves as the carrier fluid for these components, ensuring even distribution across the wafer surface.
Challenges in CMP Slurry Management
Effective slurry management is vital for ensuring the reliability and efficiency of the CMP process.
Several challenges can arise, affecting both performance and cost:
– **Slurry Delivery Consistency:** Ensuring a consistent supply of slurry to the polishing pad is essential.
Any interruptions can lead to defects or uneven polishing.
– **Slurry Degradation:** Over time, the chemical agents in the slurry can degrade, impacting the slurry’s effectiveness.
Regular monitoring and replenishment are required to maintain the desired properties.
– **Waste Management:** Slurry waste must be disposed of properly to minimize environmental impact and comply with regulations.
– **Particle Agglomeration:** If not controlled, abrasive particles can clump together, leading to imperfections on the wafer surface.
Optimizing CMP Process Control
Process control is a critical aspect of optimizing CMP operations.
Several methods and technologies can be employed to improve efficiency and output quality:
Real-Time Monitoring
Implementing real-time monitoring systems allows process engineers to track key parameters during CMP operations.
Sensors and data analytics can provide insights into slurry flow rates, pad pressure, and surface quality, enabling quick adjustments to maintain optimal conditions.
Automating Process Adjustments
Automation plays a significant role in enhancing CMP process control.
Advanced control systems can automatically adjust variables such as slurry dispense rate or polishing pad speed based on real-time data.
This reduces the chances of human error and improves overall process reliability.
Regular Maintenance and Pad Conditioning
Ensuring the polishing pad is regularly conditioned helps maintain its effectiveness.
Pad conditioning involves roughening the pad surface to retain its abrasive properties, ensuring consistent wafer contact and slurry distribution.
Use of Advanced Materials
Exploring new materials for both abrasive particles and chemical agents can lead to improvements in the CMP process.
For instance, using nanoparticles in the slurry can offer better control over surface finish and material removal rates.
Benefits of Optimized CMP Slurry Management and Process Control
Implementing effective slurry management and improving process control in CMP offers several benefits to semiconductor manufacturers:
– **Improved Wafer Quality:** Enhanced control over the polishing process results in smoother, defect-free surfaces, which is crucial for subsequent manufacturing steps.
– **Cost Savings:** Optimizing slurry usage reduces waste and consumption, lowering operational costs.
– **Increased Throughput:** Automated and well-managed processes lead to faster cycle times, boosting production rates.
– **Sustainability:** Efficient slurry management minimizes environmental impact through reduced chemical usage and improved waste handling.
Conclusion
Optimizing CMP slurry management and process control is essential for the semiconductor manufacturing industry to maintain high-quality standards and remain competitive.
By employing advanced monitoring, automation, and material innovations, manufacturers can enhance their processes, resulting in better yield, cost efficiency, and sustainability.
As technology continues to evolve, the ongoing improvement of CMP processes will play a critical role in supporting the growing demands of the semiconductor market.
資料ダウンロード
QCD調達購買管理クラウド「newji」は、調達購買部門で必要なQCD管理全てを備えた、現場特化型兼クラウド型の今世紀最高の購買管理システムとなります。
ユーザー登録
調達購買業務の効率化だけでなく、システムを導入することで、コスト削減や製品・資材のステータス可視化のほか、属人化していた購買情報の共有化による内部不正防止や統制にも役立ちます。
NEWJI DX
製造業に特化したデジタルトランスフォーメーション(DX)の実現を目指す請負開発型のコンサルティングサービスです。AI、iPaaS、および先端の技術を駆使して、製造プロセスの効率化、業務効率化、チームワーク強化、コスト削減、品質向上を実現します。このサービスは、製造業の課題を深く理解し、それに対する最適なデジタルソリューションを提供することで、企業が持続的な成長とイノベーションを達成できるようサポートします。
オンライン講座
製造業、主に購買・調達部門にお勤めの方々に向けた情報を配信しております。
新任の方やベテランの方、管理職を対象とした幅広いコンテンツをご用意しております。
お問い合わせ
コストダウンが利益に直結する術だと理解していても、なかなか前に進めることができない状況。そんな時は、newjiのコストダウン自動化機能で大きく利益貢献しよう!
(Β版非公開)