- お役立ち記事
- For processing engineers in the steel industry! How to minimize the thermal effects of plasma cutting
For processing engineers in the steel industry! How to minimize the thermal effects of plasma cutting
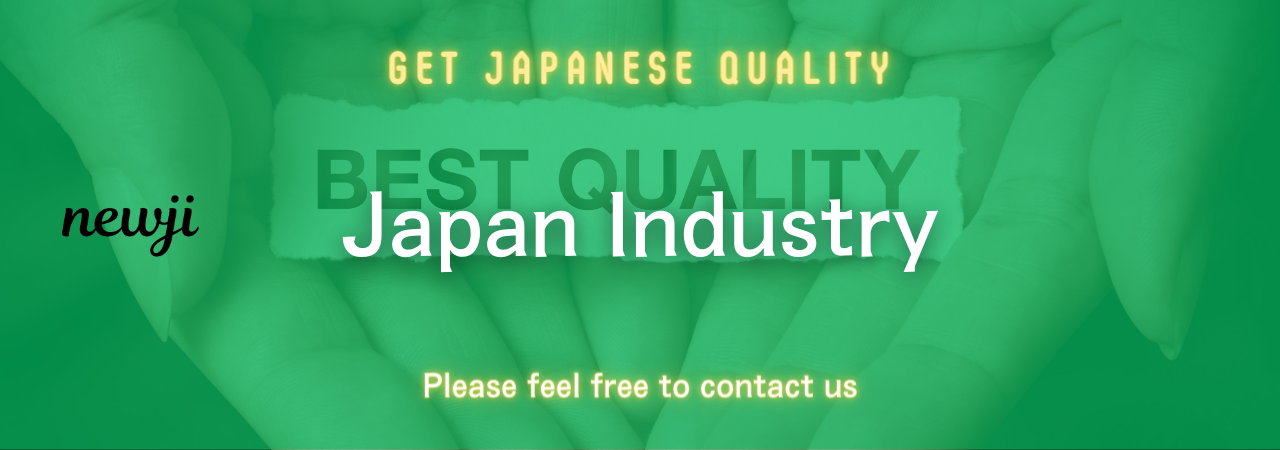
目次
Understanding Plasma Cutting and Its Thermal Effects
Plasma cutting is a widely used method in the steel industry, known for its ability to slice through metal with precision and speed.
This technique utilizes a high-velocity jet of ionized gas, or plasma, to melt and expel material from the cut area.
As efficient as it is, plasma cutting invariably introduces thermal effects on the steel being processed.
The thermal input can alter the physical and mechanical properties of the material, potentially leading to issues like warping, distortion, or changes in microstructure.
For processing engineers, managing these thermal effects is crucial to maintaining the integrity of the material.
Key Factors Influencing Thermal Effects
Several factors determine the extent of thermal impact during plasma cutting.
Understanding these can help engineers minimize unwanted effects.
1. Cutting Speed
Cutting speed significantly influences the thermal impact of plasma cutting.
Faster cutting speeds often result in less heat input per unit area, reducing the potential for heat-affected zone (HAZ) distortion.
Finding the optimal speed that balances efficiency and quality can minimize thermal effects.
2. Amperage and Voltage Settings
The amperage and voltage settings of the plasma cutter play a critical role in heat input.
Higher settings generate more heat, which can increase the size of the HAZ and affect the mechanical properties of the cut edge.
Using the lowest amperage and voltage settings suitable for the material thickness helps manage thermal effects.
3. Thickness of Material
The thickness of the steel being cut is another important factor.
Thicker materials tend to absorb more heat, which can amplify thermal effects.
Engineers should adjust cutting parameters based on material thickness to mitigate these effects.
Ways to Minimize Thermal Effects
Processing engineers can implement various strategies to minimize thermal effects during plasma cutting.
These methods help preserve the material properties and ensure high-quality cuts.
1. Optimize Cutting Parameters
Fine-tuning cutting parameters, such as speed, amperage, and voltage, is essential.
Engineers should experiment with different settings to identify the optimal combination that produces clean cuts with minimal thermal distortion.
Using modern plasma cutters with automated adjustment features can also help maintain consistent quality.
2. Use of Water Table
Incorporating a water table into the cutting process is an effective way to control thermal effects.
By submerging or applying water mist to the cutting area, the excess heat is absorbed, reducing the HAZ.
This method not only cools the material quickly but also minimizes smoke and debris.
3. Preheating
Preheating the steel before cutting can help reduce thermal shock and distortion.
By raising the material’s temperature close to its cutting temperature, the differential between heated and non-heated zones is minimized.
This technique is particularly useful for thicker sections of steel.
4. Post-Cut Heat Treatment
In some cases, post-cut heat treatment can rectify the thermal effects on steel.
Normalizing or annealing the material after cutting can restore its original mechanical properties and relieve residual stresses.
Engineers should consider this approach when precision and structural integrity are paramount.
Advanced Technologies and Techniques
The steel industry continuously evolves to incorporate advanced technologies that help mitigate thermal effects.
1. Computer Numerical Control (CNC) Systems
The integration of CNC systems in plasma cutting machines allows for greater precision and control over cutting processes.
CNC systems can automatically adjust cutting parameters in real-time to optimize performance and reduce thermal effects.
2. High-Definition Plasma Cutting
High-definition plasma cutting offers better accuracy and quality compared to conventional methods.
This technology utilizes narrow plasma arcs that focus heat more precisely, resulting in smaller HAZ and less thermal impact.
3. Laser-Assisted Plasma Cutting
Combining laser technology with plasma cutting can further enhance cutting precision and reduce thermal effects.
The laser preheats the steel, allowing for smoother cuts with minimal input of plasma heat energy.
Conclusion
In the steel industry, minimizing the thermal effects of plasma cutting is crucial for ensuring quality and maintaining structural integrity.
By understanding the factors that influence heat input and implementing strategies to control them, processing engineers can achieve more efficient and precise cuts.
From optimizing cutting parameters to utilizing advanced technologies, the methods discussed provide valuable insights into reducing the negative impact of thermal effects.
Continued innovation and adaptation in plasma cutting processes will undoubtedly drive improvements in the steel industry, enhancing both performance and sustainability.
資料ダウンロード
QCD調達購買管理クラウド「newji」は、調達購買部門で必要なQCD管理全てを備えた、現場特化型兼クラウド型の今世紀最高の購買管理システムとなります。
ユーザー登録
調達購買業務の効率化だけでなく、システムを導入することで、コスト削減や製品・資材のステータス可視化のほか、属人化していた購買情報の共有化による内部不正防止や統制にも役立ちます。
NEWJI DX
製造業に特化したデジタルトランスフォーメーション(DX)の実現を目指す請負開発型のコンサルティングサービスです。AI、iPaaS、および先端の技術を駆使して、製造プロセスの効率化、業務効率化、チームワーク強化、コスト削減、品質向上を実現します。このサービスは、製造業の課題を深く理解し、それに対する最適なデジタルソリューションを提供することで、企業が持続的な成長とイノベーションを達成できるようサポートします。
オンライン講座
製造業、主に購買・調達部門にお勤めの方々に向けた情報を配信しております。
新任の方やベテランの方、管理職を対象とした幅広いコンテンツをご用意しております。
お問い合わせ
コストダウンが利益に直結する術だと理解していても、なかなか前に進めることができない状況。そんな時は、newjiのコストダウン自動化機能で大きく利益貢献しよう!
(Β版非公開)