- お役立ち記事
- For production engineers in the doormat manufacturing industry! Tips on fiber processing to achieve both mud protection and durability
For production engineers in the doormat manufacturing industry! Tips on fiber processing to achieve both mud protection and durability
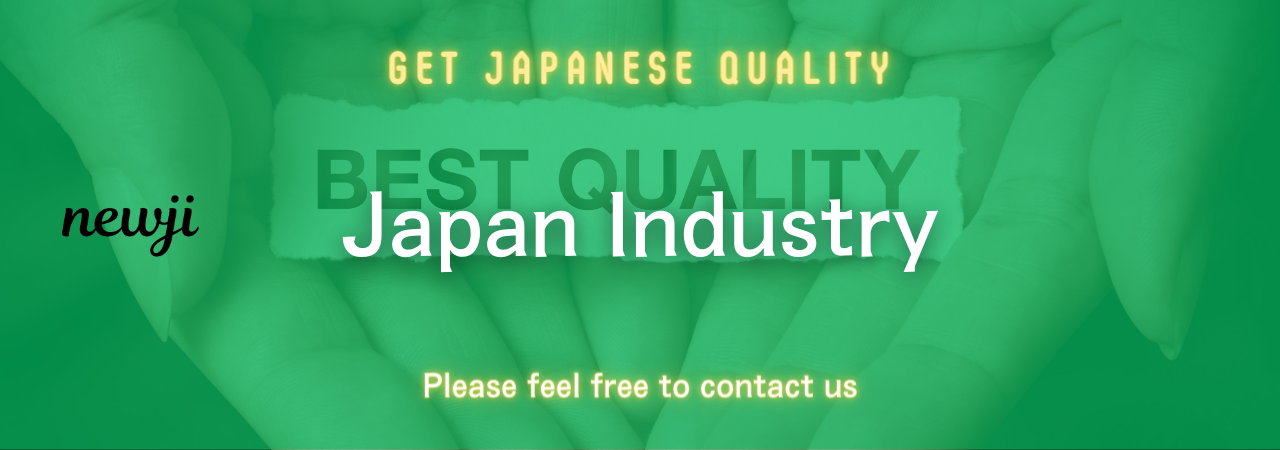
目次
Understanding the Importance of Fiber Processing in Doormat Manufacturing
Doormats serve as the first line of defense against dirt and mud entering a building, and for production engineers in the doormat manufacturing industry, ensuring both mud protection and durability is paramount.
To achieve this balance, a deep understanding of fiber processing is essential.
The right choice of materials and techniques can make all the difference in the performance of the final product.
The Role of Material Selection
The foundation of an effective doormat begins with the selection of appropriate materials.
Natural fibers such as coir, jute, and wool are popular for their absorbency and texture, which help trap dirt and mud.
Synthetic fibers like nylon, polypropylene, and rubber are known for their durability and resistance to weather conditions.
Production engineers must weigh the benefits and limitations of each to create a product that excels in both functionality and longevity.
When choosing fibers, consider the intended environment for the doormat.
For instance, mats designed for indoor use may prioritize aesthetic appeal and comfort, while outdoor doormats should focus on robustness and the ability to withstand challenging weather conditions.
Optimizing Fiber Density and Weave
Fiber density and the weaving pattern play crucial roles in enhancing the mud protection capabilities of a doormat.
A dense fiber structure minimizes gaps, enabling the mat to capture more dirt particles.
However, the key is to balance density with flexibility to ensure ease of use.
Experimenting with various weaving techniques can also improve the performance of the product.
For example, a loop pile weave offers a plush texture and good dirt scraping ability, while a cut pile provides a softer feel but may be less effective in harsh environments.
Enhancing Durability with Processing Techniques
Durability is a critical factor for doormats, especially those subjected to frequent use or extreme conditions.
Heat setting is a common processing technique that enhances the structural integrity of synthetic fibers.
This process involves exposing fibers to heat to lock in their shape and size, improving resilience and longevity.
Using reinforcing treatments, such as latex backing, can add further strength to the doormat, preventing fibers from breaking or matting.
This not only extends the product’s lifespan but also maintains its effectiveness over time.
Innovation with Blended Fibers
Blending natural and synthetic fibers can bring the best of both worlds to a doormat.
This approach allows for customizable properties, such as combining the aesthetic and absorbent qualities of natural fibers with the strength and weather resistance of synthetics.
Engineers can experiment with different ratios to achieve the desired performance characteristics.
When developing blended fiber doormats, it’s crucial to ensure compatibility between the fiber types to avoid issues such as shedding or uneven wear.
Conducting thorough testing and quality assurance processes helps prevent potential problems and ensures a high-quality product.
The Impact of Environmental Considerations
As environmental awareness increases, so does the demand for eco-friendly products.
Production engineers must consider sustainable practices in fiber processing to meet consumer expectations and regulatory requirements.
This includes using recycled materials, reducing waste, and optimizing energy efficiency during production.
Employing biodegradable materials where possible is another step towards sustainability.
These materials naturally break down over time, minimizing environmental impact.
By prioritizing eco-friendly practices, manufacturers can differentiate their products in the competitive market.
Utilizing Technological Advancements
Technological advancements have opened new possibilities in doormat manufacturing.
For example, advanced spinning and extrusion techniques allow for the creation of unique fiber textures and constructions that improve mud trapping capabilities.
Automation in weaving and tufting processes can enhance precision and consistency, reducing errors and waste.
Adopting these modern technologies can streamline production, improve product quality, and reduce costs.
For production engineers, staying informed on the latest developments in textile technology is vital to remain competitive and efficient.
Conclusion: Striking the Balance
For production engineers in the doormat manufacturing industry, achieving a balance between mud protection and durability is a nuanced process.
Through careful material selection, innovative fiber processing techniques, and a keen eye on sustainability, engineers can create products that meet and exceed consumer expectations.
By continually exploring new materials, methods, and technologies, doormat manufacturers can ensure their products provide both function and longevity.
In doing so, they contribute not only to a cleaner entryway but also to a greener planet.
資料ダウンロード
QCD調達購買管理クラウド「newji」は、調達購買部門で必要なQCD管理全てを備えた、現場特化型兼クラウド型の今世紀最高の購買管理システムとなります。
ユーザー登録
調達購買業務の効率化だけでなく、システムを導入することで、コスト削減や製品・資材のステータス可視化のほか、属人化していた購買情報の共有化による内部不正防止や統制にも役立ちます。
NEWJI DX
製造業に特化したデジタルトランスフォーメーション(DX)の実現を目指す請負開発型のコンサルティングサービスです。AI、iPaaS、および先端の技術を駆使して、製造プロセスの効率化、業務効率化、チームワーク強化、コスト削減、品質向上を実現します。このサービスは、製造業の課題を深く理解し、それに対する最適なデジタルソリューションを提供することで、企業が持続的な成長とイノベーションを達成できるようサポートします。
オンライン講座
製造業、主に購買・調達部門にお勤めの方々に向けた情報を配信しております。
新任の方やベテランの方、管理職を対象とした幅広いコンテンツをご用意しております。
お問い合わせ
コストダウンが利益に直結する術だと理解していても、なかなか前に進めることができない状況。そんな時は、newjiのコストダウン自動化機能で大きく利益貢献しよう!
(Β版非公開)