- お役立ち記事
- For production engineers in the electronic equipment manufacturing industry! A method to improve work efficiency by standardizing rework processes
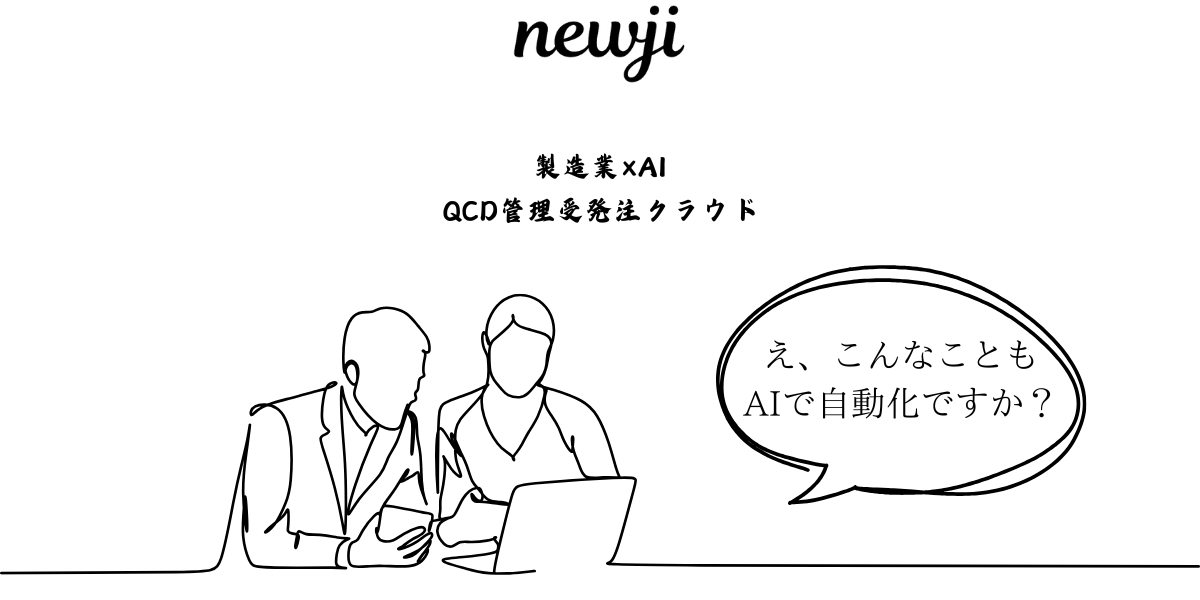
For production engineers in the electronic equipment manufacturing industry! A method to improve work efficiency by standardizing rework processes
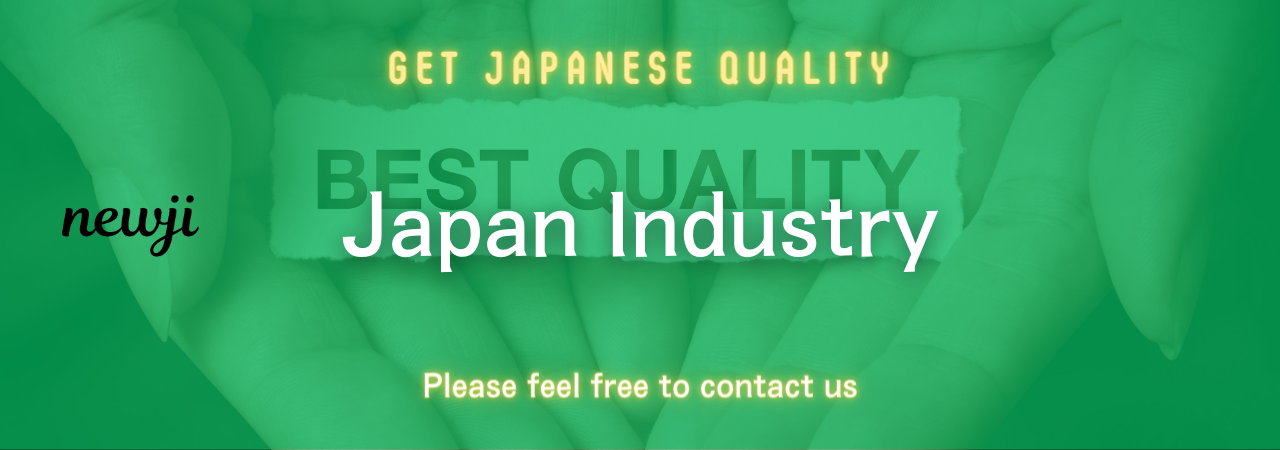
目次
Introduction
In the electronic equipment manufacturing industry, production engineers play a crucial role in ensuring that all processes run smoothly and efficiently.
One particular aspect that often presents challenges is handling rework processes when defects are discovered.
Rework, if not standardized, can lead to increased costs, delays, and inconsistencies in product quality.
This article discusses a method to improve work efficiency by standardizing these rework processes, which ultimately benefits production engineers in the electronic equipment sector.
The Importance of Standardizing Rework Processes
Standardization is the key to minimizing variability in manufacturing.
By creating a uniform approach to handling rework, companies can better manage resources, reduce waste, and improve overall product quality.
Standardizing rework processes ensures that all team members follow the same procedures, making it easier to identify issues, streamline workflows, and maintain consistent product standards.
Rework processes in the electronic equipment industry can be complex due to the intricate nature of the products involved.
Without a standardized approach, each technician may apply a different method to solve a similar issue, leading to inconsistent results.
A well-defined rework process provides a clear guideline on how to effectively address defects, ensuring that the end product meets expectations.
Steps to Standardizing Rework Processes
1. Identify Common Defects
The first step in standardizing rework processes is to identify the most common defects encountered during production.
By analyzing past data and gathering input from production teams, it’s possible to pinpoint recurring issues that require rework.
Looking at defect trends enables engineers to understand the root causes and focus their efforts on the most critical areas needing improvement.
2. Develop Rework Protocols
Once common defects are identified, the next step is to develop rework protocols.
These protocols should include detailed instructions for addressing each defect type, outlining necessary tools, techniques, and materials.
It’s crucial to ensure these protocols are clear and easily accessible to all technicians to guarantee consistent execution.
Rework protocols should also include criteria for testing and validating the reworked product, ensuring it meets the desired specifications before proceeding to the next production stage.
3. Train Production Teams
Successful implementation of standardized rework processes requires thorough training of all team members.
Training sessions should focus on teaching the developed protocols, emphasizing the importance of consistency and attention to detail.
Production engineers should provide hands-on sessions where technicians can practice the processes under supervision, fostering a deeper understanding of the standardized approach.
4. Implement Quality Control Measures
Quality control is essential to monitor the effectiveness of standardized rework processes.
Implement regular audits and inspections to assess the adherence to rework protocols and to identify areas requiring further optimization.
Feedback from quality control teams is invaluable for continuous improvement.
Regularly review and update rework protocols based on their insights, ensuring they evolve to meet changing production needs.
5. Utilize Technology for Enhanced Efficiency
Leverage technology to streamline rework processes and boost efficiency.
Automated systems can assist with defect detection, tracking rework metrics, and managing documentation.
By integrating technology, production engineers can reduce human error, improve data accuracy, and free up personnel for more value-added tasks.
Consider implementing digital platforms that allow real-time updates and communication across production teams.
This ensures everyone is informed of any procedural changes and assists in maintaining compliance with standardized practices.
6. Continuously Monitor and Optimize
Standardizing rework processes is not a one-time task.
It requires ongoing monitoring and optimization.
Establish a feedback loop where technicians and engineers can freely discuss challenges and suggest improvements.
Regularly set aside time to review the entire rework cycle, focusing on areas where delays or inefficiencies occur.
This proactive approach ensures the rework process remains effective and adapts to new challenges that arise over time.
Benefits of Standardized Rework Processes
The benefits of standardizing rework processes in the electronic equipment manufacturing industry are significant.
Firstly, it leads to reduced production costs by minimizing waste and conserving resources.
Consistent rework methods reduce the number of defects, leading to fewer product recalls and less time spent on corrective actions.
Secondly, standardized rework boosts production speed and efficiency.
Technicians spend less time figuring out how to address defects, allowing them to focus on completing tasks promptly.
Thirdly, consistent processes enhance product quality and customer satisfaction.
When products consistently meet quality standards, the brand reputation strengthens, leading to higher levels of trust and potential for increased sales.
Conclusion
For production engineers in the electronic equipment manufacturing industry, standardizing rework processes is a critical step towards improving work efficiency.
By addressing common defects with well-defined protocols, ensuring all team members are properly trained, and leveraging technology, rework becomes a more manageable and predictable aspect of manufacturing.
The result is a more efficient production line, reduced costs, enhanced product quality, and ultimately, greater customer satisfaction.
Embrace these methods today to drive significant improvements and stay competitive in the fast-paced electronic equipment sector.
資料ダウンロード
QCD調達購買管理クラウド「newji」は、調達購買部門で必要なQCD管理全てを備えた、現場特化型兼クラウド型の今世紀最高の購買管理システムとなります。
ユーザー登録
調達購買業務の効率化だけでなく、システムを導入することで、コスト削減や製品・資材のステータス可視化のほか、属人化していた購買情報の共有化による内部不正防止や統制にも役立ちます。
NEWJI DX
製造業に特化したデジタルトランスフォーメーション(DX)の実現を目指す請負開発型のコンサルティングサービスです。AI、iPaaS、および先端の技術を駆使して、製造プロセスの効率化、業務効率化、チームワーク強化、コスト削減、品質向上を実現します。このサービスは、製造業の課題を深く理解し、それに対する最適なデジタルソリューションを提供することで、企業が持続的な成長とイノベーションを達成できるようサポートします。
オンライン講座
製造業、主に購買・調達部門にお勤めの方々に向けた情報を配信しております。
新任の方やベテランの方、管理職を対象とした幅広いコンテンツをご用意しております。
お問い合わせ
コストダウンが利益に直結する術だと理解していても、なかなか前に進めることができない状況。そんな時は、newjiのコストダウン自動化機能で大きく利益貢献しよう!
(Β版非公開)