- お役立ち記事
- For production engineers in the ball cleaner manufacturing industry! Selection of materials with both frictional force and durability
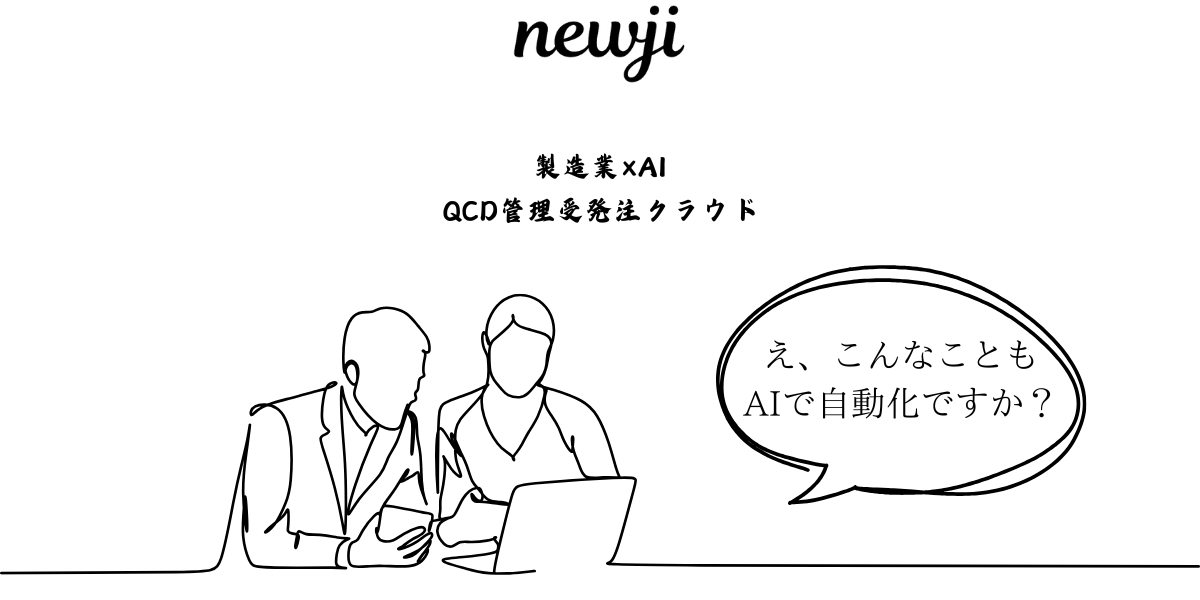
For production engineers in the ball cleaner manufacturing industry! Selection of materials with both frictional force and durability
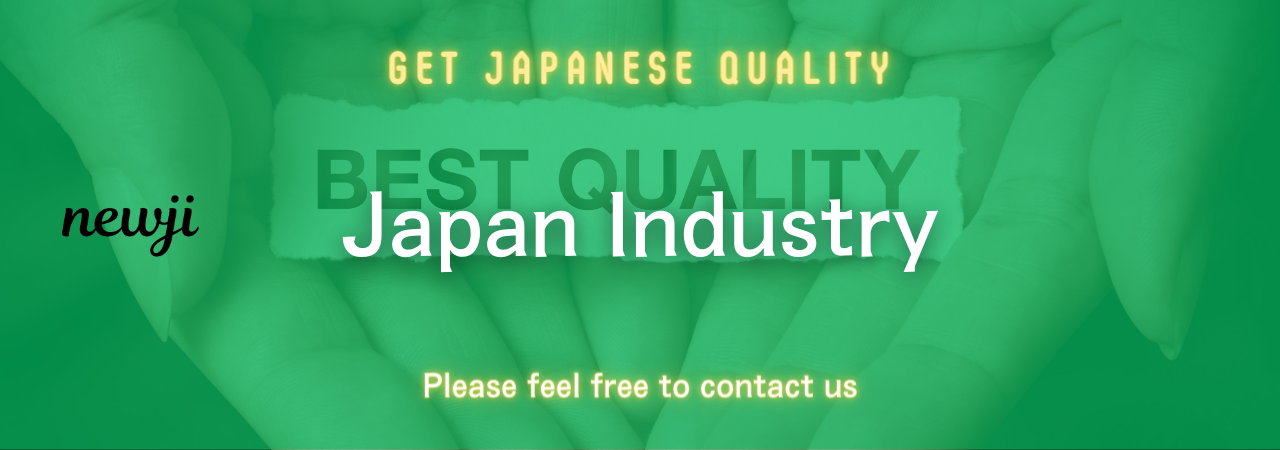
目次
Understanding the Importance of Material Selection
In the ball cleaner manufacturing industry, the selection of materials plays a crucial role in determining the product’s performance and lifespan.
Production engineers must focus on choosing materials that offer both high frictional force and durability.
The balance between these two factors ensures that the cleaner performs efficiently and lasts longer under regular use.
By understanding the specific needs of the product, engineers can make informed decisions about materials to ensure customer satisfaction and product success.
The Role of Frictional Force in Ball Cleaners
Frictional force is a key component in the function of ball cleaners.
It refers to the resistance encountered by one surface moving over another.
In ball cleaners, the frictional force helps in efficiently removing dirt, debris, and other impurities from the surface of the ball.
The higher the frictional force, the better the cleaner can scrub, leading to a cleaner ball with each use.
However, selecting a material with excessive friction can also wear down the ball, so it’s important to find a balance.
Materials That Provide Optimal Friction
Certain materials are known for their ability to provide the right amount of friction required for effective cleaning.
Rubber, synthetic polymers, and certain abrasive textiles are popular choices.
These materials can create the necessary friction without causing damage to the ball’s surface.
Additionally, these materials are versatile and can be easily shaped and combined with other materials to refine their properties.
Ensuring Material Durability
While frictional force is important, durability is equally critical in material selection.
The materials used in ball cleaners have to withstand repeated use, exposure to cleaning agents, and the stress of motion.
Durable materials ensure that the ball cleaner remains effective over a long period, providing users with a reliable product.
Durability can be achieved through careful selection of material composition, manufacturing processes, and protective coatings.
Durable Materials in Ball Cleaners
Engineers often turn to composites and high-strength polymers known for their resilience and ability to withstand wear and tear.
These materials not only offer durability but can maintain their structural integrity despite harsh conditions.
Some materials also come with protective coatings that can enhance durability.
These coatings act as a shield, preventing damage from external factors such as moisture or chemicals.
Balancing Frictional Force and Durability
The ultimate challenge for production engineers in the ball cleaner industry is to find the perfect balance between frictional force and durability.
Achieving this balance ensures that the cleaner can effectively perform its function for a long time without showing signs of wear or causing damage to the balls.
Testing and experimentation play an important role in finding this balance.
Engineers must test various material combinations to see how they perform under different conditions and stresses.
Innovative Solutions and Testing
Innovation in materials science has opened up new possibilities for creating materials that offer both high frictional force and durability.
Nanotechnology, for instance, allows for precise engineering of materials at the molecular level, optimizing their properties for specific applications.
Advanced testing techniques help engineers assess the performance of materials, making it easier to predict how they will fare in real-world conditions.
By investing in research and development, companies in the ball cleaner industry can stay ahead of the curve with new material technologies.
Environmental Considerations
In today’s world, the environmental impact of manufacturing processes and materials cannot be ignored.
Production engineers must consider not only the performance and durability of materials but also their environmental footprint.
By opting for sustainable materials, engineers can help reduce the environmental impact of their products and contribute to a more sustainable future.
Sustainable Material Choices
Sustainable materials are those that have a lesser impact on the environment from sourcing through to disposal.
Recyclable polymers, biodegradable options, and those produced with lower carbon footprints are ideal choices for ball cleaner manufacturing.
These materials can provide the necessary friction and durability while also supporting environmental goals.
Conclusion: Forward-Thinking Material Selection
For production engineers in the ball cleaner manufacturing industry, selecting the right materials is a complex but essential task.
By focusing on frictional force, durability, and environmental sustainability, engineers can design products that not only meet consumer needs but also excel in market performance.
Through innovation, careful testing, and a commitment to sustainability, engineers can ensure that ball cleaners remain effective, durable, and environmentally friendly.
資料ダウンロード
QCD調達購買管理クラウド「newji」は、調達購買部門で必要なQCD管理全てを備えた、現場特化型兼クラウド型の今世紀最高の購買管理システムとなります。
ユーザー登録
調達購買業務の効率化だけでなく、システムを導入することで、コスト削減や製品・資材のステータス可視化のほか、属人化していた購買情報の共有化による内部不正防止や統制にも役立ちます。
NEWJI DX
製造業に特化したデジタルトランスフォーメーション(DX)の実現を目指す請負開発型のコンサルティングサービスです。AI、iPaaS、および先端の技術を駆使して、製造プロセスの効率化、業務効率化、チームワーク強化、コスト削減、品質向上を実現します。このサービスは、製造業の課題を深く理解し、それに対する最適なデジタルソリューションを提供することで、企業が持続的な成長とイノベーションを達成できるようサポートします。
オンライン講座
製造業、主に購買・調達部門にお勤めの方々に向けた情報を配信しております。
新任の方やベテランの方、管理職を対象とした幅広いコンテンツをご用意しております。
お問い合わせ
コストダウンが利益に直結する術だと理解していても、なかなか前に進めることができない状況。そんな時は、newjiのコストダウン自動化機能で大きく利益貢献しよう!
(Β版非公開)