- お役立ち記事
- For production engineers in the daily necessities manufacturing industry! A guide to increasing bond strength with ultrasonic welding technology
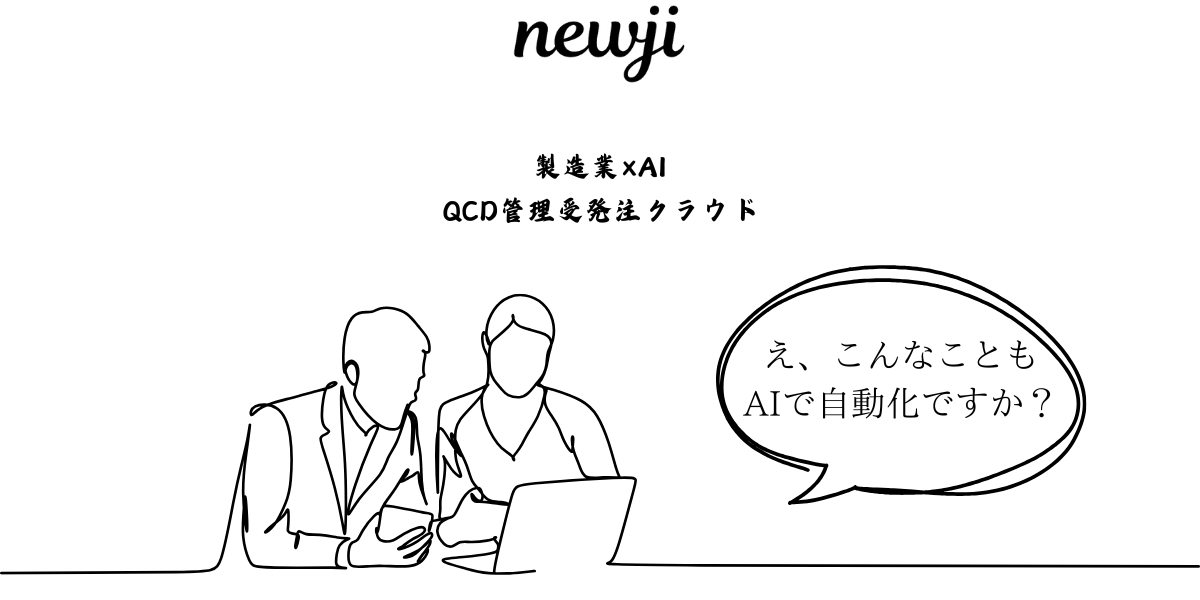
For production engineers in the daily necessities manufacturing industry! A guide to increasing bond strength with ultrasonic welding technology
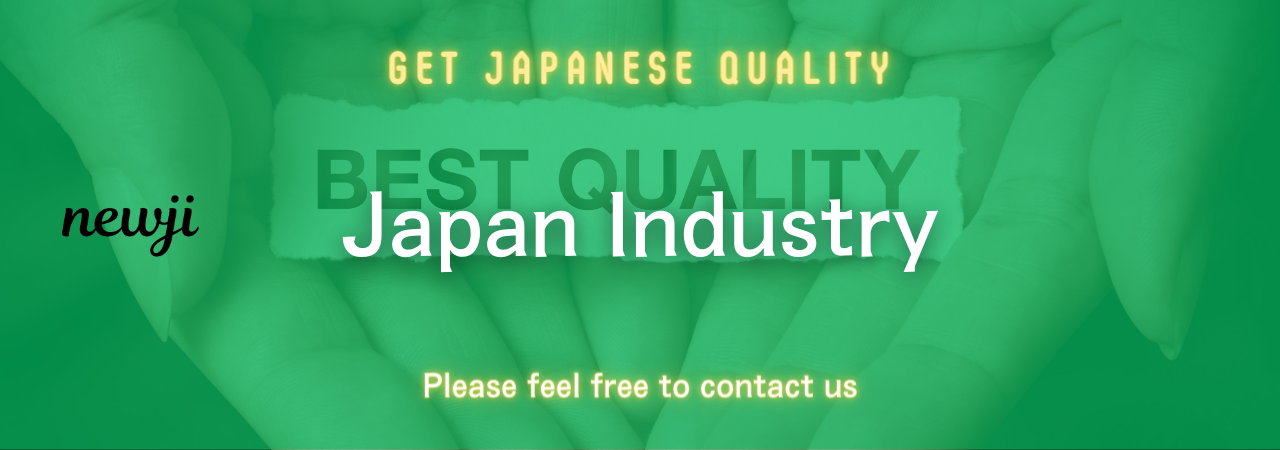
目次
Understanding Ultrasonic Welding
In the world of daily necessities manufacturing, efficiency and reliability are key components of success.
Ultrasonic welding is a technology that has proven to be pivotal in achieving both.
This innovative process, known for its precision and speed, involves joining materials using high-frequency ultrasonic acoustic vibrations.
Typically, materials such as plastics and metals are bonded through this method, resulting in durable and seamless connections.
Production engineers are increasingly relying on ultrasonic welding as it eliminates the need for additional adhesives or fasteners.
This not only reduces production costs but also minimizes the environmental impact, aligning with sustainable manufacturing goals.
Understanding how to harness this technology effectively can revolutionize a manufacturing line, significantly enhancing product quality and production efficiency.
The Science Behind Ultrasonic Welding
At the core of ultrasonic welding is the conversion of high-frequency sound waves into mechanical vibrations.
These vibrations generate localized heat, which facilitates the bonding process.
Primarily, the interface of the materials to be joined is where this energy converts into heat, allowing the materials to fuse without the application of external heat sources.
This method is especially beneficial in the manufacturing of daily necessities, where materials are often sensitive to excessive heat.
The entire process is swift, typically completed in a span of seconds, making it highly advantageous for high-volume production environments.
Key Components of Ultrasonic Welding Equipment
To understand ultrasonic welding better, it’s essential to recognize the principal components involved:
1. **Transducer**: Converts electrical energy into mechanical vibrations.
2. **Booster**: Modifies the amplitude of the vibrations and transfers them to the sonotrode.
3. **Sonotrode (or Horn)**: Directly applies the mechanical vibrations to the materials to be welded.
4. **Fixture**: Holds the materials in place during the welding process.
Each component has a pivotal role in ensuring the effectiveness and quality of the welding process.
Selection and maintenance are crucial for optimal performance, emphasizing the need for thorough understanding and expertise by production engineers.
Optimizing Bond Strength in Ultrasonic Welding
For production engineers, increasing bond strength in ultrasonic welding can lead to improved product durability and consumer trust.
Several factors play into optimizing the bond strength in this cutting-edge technology.
Material Compatibility
One primary consideration is the compatibility of the materials being welded.
While ultrasonic welding is versatile, not all materials yield the same bond strength.
Thermoplastics are typically ideal candidates due to their ability to soften and remold, facilitating a stronger bond.
Selecting the right material combinations is a fundamental step in maximizing welding outcomes.
Design and Joint Configuration
The design of the parts and the configuration of the joint significantly impacts bond strength.
Proper design can ensure that the energy is effectively transferred and distributed across the joining surfaces.
Accordingly, implementing energy directors—small, triangular sections on the surface of one of the parts—can help focus the energy and enhance the weld quality.
Process Parameters Adjustment
Fine-tuning various process parameters such as pressure, time, and amplitude is vital in ultrasonic welding.
These parameters directly affect how the energy is delivered to the joining surfaces.
Experimenting with different settings can help identify the optimal conditions for achieving maximum bond strength.
Preventing Common Welding Defects
Understanding how to prevent defects that could undermine the integrity of the bond is essential for production engineers.
Common issues involve voids, incomplete bonds, and surface damages.
Proper machine calibration and regular maintenance can go a long way in preventing these defects.
Additionally, ensuring clean joining surfaces can improve bond quality and durability.
Advantages of Ultrasonic Welding in Manufacturing
Incorporating ultrasonic welding technology offers significant advantages for manufacturers of daily necessities.
Here are some of the most impactful benefits:
Speed and Efficiency
The rapid nature of ultrasonic welding makes it ideal for high-volume production.
With some welds taking less than a second, manufacturers can drastically increase their output without sacrificing quality.
Environmental and Cost Benefits
By eliminating the need for adhesives or fasteners, this process reduces material costs and aligns with eco-friendly practices.
It significantly decreases the production of waste, enhancing the overall sustainability of manufacturing operations.
High-Quality Bonds
Ultrasonic welding produces clean, durable bonds, which are crucial for product reliability.
This high-quality output enhances consumer satisfaction and diminishes the incidence of product returns due to mechanical failures.
Conclusion
The relevance of ultrasonic welding in the manufacturing of daily necessities cannot be overstated.
By offering a precise, efficient, and cost-effective bonding solution, it provides production engineers with the tools needed to excel in a competitive market.
By understanding and optimizing the parameters that affect bond strength, engineers can significantly enhance their production processes.
Ultimately, embracing ultrasonic welding technology represents a strategic investment toward achieving long-term manufacturing excellence.
資料ダウンロード
QCD調達購買管理クラウド「newji」は、調達購買部門で必要なQCD管理全てを備えた、現場特化型兼クラウド型の今世紀最高の購買管理システムとなります。
ユーザー登録
調達購買業務の効率化だけでなく、システムを導入することで、コスト削減や製品・資材のステータス可視化のほか、属人化していた購買情報の共有化による内部不正防止や統制にも役立ちます。
NEWJI DX
製造業に特化したデジタルトランスフォーメーション(DX)の実現を目指す請負開発型のコンサルティングサービスです。AI、iPaaS、および先端の技術を駆使して、製造プロセスの効率化、業務効率化、チームワーク強化、コスト削減、品質向上を実現します。このサービスは、製造業の課題を深く理解し、それに対する最適なデジタルソリューションを提供することで、企業が持続的な成長とイノベーションを達成できるようサポートします。
オンライン講座
製造業、主に購買・調達部門にお勤めの方々に向けた情報を配信しております。
新任の方やベテランの方、管理職を対象とした幅広いコンテンツをご用意しております。
お問い合わせ
コストダウンが利益に直結する術だと理解していても、なかなか前に進めることができない状況。そんな時は、newjiのコストダウン自動化機能で大きく利益貢献しよう!
(Β版非公開)