- お役立ち記事
- For processing engineers in the steel industry! Key points for thermal control and optimization of hot stamping
For processing engineers in the steel industry! Key points for thermal control and optimization of hot stamping
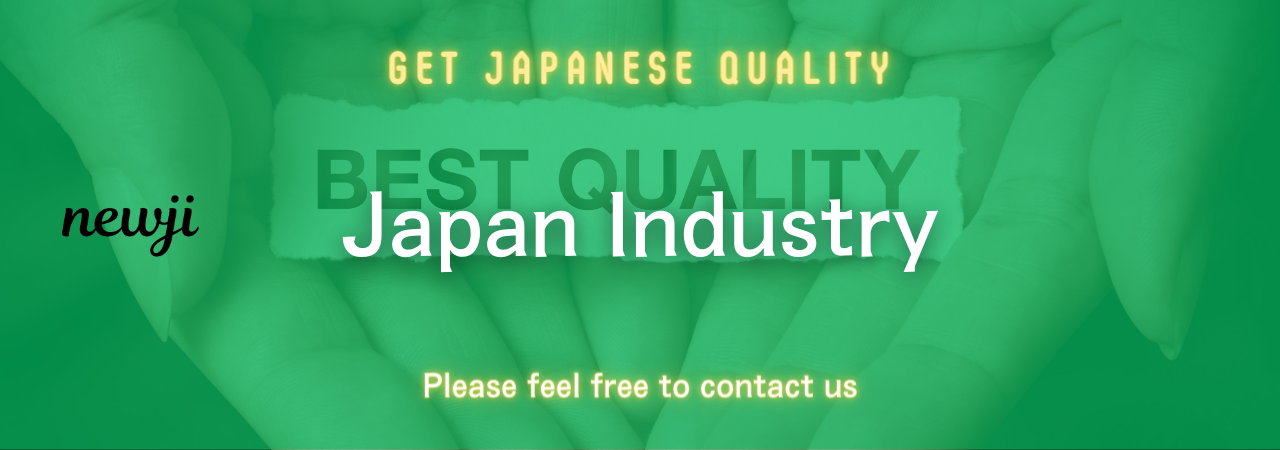
目次
Understanding Thermal Control in Hot Stamping
Thermal control in hot stamping is a crucial aspect for processing engineers in the steel industry.
In this process, achieving precise temperature management is vital to ensure the quality and efficiency of the final product.
Hot stamping involves heating steel to a high temperature before forming it into the desired shape.
This procedure not only shapes the steel but also enhances its structural properties, making it an essential technique in automotive and other industries where strength and lightness are required.
The process begins by heating the steel blanks to a temperature between 900°C and 950°C.
The heating must be uniform across the entire piece to avoid any inconsistencies in the material’s properties.
Once heated, the blank is transferred to a die for shaping and then rapidly cooled.
This rapid cooling is known as quenching and it is instrumental in giving the final part its desired hardness and strength.
The Importance of Temperature Uniformity
In hot stamping, temperature uniformity is the cornerstone of success.
If the steel does not heat evenly, sections of the blank may not achieve the necessary transformation, leading to weak points in the final product.
This uniformity is achieved through specific heating techniques and equipment that ensure all parts of the blank reach the desired temperature simultaneously.
Furthermore, monitoring the cooling process is just as critical.
During quenching, the steel must cool down rapidly to lock in the structure that provides enhanced properties.
Any variation in this phase can lead to different transformation phases in the steel, which might compromise its strength and durability.
Optimization of Heating and Cooling Processes
To optimize the hot stamping process, engineers must consider both the heating and cooling stages.
Efficient design of the furnace and precise control of temperature and timing are vital components of optimization.
Temperature control systems, such as infrared thermometers and thermocouples, can help monitor and adjust the temperature throughout the process.
In terms of cooling, innovative techniques like tailored tempering can be employed.
This involves cooling different parts of the steel at varied rates to produce parts with different mechanical properties in one piece.
Such methods can significantly enhance the performance characteristics of stamped parts for specific applications.
Significance of Material Properties in Hot Stamping
The choice of material is another critical factor in the hot stamping process.
Various steels have different thermal properties and response to both heating and cooling.
High-strength steels, commonly used in automotive applications, are ideal candidates for hot stamping.
Their superior properties, such as ductility and strength after transformation, make them perfect for components that require both durability and reduction in weight.
Therefore, understanding the specific attributes of the steel being used is essential for achieving optimal results.
Advanced Technologies in Thermal Control
Advanced technologies play a pivotal role in enhancing thermal control in hot stamping.
Laser-assisted heating and induction heating are emerging methods offering precise and rapid heating capabilities.
Laser-assisted heating, for instance, provides localized heating control that can achieve complex geometries.
Induction heating offers fast, energy-efficient, and uniform heating, reducing the risk of oxidation that can occur with conventional methods.
These technologies not only improve thermal control but also pave the way for more innovative designs and applications.
Integrating Simulation and Modeling
With the advent of digital tools, simulation and modeling have become indispensable in optimizing hot stamping processes.
Simulation software can predict how the material will behave under certain conditions, allowing engineers to tweak the process parameters before actual production.
This integration helps in anticipating potential issues, ensuring temperature uniformity, and achieving the desired mechanical properties of the final part.
By employing simulation and modeling, processing engineers can drastically reduce trial and error, saving both time and resources.
Challenges and Solutions in Thermal Optimization
While hot stamping offers many benefits, it is not without its challenges.
Warpage, springback, and insufficient hardness are common issues arising from poor thermal control.
Ensuring uniform temperature distribution and precise control of the cooling rate can mitigate these problems.
Using state-of-the-art sensors and control systems, combined with robust simulation tools, can help overcome these challenges.
Moreover, continuous research and development are crucial in finding new methods and materials to enhance the hot stamping process further.
Future Prospects of Hot Stamping in the Steel Industry
Looking ahead, the steel industry continues to explore the potential of hot stamping as an innovative forming technology.
Advancements in thermal imaging, process automation, and material science promise to drive efficiency and quality improvements.
Furthermore, the push towards greener manufacturing processes may result in the development of more energy-efficient heating methods, and sustainable materials designed specifically for hot stamping.
These innovations are set to expand the application of hot stamping beyond its current uses, contributing significantly to the evolution of the steel industry.
To conclude, thermal control and optimization in hot stamping are critical for processing engineers aiming to maximize product performance and efficiency.
By mastering the fundamentals of temperature management, leveraging advanced technologies, and integrating predictive tools into their processes, engineers can unlock new potentials in high-strength steel applications.
These efforts ensure that hot stamping remains an indispensable part of modern manufacturing technologies in the steel industry.
資料ダウンロード
QCD調達購買管理クラウド「newji」は、調達購買部門で必要なQCD管理全てを備えた、現場特化型兼クラウド型の今世紀最高の購買管理システムとなります。
ユーザー登録
調達購買業務の効率化だけでなく、システムを導入することで、コスト削減や製品・資材のステータス可視化のほか、属人化していた購買情報の共有化による内部不正防止や統制にも役立ちます。
NEWJI DX
製造業に特化したデジタルトランスフォーメーション(DX)の実現を目指す請負開発型のコンサルティングサービスです。AI、iPaaS、および先端の技術を駆使して、製造プロセスの効率化、業務効率化、チームワーク強化、コスト削減、品質向上を実現します。このサービスは、製造業の課題を深く理解し、それに対する最適なデジタルソリューションを提供することで、企業が持続的な成長とイノベーションを達成できるようサポートします。
オンライン講座
製造業、主に購買・調達部門にお勤めの方々に向けた情報を配信しております。
新任の方やベテランの方、管理職を対象とした幅広いコンテンツをご用意しております。
お問い合わせ
コストダウンが利益に直結する術だと理解していても、なかなか前に進めることができない状況。そんな時は、newjiのコストダウン自動化機能で大きく利益貢献しよう!
(Β版非公開)