- お役立ち記事
- For product design departments! Innovative design process improvement method using 7 new QC tools
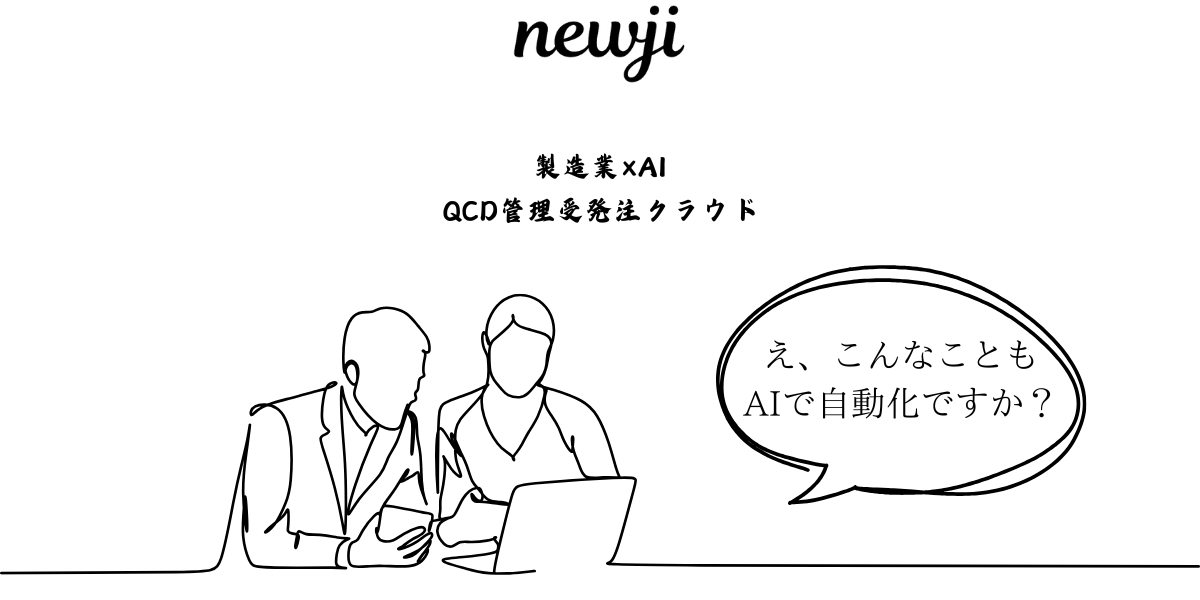
For product design departments! Innovative design process improvement method using 7 new QC tools
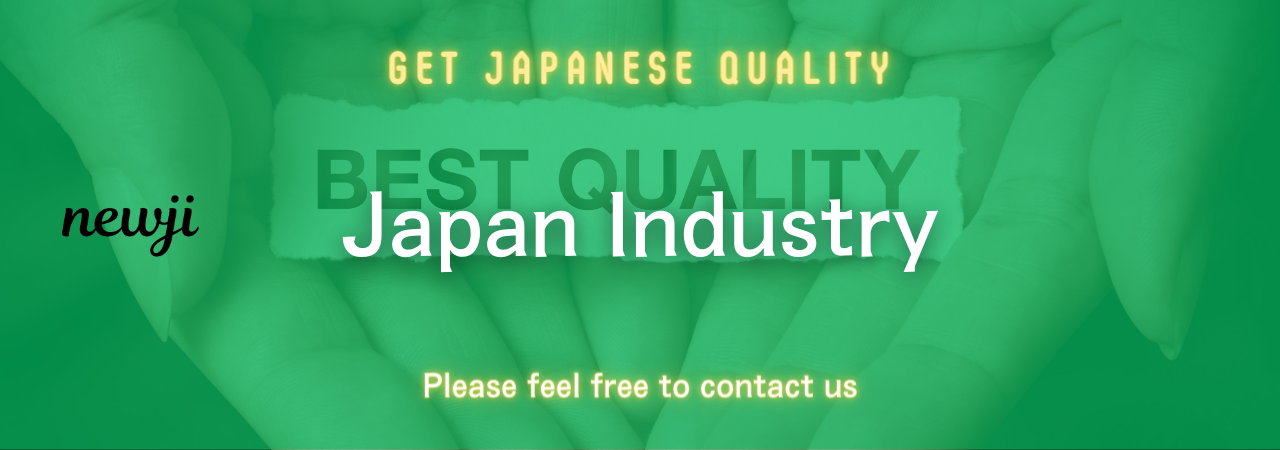
As organizations strive to lead in innovation, their product design departments must continuously improve processes to maintain a competitive edge.
One way to achieve this is by incorporating innovative methods for problem-solving and decision-making.
An effective approach involves the use of the seven new Quality Control (QC) tools, which provide product design teams with structured methods to enhance creativity and efficiency.
These tools offer fresh perspectives on how to solve design challenges, streamline workflows, and deliver superior products.
目次
Introduction to the 7 New QC Tools
Before delving into the process of improvement, it’s essential to understand what the seven new QC tools are.
These tools were introduced as a response to the increasing complexity of modern engineering and manufacturing environments.
Their goal is to improve quality through better formulation, analysis, and solution of issues.
The seven tools are:
1. Affinity Diagram
2. Interrelationship Diagram
3. Tree Diagram
4. Matrix Diagram
5. Prioritization Matrix
6. Process Decision Program Chart (PDPC)
7. Activity Network Diagram
Each tool serves a unique purpose, yet they share the common goal of refining process efficiency and encouraging innovative problem-solving.
Affinity Diagram: Organizing Ideas for Innovation
The Affinity Diagram is particularly useful during the brainstorming phase of product design.
When faced with a large set of data or ideas, this tool helps design teams to organize information into meaningful patterns.
This is achieved by grouping ideas based on natural relationships, which reveals previously unseen connections and fosters creative solutions.
Using an Affinity Diagram can streamline the initial idea-generation process, making it easier to identify the most promising concepts for further development.
Interrelationship Diagram: Understanding Cause and Effect
Complex problems often have multiple interrelated causes.
The Interrelationship Diagram enables teams to visualize these relationships, helping them to understand the influence of each factor on others.
This understanding is crucial in identifying root causes of design challenges and in prioritizing which issues to address first.
By mapping out these relationships, design teams can unravel complexity and develop more effective solutions.
Tree Diagram: Breaking Down Goals
When embarking on a new project, it’s vital to clearly define goals and the steps needed to achieve them.
The Tree Diagram is a structured way to decompose objectives into their constituent components, creating a clear path from goal to task.
For design departments, this ensures that all team members understand the overall objectives and their individual roles in achieving them.
It also helps manage resources efficiently, as it clarifies which tasks are most critical to the project’s success.
Matrix Diagram: Clarifying Relationships Between Elements
The Matrix Diagram assists in exploring and illustrating complex relationships between various elements within a design project.
By establishing a visual matrix, teams can discern connections and dependencies between tasks, objectives, or departments.
This clarity helps in resource allocation, ensuring that critical links are supported and potential conflicts are managed efficiently.
Incorporating this tool into the design process can lead to more effective collaboration and smoother project progression.
Prioritization Matrix: Managing Choices
Decisions in the design process often involve selecting the most beneficial options among many possibilities.
The Prioritization Matrix aids in this by providing a systematic approach to evaluating and ranking alternatives based on pre-defined criteria.
This helps design teams focus their efforts on the most impactful tasks, ensuring that resources are allocated to activities that will yield the greatest benefits.
Employing this tool minimizes the risk of pursuing low-value options and helps maintain focus on strategic objectives.
Process Decision Program Chart (PDPC): Preparing for Uncertainties
Designing innovative products frequently involves navigating uncertainty.
The PDPC helps teams anticipate potential problems and prepare contingency plans.
By mapping out sequences of actions and identifying possible obstacles, this tool enables preemptive planning to address unforeseen challenges.
Incorporating PDPC into the design process means that risks can be mitigated more effectively, reducing the likelihood of projects being derailed by unexpected issues.
Activity Network Diagram: Planning and Scheduling
The Activity Network Diagram is used for planning and scheduling, crucial aspects in managing design projects.
This tool helps visualize the sequence and duration of tasks, aiding in the identification of dependencies and critical paths.
Design teams can use it to align schedules with project priorities, ensuring timely completion of tasks.
By keeping the broader timeline in view, this tool assists in maintaining momentum and avoiding bottlenecks.
Integrating the 7 New QC Tools in Product Design
Integrating the seven new QC tools into a product design team’s workflow requires a thoughtful approach.
Begin by assessing current processes and identifying areas where each tool can provide the most benefit.
Training team members on how to effectively use these tools is crucial to shifting organizational culture towards one that embraces structured problem-solving and decision-making.
As the various tools are adopted, continuous monitoring and evaluation will ensure that they are used to their fullest potential and adapt them to evolving design challenges.
Conclusion
Incorporating the seven new QC tools into the design process offers substantial advantages for product design departments looking to enhance their methods and foster innovation.
By leveraging these tools, teams gain insights into complex problems, improve decision-making, and ensure efficient resource allocation.
Ultimately, the result is an enhanced ability to deliver innovative and high-quality products while maintaining a competitive edge in a rapidly changing market.
資料ダウンロード
QCD調達購買管理クラウド「newji」は、調達購買部門で必要なQCD管理全てを備えた、現場特化型兼クラウド型の今世紀最高の購買管理システムとなります。
ユーザー登録
調達購買業務の効率化だけでなく、システムを導入することで、コスト削減や製品・資材のステータス可視化のほか、属人化していた購買情報の共有化による内部不正防止や統制にも役立ちます。
NEWJI DX
製造業に特化したデジタルトランスフォーメーション(DX)の実現を目指す請負開発型のコンサルティングサービスです。AI、iPaaS、および先端の技術を駆使して、製造プロセスの効率化、業務効率化、チームワーク強化、コスト削減、品質向上を実現します。このサービスは、製造業の課題を深く理解し、それに対する最適なデジタルソリューションを提供することで、企業が持続的な成長とイノベーションを達成できるようサポートします。
オンライン講座
製造業、主に購買・調達部門にお勤めの方々に向けた情報を配信しております。
新任の方やベテランの方、管理職を対象とした幅広いコンテンツをご用意しております。
お問い合わせ
コストダウンが利益に直結する術だと理解していても、なかなか前に進めることができない状況。そんな時は、newjiのコストダウン自動化機能で大きく利益貢献しよう!
(Β版非公開)