- お役立ち記事
- For Production Engineering Departments! Secrets to Reducing Lead Time with the Toyota Production System
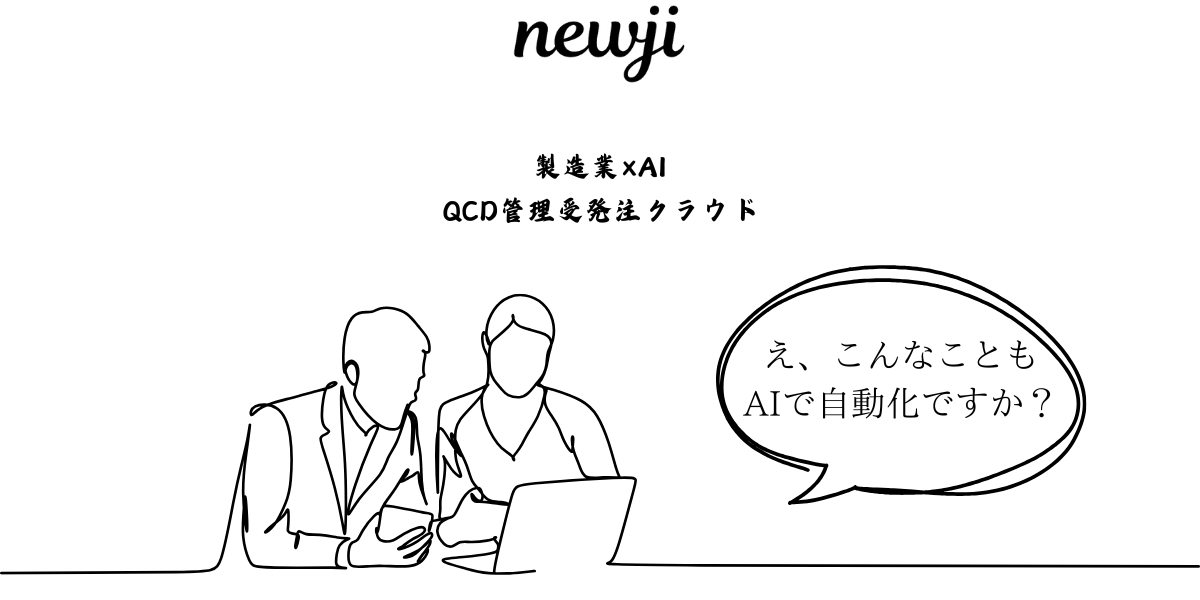
For Production Engineering Departments! Secrets to Reducing Lead Time with the Toyota Production System
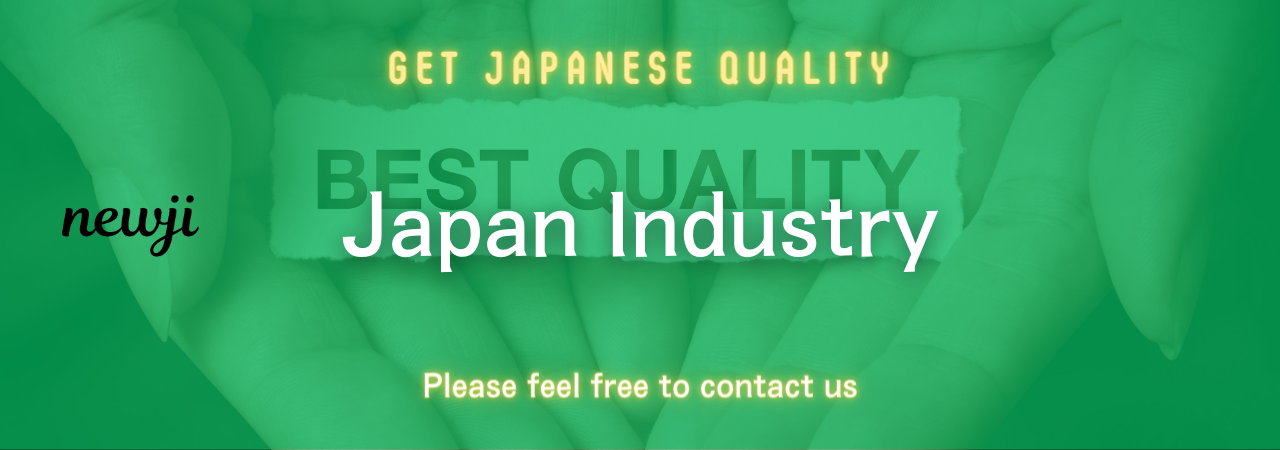
目次
Understanding the Toyota Production System
The Toyota Production System (TPS) is a methodology developed by Toyota to streamline production processes and improve efficiency.
It focuses on eliminating waste and optimizing productivity, which in turn reduces lead time.
Understanding the principles of TPS is crucial for any production engineering department aiming to enhance performance and meet deadlines effectively.
TPS is based on two main pillars: Just-in-Time (JIT) production and Jidoka.
JIT focuses on producing only what is needed, when it is needed, in the quantity that is needed.
This approach helps in minimizing inventory and reducing waste.
Jidoka, on the other hand, emphasizes building quality into the production process by allowing the machinery to detect and address issues immediately.
By incorporating these principles, production teams can significantly cut down lead times while maintaining high quality.
The Role of Lean Manufacturing in Reducing Lead Time
Lean manufacturing is an integral part of the Toyota Production System.
It aims at creating more value for customers with fewer resources by optimizing every step in the production process.
Lean principles help in identifying and eliminating non-value-added activities, also known as “waste.”
There are seven common types of waste that lean manufacturing seeks to eradicate: overproduction, waiting, transporting, over-processing, inventory, motion, and defects.
By focusing on reducing these wastes, production engineering departments can lower production costs, improve efficiency, and reduce lead times.
Moreover, lean manufacturing encourages a culture of continuous improvement, known as “Kaizen.”
Through Kaizen, small, incremental changes are constantly made to improve processes and eliminate inefficiencies.
Implementing Just-in-Time Inventory Management
A key component of TPS is the Just-in-Time (JIT) inventory management system.
JIT ensures that materials and components are delivered exactly when they are needed in the production process, thus reducing inventory costs and storage requirements.
For production engineering departments, implementing JIT means maintaining close coordination with suppliers and having a reliable and efficient supply chain.
It may involve setting up vendor-managed inventory systems or establishing long-term partnerships with key suppliers to ensure quality and timely delivery of materials.
When JIT is properly implemented, it not only reduces lead time but also enhances the overall agility of the production system.
This means that companies can respond more quickly to changes in market demand or customer requirements.
Balancing Flexibility with Stability
While JIT and TPS are focused on efficiency, it is also vital to balance flexibility with stability in production processes.
Flexibility allows production systems to adapt to changes or unexpected disruptions, while stability ensures consistent quality and minimization of errors.
To achieve this balance, production engineering departments should utilize standardized work processes and foster a culture of problem-solving and adaptability.
This approach minimizes downtime and supports continuous operations even when unforeseen challenges arise.
The Importance of Visual Management and Communication
Another secret to reducing lead time with TPS is the use of visual management and effective communication.
Visual management involves using visual signals, such as kanban boards, to manage workflow and communicate information to the production team.
Kanban boards are a fundamental part of TPS and help in visualizing tasks, monitoring progress, and identifying bottlenecks.
They enable production teams to understand priorities and allocate resources efficiently.
Moreover, regular communication and information sharing among team members is essential.
It helps in identifying issues early on and collaboratively finding solutions, which prevents delays and supports steady lead time reduction.
Streamlining Production Processes with Automation
Automation is another critical aspect that complements the Toyota Production System and aids in reducing lead time.
Automated systems can perform repetitive tasks faster and more accurately than human labor, leading to increased production speed and reduced human error.
Investing in technology and automation allows production engineering departments to enhance their capacity without the need for additional labor.
Automation also frees up employees to focus on more complex, value-added tasks, improving overall efficiency and productivity.
However, it’s important to strategically implement automation while considering the cost-benefit ratio and maintaining the essential human elements of creativity and problem-solving in the production process.
Fostering a Culture of Continuous Improvement
Continuous improvement, or Kaizen, is a cornerstone of the Toyota Production System.
This involves creating an organizational culture that encourages employees at all levels to propose improvements and continuously seek ways to enhance processes.
Producing engineering departments can implement the Plan-Do-Check-Act (PDCA) cycle to support continuous improvement.
This cycle involves planning a change, implementing it, checking the results, and acting on what is learned to refine or modify the change.
Engaging all employees in the process of improvement leverages the collective knowledge of the organization, leading to innovative solutions that enhance efficiency and reduce lead time.
Leveraging Data and Analytics for Decision Making
In the modern production environment, data and analytics play a significant role in decision-making and process optimization.
The use of data analytics can help production engineering departments identify trends, predict potential issues, and allocate resources more effectively.
By collecting and analyzing data, organizations can make more informed decisions that align with the goals of the Toyota Production System.
This data-driven approach allows for precise targeting of inefficiencies and supports proactive adjustments to reduce lead time.
Implementing sophisticated analytics tools can also provide insights into customer preferences and market dynamics, allowing production departments to be more responsive to demand variations.
Conclusion
Reducing lead time is a critical goal for production engineering departments, and the Toyota Production System offers valuable insights and strategies to achieve this.
By focusing on lean manufacturing, efficient inventory management, automation, and continuous improvement, organizations can optimize their production processes and enhance competitiveness.
With a strong commitment to visual management, communication, and data-driven decision-making, production teams can not only streamline their processes but also ensure a high level of quality.
Embracing these principles will ultimately lead to significant reductions in lead time, increased efficiency, and greater overall success in the production environment.
資料ダウンロード
QCD調達購買管理クラウド「newji」は、調達購買部門で必要なQCD管理全てを備えた、現場特化型兼クラウド型の今世紀最高の購買管理システムとなります。
ユーザー登録
調達購買業務の効率化だけでなく、システムを導入することで、コスト削減や製品・資材のステータス可視化のほか、属人化していた購買情報の共有化による内部不正防止や統制にも役立ちます。
NEWJI DX
製造業に特化したデジタルトランスフォーメーション(DX)の実現を目指す請負開発型のコンサルティングサービスです。AI、iPaaS、および先端の技術を駆使して、製造プロセスの効率化、業務効率化、チームワーク強化、コスト削減、品質向上を実現します。このサービスは、製造業の課題を深く理解し、それに対する最適なデジタルソリューションを提供することで、企業が持続的な成長とイノベーションを達成できるようサポートします。
オンライン講座
製造業、主に購買・調達部門にお勤めの方々に向けた情報を配信しております。
新任の方やベテランの方、管理職を対象とした幅広いコンテンツをご用意しております。
お問い合わせ
コストダウンが利益に直結する術だと理解していても、なかなか前に進めることができない状況。そんな時は、newjiのコストダウン自動化機能で大きく利益貢献しよう!
(Β版非公開)